How Can Shielding Gases Improve Your TIG Welding?
June 26, 2024
11 min read
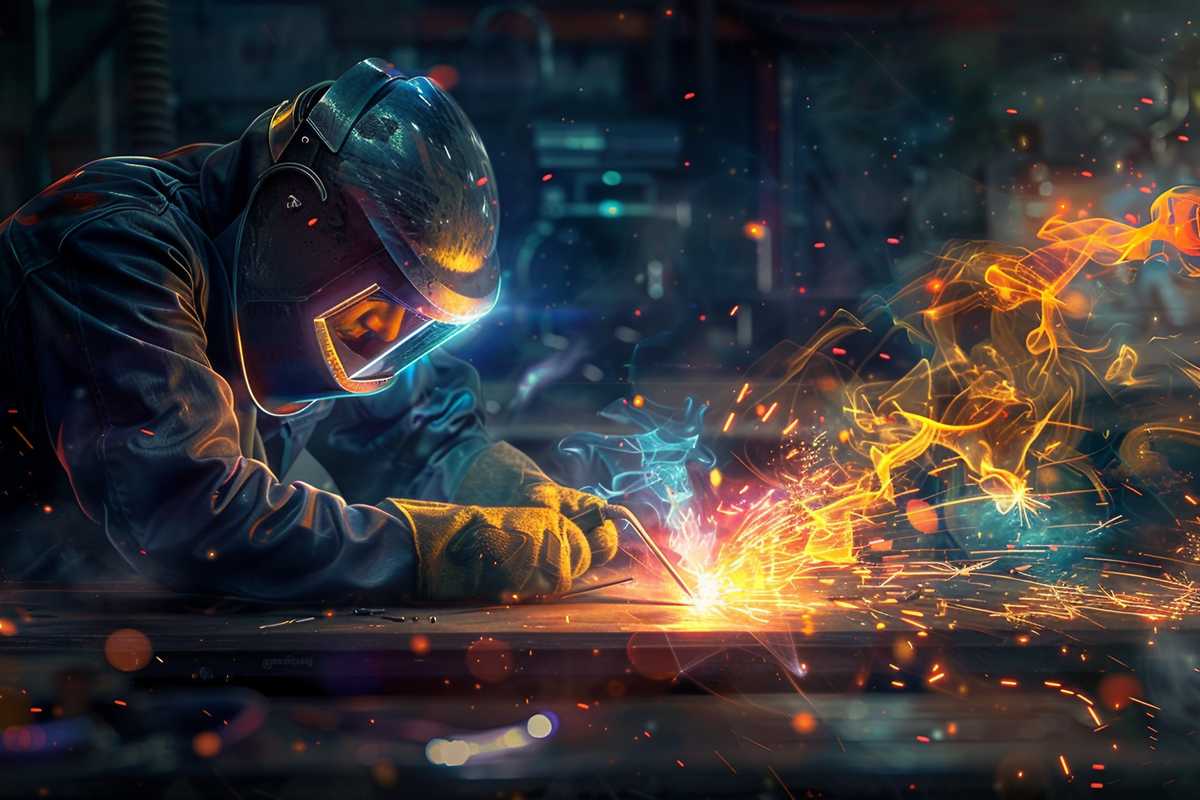
TIG welding, a method celebrated for its precision and the superior strength of its welds, is indispensable in industries where detail and durability are non-negotiable. Think of the sleek lines of a spacecraft, the robust frame of a car, or the intricate design of a metal sculpture—TIG welding plays a pivotal role in crafting each one. But what's the secret behind those perfect welds? It's all about the shielding gas.
Shielding gases are the unsung heroes of TIG welding. They're like an invisible shield, guarding the molten metal from harmful air contaminants like oxygen and moisture. Without this protection, the metal could become riddled with holes or rust, weakening the weld. That's why choosing the right shielding gas isn't just a box to tick—it's a make-or-break decision for your welding project.
In this guide, we'll dive into the world of shielding gases. You'll learn not only why they're important but also how to pick the perfect one for your project. Whether you're a seasoned welder or just starting out, we'll shed light on how to use shielding gases to turn good welds into great ones. Let's embark on this journey to master the art of TIG welding with the ultimate guide to shielding gases.
1. Mastering Shielding Gases for Optimal TIG Welding Results
In the precise world of TIG welding, the choice of shielding gas is a pivotal factor that can make or break the quality of your welds. Shielding gases are the invisible guardians that protect the molten metal from the damaging effects of the air around us. Without the right gas, your weld could end up with imperfections like porosity or oxidation, which weaken the structure and look unsightly.
The main job of a shielding gas is to create a protective bubble around the welding zone. This bubble keeps out oxygen, nitrogen, and water vapor, which at high welding temperatures, can react with the metal and cause defects. By selecting the appropriate shielding gas, you ensure a pristine environment for the weld pool, leading to stronger and more visually appealing results.
Different gases also affect the welding arc and how heat is transferred to the metal. For example, some gases can make the weld pool more fluid, allowing for smoother beads and better-looking welds. On the flip side, the wrong gas choice can introduce contamination, reduce protection, or destabilize the arc, resulting in weak welds that may crack under pressure or create a mess with excessive spatter.
To sum it up, the role of shielding gases in TIG welding is crucial. They maintain the purity of the weld area, shape the characteristics of the welding process, and determine the strength and durability of the final weld. It's essential for welders to know the properties of different shielding gases to make smart choices that lead to top-notch welding outcomes.
2. Argon: The Preferred Shielding Gas for TIG Welding
Argon stands out as the top choice for TIG welding due to its unique properties that ensure high-quality welds. Its heavier-than-air density forms a protective layer over the weld pool, shielding it from air contaminants that can weaken the weld. This is particularly crucial for metals like aluminum and magnesium, which are more sensitive to impurities.
The inert nature of Argon means it doesn't react with the metal, preserving the purity of the weld. This is essential for materials such as stainless steel, where maintaining corrosion resistance is key. Additionally, Argon's stable arc allows for smoother welding with less spatter, making it ideal for welding thin materials where precision is vital.
However, Argon isn't perfect for every situation. Its lower thermal conductivity may not be suitable for welding thicker materials that need deeper penetration. In such cases, a narrower penetration profile from pure Argon might not suffice, and a mixed gas could be more appropriate.
Argon is best used for:
- Welding materials of thin to medium thickness.
- Ensuring high-quality results on sensitive metals.
- Projects where a clean and attractive weld finish is important.
- Creating an uncontaminated welding environment.
For projects requiring deeper weld penetration or on thicker materials, consider blending Argon with other gases to achieve the desired results.
In essence, Argon is a versatile and reliable shielding gas for a broad spectrum of TIG welding tasks. Its ability to create a contaminant-free environment and support a stable welding arc makes it a popular choice. However, understanding when to use pure Argon and when to opt for a gas mixture is crucial for the success of your welding project.
3. Helium: Supercharging Your TIG Welds
Helium is the secret weapon for TIG welders tackling tough jobs that require intense heat and deep weld penetration. Think of Helium as the turbocharger in a car—it boosts performance, allowing you to weld thicker materials with precision and strength.
Why is Helium so effective? It boils down to science. Helium's atoms are nimble and carry heat exceptionally well—much better than the commonly used Argon. This means that when you use Helium as your shielding gas, you're cranking up the arc's temperature. That extra heat is a game-changer for welding hefty materials, ensuring the weld penetrates deeply and bonds securely, minimizing common issues like incomplete fusion.
Helium isn't just about heat; it's also about coverage. Its quick atoms spread the warmth over a larger area, which is perfect when you're working with metals like copper or aluminum that quickly conduct heat away. With Helium, the heat stays where you need it, ensuring a consistent, even weld pool and reducing problems like cold lapping.
But with great power comes great responsibility. Helium's intense heat isn't suitable for all materials—it can be too much for thin or delicate pieces, risking warping or burn-through. And because Helium creates a more fluid weld pool, you'll need a steady hand and sharp skills to manage it and avoid messy spatter.
Cost is another consideration. Helium tends to be pricier than Argon, so many welders use it in a blend to get the best of both worlds without breaking the bank. A mix of Argon and Helium can be tailored to the job's needs, offering a compromise between cost and welding performance.
In essence, Helium can elevate your TIG welding, especially for challenging tasks that demand deep penetration and high heat. It's a powerful addition to your toolkit, but it's essential to use it wisely, considering the material you're welding and the end goal of your project. With the right approach, Helium can help you achieve durable, high-quality welds that look as good as they hold.
4. Hydrogen in TIG Welding: A Double-Edged Sword
While Hydrogen isn't typically the star of the TIG welding show, it plays a critical role for those in the know. Dubbed the specialist's choice, Hydrogen can elevate the welding quality of specific metals, but it demands respect and expertise to avoid pitfalls.
Adding a dash of Hydrogen to your primary shielding gas can work wonders, especially with austenitic stainless steels. It's like adding a secret ingredient to a recipe that brings out the best flavors—in this case, a cleaner weld zone with a visually pleasing finish. Hydrogen's high thermal conductivity spreads heat more evenly, reducing the chance of unsightly oxidation and ensuring the metal's natural luster shines through.
Moreover, Hydrogen's ability to lower the surface tension of the molten metal is akin to smoothing out wrinkles on a bedsheet, resulting in a sleek, flat weld bead that's as functional as it is aesthetically pleasing. This can be particularly beneficial when the appearance of the weld is just as important as its structural integrity.
However, Hydrogen's benefits come with a caution label. If mishandled, it can lead to hydrogen-induced cracking—imagine a glass that cracks as it cools from a hot state. This is a serious concern when welding high-strength steels, where cracks can compromise the entire structure. To prevent such issues, it's crucial to carefully manage Hydrogen levels and adhere to precise heating and cooling protocols.
It's also worth noting that Hydrogen isn't a one-size-fits-all solution. Certain metals, like aluminum, don't play well with Hydrogen and can suffer from porosity, resulting in weak and unreliable welds. Similarly, carbon steels and low alloy steels are also off the Hydrogen compatibility list due to increased cracking risks.
In essence, Hydrogen has the potential to significantly improve the TIG welding process, but it requires a knowledgeable and measured approach. It's essential for welders to be well-versed in the materials they're working with and to follow strict guidelines when incorporating Hydrogen into their gas mix to harness its advantages while steering clear of its hazards.
5. Crafting the Perfect Blend: Shielding Gas Mixtures for TIG Welding
Choosing the right shielding gas mixture for TIG welding is a critical step that can greatly affect the quality, speed, and cost of your welding projects. Each gas blend offers unique advantages tailored to different welding challenges, so understanding how to select the perfect mix is key to achieving superior welds.
For instance, combining Argon and Helium can give you the best of both worlds: Argon's stability for a consistent arc and Helium's heat for faster welding on thicker materials. If you're working with metals like aluminum or magnesium, a higher Argon content in the mixture is often the best choice to ensure a clean, uncontaminated weld pool.
When welding stainless steel, adding a small percentage of Hydrogen to Argon can lead to a cleaner weld pool and improved arc stability, resulting in a higher quality weld. However, it's important to note that Hydrogen should be used cautiously, as it can cause cracking in certain metals.
The position of welding also matters. For overhead or vertical welding, you might need a different gas mixture than for flat or horizontal positions due to gravity's effect on the weld pool. A higher Argon content can help maintain better control and arc stability in these challenging positions.
Material thickness is another consideration. While pure Argon is often sufficient for thin materials, adding Helium can help achieve deeper penetration in thicker materials due to its superior thermal conductivity.
Don't forget to factor in your welding process parameters, such as amperage and voltage settings, as they can interact with the shielding gas to influence arc characteristics and the final appearance of the weld. A mixture that's effective at low amperage might not perform as well at higher settings.
To make an informed decision, start by listing your project's requirements, including metal type, thickness, welding position, and desired weld characteristics. Consult with gas suppliers or welding handbooks for recommended mixtures, and consider conducting a test weld to assess the mixture's performance before starting a large project.
While the ideal gas mixture can enhance weld quality and efficiency, it's also crucial to consider the cost. Specialty gas mixtures can be more expensive, so weigh the benefits against your project budget.
In summary, selecting the right gas mixture for TIG welding is about understanding the interactions between different gases and how they affect various metals and welding conditions. By carefully choosing the most suitable mixture, you can ensure high-quality, cost-effective welds that meet your project's specific needs.
6. Final Thoughts: Elevating Your TIG Welding with the Right Shielding Gas
In the intricate dance of TIG welding, the choice of shielding gas plays a starring role in determining the strength, aesthetics, and integrity of your welds. This comprehensive guide has taken you through the characteristics of Argon, Helium, and Hydrogen—each with its own set of benefits for specific welding scenarios.
Argon has proven to be the all-rounder, favored for its adaptability and affordability, making it a staple for welding a variety of metals. Helium, on the other hand, has shown its prowess in generating the intense heat needed for welding thicker materials, ensuring deep and robust welds. Hydrogen, while less commonly used, offers a specialized advantage by producing exceptionally clean and smooth welds on certain types of stainless steel, though it requires careful handling due to its reactive nature.
We've also highlighted the strategic use of gas mixtures, which can be customized to conquer the unique challenges of each welding project. By considering the metal type, thickness, and the weld's desired attributes, you can craft a gas blend that brings out the best in your work.
While quality is paramount, we cannot ignore the impact of cost on your welding operations. It's important to strike a balance between the benefits of a particular gas or mixture and the associated expenses, ensuring that you deliver top-notch work without unnecessary costs.
As you refine your TIG welding skills, let the insights on shielding gases empower you. Apply the knowledge shared here to produce welds that are not only structurally sound but also visually impressive. Experiment with gas combinations, uphold safety standards, and aim for precision in every weld.
By choosing the optimal shielding gas for your projects, you'll not only meet the requirements but also surpass them, establishing a new benchmark for quality in your welding craft.
Sharing is Caring
Feedback
At WeldWins, we know we aren't perfect which is why we're always looking for ways to improve. You can help us do better by taking 2 minutes to fill out our simple feedback form.
Any and all feedback is welcome. It could be a complaint, an idea, or even just a comment, we'll always be grateful to hear what you think.