How Has MIG Welding Transformed Modern Manufacturing?
June 8, 2024
10 min read
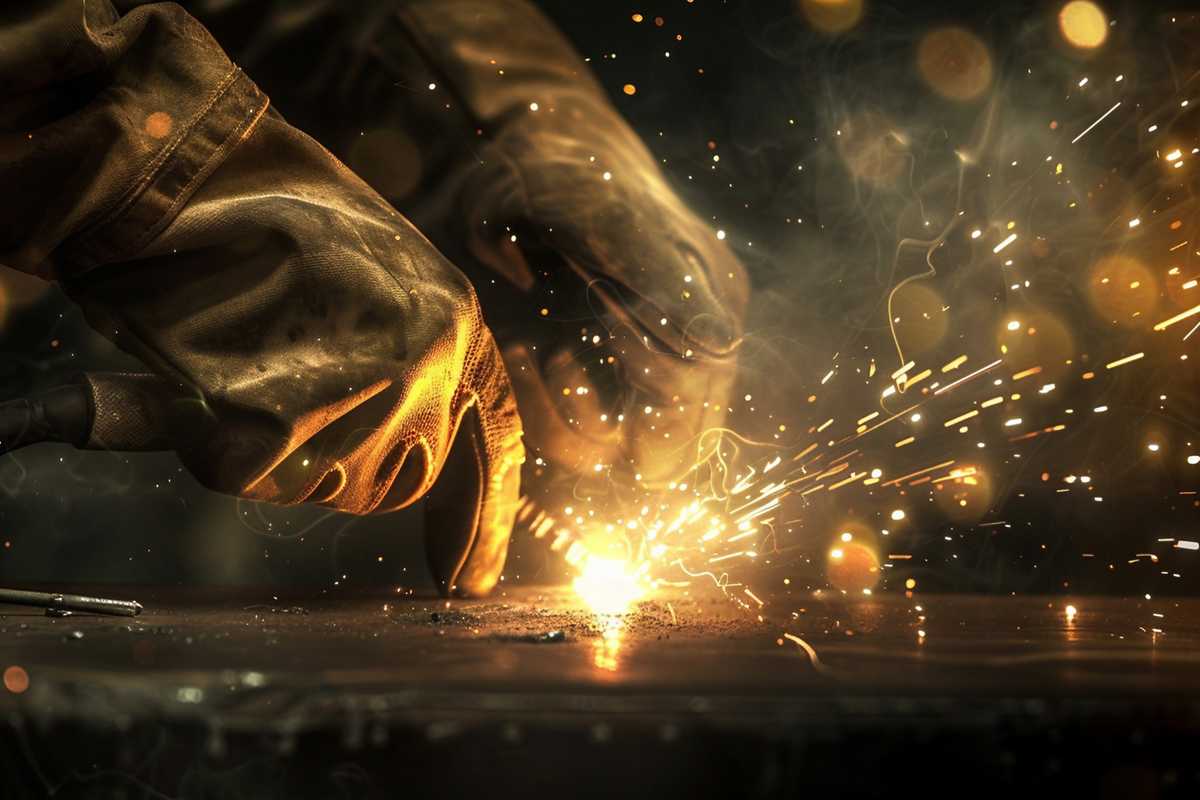
The art of joining metals has been pivotal to human progress, and among the many techniques developed, MIG welding has been a game-changer. This method, also known as Gas Metal Arc Welding (GMAW), uses a wire electrode that's continuously fed through a welding gun, along with a stream of inert gas to shield the weld from contamination. This combination results in durable, high-quality welds executed with remarkable speed and efficiency.
MIG welding's journey from a novel idea to a fundamental industry standard is a testament to its adaptability and effectiveness. It's a technique that has simplified the complex task of metal joining, making it accessible and reliable for a wide range of applications. From the towering structures that define our city skylines to the intricate assemblies within our vehicles, MIG welding has been integral in shaping the modern world.
In this article, we'll trace the origins of MIG welding, celebrate the era of innovation that honed it, and examine the contemporary advancements that have automated the process. As we explore the rich history and the current state of MIG welding, we'll understand why it remains a critical process in metalwork and how it continues to evolve and influence the industry.
1. The Origins and Impact of MIG Welding
The inception of Metal Inert Gas (MIG) welding marked a pivotal moment in metalworking history, revolutionizing the way we join metals with its innovative approach. The roots of MIG welding can be traced back to the 19th century, where the quest for a reliable metal joining method led to the creation of arc welding. This technique used an electric arc to melt and fuse metals together, but it was the addition of a protective gas shield that truly paved the way for MIG welding's emergence.
The gas shield, an essential component of MIG welding, was a groundbreaking innovation that protected the molten metal from the negative effects of the surrounding air, resulting in stronger, cleaner welds. The early champions of welding technology, including Nikolay Benardos and Charles L. Coffin, made significant strides with their patents in electrode and arc welding processes, setting the foundation for future advancements.
However, the transformational leap occurred in the early 20th century with the introduction of inert gases to shield the welding zone from oxidation and contamination. This concept was the cornerstone of MIG welding as we know it today. The urgency of World War II further accelerated MIG welding's development, as the need for quick and reliable metal joining became critical for producing ships and aircraft. During this time, enhancements in electrode wire and gas shielding techniques led to a more efficient and adaptable welding process.
MIG welding's early days were characterized by its speed and the superior quality of the welds it produced, outperforming traditional methods. These initial advancements laid the groundwork for MIG welding's widespread adoption in various industries, transforming the manufacturing of metal products on a global scale. The birth of MIG welding was not just a technical milestone; it was a significant leap forward that continues to influence the way we build and create with metal today.
2. The Golden Age of MIG Welding: Mid-20th Century Innovations
During the mid-20th century, MIG welding underwent a period of significant innovation, often hailed as its Golden Age. This era was marked by two key advancements that revolutionized the welding industry: the perfection of gas shielding techniques and the creation of specialized electrodes.
The introduction of inert gases like argon and helium transformed MIG welding by providing a shield to the molten weld pool from the surrounding air. This breakthrough meant that welds were now cleaner and stronger, with a reduced risk of oxidation and other common defects. The use of these gases was a turning point, ensuring that metals could be joined with unprecedented purity and strength.
Simultaneously, the development of electrodes tailored to different metals and thicknesses broadened the scope of MIG welding. Welders were now equipped to handle a variety of materials with precision, from delicate thin sheets to robust thick plates. This versatility was crucial in meeting the diverse needs of growing industries, particularly in automotive and aerospace manufacturing, where long, uninterrupted welds became the norm.
These innovations did more than just improve the technical aspects of welding; they revolutionized the speed and reliability of the process. MIG welding's newfound efficiency made it the preferred choice for many industrial applications, streamlining production lines and enhancing the quality of the final products.
The Golden Age of MIG welding laid the groundwork for its widespread adoption and established it as an essential technique in modern metal fabrication. The strides made during this time ensured that MIG welding would remain a vital tool in the metalworking industry, shaping the advanced welding technologies we rely on today.
3. Harnessing Technology: The Rise of Automated MIG Welding
In the modern chapter of MIG welding's history, we witness a transformative era where technology and automation redefine efficiency and precision in metal fabrication. The advent of computerized controls in welding equipment marks a pivotal shift, propelling the welding process to new heights of productivity.
These sophisticated controls enable welders to fine-tune welding parameters with exceptional accuracy, including voltage, current, and wire feed speed. Such meticulous adjustments lead to uniform weld quality and significantly reduce the margin for human error. Consequently, this translates into a more dependable welding process with diminished waste and fewer instances of rework.
The spotlight in this technological revolution shines on automation. Robotic welding systems have become a staple in manufacturing settings, tirelessly executing repetitive, high-volume welding tasks with unwavering precision. These robotic marvels are adept at performing intricate welding operations that would otherwise be daunting and labor-intensive for human welders. The automation of these processes not only accelerates production rates but also curtails labor expenses while upholding superior weld quality.
The fusion of automation into MIG welding has not only streamlined the welding process but has also sparked a wave of innovation. For example, the integration of sensors and advanced algorithms enables real-time monitoring and dynamic adjustments during the welding process. Welding systems can now autonomously detect and adapt to variations in materials or environmental conditions, ensuring consistently optimal welds.
Furthermore, the technological advancements have rendered MIG welding more user-friendly and accessible. Modern welding machines come equipped with preset programs for a variety of applications, simplifying the operator's job to achieve professional results without the need for extensive training. This democratization of welding technology has expanded its reach across different industries and has equipped a new wave of welders with the tools to excel with a shorter learning curve.
In essence, the modern era of MIG welding is characterized by the seamless marriage of cutting-edge computerized controls and automation. These breakthroughs have not only transformed the welding landscape but have also laid the groundwork for ongoing enhancements and creativity in the domain. Looking ahead, the horizon is brimming with potential for further technological leaps in MIG welding, promising even more remarkable gains in efficiency, precision, and adaptability in the world of metalwork.
4. MIG Welding: The Backbone of Modern Manufacturing
MIG welding, short for Metal Inert Gas welding, is a technique that has revolutionized the manufacturing industry. Known for its speed and flexibility, it's the go-to method for a wide range of projects, from mass-produced goods to custom designs.
Take the automotive industry, for example. Here, MIG welding is crucial. It's used to assemble cars and trucks, creating strong bonds that are vital for the vehicle's safety and longevity. The process is perfect for joining thin metal sheets without distorting them, which is essential for both the aesthetic and structural aspects of vehicles. Whether it's putting together the main body of the car or attaching smaller engine parts, MIG welding helps speed up the production line without compromising on quality.
In construction, MIG welding is just as important. It's used to build the metal frameworks that are the backbone of skyscrapers, bridges, and other infrastructure. With MIG welding, workers can quickly join large metal beams and smaller fixtures alike, ensuring that everything from the main structure to the handrails is strong and secure.
Aerospace is another area where MIG welding shines. In this industry, precision is everything, as aircraft and spacecraft parts must endure extreme conditions. MIG welding is precise enough for these high-stakes applications and versatile enough to handle a variety of metals, including aluminum and titanium, which are commonly used in aerospace.
Shipbuilding also benefits from MIG welding. The hulls of ships and submarines are often put together using this method because it produces long, continuous welds that can stand up to the harsh marine environment.
But MIG welding isn't just for heavy industry. It's also used in creating everyday products like home appliances and furniture, and it's even made its way into the art world. Its ability to adapt to different designs makes it a favorite among artists and designers who work with metal.
Lastly, the energy sector, including renewable energy, is increasingly turning to MIG welding. Components for wind turbines and solar panel frames are often made using MIG welding, contributing to the creation of sustainable energy solutions.
In summary, MIG welding's contribution to modern industries is vast and varied. Its combination of speed, reliability, and versatility makes it indispensable in the production of everything from cars to art installations. As technology and materials continue to advance, MIG welding is expected to remain a fundamental process in metal fabrication.
5. Reflecting on MIG Welding's Transformative Journey
As we reach the end of our exploration into MIG welding's rich history and its impact on modern manufacturing, it's clear that this technique is more than just a method for joining metals—it's a symbol of industrial innovation. The transformation from basic welding methods to today's advanced, computerized systems underscores the remarkable progress made in this field.
MIG welding has become an integral part of industries worldwide, demonstrating its versatility and critical role in production. Its applications range from the detailed work in automotive assembly lines to the sturdy construction of towering skyscrapers. The progression in gas shielding and electrode technology has not only elevated the quality of welds but also expanded the horizons for future metalwork innovations.
Looking ahead, the possibilities for MIG welding are as vast as the industries it serves. The trend towards automation and the potential integration of artificial intelligence hint at a future where MIG welding could achieve unprecedented levels of precision and efficiency. The commitment to advancing this technology ensures that MIG welding will continue to be a vital player in the evolution of metal fabrication.
In summing up, MIG welding's journey is one of continuous advancement and mastery. It reflects our ongoing quest for industrial excellence and stands as a testament to human creativity and problem-solving. As we push forward, MIG welding is set to maintain its position as a pivotal process, shaping the future of manufacturing and leaving a lasting impact on the world around us.
Sharing is Caring
Feedback
At WeldWins, we know we aren't perfect which is why we're always looking for ways to improve. You can help us do better by taking 2 minutes to fill out our simple feedback form.
Any and all feedback is welcome. It could be a complaint, an idea, or even just a comment, we'll always be grateful to hear what you think.