Mastering TIG Welding Aluminum - A Beginner's Guide
April 28, 2024
14 min read
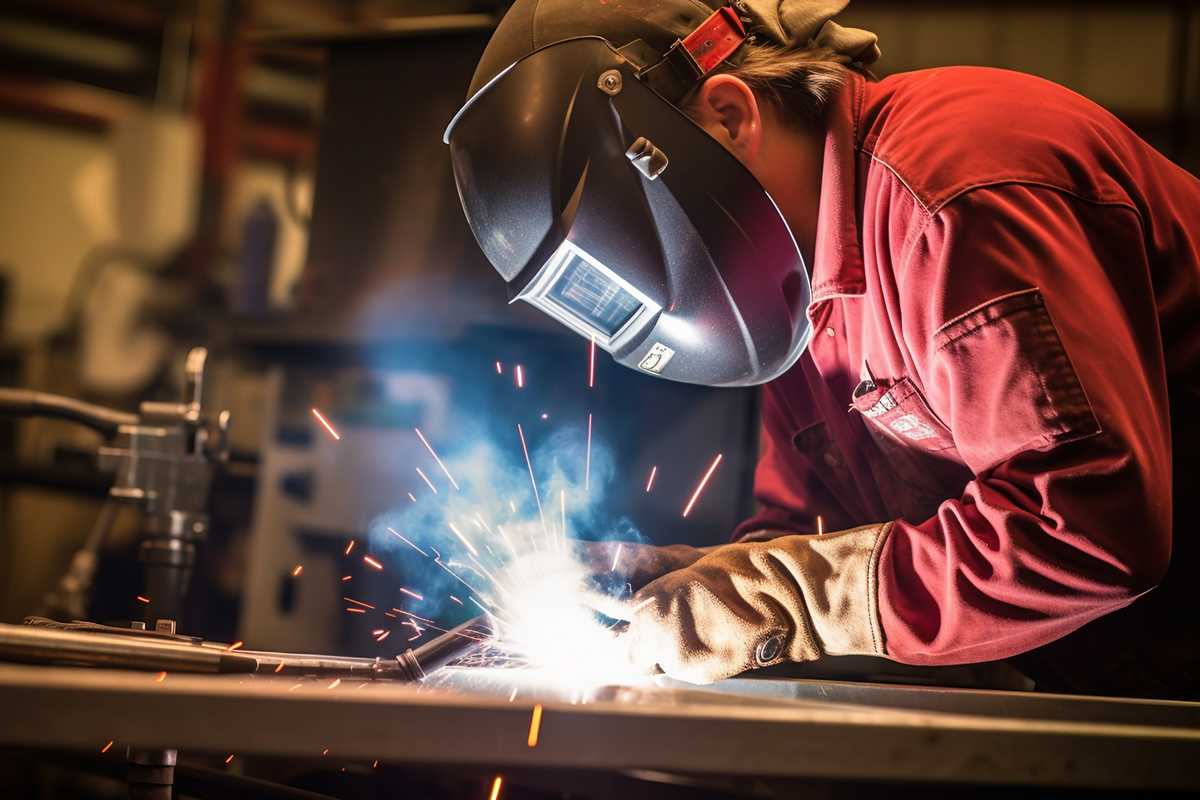
1. The Art of Fusing Aluminum with TIG Welding
Welcome to the world of TIG welding, a precise and rewarding craft that marries the strength of aluminum with the finesse of welding. TIG, or Tungsten Inert Gas welding, is a technique that stands out for its ability to create strong, clean, and aesthetically pleasing joints in aluminum—a metal celebrated for its lightness and durability. By using a non-consumable tungsten electrode, TIG welding ensures the integrity of the weld without compromising the metal's quality. Argon gas plays a crucial role as well, shielding the weld from any atmospheric impurities.
This guide is designed for beginners eager to navigate the nuances of TIG welding aluminum. Whether you're an aspiring hobbyist or a professional looking to sharpen your skills, we'll provide you with a comprehensive walkthrough. From the rationale behind choosing TIG welding for aluminum to the safety protocols that safeguard your well-being, we've got you covered. By the end of this guide, you'll be equipped with the foundational knowledge to start your TIG welding journey with confidence and creativity.
2. The Superiority of TIG Welding for Aluminum
Aluminum, with its combination of lightness and strength, is a popular choice for a variety of projects, from intricate art pieces to robust structural components. When it comes to welding this versatile metal, TIG (Tungsten Inert Gas) welding stands out as the method of choice for professionals who value precision and aesthetics. But what makes TIG welding the superior technique for aluminum? Let's explore the key benefits that give TIG welding its edge.
Enhanced Precision and Heat Control
TIG welding's hallmark is its exceptional precision and control over heat application. This is especially beneficial for aluminum, which is more prone to warping due to its lower melting point compared to steel. The ability to finely tune the heat input with TIG welding means that even the most delicate aluminum parts can be joined without the risk of burn-through or distortion.
Superior Weld Quality
The aesthetic appeal of TIG welds cannot be overstated. The process yields clean, spatter-free welds with a smooth finish, which is particularly important for projects where appearance is paramount, such as in custom automotive builds or architectural metalwork. The non-consumable tungsten electrode used in TIG welding ensures that no extra material is introduced into the weld pool, resulting in a neat and attractive final weld.
Adaptability Across Aluminum Alloys
Aluminum's diversity in alloys, each with its unique welding characteristics, requires a versatile welding approach. TIG welding's adaptability shines here, as it can be fine-tuned to accommodate the vast range of aluminum types and thicknesses, ensuring a reliable weld regardless of the specific alloy or project complexity.
Strength and Durability of Welds
The bonds formed through TIG welding are not just aesthetically pleasing but also incredibly robust. This is critical for aluminum applications that demand both lightness and durability. TIG welding achieves deep penetration into the aluminum, forging a strong and long-lasting joint that can endure significant stress and strain.
Reduced Post-Weld Cleanup
Efficiency is key in any professional setting, and TIG welding aids in this by minimizing the post-weld cleanup. The process produces little to no spatter and no slag, which means less time is spent grinding and cleaning up after welding. This is a substantial advantage when working with aluminum, where a flawless finish is often required.
In conclusion, TIG welding's unmatched precision, superior weld quality, versatility, and the strength of the joints it produces make it the go-to method for aluminum welding. Whether you're a beginner eager to learn the craft or an experienced welder striving for perfection in your aluminum projects, TIG welding offers the capabilities to achieve exceptional results.
3. Overcoming the Hurdles of TIG Welding Aluminum
TIG welding aluminum is a skill that, once mastered, can open up a world of possibilities for creating strong, lightweight structures. However, beginners may find themselves facing several hurdles that can seem overwhelming at first. Let's break down these challenges and provide clear solutions to help you overcome them.
Heat Management
Aluminum's high thermal conductivity means it heats and cools quickly, which can cause warping. To prevent this, you need to manage your heat input carefully. Start with a lower amperage and increase it gradually until you find the sweet spot where the weld pool is stable without overheating the metal. For example, if you're working with a 1/16-inch thick aluminum sheet, you might begin at around 60 amps and adjust as needed.
Cleaning the Oxide Layer
The oxide layer that forms on aluminum has a higher melting point than the aluminum itself, which can prevent proper fusion. To tackle this, clean the surface with a dedicated stainless steel brush—brushing in one direction only—and then wipe it down with a solvent like acetone right before welding. This will remove the oxide layer and any other contaminants.
Contamination Prevention
Aluminum is more sensitive to contamination than steel. Keep your work area free of dirt, oil, and other metals to avoid a weak or porous weld. For instance, make sure your gloves are clean and don't handle any other metals before touching the aluminum.
Filler Material Selection
Choosing the right filler rod is crucial. It must match the aluminum alloy you're welding. For example, a 4043 filler rod is a common choice for general welding, but for a part that will be anodized, a 5356 rod would be better as it anodizes to a closer color match to the base material.
Feeding the Filler Rod
Due to aluminum's softness, feeding the filler rod requires a steady hand. You need to add the rod smoothly to avoid disrupting the arc or adding too much material. Practice feeding the rod consistently at the right speed and angle to maintain a uniform weld bead.
Machine Setup
Setting up your welding machine correctly is essential. Aluminum welding typically requires AC, which can be more complex than DC. You'll need to adjust the balance between penetration and cleaning action by setting the AC frequency and balance controls on your machine. For instance, a higher AC frequency can provide a more focused arc, while adjusting the balance control can increase the cleaning effect on the oxide layer.
By understanding and addressing these challenges with the right techniques and settings, you'll be well on your way to producing strong, clean welds on aluminum. Remember, it's all about practice and patience—don't get discouraged by initial setbacks. Keep refining your approach, and you'll see improvement with every weld you make.
4. Essential Steps for Preparing Aluminum for TIG Welding
Before you ignite the TIG torch and begin the intricate process of welding aluminum, it's imperative to meticulously prepare your materials. This preparation is the bedrock of a successful weld, ensuring that the final joint is both aesthetically pleasing and structurally sound. Let's walk through the key steps to prime your aluminum for the TIG welding process.
Thorough Surface Cleaning
Aluminum's natural resistance to rust is due to a protective oxide layer that forms on its surface. However, this same layer can be a welder's nemesis, as it melts at a higher temperature than the aluminum beneath it, potentially leading to a weak weld. To combat this, start with a dedicated stainless steel wire brush—only used for aluminum—to scrub away the oxide layer. Brush consistently in one direction to avoid pushing contaminants back into the metal. After brushing, a solvent such as acetone should be applied with a clean cloth to remove any residual oils or dirt. This cleaning should be done immediately before welding to prevent the oxide from re-forming.
Selecting the Right Shielding Gas
The choice of shielding gas can make or break your TIG welding project. Pure argon is the standard choice for its ability to provide a stable arc and help clean the aluminum during the weld. For projects involving thicker aluminum, a blend of argon and helium can offer deeper penetration due to helium's higher heat contribution. However, this blend is costlier and may not be necessary for all projects. Beginners should start with pure argon and only switch to a blend if penetration issues arise.
Choosing Tungsten and Filler Material
The selection of tungsten and filler material is critical. A pure tungsten electrode or one alloyed with lanthanum or cerium is best suited for aluminum. Sharpen these electrodes to a fine point to concentrate the arc for improved control. As for filler rods, it's essential to match them to the aluminum alloy you're working with. The 4043 alloy filler rod is a common and versatile choice, melting easily and working well with most aluminum grades. If you're welding a piece that will undergo anodizing, opt for a 5356 alloy filler rod to ensure the weld area color matches the rest of the material after the anodizing process.
By following these essential preparation steps, you're not just getting ready to weld; you're setting yourself up for a TIG welding session that results in durable, high-quality joins. Proper preparation minimizes welding complications and ensures that your efforts result in a product you can be proud of.
5. Ensuring a Safe TIG Welding Experience
When engaging in TIG welding, particularly with aluminum, it's essential to prioritize safety. The high temperatures, intense UV light, and the use of inert gases can present significant hazards if not managed correctly. To ensure a safe welding experience, follow these comprehensive safety guidelines.
Personal Protective Equipment (PPE)
Equipping yourself with the appropriate Personal Protective Equipment (PPE) is the first line of defense against potential hazards. Here's what you need:
- Auto-Darkening Welding Helmet: Protect your eyes from harmful UV and IR radiation with a quality helmet that darkens automatically when the arc is struck.
- Leather Welding Gloves: Shield your hands from burns and electric shocks with durable gloves designed for welding.
- Flame-Resistant Clothing: Cover your skin with clothing that resists ignition, such as a long-sleeved shirt and pants made from materials like leather or treated cotton.
- Safety Glasses with Side Shields: Even when not welding, keep your eyes safe from debris with safety glasses.
- Respirator: In areas with poor ventilation, wear a respirator to filter out harmful fumes and gases.
Ventilation and Fume Control
Good ventilation is crucial for dispersing toxic fumes. Use a fume extraction system or ensure the workspace is well-ventilated, especially when working indoors. In confined spaces, additional fans or exhaust equipment may be necessary.
Electrical Safety
To prevent electrical hazards, ensure your TIG welding equipment is properly grounded. Inspect all cables and connections regularly for wear and tear, and keep the welding area dry to avoid electric shocks.
Fire Prevention
Welding can produce sparks that might ignite nearby flammable materials. Always have a fire extinguisher within reach, and maintain a clean workspace, free from any flammable substances. A fire blanket is also useful for quickly smothering small fires.
Handling Gas Cylinders
The argon gas used in TIG welding is stored under high pressure and requires careful handling:
- Always secure cylinders in an upright position to a stable support to prevent them from tipping over.
- Keep cylinders away from potential heat sources and electrical hazards.
- Regularly check for gas leaks at connections with a soapy water solution; bubbles will form if there's a leak.
Knowledge and Preparedness
Proper training and knowledge of your equipment are essential. Before you begin welding, familiarize yourself with the operation of your equipment and read all relevant safety instructions. Being aware of the potential risks and knowing how to avoid them is crucial for maintaining a safe welding environment.
By following these safety measures, you can minimize risks and concentrate on honing your TIG welding skills. Remember, integrating safety into every aspect of your welding routine is not just good practice—it's essential for your protection.
6. Optimizing TIG Welding Settings for Aluminum Success
Achieving excellence in TIG welding aluminum hinges on fine-tuning your equipment settings and mastering specific welding techniques. This section is dedicated to helping you understand and apply the optimal settings and methods for first-rate aluminum welds.
Understanding AC's Role in Aluminum Welding
For TIG welding aluminum, alternating current (AC) is the gold standard. AC is essential because it alternates between positive and negative currents, effectively "cleaning" the stubborn oxide layer that forms on aluminum, allowing the weld to penetrate deeply. In contrast, direct current (DC) is more suited to metals like steel and lacks the cleaning capability necessary for aluminum.
Dialing in Argon Flow and Amperage
The right argon gas flow rate is critical. Aim for a flow of 15-20 cubic feet per hour (CFH) to protect your weld without causing gas turbulence that could contaminate the weld pool. As for amperage, a general guideline is 1 amp per .001 inch of aluminum thickness. For instance, welding a 1/8 inch thick piece would typically start at about 125 amps. Adjustments may be needed based on your specific project and welder model.
Techniques for TIG Welding Aluminum
Here are actionable techniques to improve your TIG welding on aluminum:
- Preheat aluminum pieces over 1/4 inch thick to between 100°F and 250°F to minimize cracking.
- Keep your travel speed steady to distribute heat evenly and prevent warping or burn-through.
- Use a push technique, tilting the torch forward 10-15 degrees to direct heat away from the weld puddle, resulting in a cleaner, more penetrating weld.
- Maintain a clean, well-shaped tungsten electrode. For AC aluminum welding, a slightly rounded tip is ideal.
- Get comfortable with the foot pedal to control heat input on the fly, which is crucial for managing aluminum's fluid weld pool.
- Watch the weld pool closely; it should be clear and well-defined. A murky pool suggests possible contamination or incorrect settings.
By focusing on these settings and techniques, you're setting yourself up for TIG welding success with aluminum. Practice is essential, so don't get discouraged by early mistakes. Experiment with different settings and techniques to discover what yields the best results for your projects.
7. Embarking on Your TIG Welding Aluminum Adventure
As we wrap up this comprehensive guide, you're now better equipped to begin your TIG welding aluminum journey with confidence. We've traversed through the critical knowledge and techniques that lay the foundation for successful welding projects. From understanding why TIG welding is the preferred method for aluminum to the meticulous preparation of your materials and workspace, we've set the stage for your welding endeavors.
Throughout the guide, we've emphasized the importance of surface cleanliness, the strategic selection of shielding gas, and the careful choice of tungsten and filler materials. These elements are vital for creating welds that are not only aesthetically pleasing but also mechanically sound. We've also underscored the importance of safety, highlighting the need for proper protective gear and a well-ventilated workspace to ensure your welding practice is as safe as it is productive.
The guide has provided you with a deeper understanding of the technical aspects of TIG welding, such as the role of AC current in managing aluminum's oxide layer and the importance of precise argon flow and amperage settings. These insights are crucial for avoiding common welding challenges and for enhancing the overall quality of your welds.
Moreover, we've shared practical tips and techniques that are essential for honing your TIG welding skills. Remember that mastering TIG welding aluminum is a journey of patience and continuous learning. Each project you take on will add to your growing expertise, helping you navigate and overcome the complexities of welding this unique metal.
As you move forward, keep in mind that the path to becoming a skilled TIG welder is one of perseverance and attention to detail. Your dedication to the craft will enable you to create projects that not only meet but exceed expectations in both form and function.
Continue to learn, prioritize safety, and embrace the fulfilling experience of mastering TIG welding aluminum. Your commitment to this craft will yield results that are both personally rewarding and professionally commendable.
Sharing is Caring
Feedback
At WeldWins, we know we aren't perfect which is why we're always looking for ways to improve. You can help us do better by taking 2 minutes to fill out our simple feedback form.
Any and all feedback is welcome. It could be a complaint, an idea, or even just a comment, we'll always be grateful to hear what you think.