Mastering MIG Welding Aluminum - A Comprehensive Guide
April 28, 2024
13 min read
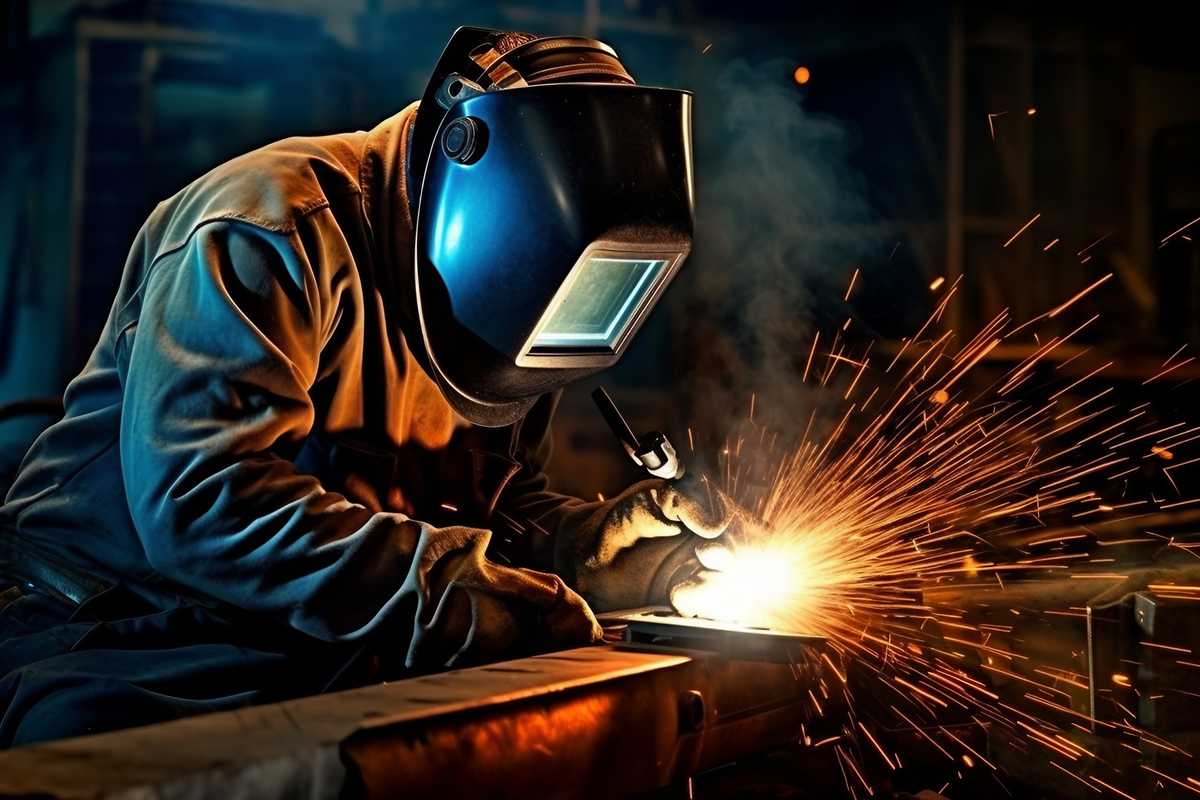
Introduction
Embarking on the journey of MIG welding aluminum can be a rewarding endeavor for both seasoned professionals and enthusiastic hobbyists. Known for its lightweight yet strong characteristics, aluminum is a favored material in various industries. MIG welding serves as an efficient technique to join aluminum parts, but it comes with its own set of challenges that differ from welding other metals like steel.
The high thermal conductivity and lower melting point of aluminum mean that it reacts to heat much faster, which can lead to complications such as warping or burn-through if not handled correctly. Additionally, aluminum is prone to forming a stubborn oxide layer when exposed to air, complicating the welding process due to its higher melting point than the aluminum itself.
This article is designed to navigate you through the complexities of MIG welding aluminum. We'll cover the essential steps and strategies to tackle common issues like managing heat, dealing with the oxide layer, and achieving clean, robust welds. Whether you're just starting out or aiming to refine your existing skills, the insights provided here will help you consistently produce superior welds with aluminum.
2. Navigating Aluminum's Welding Quirks
Aluminum's allure in industries from automotive to aerospace is undeniable, given its lightweight yet robust nature. However, its welding process is not without its quirks. As we delve into the intricacies of MIG welding aluminum, it's crucial to understand and adapt to these peculiarities to ensure strong, defect-free welds.
Aluminum's high thermal conductivity is a double-edged sword. While it's beneficial for applications requiring quick heat dissipation, it poses a challenge for welders. The rapid heat transfer away from the weld zone can result in uneven heating and cooling, potentially causing warping or, worse, burn-through. To counter this, welders must fine-tune their heat management skills, ensuring a consistent temperature throughout the welding process.
The metal's lower melting point, when juxtaposed with its quick heat conduction, demands a swift and skilled welding hand. Welders must work at a brisk pace, avoiding excessive heat buildup that could undermine the weld's integrity.
A notorious hurdle in aluminum welding is its propensity to form an oxide layer when exposed to air. This stubborn layer, melting at a higher temperature than the aluminum beneath, can thwart the welding process by preventing a clean fusion between the base metal and the filler material. Left unaddressed, it can introduce porosity—tiny gas pockets that weaken the weld. To combat this, the oxide layer must be meticulously removed before welding, using a stainless steel brush or a chemical solvent designed for aluminum. Timing is of the essence here, as the oxide layer can swiftly reform.
Moreover, aluminum's sensitivity to impurities surpasses that of steel. Traces of oil, moisture, or dirt can lead to weld defects. A thorough cleaning of the aluminum workpiece is paramount before initiating the welding process.
By grasping these welding challenges unique to aluminum, welders can arm themselves with the right techniques and precautions. This knowledge is the cornerstone of mastering MIG welding aluminum, paving the way for durable and reliable welds.
3. Essential Preparation for MIG Welding Aluminum
Before igniting the welding arc, the preparation of aluminum surfaces is a pivotal step that directly impacts the strength and appearance of your welds. Properly preparing aluminum can prevent common welding problems such as porosity, which are tiny holes that weaken the weld, and lack of fusion, where the weld does not properly bond with the base metal.
Thorough Cleaning: The First Line of Defense Against Weld Defects
Aluminum is notorious for its quick formation of an oxide layer when exposed to the atmosphere. This layer is stubborn and has a higher melting point than aluminum itself, which can obstruct the welding process. To combat this, begin with a meticulous cleaning regimen. Use a stainless steel wire brush specifically for aluminum to scrub along the grain of the metal. This action helps dislodge the oxide layer without leaving behind any foreign metal particles.
After brushing, it's crucial to eliminate any residual contaminants that could compromise the weld. Wipe down the surface with a clean rag soaked in acetone or a commercial aluminum cleaner. This step ensures the removal of oils, dirt, and moisture. Remember to wear gloves to prevent transferring oils from your skin onto the metal.
Selecting the Right Tools and Consumables for a Flawless Weld
Equally important to the cleaning process is the selection of appropriate welding equipment and materials. The right choices here can lead to smoother welding experiences and superior weld quality.
Welder Selection: Power and Precision
Choose a MIG welder that's up to the task of handling aluminum's unique properties. A welder with pulse welding capabilities is advantageous, as it allows for precise control over the heat input, which is particularly useful for welding thin aluminum sheets without causing burn-through. Ensure that the welder can deliver enough power for the thickness of the aluminum you're working with.
Filler Wire: Matching Material and Strength
The filler wire is a critical component in MIG welding aluminum. The two most commonly used wires are ER4043, which is known for its excellent weldability and reduced risk of cracking, and ER5356, which is stronger but more susceptible to cracking and is often used for welding 5xxx series aluminum alloys. Your choice should be based on the base material and the mechanical properties needed for the weld.
Shielding Gas: Creating the Perfect Environment for Welding
Argon is the go-to shielding gas for MIG welding aluminum due to its ability to produce a stable arc and clean the weld area. For thicker pieces or when you need to weld faster, a mixture of argon and helium can provide deeper penetration and improve the fluidity of the weld pool. However, be cautious with helium as it can make the arc less stable, so it's important to adjust your technique accordingly.
Wire Feeding: Ensuring Consistency and Reliability
Aluminum wire is softer and more prone to feeding problems than steel wire. To prevent issues, consider using a spool gun, which holds a small spool of wire close to the torch to reduce the feeding distance. Alternatively, a graphene liner in your MIG gun can decrease friction and facilitate smoother wire feeding in a standard setup.
By dedicating time to proper aluminum preparation and selecting the right welding equipment and materials, you lay the groundwork for successful MIG welding. Clean surfaces, a capable welder, the right filler wire, the correct shielding gas, and smooth wire feeding are the cornerstones of achieving strong, defect-free aluminum welds.
4. Mastering MIG Welding Techniques for Aluminum
When it comes to MIG welding aluminum, the right techniques can make all the difference. Aluminum's distinct characteristics mean that you can't approach it the same way you would steel. Let's break down the essential steps to ensure your aluminum welds are not only strong but also aesthetically pleasing.
4.1. Optimal Welder Configuration
To start, your MIG welder needs to be fine-tuned for aluminum. Here's what to focus on:
- Wire Feed Speed: Aluminum wire is more pliable than steel wire, which means it feeds differently through the welder. Set a higher wire feed speed to avoid clogging and to maintain a consistent arc.
- Voltage Settings: The thickness of your aluminum piece dictates the voltage required. Thicker pieces need more voltage for the weld to penetrate deeply enough.
- Polarity: Set your MIG welder to direct current electrode positive (DCEP) for effective aluminum welding.
4.2. Balancing Speed and Temperature
Aluminum heats up and cools down rapidly, so managing your travel speed and heat input is critical. If you move too slowly, you might overheat the metal and cause a burn-through. If you move too quickly, the weld might not penetrate enough, resulting in a weak joint. Practice on scrap aluminum to get a feel for the right speed for your project.
4.3. Achieving the Ideal Metal Transfer
Spray transfer is your goal for a smooth aluminum weld. It's a technique where tiny droplets of molten metal are sprayed across the arc. To get there:
- Gas Mix: Use pure argon or a blend of argon and helium to maintain a stable arc and facilitate spray transfer.
- Machine Settings: Increase both voltage and amperage compared to what you'd use for short-circuit welding to encourage a steady flow of metal to the weld pool.
4.4. The Push Technique: A Clearer View for Better Welds
The push technique is a welder's best friend for aluminum. By pushing the torch forward, you get:
- Enhanced Shielding Gas Coverage: This reduces oxidation and contamination.
- Visibility: You can see the weld pool more clearly, which helps you control the weld bead's shape and quality.
- Less Porosity: Pushing the torch can help avoid porosity, which are those pesky air pockets that weaken the weld.
4.5. Keeping Distortion at Bay
Aluminum's quick reaction to heat means it can warp if you're not careful. To prevent this:
- Stabilize with a Jig or Fixture: This keeps your workpieces in place and aligned.
- Segment Your Welds: Tack weld first, then complete your welds in shorter stretches, allowing cooling periods in between to minimize heat buildup.
- Spread the Heat: Alternate your welding spots along the joint to distribute the heat more evenly and avoid warping.
By incorporating these techniques into your MIG welding routine, you'll be better prepared to tackle the unique challenges of aluminum. Practice is essential, so work with scrap pieces to refine your skills before moving on to more critical projects. And never forget the importance of safety—always wear the right protective gear when welding.
5. Overcoming Specific MIG Welding Challenges with Aluminum
MIG welding aluminum can sometimes feel like navigating a minefield of potential issues. But with the right knowledge and a few clever tricks, you can defuse these problems and achieve a clean, strong weld. Let's dive into some common challenges and the practical solutions to overcome them.
5.1. Avoiding Burn-Through
The combination of aluminum's high heat conductivity and low melting point can be a recipe for burn-through, particularly with thin materials. Here's how to avoid it:
- Dial Down the Power: Use the lowest welding current and voltage that still allows for a stable arc. This reduces the heat input and minimizes the risk of melting through the metal.
- Pick Up the Pace: Move your welding gun more quickly than you might with steel. This spreads the heat out and prevents it from concentrating in one spot.
- Back It Up: Use a backing plate made of a thicker aluminum piece behind your weld. This acts as a heat sink, drawing away excess heat and preventing burn-through.
5.2. Ensuring Clean Welds
Dirty welds are not just unsightly; they're structurally weak. Aluminum is particularly sensitive to contamination, but you can keep it clean with these steps:
- Scrub-a-Dub-Dub: Before you strike an arc, take a stainless steel brush (only used for aluminum) and give the welding area a good scrub to remove the oxide layer and any other contaminants.
- Gas Flow Is Key: Double-check your shielding gas flow before starting. A consistent flow of argon gas is essential to protect the weld pool from the air, which can lead to a dirty weld.
- Dry as a Bone: Aluminum absorbs moisture, which can lead to hydrogen in your weld and cause porosity. Keep your metal and filler wire dry to avoid this issue.
5.3. Tackling Wire Feeding Snags
Aluminum wire is notoriously soft and can be a hassle to feed through a MIG gun. Here's how to keep it moving:
- Shorten the Path: Use a spool gun, which holds the wire close to the torch, or a graphene liner in your MIG gun to reduce the distance the wire has to travel, preventing tangles and jams.
- Straighten Up: Keep the MIG gun's cable as straight as possible to ease the wire's journey.
- Just the Right Grip: Adjust the tension on the wire spool and the drive rolls. Too tight, and you'll crush the wire; too loose, and it won't feed properly.
By tackling these common MIG welding challenges head-on with the right techniques, you'll be on your way to producing top-notch aluminum welds. Regular maintenance of your equipment and sticking to these best practices will help you avoid these issues in the first place. Remember, every welder encounters problems from time to time, but with practice and patience, you'll learn to quickly identify and fix them, enhancing your MIG welding prowess.
Wrapping Up: Your Path to Aluminum MIG Welding Mastery
In this comprehensive guide, we've journeyed through the nuances of MIG welding aluminum—a skill that marries the science of metallurgy with the art of craftsmanship. By now, you should have a solid understanding of the techniques and considerations that are key to producing strong, visually appealing welds on this versatile metal.
Let's recap the critical points that will help you excel in MIG welding aluminum:
-
Surface Preparation: A clean workpiece is non-negotiable. Use a dedicated stainless steel brush to scrub away the oxide layer and follow up with a solvent wipe to remove any contaminants. This step is vital for preventing weld defects and ensuring a strong bond.
-
Equipment and Material Selection: Your success hinges on using the right tools. A MIG welder with pulse capability, a spool gun or a graphene liner for smooth wire feeding, and the appropriate filler wire (ER4043 or ER5356) are your allies in achieving high-quality welds.
-
Technique and Skill: Mastering spray transfer and the push technique will not only improve the integrity of your welds but also their appearance. Practice these methods to enhance your welding finesse.
-
Troubleshooting Common Problems: Be proactive in preventing burn-through by controlling your heat input and travel speed. Keep your welds clean by ensuring a proper gas flow and moisture-free materials. Address wire feeding issues with the right setup and tension adjustments.
-
Continuous Learning and Practice: Welding is a craft that benefits from ongoing practice and staying informed about the latest advancements in welding technology. Each project is an opportunity to refine your skills and learn from any challenges that arise.
-
Safety First: Always prioritize your safety and that of your workspace. Proper protective gear and a secure environment are essential to your well-being as you weld.
By adhering to these guidelines and committing to continual improvement, you're setting yourself up for success in the world of MIG welding aluminum. With each weld you lay down, your confidence and capability will grow, propelling you towards mastery of this valuable skill. Keep pushing the boundaries of your welding abilities, and you'll soon be rewarded with the satisfaction of crafting strong, professional-grade aluminum welds.
Sharing is Caring
Feedback
At WeldWins, we know we aren't perfect which is why we're always looking for ways to improve. You can help us do better by taking 2 minutes to fill out our simple feedback form.
Any and all feedback is welcome. It could be a complaint, an idea, or even just a comment, we'll always be grateful to hear what you think.