Mastering Aluminum Stick Welding - A Comprehensive Guide
April 28, 2024
10 min read
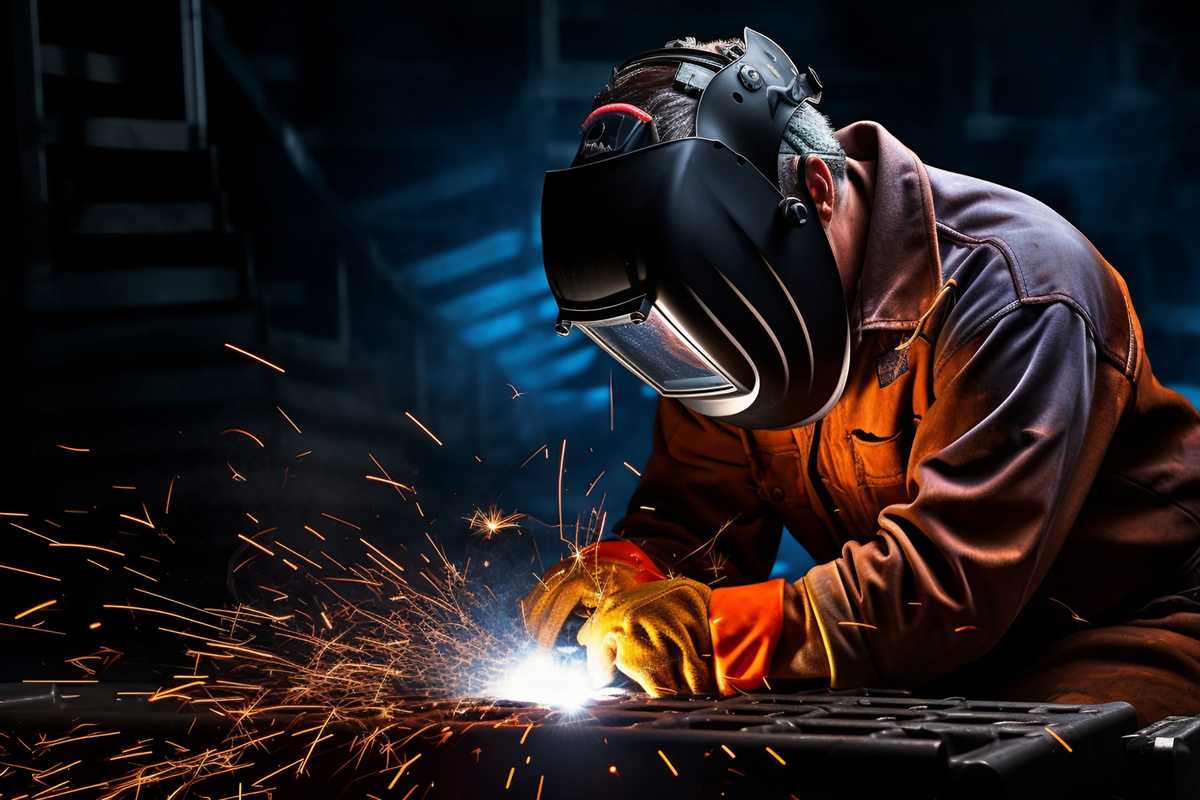
1. Demystifying Aluminum Stick Welding: An Introductory Guide
The notion that stick welding aluminum is a herculean task is widespread among welders. Some even deem it an unattainable skill. However, this guide is set to challenge those beliefs and demonstrate that, with the right knowledge and approach, stick welding aluminum is not only possible but can be highly effective. Our goal is to clear up misconceptions and provide a detailed walkthrough for those eager to learn or perfect this technique.
We will dissect the unique characteristics of aluminum that make welding it a distinct challenge. The guide will cover essential topics such as the meticulous preparation of the metal surface, the careful selection of appropriate electrodes, and a detailed, step-by-step guide to the stick welding process for aluminum. We'll also share valuable tips on mastering the welding technique and managing the heat effectively, address common pitfalls, and draw comparisons with other welding methods like MIG and TIG.
This guide is crafted for both the enthusiast looking to broaden their welding skills and the seasoned professional aiming to polish their technique. By the end of this journey, you'll be equipped with the knowledge and practical know-how to produce robust, enduring welds with a stick welder on aluminum. Let's begin this educational journey into the world of aluminum stick welding.
2. Navigating the Complexities of Aluminum Welding
Aluminum is a popular material in manufacturing and construction due to its impressive strength-to-weight ratio and resistance to corrosion. Yet, when it comes to welding, it poses unique challenges that set it apart from other metals like steel. For those keen on mastering aluminum stick welding, a deep understanding of these challenges is essential.
One of the main hurdles with aluminum is its high thermal conductivity. This property means that aluminum spreads heat quickly, which can cause the heat necessary for welding to dissipate too fast. This results in an inconsistent weld pool, making it difficult to achieve a strong weld. To counter this, welders often have to increase the amperage settings, ensuring enough heat is concentrated to form a stable weld pool.
Another obstacle is the stubborn oxide layer that forms on aluminum when it's exposed to air. This layer is beneficial for preventing corrosion but has a higher melting point than the aluminum beneath it—approximately 3,700 degrees Fahrenheit compared to aluminum's 1,200 degrees Fahrenheit. Before welding, this layer must be meticulously removed to avoid weld contamination and to ensure a solid bond is formed.
The oxide layer can also impede the welding process by obstructing electron flow, leading to an unstable arc. If not removed correctly, it can get trapped in the weld, causing porosity—tiny holes that weaken the weld's integrity.
Aluminum's sensitivity to heat introduces another challenge: warping and distortion. This is particularly problematic for thin aluminum pieces, which can warp dramatically if not handled with care. Welders need to be strategic about heat management, employing techniques like using a heat sink or welding in short bursts to mitigate warping.
Lastly, aluminum's softness can cause issues with feeding the electrode during welding, and the risk of hydrogen contamination can lead to porosity, compromising the weld's strength. Proper storage of aluminum electrodes and adherence to precise welding techniques are critical to prevent these problems.
In essence, the key challenges in welding aluminum are its rapid heat conduction, the presence of an oxide layer, its tendency to warp under heat, and the risk of hydrogen-induced porosity. By understanding and preparing for these issues, welders can adapt their techniques to produce durable and reliable aluminum welds.
3. The Practical Guide to Stick Welding Aluminum
Stick welding aluminum may seem daunting, but with a methodical approach, you can produce durable and clean welds. This practical guide will walk you through each step, ensuring you understand how to tackle the task with confidence.
Equipment and Safety First
Before diving into the welding process, it's crucial to set up your equipment correctly for aluminum welding. Verify that your welding machine can handle AC (alternating current), which is essential for effectively breaking down the aluminum's oxide layer. Inspect all components, including the electrode holder and ground clamp, for damage. Safety is paramount, so gear up with a welding helmet that has the right filter shade, fire-resistant clothing, gloves, and boots to protect yourself from sparks and intense light.
Choosing the Right Electrode
Selecting the appropriate electrode is vital for a successful weld. For aluminum, you'll want an electrode like the E4043, which is designed with a special flux coating to facilitate stable arc creation. This electrode also has a lower melting point to reduce the risk of burning through the material. Make sure your electrodes are stored in a dry environment to prevent moisture, which can cause weld defects such as porosity.
Dialing in the Welder Settings
Aluminum's high thermal conductivity means you'll need to adjust your welder to a higher amperage compared to welding steel. The correct setting depends on the aluminum's thickness and the chosen electrode. Start with the manufacturer's recommended settings and tweak as necessary for your specific project.
Preparing the Aluminum Surface
A clean surface is key to a strong weld. Begin by removing any contaminants, oils, or dirt from the aluminum. Then, take a stainless steel brush—reserved exclusively for aluminum—to scrub off the oxide layer on the welding area. This step ensures a clean, contaminant-free surface for welding.
Initiating the Arc
Starting an arc on aluminum requires a bit more finesse due to the oxide layer's resistance. Use a scratching motion with the electrode against the workpiece to ignite the arc. You might need to increase the amperage to overcome the oxide layer's resistance.
Managing the Arc and Weld Pool
Once the arc is lit, keep the arc length short to avoid overheating and weakening the weld. Angle the electrode slightly, about 15 degrees, in the direction you're welding to help guide the molten pool.
Controlling Travel Speed and Heat
Because aluminum conducts heat away quickly, it's important to find a balance in your travel speed. Move too slowly, and you risk burn-through; too quickly, and the weld won't fuse properly. If the metal gets too hot, pause to let it cool before proceeding.
Finishing Up
After you've completed the weld, let the piece cool down naturally. Quenching in water can cause cracking due to thermal stress. Once cool, inspect the weld for any imperfections and clean up the bead with a file or grinder if needed.
By following these detailed steps, you'll be on your way to mastering stick welding aluminum. Practice makes perfect, so hone your skills on scrap material before moving on to more complex projects.
4. Exploring Welding Alternatives for Aluminum
While stick welding has its place in the aluminum joining toolbox, it's not the only method at a welder's disposal. It's crucial to be aware of the alternatives, as each project may call for a different approach. In this section, we'll delve into two widely-used welding processes—MIG and TIG welding—and discuss how they stack up against stick welding when it comes to working with aluminum.
MIG Welding: The Fast and User-Friendly Option
MIG welding stands out for its speed and user-friendliness, making it a go-to choice in many industrial applications. When it comes to aluminum, using a spool gun or a push-pull gun is common practice to overcome wire feeding challenges. The continuous wire feed characteristic of MIG welding simplifies the process of laying down long welds without interruption.
Advantages of MIG welding aluminum include:
- Quick welding speeds that boost productivity.
- A straightforward learning curve, particularly for novices.
- Optimal for thin aluminum sheets, resulting in a clean finish with minimal post-weld cleanup.
However, MIG welding isn't without its drawbacks:
- The setup is more intricate, requiring a compatible MIG welder and the right shielding gas.
- Portability is compromised compared to stick welding, which can be a setback for on-site repairs.
- It may struggle with thicker aluminum sections where stick welding might excel.
TIG Welding: Precision and Quality for Complex Projects
For projects demanding precision and a high-quality finish, TIG welding is often the method of choice. This technique uses a non-consumable tungsten electrode, renowned for producing strong, aesthetically pleasing welds on aluminum.
The benefits of TIG welding aluminum are:
- Exceptional weld quality with a neat, precise bead.
- Enhanced control over the heat and weld pool, minimizing the risk of distortion and burn-through.
- A clean process with no spatter and little need for post-weld cleanup.
On the flip side, TIG welding presents its own set of challenges:
- It's a slower process compared to MIG and stick welding, which may not be ideal for large-scale production.
- It demands a higher skill level due to the need to manage the torch, filler material, and foot pedal all at once.
- The equipment can be more expensive, and the technique is less tolerant of any surface impurities.
Making an Informed Choice
Deciding whether to use stick, MIG, or TIG welding for an aluminum project involves weighing factors such as material thickness, weld quality requirements, equipment availability, and the welder's expertise. Stick welding might be the answer for quick fixes or situations where equipment mobility is key. MIG welding could be the better choice for projects prioritizing speed and simplicity, especially with thinner materials. For precision work demanding the highest quality, TIG welding is often the preferred route.
Each welding process has its unique advantages and challenges. By understanding these alternatives, welders can make educated choices and select the most suitable method for their specific aluminum welding needs.
5. Perfecting Your Aluminum Stick Welding Technique: A Summary
Embarking on the path to proficient aluminum stick welding is a journey of dedication and skill-building. This comprehensive guide has aimed to arm you with the essential knowledge and practical steps necessary to navigate the complexities of welding this versatile but challenging metal. From understanding aluminum's unique properties to meticulously preparing the surface and selecting the right electrode, each aspect plays a pivotal role in the success of your welding projects.
Throughout your practice, remember that controlling the arc length and travel speed is critical to prevent common issues like warping and cracking. It's also important to be vigilant and ready to troubleshoot any problems that arise, as this will not only fix immediate issues but also contribute to your long-term development as a skilled welder.
While this guide has focused on stick welding, don't forget to consider other welding methods such as MIG and TIG for certain projects. These techniques may offer advantages in precision and finish that stick welding cannot match, especially when working with various aluminum alloys or when a higher degree of detail is required.
We trust that the insights and instructions provided here will serve as a solid foundation for your aluminum stick welding endeavors. As you continue to weld, each bead laid down is a step closer to mastery. Keep honing your skills, adhere to safety protocols, and embrace the continuous learning process that defines the craft of welding. Your dedication to the art will undoubtedly lead to stronger, more reliable welds and a rewarding sense of accomplishment in your work.
Sharing is Caring
Feedback
At WeldWins, we know we aren't perfect which is why we're always looking for ways to improve. You can help us do better by taking 2 minutes to fill out our simple feedback form.
Any and all feedback is welcome. It could be a complaint, an idea, or even just a comment, we'll always be grateful to hear what you think.