What is Plasma Arc Welding and How Can It Transform Metal Joining?
June 25, 2024
10 min read
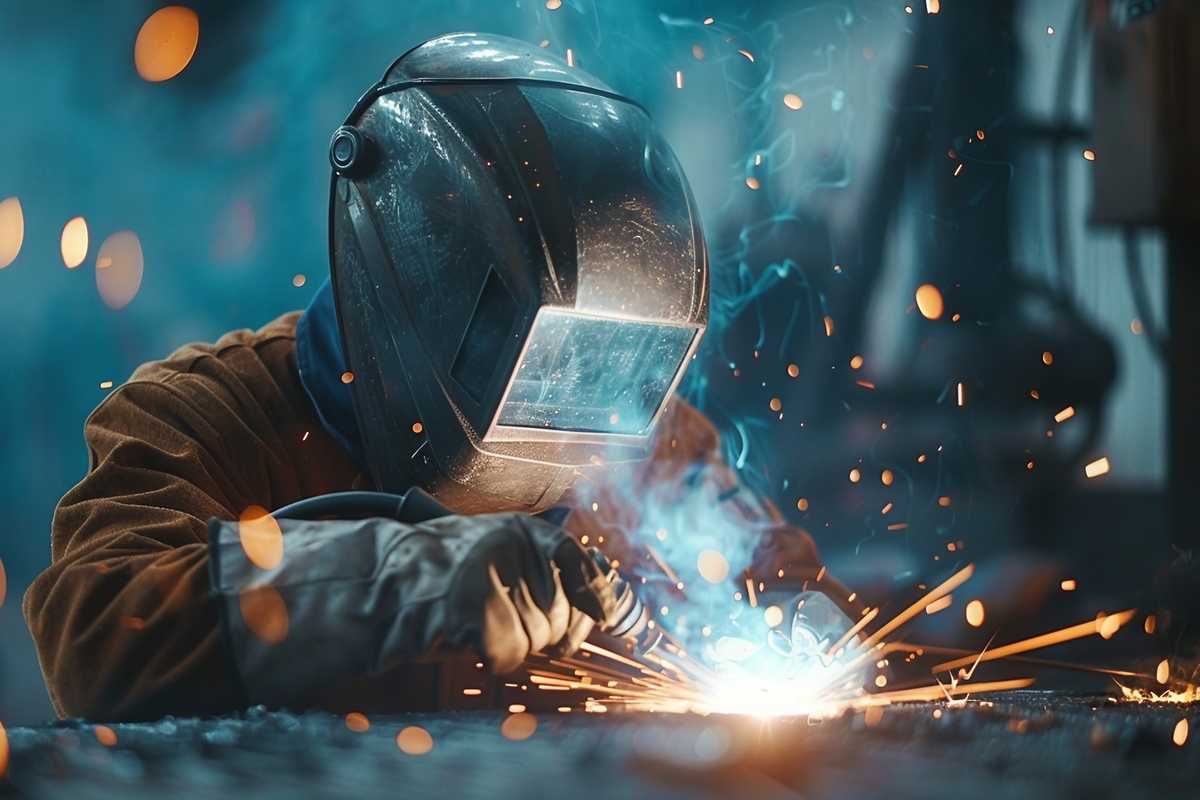
Plasma Arc Welding (PAW) is a high-precision technique that welders must thoroughly understand to achieve mastery. Unlike traditional methods, PAW uses a concentrated plasma arc, offering unmatched control for joining metals. This guide will take you through the essential techniques, modes of operation, and the distinct advantages that PAW brings to the table.
To excel in PAW, it's crucial to grasp the different operational modes—microplasma, medium current, and keyhole. Microplasma is perfect for delicate tasks, such as welding thin metal sheets or intricate components, due to its low current range and minimal heat application. Medium current mode steps up the power, ideal for thicker materials, balancing precision with the capability to handle more substantial metal sections. The keyhole mode is the powerhouse, suited for thick materials, creating a "keyhole" as the plasma jet penetrates through the workpiece, resulting in strong, single-pass welds.
The benefits of PAW are plentiful. It delivers precision that leads to robust, high-quality welds. Its adaptability spans across various applications, from crafting aerospace parts to assembling complex medical devices, where weld integrity is critical. Although PAW comes with its set of challenges, such as equipment costs and maintenance needs, the investment pays off with the superior capabilities of the technique.
In the sections to follow, we'll dive deeper into the components of the plasma torch, the intricacies of the welding circuit, and the specific currents needed for diverse welding tasks. We'll also provide a balanced view of PAW's pros and cons, supplemented with real-world examples from industries that benefit from its application. By the end of this guide, you'll have a comprehensive understanding of PAW, empowering you to harness this advanced welding technology to its fullest potential.
1. Plasma Arc Welding: Unveiling the Process and Its Modes
Plasma Arc Welding (PAW) is a cutting-edge technique that has transformed metal joining. It utilizes plasma, an electrically charged gas with incredible heat, to fuse metals together. The process begins by igniting an electric arc between a tungsten electrode and the metal workpiece. This arc superheats a gas—typically argon—until it ionizes into plasma. The plasma is then directed through a narrow copper nozzle, which focuses the flow, intensifying the heat and velocity to create a plasma jet hot enough to melt metals.
PAW is versatile, with three main modes tailored for specific tasks. The microplasma mode is for delicate work, using low currents (0.1 to 15 amps) ideal for welding thin metal sheets or intricate parts with precision. Medium current mode, ranging from 15 to 200 amps, steps up the power for thicker materials, offering a balance between detail and strength. The keyhole mode is the most robust, using currents above 100 amps to penetrate through thick workpieces, forming a keyhole that fills with molten metal to create a durable, full-penetration weld in a single pass.
Each mode of PAW is designed for different applications, making it a flexible choice for projects ranging from fine electronic components to heavy industrial assemblies. Mastery of PAW means understanding how to control the plasma arc to achieve the best results for any given task.
2. The Superior Edge of Plasma Arc Welding
Plasma Arc Welding (PAW) stands out in the welding world for its unmatched precision and efficiency, making it the technique of choice for projects that require the utmost accuracy. Its ability to produce consistent, high-quality welds with minimal warping is a game-changer, especially when dealing with delicate or thin materials. This level of control is a boon for tasks that demand intricate welding, such as in the electronics industry where precision is non-negotiable.
Speed is another hallmark of PAW. It leaves traditional methods like TIG welding in the dust, achieving faster travel speeds without sacrificing weld quality. This translates to increased productivity, allowing manufacturers to complete projects quicker and more efficiently.
PAW's adaptability is another feather in its cap. It can seamlessly weld a diverse array of metals and alloys, from the stainless steel used in kitchen appliances to the titanium found in aerospace components. This versatility is invaluable in sectors that work with multiple material types. Moreover, PAW's compatibility with automation paves the way for uniform, repeatable results in mass production settings.
The technique's prowess isn't limited by material thickness either. Whether joining ultra-thin sheets or hefty metal blocks, PAW's concentrated arc can be finely tuned to the task, ensuring optimal penetration and reducing the heat-affected zone. This preserves the integrity of the material close to the weld, which is crucial in applications like medical device manufacturing where material properties must remain unaltered.
Outdoor welding can be fraught with challenges, but PAW's arc stability holds steady even in breezy conditions. This reliability is essential for construction and repair work in open environments, where other welding processes might struggle.
Aesthetically, PAW scores high as well. The neat, clean welds it produces often require little to no finishing work, saving valuable time and resources. This aspect is particularly important in consumer goods and automotive industries, where the appearance of a weld can be just as important as its strength.
Industries that prioritize safety and performance, such as aerospace and automotive, have embraced PAW for its consistent results. In aerospace, for example, the integrity of a weld can mean the difference between safety and disaster, making PAW's precision non-negotiable.
In essence, PAW's combination of precision, speed, versatility, and quality makes it an indispensable asset in the welding industry. These strengths not only improve the efficiency and outcome of welding projects but also drive innovation in metalworking.
3. Navigating the Hurdles of Plasma Arc Welding
Plasma Arc Welding (PAW) is a sophisticated technique that comes with its own set of hurdles. The cost of PAW equipment is notably higher than that of more common welding methods like TIG or MIG. This can be a tough pill to swallow for small businesses or solo welders who are considering upgrading to PAW. The high price tag is linked to the advanced technology and precision components that make PAW so effective, but it also means a heftier initial investment.
The complexity of PAW is another obstacle. It's not just about buying the equipment; you also need to know how to use it. PAW demands a higher skill level than other welding methods, requiring welders to have a steady hand and a keen eye for detail. This means more time and money spent on training before a welder can perform PAW efficiently.
Maintenance is another area where PAW can be more demanding. The plasma torch and its parts are high-tech and sensitive to damage. They need regular check-ups and can be costly to repair or replace if something goes wrong. This is because PAW components are finely tuned and can be easily damaged if not handled correctly.
However, it's not all doom and gloom. There are ways to tackle these challenges. Investing in top-notch equipment and training can pay off in the long run by reducing maintenance costs and downtime. Automated PAW systems can also make the process more user-friendly, cutting down on the need for highly skilled manual work.
Moreover, the precision of PAW can lead to less wasted material and better-quality welds, which can help recoup the initial costs over time. By choosing projects that make the most of PAW's strengths, businesses can see a good return on their investment.
In essence, while PAW does come with its fair share of challenges, such as higher costs, a steep learning curve, and maintenance demands, these can be managed with careful planning and investment in quality resources. By understanding and addressing these issues, welders and businesses can integrate PAW into their workflow and reap the substantial benefits it offers.
4. Plasma Arc Welding: Revolutionizing Industry Standards
Plasma Arc Welding (PAW) is not just another welding process; it's a revolution in precision and efficiency that's reshaping how industries approach joining metals. Its unmatched accuracy and control make it indispensable in fields where the stakes are high and the margins for error are slim.
Take the aerospace industry, for example. Here, PAW is the hero, creating flawless welds on airframes and engine components that must endure the rigors of flight and the vacuum of space. The technique's finesse is perfect for the delicate, thin-walled tubes in aircraft, where a single flaw could lead to disaster.
In the world of automobiles, PAW's precision is equally crucial. It's the go-to method for assembling parts like exhaust systems and gearboxes, where every millimeter counts. The heat of the plasma arc is so well-controlled that it prevents warping, ensuring each part fits perfectly and performs flawlessly.
The medical sector relies on PAW's clean and precise welds for life-saving devices. Implants and surgical instruments, often made from tough stainless steel or lightweight titanium, benefit from the gentle touch of PAW, which maintains the integrity of these critical tools.
Electronics manufacturing also leans on PAW's ability to join tiny, heat-sensitive components without causing collateral damage. The focused arc ensures that the surrounding parts stay cool and intact, preserving the delicate electronic assemblies.
When it comes to energy—be it nuclear reactors or solar panels—PAW is there, too. It's capable of penetrating thick, sturdy materials, creating joins that can withstand the intense conditions of power generation and last for decades.
And let's not forget the marine industry, where the strength of a ship or submarine's hull is paramount. PAW's deep-penetrating welds hold up against the relentless pressure of the ocean's depths, proving that this technique is as versatile as it is precise.
In every application, PAW is changing the game, delivering speed, accuracy, and a level of versatility that other welding methods can't match. As technology advances and industries demand more from their welds, PAW is poised to become even more integral to manufacturing and repair, proving that in the world of welding, precision is power.
5. Harnessing the Future: The Expanding Role of Plasma Arc Welding
As we wrap up our comprehensive journey through the world of Plasma Arc Welding (PAW), it's clear that this advanced technique is more than just a method—it's a pathway to the future of fabrication and repair. We've delved into the mechanics behind plasma generation, the sophisticated design of the plasma torch, and the detailed welding circuitry. We've also highlighted the adaptability of PAW across its various operational modes, from the finesse of microplasma to the robustness of keyhole welding, showcasing its suitability for a spectrum of material thicknesses and specialized tasks.
PAW's standout features—its rapid welding speeds and pinpoint accuracy—have established it as a prized asset in fields where precision is paramount. This technology shines in its capacity to work with diverse materials, proving indispensable in industries ranging from the precision of aerospace engineering to the intricate requirements of electronic assembly.
Despite the hurdles such as the upfront cost of equipment and the demand for skilled technicians, we've explored practical solutions that help mitigate these issues. The investment in PAW can yield long-term dividends, with its efficiency and superior weld quality often offsetting initial expenses.
Looking ahead, the evolution of industry standards and the escalating need for superior welding solutions signal a growing prominence for PAW. Technological advancements and broader access to specialized training are likely to make PAW more accessible, broadening its application and influence. The trajectory for PAW is set towards innovation, as it continues to push the limits of welding capabilities.
In essence, PAW is not just maintaining pace with the demands of modern manufacturing—it's setting the pace, ensuring that today's technology is ready to meet the challenges of tomorrow. For intricate component work or durable structural connections, PAW is poised to remain a vital instrument in the welder's toolkit, embodying the fusion of skill and technology in the art of joining metals.
Sharing is Caring
Feedback
At WeldWins, we know we aren't perfect which is why we're always looking for ways to improve. You can help us do better by taking 2 minutes to fill out our simple feedback form.
Any and all feedback is welcome. It could be a complaint, an idea, or even just a comment, we'll always be grateful to hear what you think.