How Can You Master the Art of Aluminum Welding?
July 6, 2024
11 min read
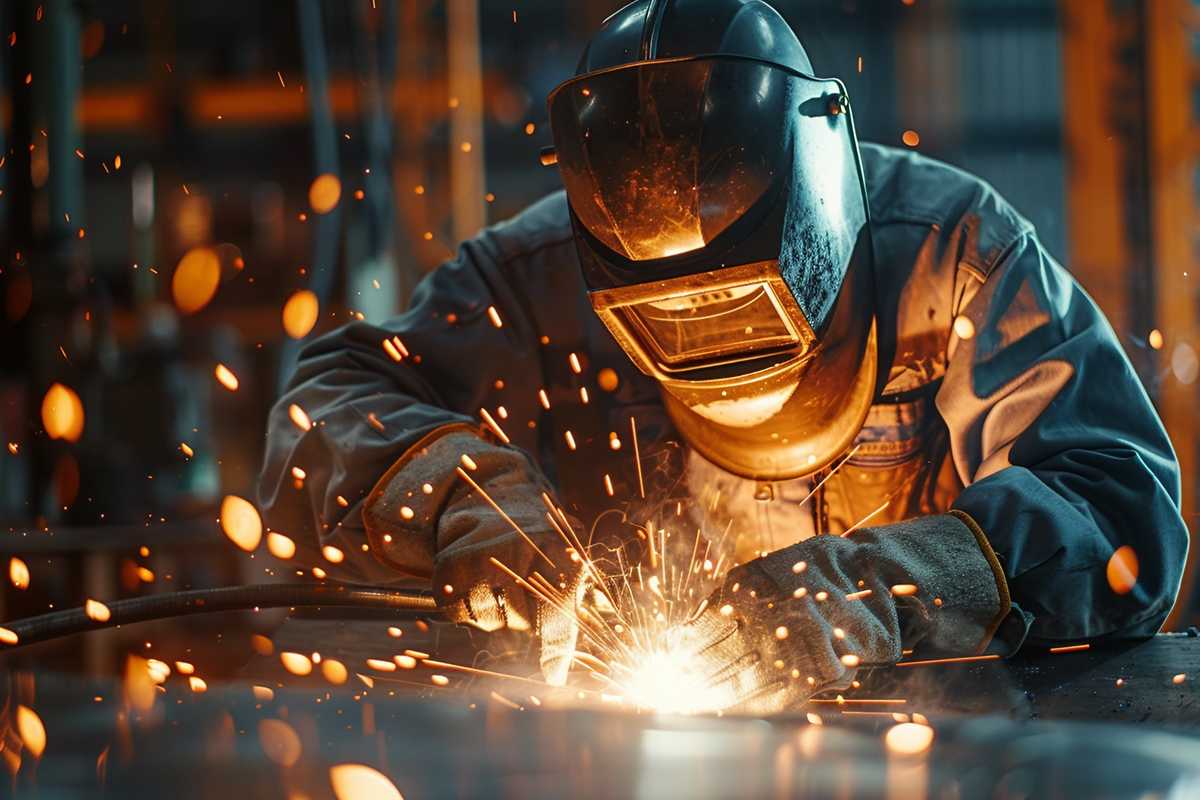
Aluminum's unique blend of strength and lightness has made it a go-to material for countless applications, from sleek aircraft to everyday kitchen utensils. Its impressive strength-to-weight ratio allows for the creation of sturdy yet lightweight products, a quality highly sought after in many fields. Consequently, welding aluminum has become an indispensable skill for fabricators and hobbyists who aim to craft durable and high-quality items.
Yet, welding this versatile metal isn't without its challenges. Aluminum's lower melting point and higher conductivity compared to steel mean that welders must employ specific techniques and tools to achieve the best results. Moreover, aluminum's tendency to form an oxide layer when exposed to air can interfere with the welding process, potentially compromising the strength and appearance of the weld.
Despite these hurdles, mastering aluminum welding is a rewarding endeavor that unlocks the potential to build robust, long-lasting creations. This guide will walk you through the essential practices and insights needed to excel in aluminum welding. Whether you're a seasoned welder or just starting, you'll learn the foundational skills necessary to ensure your projects not only perform well but also withstand the test of time. Let's embark on this journey to welding excellence together.
1. The Key Characteristics of Aluminum for Welders
Aluminum's popularity in industries like aerospace and automotive is undeniable, thanks to its remarkable combination of lightness and strength. But when it comes to welding, aluminum's distinct characteristics set it apart from other metals like steel. Understanding these traits is crucial for any welder looking to achieve strong and durable aluminum welds.
Firstly, aluminum's most noticeable trait is its weight—or lack thereof. Weighing in at about a third of steel's mass, aluminum is a dream to work with, especially when constructing structures where every ounce counts. Yet, this advantage has its trade-offs. Aluminum's high thermal conductivity means it sheds heat rapidly, which can be a double-edged sword. While it reduces the risk of overheating, it also necessitates the use of more heat from the welder to maintain the right temperature for a proper weld pool.
The presence of an aluminum oxide layer is another critical factor. This protective layer forms naturally when aluminum is exposed to the air, and it's stubbornly resistant to heat—more so than the aluminum beneath it. If not removed before welding, this layer can mix into the weld, weakening the joint and potentially leading to failure. Moreover, if the oxide isn't completely eliminated, it can tarnish the appearance of the weld, which is less than ideal for projects where looks matter.
To tackle these challenges, welders must choose their techniques wisely and prepare the aluminum with care. Recognizing the quick heat dissipation of aluminum, adjustments in the welding approach are necessary to keep the weld pool stable. Dealing with the oxide layer effectively is just as important to avoid contamination and ensure a robust, clean weld.
In essence, aluminum's lightweight nature, its propensity to conduct heat quickly, and the ever-present oxide layer are all factors that influence the welding process. By fully understanding and adapting to these properties, welders can navigate the challenges they pose and execute successful, high-quality welds on their aluminum projects.
2. Mastering Aluminum Welding Techniques: TIG vs. MIG
Aluminum welding requires a skilled hand and knowledge of the right techniques to ensure a strong and lasting join. The two primary methods used by professionals are Tungsten Inert Gas (TIG) welding and Metal Inert Gas (MIG) welding. Each has distinct advantages and is better suited to specific applications. Understanding when and how to use each technique is key to producing superior welds.
TIG Welding: The Art of Detail
TIG welding is the go-to method for projects that demand precision. It's like using a fine brush for a detailed painting. This method uses a tungsten electrode that doesn't melt, allowing you to add a separate filler material at your own pace. It's perfect for delicate tasks or when you're working with very thin aluminum sheets. You can think of TIG welding as a dance where you control the rhythm, adjusting the heat to prevent the aluminum from warping or developing holes. The result? A clean, spatter-free weld that looks as good as it holds.
MIG Welding: Fast and Furious
MIG welding is the sprinter of the welding world, known for its speed and efficiency. It's ideal for thicker aluminum pieces and when you need to weld a lot in a short time, like in production lines. In MIG welding, the wire feeds through the gun continuously, serving as both electrode and filler. It's generally easier to pick up than TIG welding and can be automated, which is a bonus for large-scale operations. While it may not always give you the polished finish of TIG welding, with the right settings and a steady hand, MIG can produce strong, effective welds quickly.
Equipment and Settings: The Welder's Toolbox
No matter which method you choose, the right equipment and settings are your best allies. You'll need a power source that lets you tweak the amperage and voltage to match the demands of your project. The filler material should be compatible with the aluminum alloy you're working with to ensure a bond that's as strong as it is seamless.
For TIG welding, consider using a high-frequency start to ignite the arc cleanly without affecting the weld pool. MIG welders can benefit from a pulse welding technique, which alternates between high and low currents to manage the heat and prevent burn-through.
In summary, TIG welding shines for its precision and finesse, making it suitable for intricate or cosmetic applications. MIG welding is valued for its quick pace and productivity, especially in larger projects or where time is of the essence. By understanding each method's strengths and configuring your equipment accordingly, you can tackle the challenges of aluminum welding and achieve results that are both aesthetically pleasing and structurally sound.
3. Navigating Aluminum Welding Challenges: Expert Tips for Quality Joints
Welding aluminum can be a tricky endeavor, even for seasoned professionals. The metal's unique properties often lead to common issues that can compromise the integrity of the weld. In this section, we'll address these challenges head-on, offering expert advice and proven solutions to help you achieve flawless results in your aluminum welding projects.
Tackling Oxidation with Precision Cleaning
The moment aluminum comes into contact with air, it begins to oxidize, forming a stubborn layer that's more resistant to heat than the aluminum itself. This can wreak havoc on your welds, leading to weak joints and an unattractive finish. The key to overcoming this is meticulous cleaning. Use a dedicated stainless steel brush to scrub away the oxide layer just before welding. For an even cleaner weld, opt for AC TIG welding, which has a cleaning effect that disrupts the oxide during the welding process.
Ensuring a Porosity-Free Weld
Porosity, or tiny holes in your weld, can occur when contaminants like oil or moisture get trapped in the metal. These imperfections weaken the weld and can lead to failure under stress. To avoid this, always start with aluminum that's clean and completely dry. Employ a shielding gas such as pure argon or an argon-helium mix to protect the weld pool, and make sure your gas flow is strong enough to keep the air at bay.
Preventing Burn-Through with Controlled Heat
Aluminum's rapid heat absorption can cause burn-through, particularly with thin materials. To prevent this, position a thicker metal piece behind your weld area to absorb excess heat. Pulse welding is another effective strategy, where you alternate between high and low currents to moderate the temperature, giving the metal time to cool during the process.
Minimizing Distortion for a Straight Finish
Aluminum's propensity to warp under heat can lead to distortion, ruining the shape and fit of your project. Combat this by securing the pieces firmly with appropriate fixtures. Employ tack welding at strategic intervals to keep everything aligned. Distribute your welds evenly across the joint to spread out the heat, reducing the likelihood of warping.
Cracking Down on Cracking
Cracking is a common issue, especially at the beginning and end of a weld where temperature shifts are most extreme. To prevent cracks from forming, use the backstepping technique: begin welding at the end of the seam and then reverse direction to complete the start. This preheats the area, evening out the temperature changes. Also, ensure you're using a filler material that's compatible with the specific aluminum alloy you're working with to reduce the risk of cracking.
By mastering these solutions to common aluminum welding challenges, you'll be well on your way to producing strong, aesthetically pleasing welds. Remember, achieving proficiency in aluminum welding is a matter of practice and persistence. As you continue to refine your techniques, you'll find the process becoming more intuitive and your welds more consistent.
4. Essential Safety Protocols for Aluminum Welding
Aluminum welding, while effective for fusing metal, comes with its own set of hazards. To ensure a safe welding environment, it's imperative to follow stringent safety protocols tailored to the specific challenges of working with aluminum.
Personal Protective Gear: Your First Line of Defense
The intense light and UV radiation produced during welding can be harmful, so a welding helmet with the correct filter shade is non-negotiable. It's not just about eye protection; the helmet also guards your face against the heat and flying sparks. To shield the rest of your body, wear flame-resistant clothing like a long-sleeved jacket and pants—preferably made of leather or thick cotton. Don't forget durable gloves to protect your hands from the heat, sparks, and the risk of electric shock.
Ventilation: Keeping the Air Clean
Aluminum welding can release harmful fumes that are dangerous if inhaled. To combat this, work in a well-ventilated space with plenty of airflow. If you're in a confined area, consider using an exhaust system or fans, and don't hesitate to wear a respirator for added lung protection.
Electrical Hazards: Prevention is Better Than Cure
Before you strike an arc, inspect your welding equipment for damage. Check that all cables and connections are secure and that your setup is properly grounded. This will help prevent electrical shocks, which can be severe.
Fire Safety: Be Prepared
Sparks and hot metal from welding can easily start a fire, so keep a fire extinguisher within reach. Clear the area of any flammable materials, and if you're working in a place where sparks might reach combustible materials, have someone stand by as a fire watch.
Handling Hot Metal: Caution is Key
Aluminum retains heat long after the welding is done, posing a burn hazard. Handle newly welded parts with care, let them cool down sufficiently, or use the right tools to move them without direct contact.
By rigorously applying these safety measures, you'll significantly reduce the risks that come with aluminum welding. Safety is a continuous practice, not just a checklist. Make it a part of your welding routine to ensure a secure and productive work environment.
5. Wrapping Up: Your Path to Aluminum Welding Mastery
Embarking on the path to becoming an adept aluminum welder is an adventure that marries the technical with the practical. We've journeyed through the intricacies of aluminum's unique characteristics, uncovering why its lightness and strength pose both opportunities and challenges. We've highlighted the critical step of metal preparation, emphasizing that a clean surface is the foundation of a dependable weld.
Our exploration of TIG and MIG welding has armed you with the knowledge to select the most suitable technique for your project. Whether you're aiming for the meticulous artistry of TIG or the rapid pace of MIG, understanding these methods is crucial for your welding success.
We've confronted the typical hurdles you might face, such as the pesky aluminum oxide layer, the threat of porosity, and the dreaded burn-through. For each problem, we've offered targeted strategies, like using a stainless steel brush for cleaning, ensuring a dry workpiece to prevent porosity, and controlling heat to avoid burn-through.
Safety has been a golden thread throughout our discussion, with reminders to gear up with the right protective equipment, maintain a well-ventilated workspace, and stay vigilant about potential fire hazards.
As you continue to hone your welding skills, patience will be your greatest ally. Every weld is a chance to learn and improve. Experiment with your equipment's settings, try out different welding techniques, and practice on various aluminum pieces to find your rhythm.
Ultimately, the art of aluminum welding is a testament to your commitment to the craft. Keep your equipment primed, your aluminum spotless, and your concentration laser-focused. Here's to your welding journey—may it be as rewarding as it is enlightening. Happy welding!
Sharing is Caring
Feedback
At WeldWins, we know we aren't perfect which is why we're always looking for ways to improve. You can help us do better by taking 2 minutes to fill out our simple feedback form.
Any and all feedback is welcome. It could be a complaint, an idea, or even just a comment, we'll always be grateful to hear what you think.