How Critical Is Weld Testing for Our Safety and Infrastructure?
April 28, 2024
12 min read
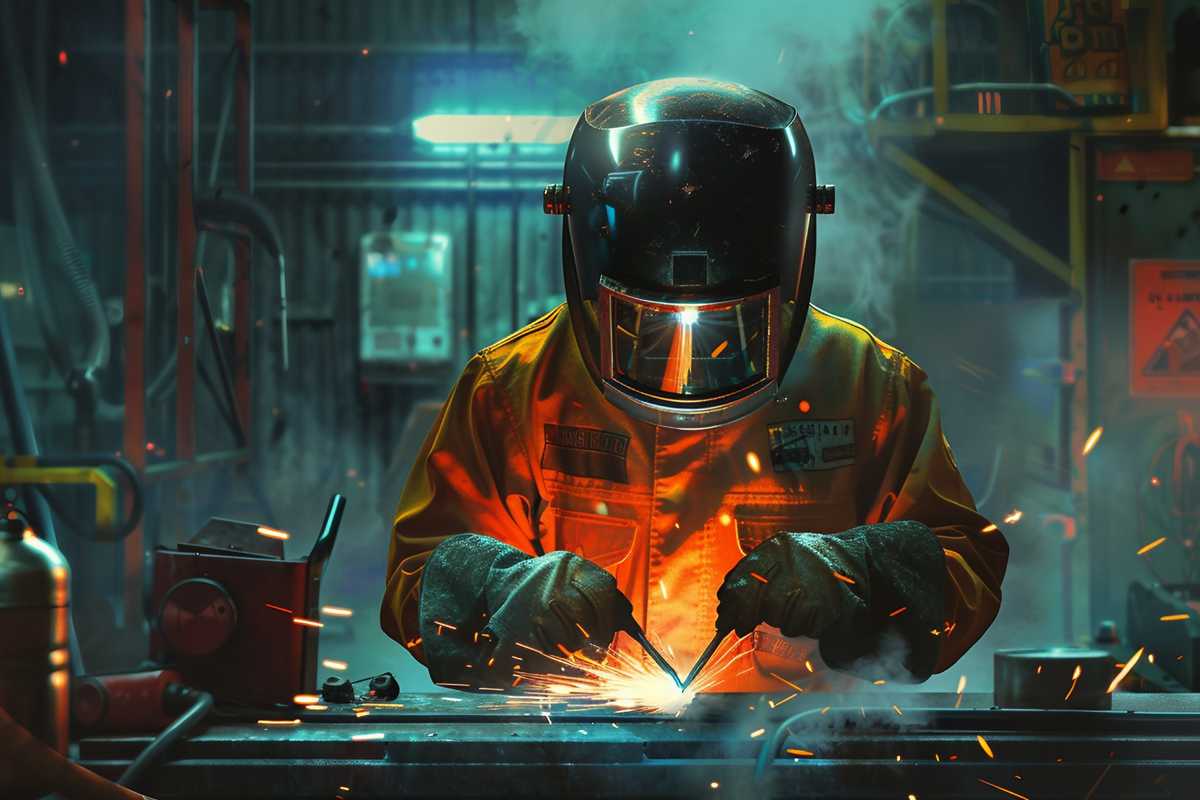
1. Welding: The Invisible Glue of Our World
Imagine the world around you – the buildings you enter, the cars you drive, and the bridges you cross. What's the invisible glue holding them all together? It's welding, a fundamental process that fuses materials to support the structures of our daily lives. But the true strength of a weld isn't just in its creation; it's in its ability to hold fast under pressure. That's where weld testing comes in.
Weld testing is a critical step in ensuring that these invisible connections are safe and reliable. It's like giving a weld a thorough health check-up to make sure it's fit for duty. Without these tests, we'd have no way to predict if a weld could fail, potentially leading to dangerous situations.
In this article, we're going to take a closer look at the world of weld testing. We'll explore the different ways welds are put to the test, both by pushing them to the brink and by examining them with advanced technology that doesn't leave a mark. For anyone involved in making or maintaining welded structures, this is essential knowledge. So, let's dive into the details and discover how these critical tests keep our world safely held together.
2. The Critical Role of Weld Testing in Safety and Quality Assurance
Weld testing is an essential practice in industries where the fusion of metals is fundamental to the construction of reliable and safe structures. It acts as a safeguard, ensuring that every weld can bear the loads and stresses of everyday use. From towering skyscrapers to the cars we drive, the resilience of these welded joints is crucial to preventing structural failures that could have dire consequences.
The process begins with adherence to stringent standards set by regulatory authorities, which dictate the performance criteria for welds. Testing is the only way to certify that these benchmarks are met, providing a stamp of approval that the welds are fit for purpose. Without this validation, there's no telling whether a weld might give way under stress, posing risks to safety and incurring financial losses through damage or injury.
Identifying defects early is another cornerstone of weld testing. Flaws like cracks or gas pockets within the weld can significantly weaken the joint. By detecting these imperfections early, repairs can be made before the welded item is put to use, averting potential failures. This proactive approach not only saves on repair costs but also avoids the higher costs associated with accidents or malfunctions.
Weld testing also serves as a feedback mechanism for improving welding techniques. By analyzing test outcomes, welders and engineers can refine their methods, ensuring that future welds are of even higher quality. This cycle of continuous improvement is vital for the advancement of welding technology and maintaining the integrity of welded structures.
In high-stakes industries such as aerospace or civil engineering, the importance of rigorous weld testing is amplified. The catastrophic outcomes of weld failure in these fields highlight the necessity for meticulous testing protocols. By ensuring that welds are up to standard, manufacturers and construction firms not only protect end-users but also uphold their reputations for producing dependable, high-quality products.
In essence, weld testing is the cornerstone of manufacturing and construction processes involving metalwork. It guarantees that welded structures are capable of withstanding their intended loads, conform to industry standards, and are free from defects that could compromise their strength. The significance of weld testing is paramount—it is the critical factor that ensures the safety, durability, and longevity of welded assemblies.
3. Exploring the Rigorous World of Destructive Weld Testing
Destructive weld testing is a rigorous approach to ensuring the strength and quality of welded joints. These tests intentionally push welds to their breaking point to reveal their characteristics under stress. The insights gained from these tests are crucial for determining whether a weld is up to the task it's meant for. Let's delve into some of the key destructive testing methods that help keep our structures safe.
Macro Etch Test: Revealing Hidden Flaws
The Macro Etch Test is akin to giving a weld an x-ray. By polishing and etching a weld's cross-section with acid, this test uncovers any hidden flaws within. Inspectors look for signs of poor fusion, trapped slag, or tiny holes known as porosity. These defects can weaken a weld, and identifying them is essential for ensuring the weld's reliability.
Fillet Weld Break Test: A Stressful Challenge
Imagine bending a metal joint until it snaps—that's the essence of the Fillet Weld Break Test. It's a straightforward but effective way to test the strength of a fillet weld, which connects two pieces at a right angle. The point where the weld breaks is then examined for defects that could have caused the failure, providing a clear picture of the weld's integrity.
Transverse Tension Test: Measuring Weld Muscle
The Transverse Tension Test is like a tug-of-war for welds. A sample with a weld is pulled from both ends until it tears apart. This brutal test measures the weld's tensile strength—the maximum stress it can withstand before failing. Understanding this limit is vital for ensuring a structure can handle the loads it will face in real-world conditions.
Guided Bend Test: Bending Without Breaking
Flexibility is just as important as strength, and the Guided Bend Test assesses just that. A welded sample is bent over a rod to see how well it can flex without cracking. This test is especially good at finding hidden issues like internal cracks or areas where the weld didn't fully penetrate the metal.
These destructive tests are essential tools for weld inspectors, providing them with the data needed to make informed decisions about a weld's performance. By intentionally taking welds to the point of failure, we can ensure that the structures we depend on every day—from bridges to buildings—are safe, sturdy, and reliable.
4. Essential Non-Destructive Testing Methods for Weld Integrity
Non-destructive testing (NDT) is a cornerstone of weld inspection, providing a window into a weld's health without damaging the component. These methods are vital for the safety and durability of structures across various sectors, from the cars we drive to the bridges we traverse. Let's delve into the most prevalent NDT techniques that help ensure our welded structures are up to the task.
Visualizing Flaws with Magnetic Particle Inspection
Magnetic Particle Inspection (MPI), a widely adopted NDT technique, is particularly adept at uncovering surface and just-below-surface defects in ferromagnetic materials. The process begins by magnetizing the weld zone. We then sprinkle fine magnetic particles over the area—these could be in dry powder form or suspended in a liquid. Flaws such as cracks or voids disrupt the magnetic field, causing the particles to cluster visibly at the defect site, much like iron filings on a magnet. MPI is favored for its speed, simplicity, and effectiveness, making it a first-line defense in weld inspection.
Peering Inside with Radiographic Testing
Radiographic Testing, encompassing both X-Ray and Gamma Ray methods, acts like a super-powered X-ray that can see into a weld's core. By shooting high-energy radiation through the weld and capturing the image on a detector or film, inspectors can spot variations in density or thickness that indicate problems like gaps or foreign materials. These techniques are indispensable for internal assessments, especially when the weld must perform flawlessly. However, due to the radiation involved, they require specialized equipment and strict safety measures.
Listening for Defects with Ultrasonic Testing
Ultrasonic Testing (UT) listens to the echoes of high-frequency sound waves sent through a weld to find hidden imperfections. A device called a transducer sends these waves into the weld. When they hit a flaw, they bounce back, and the device calculates the flaw's size and location based on the echo. UT is a powerful tool that can detect both surface and deeper issues, offering a detailed picture of a weld's internal soundness. It's adaptable to various materials and weld types, making it a versatile choice for inspectors.
In summary, NDT methods like Magnetic Particle Inspection, Radiographic Testing, and Ultrasonic Testing are indispensable for verifying weld quality without causing any damage. These techniques allow for the early detection of potential problems, ensuring that welds meet safety standards and are ready for real-world demands. By integrating these NDT methods into regular inspection routines, we can prevent failures and uphold the structural integrity of our engineered projects.
5. Advancements in Weld Testing: Ensuring Future Safety
The landscape of weld testing is rapidly transforming, driven by technological breakthroughs aimed at improving the precision and speed of inspections. These advancements are vital for meeting the stringent safety requirements of today's complex engineering projects. Let's delve into the latest innovations that are setting new standards in the field of weld testing.
Revolutionizing Inspection with Digital Radiography
Digital radiography is revolutionizing weld inspections by replacing traditional film with digital images. This leap forward allows for instant image processing, slashing inspection times. It provides clearer, more detailed images that can be zoomed in to scrutinize specific sections of a weld, ensuring nothing is missed. Moreover, it's a greener option, doing away with the chemicals needed for film development.
Enhanced Defect Detection with Phased Array Ultrasonic Testing (PAUT)
Phased array ultrasonic testing (PAUT) is a game-changer, employing an array of ultrasonic probes to produce focused beams that sweep through a weld. This method generates detailed images, revealing the exact nature of any defects. PAUT excels at inspecting complex shapes and thick materials, making it indispensable for ensuring the integrity of critical welds.
Precision Mapping with Laser Scanning
Laser scanning offers a swift, non-contact approach to assess welds. It rapidly maps the weld's surface, pinpointing any irregularities that deviate from the design. This technique is especially useful for evaluating the external characteristics of a weld and can be paired with other methods for a thorough analysis.
The Rise of Automated Inspection Systems
The push towards automation has led to the development of robotic systems capable of performing inspections with little human input. These robots can navigate intricate structures and carry out consistent, precise testing, especially useful in environments that are dangerous or hard to reach. This not only boosts safety but also enhances the efficiency of the inspection process.
Smarter Inspections with AI and Machine Learning
Artificial intelligence (AI) and machine learning are starting to make their mark on weld testing. These technologies analyze data from various inspection methods to spot patterns and irregularities that could indicate defects. As these systems learn and improve over time, they may even predict potential failures, enhancing the predictive maintenance of welds.
Real-Time Monitoring with Smart Sensors
The latest sensor technology enables real-time monitoring of welds during the actual welding process. These smart sensors can detect changes in temperature and pressure, among other factors, that could compromise the quality of a weld. This immediate feedback allows for on-the-spot adjustments, minimizing defects and bolstering the overall quality of the weld.
In conclusion, the field of weld testing is embracing a new era of innovation, focusing on precision, efficiency, and safety. By harnessing the power of digital tools, automation, and smart technologies, the industry is better equipped to guarantee the structural soundness of welds in demanding environments. These cutting-edge developments not only enhance the trustworthiness of weld inspections but also drive the creation of industry benchmarks and best practices.
6. Securing Our Future: The Pivotal Role of Weld Testing
In the intricate dance of engineering, weld testing is the silent guardian ensuring our safety and the enduring strength of the structures that underpin our society. This article has taken you through the meticulous processes that scrutinize the welds holding together everything from the bridges we traverse to the buildings we inhabit, ensuring they stand the test of time and stress.
We've explored the diverse arsenal of tests, both destructive and non-destructive, that serve as the industry's commitment to excellence. Destructive testing sacrifices a piece to learn about the whole, offering a deep dive into a weld's resilience and adaptability. Non-destructive testing, meanwhile, acts as a vigilant overseer, assessing the health of welds while keeping them intact for continued service.
The relentless march of innovation in weld testing is equipping us with ever more refined tools, capable of detecting the slightest imperfections that once would have gone unnoticed. These technological leaps are not just enhancing the trustworthiness of our structures but are also shaping the standards by which they are judged, ensuring they are not just built, but built to last.
Understanding the results of these tests is as critical as conducting the tests themselves. It demands a comprehensive grasp of the techniques and the materials at hand. Our engineers and technicians are the skilled interpreters of this data, translating the findings into actionable insights that uphold the quality and safety of our welded bonds.
In closing, the role of advanced weld testing cannot be overstated. It is the rigorous practice that confirms the reliability of the unseen connections that hold our world together. As we continue to refine these methods and apply them with diligence, we reinforce the highest standards of structural integrity, protecting our communities and preserving our environment for the future.
Sharing is Caring
Feedback
At WeldWins, we know we aren't perfect which is why we're always looking for ways to improve. You can help us do better by taking 2 minutes to fill out our simple feedback form.
Any and all feedback is welcome. It could be a complaint, an idea, or even just a comment, we'll always be grateful to hear what you think.