How Critical Are Weld Inspections for Structural Safety?
June 17, 2024
11 min read
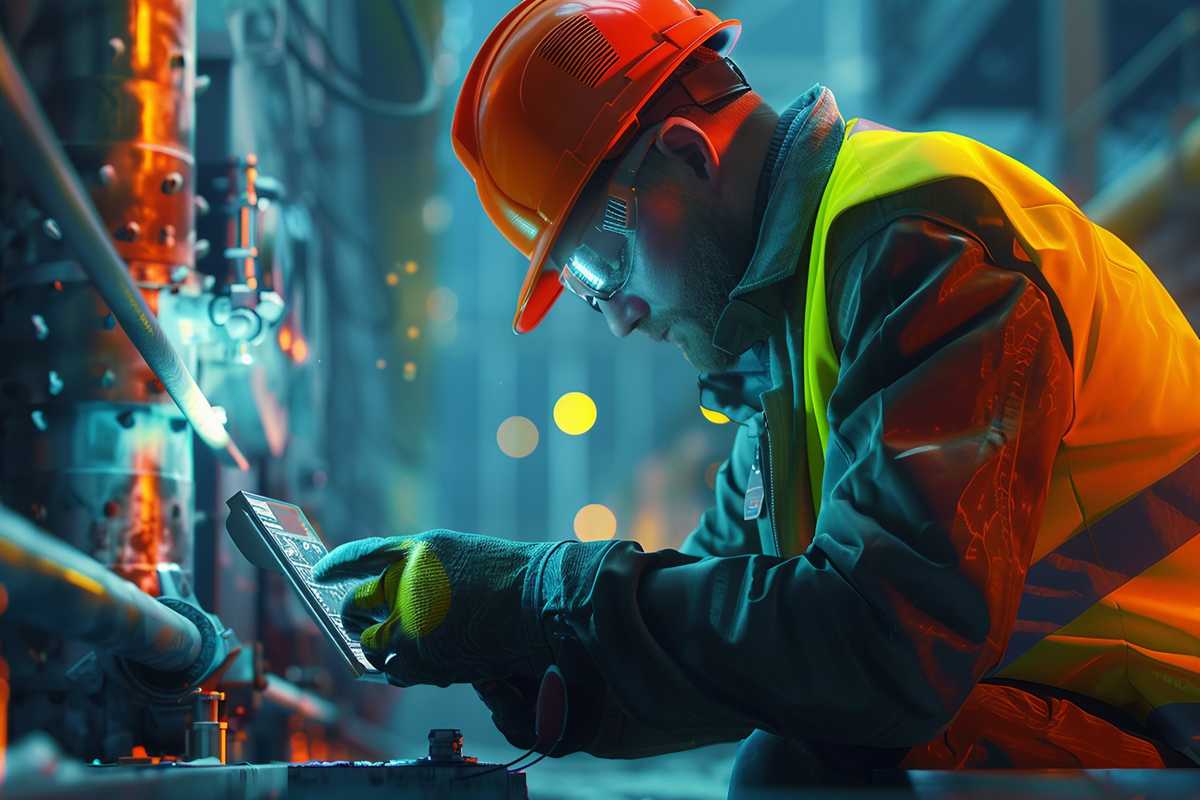
Welding is more than just fusing metals together; it's a craft that holds our world together, from the cars we drive to the bridges we cross. But even the smallest flaw in a weld can have disastrous consequences. That's why weld inspections are not just a formality—they're a crucial safeguard.
In this article, we'll explore the art of ensuring weld quality. We'll look at the common defects that can occur, the various inspection methods available, and how these techniques help prevent dangerous failures. Whether it's a pipeline, a skyscraper, or an aircraft, the quality of welding is paramount. Join us as we uncover the meticulous process of weld inspections that keep our daily lives safe and structures standing strong.
1. Examining the Essentials of Weld Inspections
Weld inspections are a crucial safeguard in industries where the strength of metal bonds is paramount. These inspections ensure that welded connections are robust and meet stringent safety and quality standards. In this section, we'll explore the objectives of weld inspections and identify common issues associated with various weld types.
Objectives of Weld Inspections
The main aim of weld inspections is to ascertain the safety and durability of welds, which are critical to the structural integrity of various constructions. Inspections are vital for several reasons:
- Compliance with Standards: They confirm that welding practices adhere to industry codes and specifications.
- Safety Assurance: Inspections detect flaws that could compromise the weld's strength, thereby preventing potential hazards.
- Performance Optimization: Regular checks can spot early signs of trouble, allowing for timely interventions that enhance the lifespan of the structure.
- Quality Assurance: They act as a checkpoint to ensure the welding process was executed properly, resulting in a product that meets quality expectations.
Recognizing Weld Types and Their Potential Issues
Different welds are prone to specific problems, and recognizing these is key to effective inspections. Here's a brief overview:
- Butt Welds: These join metal pieces end-to-end and may suffer from issues like incomplete fusion or tiny holes known as porosity.
- Fillet Welds: Used at right angles, these welds can have problems like trapped slag, cracks, or being the wrong size.
- Lap Welds: Overlapping metals are joined here, and inspectors look out for issues like insufficient penetration or too much spatter.
- Corner and Edge Welds: These are found at the edges of metal pieces and can have alignment issues or uneven weld lines.
Inspectors must be adept at spotting these faults, which can range from visible surface defects to hidden internal ones. For example, a butt weld might look perfect on the outside but have internal voids, while a fillet weld's irregular bead is easier to spot.
In essence, weld inspections are indispensable for maintaining the reliability and safety of structures that rely on metal welding. Understanding the objectives of these inspections and the typical faults in different weld types is crucial for inspectors to provide feedback that ensures the integrity and longevity of the final product.
2. Unveiling Non-Destructive Testing: The Guardians of Weld Integrity
In the realm of welding, ensuring the strength and safety of connections without causing harm to the materials is paramount. This is where Non-Destructive Testing (NDT) methods shine as the guardians of weld integrity. These sophisticated techniques allow inspectors to detect hidden flaws and ensure that welded structures are up to the task of withstanding the demands of their application. Let's explore the most prevalent NDT methods that serve as the first line of defense in weld inspections.
The Eyes of Inspection: Visual Testing (VT)
Visual Testing (VT) stands as the most accessible and immediate form of NDT. It's akin to a detective conducting a preliminary survey of a scene. Inspectors use their trained eyes, possibly aided by magnifying tools and mirrors, to spot surface irregularities like cracks or pits. While VT is limited to what's visible on the surface, it's a critical first step in the inspection process.
X-Ray Vision for Metals: Radiographic Testing (RT)
Radiographic Testing (RT) is the industrial equivalent of an X-ray. By directing X-rays or gamma rays through the weld, inspectors can capture an image revealing the internal structure. This method excels at uncovering hidden voids or inclusions that could compromise the weld's integrity. The resulting images serve as a permanent record, although safety measures are essential to protect against radiation.
Echoes of Flaws: Ultrasonic Testing (UT)
Ultrasonic Testing (UT) uses high-frequency sound waves that penetrate materials. Like an echo bouncing off a canyon wall, these waves reflect back when they encounter inconsistencies, such as cracks or gaps within the weld. UT is not only adept at finding these hidden defects but can also measure material thickness, making it a versatile ally in the inspection toolkit.
The Magnetic Attraction of Imperfections: Magnetic Particle Testing (MT)
Magnetic Particle Testing (MT) is a method tailored for ferromagnetic materials. By magnetizing the weld area and sprinkling fine magnetic particles over it, any surface or near-surface discontinuities will disrupt the magnetic field and attract the particles, visibly outlining the defect. MT is a swift and straightforward technique that provides instant feedback on the weld's condition.
Revealing the Unseen: Liquid Penetrant Testing (PT)
Liquid Penetrant Testing (PT) is the method of choice for exposing surface-breaking defects that might otherwise remain hidden. A dye with superior wetting properties is applied to the weld's surface. After it seeps into any cracks or crevices, a developer is used to draw the dye out, creating a visible indication of the flaw. PT is effective on various materials and is particularly good at highlighting fine surface anomalies.
By integrating these NDT methods, inspectors can assemble a comprehensive picture of a weld's health, ensuring that the structures we rely on daily are safe and sound. Each technique has its unique strengths, and in combination, they form a robust defense against the risks of undetected weld failures. Through the diligent application of these methods, we uphold the highest standards of safety and quality in welded constructions.
3. Assessing Weld Quality Through Destructive Testing
To guarantee the utmost quality and safety in welding, destructive testing is indispensable. This rigorous approach involves sacrificing a part of the welded material to scrutinize its characteristics and performance thoroughly. Unlike non-destructive methods, these tests intentionally push the weld to its breaking point to provide a clear picture of its strength and durability under stress.
The Macro Etch Test: Revealing the Weld's Inner Secrets
Imagine slicing through a weld and magnifying its inner world. The Macro Etch test does precisely that. It unveils the weld's internal structure by polishing a section and bathing it in acid, which etches away to reveal any hidden flaws. Inspectors can then detect issues with weld penetration, the melding of base and filler metals, and any imperfections like cracks or voids. This test is like an open book, offering a glimpse into the weld's core and the quality of the welding process.
The Tensile Test: Measuring Weld Strength
Strength is a non-negotiable attribute of a good weld, and the Tensile test is the ultimate measure of this quality. By pulling a welded sample apart until it fractures, this test quantifies the force needed to break the weld. The resulting data tells us if the weld can handle the stress it will face in real-world applications. It's a straightforward yet powerful way to ensure that a weld won't buckle under pressure.
The Bend Test: Testing Flexibility and Flawlessness
Flexibility is another critical trait of a reliable weld, and the Bend test is designed to assess just that. By bending a welded sample to a certain degree or until it cracks, this test can expose any surface or hidden defects. Whether it's a face bend, root bend, or side bend test, each variation targets a specific aspect of the weld's resilience. A weld that can bend without breaking is a sign of excellent craftsmanship and material integrity.
In essence, destructive testing methods are a vital component of welding quality assurance. They provide concrete proof of a weld's ability to perform under various conditions and are often used alongside non-destructive methods for a full assessment. While these tests may destroy a sample, the insights gained are crucial for refining welding techniques, meeting industry standards, and ensuring the safety of structures that play a critical role in our daily lives.
4. Navigating the Next Frontier in Weld Inspections
The landscape of weld inspections is on the cusp of a revolution, with emerging technologies set to redefine the standards of accuracy, efficiency, and safety in the field. These advancements are not just incremental improvements but are shaping up to be game-changers in how we approach the critical task of ensuring weld quality.
Embracing Digital Transformation
The digital wave is sweeping across the weld inspection industry, bringing with it a suite of sophisticated tools that are transforming traditional practices. For instance, software capable of intricate data analysis is now a staple in the inspector's toolkit. It can swiftly interpret results from various testing methods, pinpointing flaws with a level of precision that was once beyond human capability.
Consider the use of drones, which are fast becoming indispensable in the inspection of expansive or challenging structures. These unmanned aerial vehicles, equipped with high-definition cameras and sensors, can safely navigate areas that are otherwise risky or inaccessible to human inspectors. The benefits are manifold: enhanced safety for inspection personnel, reduced downtime, and considerable cost savings.
Harnessing the Power of AI and Robotics
Artificial intelligence (AI) and machine learning are at the forefront of predictive maintenance. By analyzing historical inspection data, AI algorithms can forecast potential weld failures, allowing for preemptive action to avert accidents. This proactive approach is invaluable for maintenance scheduling and long-term asset management.
Robotics, too, is carving out a role in routine inspections. Robots can tirelessly perform checks with unwavering precision, freeing up human inspectors to focus on more complex analysis and decision-making tasks. This collaboration between human expertise and robotic consistency is setting a new standard in weld inspection practices.
Advancing Safety and Precision
The paramount concern in weld inspections is the safety of both the inspectors and the structures they assess. The integration of technology like drones and robotic systems significantly reduces the need for human presence in hazardous environments, thereby minimizing the risk of workplace accidents.
The precision of inspections is also set to reach new heights. Advanced equipment and analytical software enable inspectors to uncover issues with an unprecedented level of detail, ensuring that every decision regarding weld integrity is informed and reliable.
Streamlining Inspection Workflows
The future also promises a more streamlined inspection workflow. The shift from paper-based to digital documentation simplifies the management of inspection records, making it easier to access, analyze, and share critical data. This digital transition paves the way for improved collaboration and communication across all stages of construction and maintenance.
In conclusion, the horizon for weld inspections is bright with the promise of technological innovation. These advancements are not just enhancing current practices but are paving the way for a new era of smarter, safer, and more efficient inspections. As the industry adapts to these tools and methods, we can expect welded structures to meet ever-higher benchmarks of quality and safety, safeguarding the infrastructure that underpins our modern world.
5. Ensuring Safety and Excellence: The Future of Weld Inspections
As we conclude, it's clear that the meticulous practice of weld inspections is not just about achieving technical precision; it's a vital safeguard for the safety and durability of structures in manufacturing and construction. The inspection methods we've discussed—from the straightforward visual checks to the more complex radiographic and ultrasonic testing—equip us with a detailed toolkit for identifying any defects, whether they're on the surface or hidden within.
Looking ahead, the field of weld inspections is poised for a technological leap forward. Innovations like drone surveillance and sophisticated imaging techniques are set to become commonplace, revolutionizing the way we ensure the safety and quality of welded structures. These advancements will not only improve the accuracy of inspections but also make them more efficient, setting new industry benchmarks.
The true value of these inspection techniques lies in their ability to prevent catastrophic failures, safeguard lives, and uphold the integrity of industries that are the backbone of our economy. For professionals in the field, mastering these techniques is more than just a job—it's a commitment to upholding the highest standards of construction and manufacturing. In the end, the art and science of weld inspections are essential, reflecting our dedication to excellence and the well-being of society at large.
Sharing is Caring
Feedback
At WeldWins, we know we aren't perfect which is why we're always looking for ways to improve. You can help us do better by taking 2 minutes to fill out our simple feedback form.
Any and all feedback is welcome. It could be a complaint, an idea, or even just a comment, we'll always be grateful to hear what you think.