Mastering the Art of TIG Welding - A Comprehensive Guide
July 7, 2024
17 min read
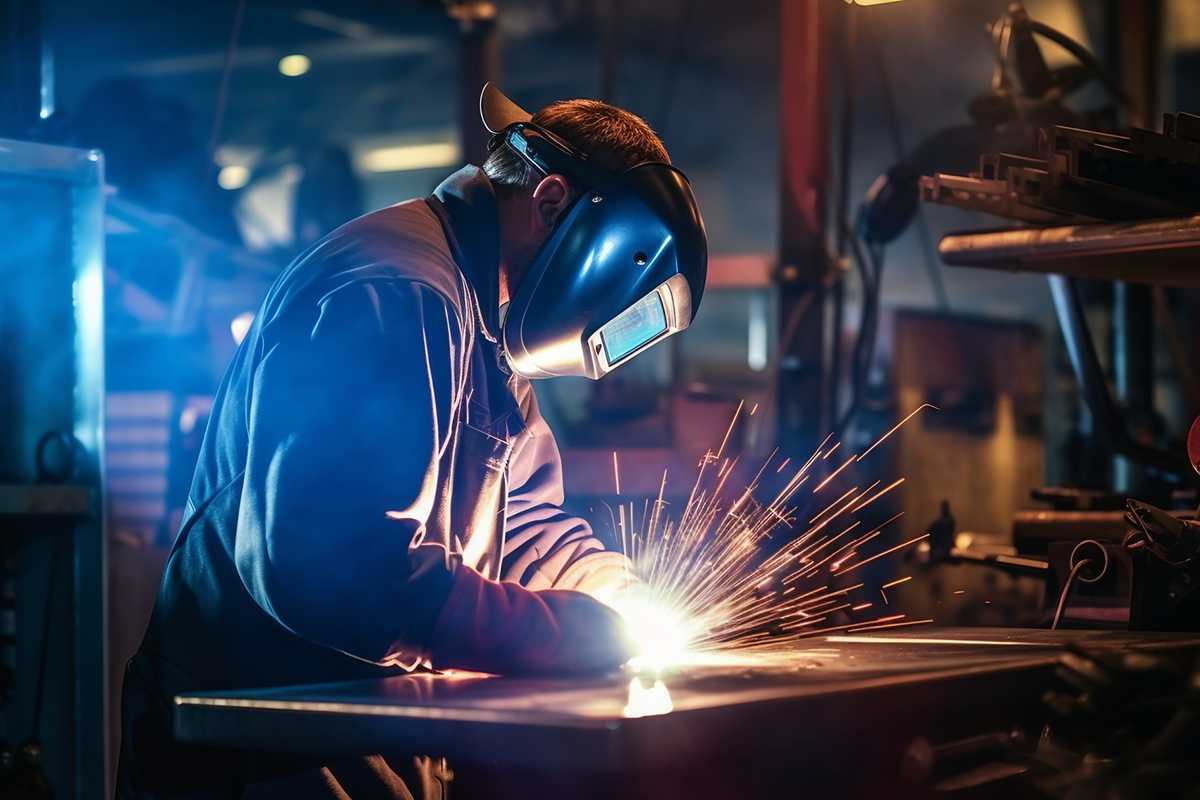
Welcome to the world of TIG welding, a craft where precision is paramount and the finish of your work speaks volumes about your skill. TIG welding, or Tungsten Inert Gas welding, is a technique that stands out for its ability to produce exceptionally clean and high-quality welds. It's a method favored in industries where the details matter just as much as the durability of the join.
The essence of TIG welding lies in its use of a non-consumable tungsten electrode, which, when combined with an inert shielding gas like argon, protects the weld from atmospheric contaminants. This fusion process creates welds that are not only aesthetically pleasing but also strong and resistant to corrosion.
This guide is designed for anyone with an interest in TIG welding, from the experienced professional seeking to perfect their craft to the beginner ready to dive into the art of welding. We'll cover everything from the basics of TIG welding to the nuances that distinguish it from other welding methods. You'll learn about its applications across various industries, the benefits it brings, and the challenges it poses. We'll also provide a detailed, step-by-step guide to help you get started with TIG welding, and we'll explore the career opportunities that await those who master this skill.
Embark on this journey with us as we delve into TIG welding, where every weld is a testament to the welder's expertise and commitment to quality.
1. The Essentials of TIG Welding: Techniques and Tools
TIG welding, also known as Tungsten Inert Gas welding, is a method that demands precision and produces high-quality finishes. It's a favorite among professionals for its clean and strong welds. The process involves a non-consumable tungsten electrode that creates the weld, while an inert gas, usually argon, shields the weld area from any contamination.
Mastering the Technique
TIG welding is all about control and finesse. It requires the welder to use one hand to manage the torch, which holds the tungsten electrode, and the other hand to feed in the filler metal. This dual-action allows for detailed work and is essential when dealing with thin materials or complex shapes. The heat needed to form the weld comes from an electric arc that is established between the electrode and the metal pieces being joined.
The type of current used in TIG welding can be either AC (alternating current) or DC (direct current). The choice depends on the material you're working with. For example, AC is typically used for welding aluminum, while DC is preferred for materials like steel and stainless steel.
A unique feature of TIG welding is the ability to control the heat input with a foot pedal or fingertip remote. This precision is crucial for preventing damage to the workpiece, especially when working with thin materials that can easily warp or burn through.
Gathering Your Equipment
To embark on TIG welding, you'll need specific tools and materials. Here's a checklist of the essentials:
- TIG Welding Machine: This is your power source and can be set to either AC or DC.
- TIG Torch: The torch holds the tungsten electrode and channels the shielding gas to the weld area.
- Tungsten Electrodes: These come in various sizes and types, each suited to different welding tasks.
- Shielding Gas: Argon is the most common choice to protect the weld from air contaminants.
- Filler Metal: This is used to add substance to the weld pool, helping to fill gaps and strengthen the joint.
- Personal Protective Equipment (PPE): Safety is paramount, so equip yourself with a welding helmet that has the right filter shade, gloves, and protective clothing to shield against UV radiation, heat, and metal splatter.
Understanding how each piece of equipment functions and choosing the right materials are key steps to achieving the best results in TIG welding. With the right setup and a solid grasp of the technique, welders can produce work that is not only structurally sound but also visually impressive.
2. TIG vs. MIG Welding: Key Differences and Considerations
When faced with a welding project, choosing the right method is crucial for success. TIG (Tungsten Inert Gas) and MIG (Metal Inert Gas) welding are two prominent techniques, each with its own set of strengths and ideal applications. Understanding their differences is essential for any welder looking to make an informed decision on which to use for their specific needs.
TIG welding is celebrated for its precision and the superior quality of its welds. It employs a non-consumable tungsten electrode to create the weld, while the welder manually adds a separate filler rod. This method is slower compared to MIG welding but provides unparalleled control, making it perfect for tasks requiring detailed work, such as in custom metal fabrication or intricate aerospace components.
Conversely, MIG welding is known for its speed and user-friendliness, especially for beginners. It utilizes a consumable wire electrode that automatically feeds through a welding gun, simultaneously dispensing a shielding gas to protect the weld from external contaminants. While MIG may not match TIG's precision, it excels in its versatility and is the go-to choice for welding thicker materials or executing long, uninterrupted welds in projects like construction or heavy industrial fabrication.
When deciding between TIG and MIG welding, consider these factors:
- Material Thickness: TIG shines with thin materials, while MIG is adept at handling thicker ones.
- Weld Quality: TIG is the winner for producing aesthetically clean and precise welds.
- Speed: MIG takes the lead in efficiency, ideal for projects under tight time constraints.
- Ease of Use: MIG's straightforward approach makes it more accessible for novices.
- Versatility: MIG's forgiving nature allows it to work with a broader array of materials.
Ultimately, the choice between TIG and MIG welding hinges on the project's specific demands, the materials in question, and the welder's expertise. TIG is the method of choice for projects where precision and finish are paramount, while MIG is favored for its quick application and ease, particularly on larger projects or with thicker materials.
3. The Versatile World of TIG Welding: From Aerospace to Art
TIG welding, with its hallmark precision and spotless finishes, is a prized technique across a spectrum of industries. It's the go-to method when both the strength and the appearance of the weld are paramount. Let's delve into the diverse applications of TIG welding, showcasing its versatility and the critical role it plays in various sectors.
Aerospace Excellence
In the high-stakes realm of aerospace, every component must be lightweight yet incredibly strong. TIG welding rises to the challenge, joining metals like aluminum and titanium—favorites in the construction of aircraft and spacecraft. The meticulous TIG process ensures each weld can endure the rigors of flight and the harshness of space.
Automotive Precision
The automotive industry depends on TIG welding for both crafting bespoke fabrications and mending parts made of aluminum and stainless steel. The technique's heat control is perfect for the thin metals found in vehicle bodies and engines, delivering welds that are as attractive as they are robust.
Artistic Creations
Metal artists and sculptors often turn to TIG welding to bring their visions to life. The method's capacity for fine detail and polished joins is ideal for sculptures and installations that captivate and inspire. With TIG welding, artists can manipulate a variety of metals, pushing the boundaries of their creativity.
Architectural Strength and Beauty
In the world of construction and architecture, TIG welding is the method of choice for crafting metal frameworks, railings, and other elements where aesthetics are crucial. It's commonly used with stainless steel and other corrosion-resistant materials, ensuring structures are not only visually appealing but also enduring, whether indoors or out.
Medical Device Precision
The medical field demands the utmost precision for the equipment that could mean the difference between life and death. TIG welding's ability to join small, delicate parts without compromising their integrity makes it indispensable in the manufacture of medical devices that adhere to stringent safety regulations.
Repair and Maintenance Versatility
TIG welding's adaptability makes it a valuable tool for maintenance teams in various industries. Whether it's fixing a piece of machinery or mending kitchen equipment in a restaurant, TIG welding's compatibility with a wide range of metals makes it a universal solution for repairs.
Marine Durability
The unforgiving marine environment requires metal structures that can resist corrosion. TIG welding is utilized in both the construction and repair of boats and ships, especially for parts made of aluminum and stainless steel that face constant exposure to saltwater. The robust, immaculate welds contribute to the vessels' safety and longevity.
In each application, TIG welding distinguishes itself by delivering top-tier, visually pleasing welds that don't sacrifice structural integrity. From the intricate requirements in medical device manufacturing to the demanding specifications of aerospace engineering, TIG welding offers unmatched precision and finish that other welding methods struggle to achieve.
4. The Balance of Benefits and Challenges in TIG Welding
TIG welding, known for its precision and versatility, is a favored technique among professionals who demand the highest quality in their welds. This section will delve into the advantages and challenges that come with TIG welding, providing a comprehensive understanding for those considering its use.
Advantages of TIG Welding
Versatility Across Metals
TIG welding's ability to join a diverse array of metals is one of its standout benefits. Whether you're working with common materials like steel and stainless steel or more exotic ones such as magnesium and copper alloys, TIG welding is up to the task. This adaptability is particularly valuable in fields where metal variety is prevalent.
Precision and Control
The precision TIG welding affords is second to none. Welders can finely control the heat and the weld pool, which is crucial for projects that involve intricate designs or delicate components. This control results in strong, high-quality welds that are aesthetically pleasing, with minimal splatter and a clean finish.
Superior Weld Quality
With TIG welding, the likelihood of encountering common weld defects such as cracking or porosity is significantly reduced. This stems from the use of a non-consumable tungsten electrode, which doesn't melt into the weld pool, thereby maintaining the purity of the materials being joined.
Cleaner Work Environment
TIG welding is also recognized for its clean operation. Since there's no need for flux, the process doesn't generate harmful smoke or fumes, creating a safer environment for welders and reducing the impact on the surrounding area.
Challenges of TIG Welding
Skill Level Requirement
Despite its many advantages, TIG welding is not without its challenges. It is a complex technique that demands a steady hand and a great deal of practice to master. This steep learning curve can be daunting for beginners or those who weld only occasionally.
Pace of Work
TIG welding is generally slower than other methods like MIG welding. The attention to detail required for its precision and quality means it may not be the most efficient choice for projects where speed is of the essence or for large-scale production.
Sensitivity to Contaminants
The quality of a TIG weld can be compromised by any contaminants present on the workpiece or filler material. This necessitates a thorough cleaning process prior to welding, which adds to the overall preparation time.
Cost of Equipment
Lastly, the initial investment for TIG welding equipment and accessories can be higher than for other welding methods. This cost can be a significant consideration for hobbyists or small operations just starting out.
In conclusion, TIG welding is a technique that offers unmatched precision and a clean work environment but requires a significant investment in terms of skill development, time, and equipment. When choosing a welding method, it's important to weigh these factors against the specific needs of your project to determine if TIG welding is the right fit.
5. Step-by-Step TIG Welding Guide: Achieving Precision and Strength
TIG welding is a meticulous process that combines precision with strength, resulting in clean and durable welds. To help you master this technique, we've compiled a comprehensive step-by-step guide that breaks down the TIG welding process into manageable stages. By following these steps, you'll be well on your way to producing welds that not only look professional but also stand the test of time.
Setting Up Your Workspace
Before you ignite the torch, it's crucial to prepare your workspace. Ensure it's tidy, has good airflow, and is devoid of any materials that could catch fire. Assemble all the gear you'll need: a TIG welder, a sharpened tungsten electrode, filler metal, and protective equipment like a welding helmet, gloves, and fire-resistant clothing.
Preparing the Metal
Next, turn your attention to the metal pieces you'll be joining. Clean them thoroughly to remove any dirt, grease, or rust. This step is vital because any impurities can weaken your weld. For thicker metals, bevel the edges to create a groove for the filler metal, which will result in a stronger bond.
Assembling Your Welder
Now, it's time to set up your TIG welder. Connect the torch, the ground clamp, and, if your model has one, the foot pedal. Choose a tungsten electrode that matches the metal you're working with and sharpen it to a fine point for precise welding. Insert it into the torch, following the manufacturer's guidelines for how far it should stick out.
The Welding Process
With everything in place, you're ready to start welding. Here's what to do:
-
Safety First: Double-check that your protective gear is on correctly and that all connections are secure.
-
Adjust Settings: Tailor your TIG welder's settings to the metal's thickness and type. If your welder has a foot pedal, get comfortable with it, as you'll use it to regulate the heat during welding.
-
Tack Welds: Begin by placing several tack welds along the joint. These small welds act like pins, holding the pieces together and preventing them from warping as you work.
-
Start Welding: Position yourself at one end of the joint. Hold the torch in one hand and the filler rod in the other. Strike the arc with the foot pedal or a lift start, depending on your welder model.
-
Maintain the Arc: Keep the arc length consistent, about as thick as the electrode itself. Introduce the filler metal into the weld pool with a dabbing motion—don't drag it through.
-
Control the Heat: Use the foot pedal to adjust the heat input. Too much heat can warp the metal or burn through it, while too little can result in a weak weld. Observe the weld pool and adapt your heat input as needed.
-
Finish Strong: When you reach the end of the weld, gradually decrease the current to let the weld pool cool and solidify smoothly. If your welder has a post-flow feature, use it to protect the weld and electrode as they cool.
-
Inspect and Clean: Once the weld has cooled, examine it for any flaws, such as cracks or gaps. Clean the weld area with a wire brush to remove any oxidation or leftover residue.
By carefully following these steps and dedicating time to practice, you'll develop the ability to create strong, visually appealing TIG welds. Remember, TIG welding is as much about artistry as it is about technique, so be patient as you refine your skills.
6. Navigating a Career in TIG Welding: Opportunities, Training, and Growth
TIG welding isn't just a technical skill—it's a craft that can lead to a fulfilling career with a multitude of opportunities in various high-demand industries. Whether it's joining the sleek body of an airplane or crafting a custom piece of art, TIG welders are sought after for their precision and expertise. In this section, we'll explore the career paths available to TIG welders, the training required to enter the field, and the potential for growth and specialization.
Career Opportunities in Diverse Industries
TIG welding skills open doors to careers in sectors that value detailed and high-quality metalwork. Aerospace companies need welders to assemble aircraft with lightweight metals like titanium and aluminum. The automotive industry looks for TIG welders to create custom parts and perform delicate repairs. Even artists seek out TIG welders to help bring their metal sculptures to life. Other industries that rely on TIG welding include maritime for shipbuilding and repairs, and the medical field for creating precise surgical tools.
Training: The First Step to Mastery
To start a career in TIG welding, you'll need the right training. Vocational schools and community colleges often offer welding programs that teach the fundamentals of TIG welding, including both the theory behind the technique and hands-on practice. These programs also emphasize safety in welding, which is crucial for any professional in the field.
The Importance of Certification
Certification is a key milestone for TIG welders. It's like a stamp of approval on your skills. The American Welding Society (AWS) is one of the organizations that offer certifications, such as the Certified Welder program. Being certified can lead to better job opportunities and higher pay.
Advancing Your Career Through Continuous Learning
The welding industry is always changing, with new technologies and materials constantly emerging. To keep up and advance in your career, it's important to continue learning. This could mean taking additional courses, attending workshops, or getting more certifications. Staying current with industry trends can lead to higher positions, such as a welding inspector or supervisor, and for some, it might even lead to starting their own welding business.
Experience: The Path to Specialization and Complex Projects
As with many crafts, experience in TIG welding is invaluable. Over time, as you work on a variety of projects and face different challenges, your skills will sharpen. You might find yourself specializing in a particular type of metal or welding technique, which can make you stand out in the job market. Experienced welders often take on more complex and higher-paying projects, further advancing their careers.
In conclusion, TIG welding offers a rich career path with plenty of room for growth. With the right training, certification, and a commitment to ongoing education, a welder can not only secure a place in the industry but also climb the ladder to more advanced and rewarding positions. Whether you're just starting out or looking to expand your expertise, the world of TIG welding is full of potential.
7. Conclusion: The Art and Science of TIG Welding
As we conclude this comprehensive guide, it's evident that TIG welding is more than just a method of joining metals—it's a fusion of art and science. This technique, with its unmatched precision and aesthetic finesse, is a testament to the skill and dedication of the welder. Throughout this guide, we've journeyed through the fundamentals of TIG welding, comparing it with other methods like MIG welding and highlighting its unique advantages in producing superior finishes.
We've seen how TIG welding's meticulous nature makes it the preferred choice in industries where detail and quality are non-negotiable, such as aerospace and custom automotive work. Its application in art and architecture underscores its versatility and the beauty it can bring to metalwork. The guide has also addressed the challenges inherent to TIG welding, from its steep learning curve to the need for thorough surface preparation, offering a realistic view of what it takes to excel in this craft.
For those aspiring to a career in TIG welding, the path is clear: proper training, practice, and a commitment to ongoing learning are essential. The demand for skilled TIG welders is robust, with opportunities spanning from intricate artistic endeavors to cutting-edge industrial projects.
In mastering TIG welding, you embrace a craft that requires a blend of patience, precision, and an eye for detail. It's a journey of continuous learning, where each weld is an opportunity for improvement and each project a chance to showcase your evolving skills. Whether you're starting as a hobbyist or honing your professional expertise, TIG welding offers a rewarding pathway to both personal satisfaction and professional advancement. With dedication and practice, the world of TIG welding is yours to shape and create enduring works of metal that are as strong as they are striking.
Sharing is Caring
Feedback
At WeldWins, we know we aren't perfect which is why we're always looking for ways to improve. You can help us do better by taking 2 minutes to fill out our simple feedback form.
Any and all feedback is welcome. It could be a complaint, an idea, or even just a comment, we'll always be grateful to hear what you think.