Is Plasma Arc Welding the Future of Metal Fabrication?
April 28, 2024
11 min read
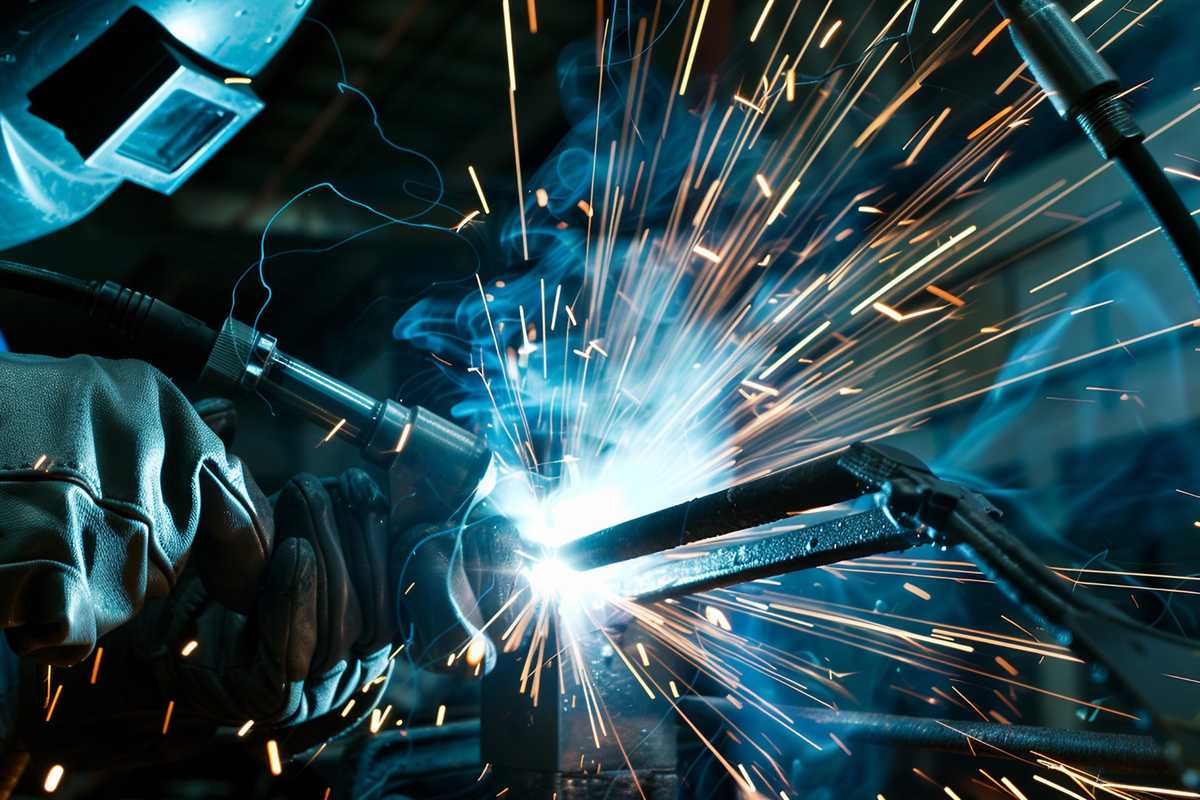
Welcome to the Precision Era: Unveiling Plasma Arc Welding
Welcome to the precision era of metal fabrication, where Plasma Arc Welding (PAW) stands as a beacon of innovation. This advanced technique has revolutionized the way we join metals, combining strength and accuracy to meet the highest quality standards. PAW's unique ability to harness a plasma arc for welding ensures that each joint is not just strong, but also crafted with the utmost precision.
PAW's edge lies in its clean, precise welds, which outshine those achieved by conventional welding methods. This makes it the method of choice for intricate projects in aerospace, automotive, and manufacturing industries, where every detail counts. With PAW, even the most complex designs are executed with a finesse that was once thought impossible.
In this guide, we'll delve into the intricacies of Plasma Arc Welding. We'll dissect its mechanics, introduce the specialized tools it employs, and discuss the distinct features that set it apart from other welding techniques. We'll celebrate the benefits PAW brings to the table, such as enhanced precision and control, and consider how these lead to more efficient welding operations. We'll also explore the diverse applications of PAW across various industries and tackle the challenges and limitations that come with this sophisticated technology.
Embark on this journey with us to discover why Plasma Arc Welding is a pivotal element in the world of metalwork and how it continues to redefine the standards of fabrication.
1. Understanding Plasma Arc Welding: The Art of Precision in Metalwork
Plasma Arc Welding (PAW) is a sophisticated form of welding that has carved a niche for itself in the realm of metal fabrication due to its unmatched precision and efficiency. To fully grasp the prowess of PAW, it's essential to start with the basics: plasma—the fourth state of matter. When a gas is superheated, it ionizes into plasma, a mixture of charged particles including ions and electrons. PAW leverages this electrically conductive plasma to generate a highly focused arc capable of melting metals for fusion.
The PAW process begins with a tungsten electrode housed in a meticulously designed torch. This electrode is the heart of the arc. The plasma arc is then funneled through a constricted copper nozzle, intensifying the heat and velocity of the plasma to produce a concentrated and potent welding flame. This flame reaches temperatures high enough to melt the workpiece, allowing two pieces of metal to coalesce into a single entity.
What distinguishes PAW from other welding techniques is its dual-gas system. It employs a primary gas, which is ionized into plasma to start the arc, and a secondary shielding gas that protects the molten weld pool from atmospheric impurities. This two-gas approach is crucial for achieving pristine, high-caliber welds.
PAW can be utilized in two distinct modes: transferred arc mode and non-transferred arc mode. In transferred arc mode, the arc leaps from the electrode to the workpiece, incorporating it into the electrical circuit for welding purposes. Non-transferred arc mode keeps the arc confined within the torch, which is ideal for plasma cutting or spraying applications.
The true beauty of PAW lies in the control it offers. The narrow arc minimizes splatter, reduces the heat-affected zone, and consequently, diminishes metal warping. This level of precision is particularly beneficial for tasks requiring exactitude, such as the fabrication of delicate aerospace parts or complex electronic assemblies.
In summary, Plasma Arc Welding is akin to a master painter's fine brushstroke, delivering a degree of detail and finesse that broader, traditional welding methods cannot achieve. Its fusion of a tight arc with a dual-gas system yields unparalleled precision, cementing PAW's role as an essential technique in contemporary metalworking.
2. Harnessing the Power of Precision: Advantages of Plasma Arc Welding
Plasma Arc Welding (PAW) stands at the forefront of metal fabrication, offering a myriad of advantages that surpass conventional welding techniques. Its primary benefit is the remarkable precision and control it provides. With a tightly focused plasma arc, welders can target specific areas with extreme accuracy, minimizing the risk of damaging sensitive materials or intricate designs due to excessive heat.
The consistency and purity of welds achieved through PAW are unparalleled. The stable arc ensures deep penetration and a clean weld pool, resulting in stronger and more reliable joints. This is crucial in industries like aerospace and medical equipment manufacturing, where the slightest imperfection can lead to catastrophic outcomes. PAW's versatility also shines through its ability to join a wide range of metals, including those that are typically challenging to weld, making it the tool of choice for complex and high-stakes projects.
When it comes to speed, PAW excels by rapidly melting and fusing metals, leading to faster production times and reduced labor costs. The process is ripe for automation, which can further enhance productivity and guarantee consistency across multiple welds—key factors for large-scale manufacturing operations.
PAW's flexibility is another significant asset. It is equally effective in manual and automated settings, capable of performing delicate micro-welding tasks as well as joining large metal sections. This flexibility ensures that PAW can be tailored to meet the specific needs of various industries, making it an invaluable technique for custom metalwork solutions.
Moreover, PAW is recognized for its cleaner operation. It produces fewer welding fumes and operates at lower noise levels compared to other methods like Shielded Metal Arc Welding (SMAW) or Gas Metal Arc Welding (GMAW). This contributes to a better work environment and helps companies meet stringent health and safety regulations.
In summary, the combination of precise control, high-quality welds, efficiency, adaptability, and cleaner operations makes Plasma Arc Welding a preferred method for businesses that demand excellence in weld quality and operational effectiveness.
3. Plasma Arc Welding: A Multifaceted Tool for Diverse Industries
Plasma Arc Welding (PAW) is a versatile and precise welding method that has become indispensable across various sectors. Its ability to produce high-quality welds with minimal defects makes it the preferred choice for projects where traditional welding falls short. Let's explore how PAW is applied in different industries, showcasing its adaptability and the unique benefits it offers.
Aerospace: Engineering Safety and Performance
In the aerospace industry, precision is paramount. PAW is instrumental in constructing aircraft components, such as engine parts and airframe structures. The method's controlled heat prevents distortion of the thin metal sheets used in aircraft exteriors, ensuring structural integrity and safety at high altitudes.
Automotive: Crafting the Cars of Tomorrow
The automotive industry continually seeks to enhance vehicle efficiency through the use of lighter, stronger materials. PAW's pinpoint accuracy allows for the assembly of complex parts that contribute to the overall performance and safety of modern vehicles.
Electronics: Precision on a Micro Scale
As electronic components become increasingly miniature, PAW offers the precision necessary to join small parts without causing thermal damage to surrounding areas. This ensures the longevity and reliability of electronic devices that have become integral to our daily lives.
Medical Devices: Fusing Metals with Finesse
The medical field depends on PAW for its clean, precise welds, especially when working with metals like titanium and stainless steel. These materials are common in medical devices and implants, which require adherence to stringent health and safety standards.
Pipes and Tubes: Ensuring Durability Under Pressure
PAW is adept at producing deep penetration welds needed for pipes and tubes in high-pressure environments, such as power plants and chemical processing facilities. These welds are crucial for maintaining the integrity of pipelines that transport vital resources.
Energy: Constructing a Sustainable Future
In both traditional and renewable energy sectors, PAW plays a critical role in building robust and precise components. For instance, in solar energy, PAW is used to accurately join thin films and conductive materials, which are essential for the efficiency and longevity of solar panels.
PAW's adaptability and the quality of its welds make it an invaluable tool in industries where metal joints must be reliable, durable, and precise. As we continue to push the boundaries of technology and material science, PAW's role is only expected to grow, further solidifying its importance in the future of industrial fabrication.
4. Overcoming the Obstacles of Plasma Arc Welding
Plasma Arc Welding (PAW) is a cutting-edge technique that offers unmatched precision in metal fabrication. However, it comes with its own set of challenges that businesses and welders must navigate to leverage its full potential. Here, we address the common obstacles associated with PAW and provide practical insights to help you overcome them.
Investment in High-End Equipment
The initial setup for PAW can be costly due to the need for advanced equipment such as a specialized power supply, a plasma torch, and computerized controls for precise welding parameters. This investment might be substantial for some businesses, but it's important to consider the long-term benefits of superior weld quality and the potential for automation. Regular maintenance is also crucial to ensure the longevity and performance of this equipment.
Demand for Specialized Skills
PAW requires welders to have a deep understanding of the process, including managing plasma gas flow, arc length, and heat input. This expertise often necessitates additional training, which can be an investment in both time and money. However, the investment in training can pay off through the ability to perform high-quality welds that meet stringent industry standards.
Selecting the Right Materials
Not all metals are suitable for PAW; it excels with certain materials and specific thicknesses. For example, reflective metals like aluminum and stainless steel may present challenges due to their tendency to deflect the plasma arc. It's essential to match the welding method with compatible materials to ensure consistent and strong welds.
Prioritizing Safety Measures
The intense nature of the plasma arc means that safety cannot be overlooked. Welders must use appropriate protective gear, including eye protection with the correct filter shade to prevent arc eye, and adhere to safe operating practices. Establishing a culture of safety reduces the risk of accidents and ensures a healthy work environment.
Balancing Speed with Precision
While PAW is known for its precision, it may not be the fastest welding method available. In scenarios where production speed is critical, the meticulous nature of PAW might be seen as a disadvantage. However, the trade-off for precision can lead to fewer errors and less rework, ultimately saving time and resources in the long run.
Environmental Impact
PAW can produce harmful fumes and ultraviolet radiation, making it imperative to have effective ventilation and safety protocols in place. Protecting the health of welders and minimizing environmental impact should be a priority for any business employing this technology.
In summary, while PAW presents certain challenges, understanding and preparing for these hurdles allows businesses to effectively incorporate this technology into their operations. The key is to balance the initial investment and training with the long-term benefits of high-quality, precise welds. With the right approach, PAW can be a valuable asset in the metal fabrication industry.
Conclusion: The Future is Bright with Plasma Arc Welding
In wrapping up our deep dive into the world of Plasma Arc Welding (PAW), we've seen how this innovative method is transforming the field of metal fabrication. Our journey through the article has highlighted PAW's exceptional ability to deliver precise and high-quality welds, thanks to its focused and intense plasma arc. This technology is not just reducing the likelihood of metal distortion, but it's also setting new benchmarks for weld quality.
The advantages of PAW are clear and compelling. Its unmatched precision, control, and efficiency are invaluable, particularly in high-stakes sectors like aerospace and automotive manufacturing. PAW's meticulous nature ensures that even the most complex and critical metalwork is executed with unparalleled precision and skill.
Yet, it's important to recognize the hurdles associated with PAW. The sophisticated equipment required comes with a high price tag, and the need for specialized training presents a steep learning curve for operators. These factors may initially seem daunting, but the investment in quality tools and proper training can yield substantial returns. Mastering PAW opens up opportunities for superior craftsmanship and innovation in metalworking.
Throughout this guide, we've established that PAW is more than just a welding technique; it's a symbol of progress in the metal fabrication industry. For those who aim to push beyond the capabilities of conventional welding, PAW offers a pathway to achieving new levels of excellence and efficiency. Looking ahead, we can expect the influence of Plasma Arc Welding to grow, cementing its role as a pivotal force in the ongoing evolution of metal joining techniques.
Sharing is Caring
Feedback
At WeldWins, we know we aren't perfect which is why we're always looking for ways to improve. You can help us do better by taking 2 minutes to fill out our simple feedback form.
Any and all feedback is welcome. It could be a complaint, an idea, or even just a comment, we'll always be grateful to hear what you think.