What is Pulse MIG Welding and How Can It Transform Your Metalwork?
June 27, 2024
9 min read
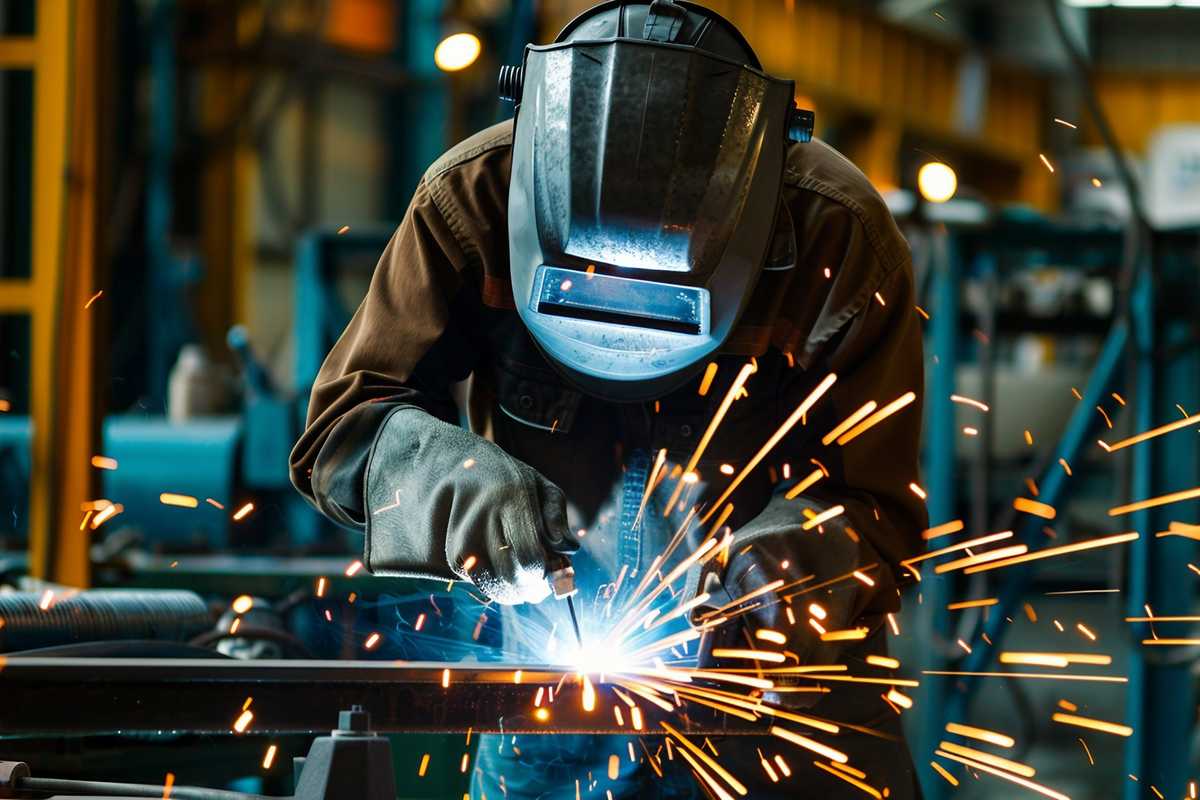
Embark on a journey through the innovative world of Pulse MIG welding, a technique that's transforming metalwork with its precision and versatility. Ideal for both experienced welders and those new to the craft, Pulse MIG welding offers a way to achieve cleaner, stronger welds across a variety of projects. In this comprehensive guide, we'll explore the essentials of Pulse MIG welding, from its unique benefits to the specialized equipment needed. Get ready to unlock the potential of this advanced welding method and take your metalworking skills to the next level.
1. Mastering the Technique of Pulse MIG Welding
Pulse MIG welding is an advanced form of welding that enhances the precision and quality of metal joints. Unlike traditional MIG welding, which uses a constant stream of electricity, Pulse MIG welding operates by rapidly switching between high and low electrical currents. This pulsing action allows for meticulous control over the heat applied to the metal, leading to stronger and more consistent welds.
Imagine Pulse MIG welding as an artist using fine brush strokes to create a detailed painting. The high peak current acts like a bold stroke that melts the metal, forming a pool that fuses the pieces together. Then, as the artist pauses to let the paint settle, the low background current gives the molten pool a moment to cool, preventing overheating and reducing the risk of warping or burn-through.
This method is particularly beneficial when working with thin or heat-sensitive metals, as it minimizes the chance of damaging the material. It's also versatile, allowing welders to work in various positions—whether on a flat surface or overhead—without sacrificing the quality of the weld.
To start Pulse MIG welding, you'll need to set up your welding machine with the right parameters, such as pulse frequency and current levels. These settings depend on the metal type and the desired weld quality. For example, welding aluminum might require different settings than welding stainless steel.
During the welding process, the equipment alternates between the two current levels. The high peak current penetrates deeply to create a robust weld, while the low background current lets the metal cool, solidifying the joint and preventing deformities.
In essence, Pulse MIG welding is a sophisticated technique that offers welders greater command over their work. By grasping its fundamental principles and how it differs from traditional MIG welding, you can leverage its advantages to produce top-notch, precise welds that are both strong and visually appealing.
2. Elevating Metalwork with Pulse MIG Welding Benefits
Pulse MIG welding is a game-changer in the metal fabrication industry, offering a suite of benefits that enhance the quality and efficiency of welding projects. This section highlights the key advantages that make Pulse MIG welding a standout choice for professionals seeking to refine their craft.
One of the most significant benefits of Pulse MIG welding is its ability to maintain low heat input. This is particularly advantageous when welding thin or complex pieces, as it reduces the likelihood of warping or altering the shape of the metal. By carefully managing the heat, the structural strength of the metal is preserved, resulting in durable and dependable welds.
Another advantage is the reduction of spatter, the pesky droplets of metal that can scatter during welding. Pulse MIG welding keeps the work area cleaner and saves time on post-weld cleanup, which is especially valuable when the final appearance of the weld is critical, such as in automotive or consumer product manufacturing.
The aesthetic quality of welds is also improved with Pulse MIG welding. The technique allows for greater control over the molten pool, leading to smooth, uniform weld beads that are visually appealing. This is essential in industries where the look of the weld is just as important as its strength.
Control is a recurring theme with Pulse MIG welding. The ability to fine-tune the peak and background currents gives welders the power to tailor the welding parameters to the specific needs of each job. This precision is key in achieving consistent, high-quality welds, particularly in jobs that demand exactitude.
Versatility is another hallmark of Pulse MIG welding. It's effective on a range of metals, including aluminum, stainless steel, and various alloys, making it a versatile tool for industries like aerospace and construction that use diverse materials.
Finally, Pulse MIG welding can boost productivity. It's generally faster than traditional MIG welding, allowing for quicker completion of tasks without sacrificing weld quality. This speed can lead to cost savings and increased output for businesses.
In essence, Pulse MIG welding excels in providing lower heat input, minimal spatter, better-looking welds, precise control, material versatility, and improved productivity. These benefits position Pulse MIG welding as an attractive option for those looking to enhance their welding processes and achieve superior results, no matter the scale of the project.
3. Selecting the Ideal Pulse MIG Welding Equipment
To excel in Pulse MIG welding, the right tools are indispensable. The equipment you choose directly influences the finesse and strength of your welds. Let's delve into the essentials of Pulse MIG welding machines and what to consider when selecting the perfect one for your needs.
Understanding Pulse MIG Welder Varieties
Pulse MIG welders come in two primary types, each catering to different skill levels and preferences:
-
Synergic Pulse MIG Welders: These user-friendly devices are a boon for welders at all levels. They automatically adjust welding parameters to match the wire feed speed and material thickness, simplifying the process and promoting uniform results.
-
Non-Synergic Pulse MIG Welders: For those who prefer a hands-on approach, these welders offer manual control over pulse settings. They're ideal for seasoned welders who demand precise control but require a bit more expertise to operate effectively.
Essential Features for Top-Notch Welding
When shopping for a Pulse MIG welder, keep an eye out for these critical features:
-
Pulse Frequency Adjustment: This feature lets you dictate the pulse rate, which you can customize based on the metal type and its thickness for optimal results.
-
Peak and Background Current Control: Fine-tuning the currents helps manage the heat and shape the weld bead, crucial for achieving the look and strength you desire.
-
Programmable Memory Settings: Some welders offer memory slots to save your settings, streamlining the setup for recurring jobs and ensuring consistency.
-
Digital Display and Controls: A clear interface and straightforward controls make it easier to tweak settings and keep an eye on the welding process.
Balancing Quality with Budget
Pulse MIG welders range from feature-rich, high-end models to more affordable, basic ones. The high-end options offer precision, a plethora of programmable features, and durability for heavy-duty use. They're a fit for industrial settings where the equipment sees regular use.
Conversely, budget-friendly models, while less feature-packed, can still perform admirably for smaller operations or hobbyists who don't need all the bells and whistles.
When deciding on a welder, weigh the complexity of your projects, how often you'll use the machine, and how much you're willing to invest. It's about finding the sweet spot between cost and the features that will genuinely enhance your welding work.
In essence, the right Pulse MIG welder can make a world of difference in your welding projects. By understanding the types of welders, the must-have features, and the balance between price and functionality, you can select a machine that will help you harness the full potential of Pulse MIG welding for consistently excellent welds.
4. Comparing Pulse MIG Welding to Conventional Methods
Welding professionals have a toolbox of methods at their disposal, each suited to different tasks. Pulse MIG welding is a standout technique that's often weighed against traditional MIG and TIG welding. Let's break down how Pulse MIG differs and why it might be the best choice for certain projects.
The Basics of Traditional MIG Welding
Traditional MIG welding is a go-to for its quick pace and simplicity. It involves a steady wire feed and a fixed voltage to fuse metal. It's great for joining thinner metals fast, but it's not without its downsides. More spatter can occur, and the continuous heat can distort the metal pieces being joined.
The Precision of TIG Welding
TIG welding is the method of choice for jobs needing meticulous attention to detail. It uses a tungsten electrode that doesn't melt away, making it perfect for delicate or very thin materials. TIG gives you a lot of control, but it's slower and demands more skill from the welder.
The Advantages of Pulse MIG Welding
Pulse MIG welding shines with its pulsing current, which switches between high and low levels. This unique feature allows for precise heat management, reducing warping risks and minimizing spatter—meaning less cleanup. It's like having the control of TIG with the speed of traditional MIG, plus it's easier to pick up for beginners.
Pulse MIG can handle a variety of metals, including tricky ones like aluminum and stainless steel, which can be a challenge for standard MIG methods. It's a versatile option that balances speed, ease, and quality.
In a nutshell, Pulse MIG welding is a middle-of-the-road technique that offers the quickness of traditional MIG with a level of precision close to TIG welding. It's a controlled, cleaner way to weld that can handle a range of materials. For welders aiming to step up their game, Pulse MIG is a technique worth exploring.
5. Harnessing the Future of Welding: Embrace Pulse MIG Welding
In the realm of metal fabrication, Pulse MIG welding emerges as a cutting-edge technique that significantly enhances the quality and efficiency of your welding endeavors. This innovative method, with its dynamic control over peak and background currents, offers unparalleled precision, leading to less distortion and a more refined weld finish. The strategic reduction of spatter and the heightened command over the weld pool are among the many reasons why Pulse MIG welding is becoming an indispensable skill for welders in diverse sectors.
For those faced with the challenges of working on delicate materials or intricate welding tasks, Pulse MIG welding provides an effective solution where conventional MIG welding falls short. The availability of equipment tailored to various budgets—from premium, feature-rich models to cost-effective, essential units—ensures that the benefits of Pulse MIG welding are accessible to all.
As you gear up for your upcoming welding projects, consider the distinct advantages that Pulse MIG welding offers. It's not merely a method for joining metals; it's a craft that, when mastered, results in robust, visually striking welds that reflect a superior level of workmanship. Step into the future of welding by adopting Pulse MIG welding, and watch as it revolutionizes your approach to metalwork.
Sharing is Caring
Feedback
At WeldWins, we know we aren't perfect which is why we're always looking for ways to improve. You can help us do better by taking 2 minutes to fill out our simple feedback form.
Any and all feedback is welcome. It could be a complaint, an idea, or even just a comment, we'll always be grateful to hear what you think.