How Can You Master Welding Stainless Steel?
July 8, 2024
14 min read
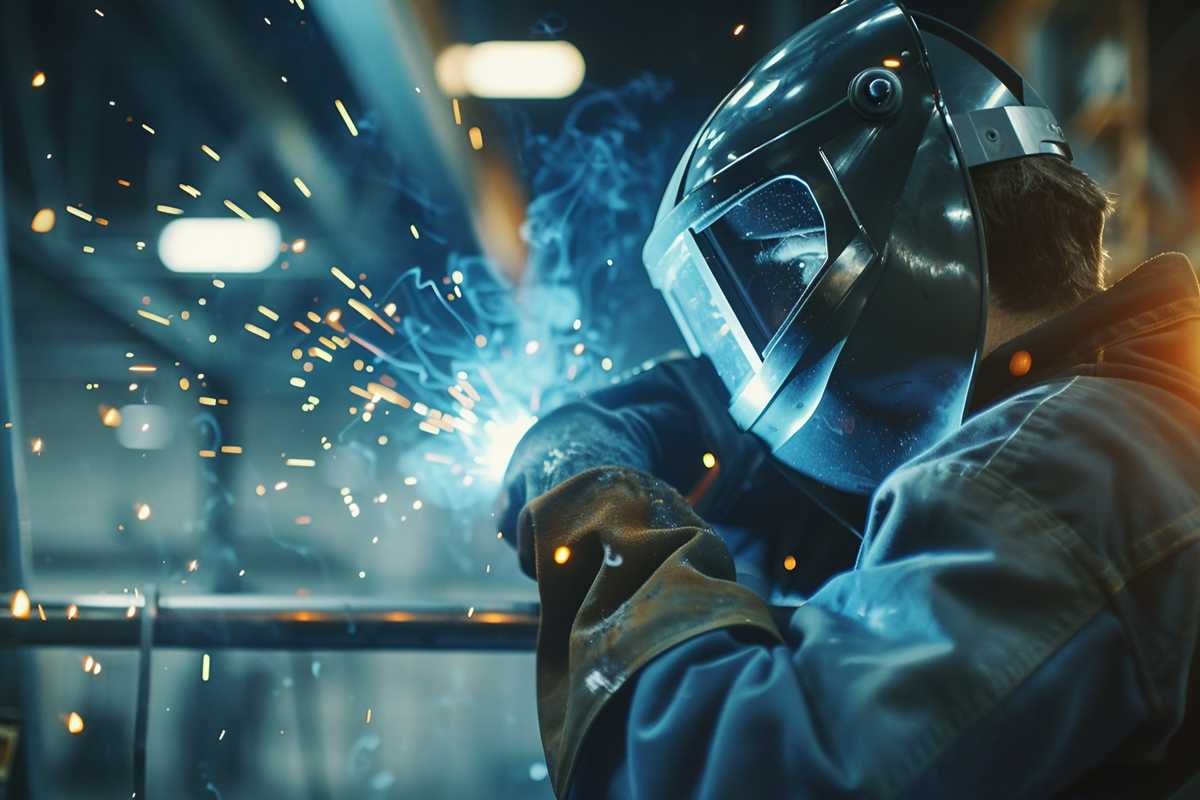
Embarking on the journey of welding stainless steel is akin to stepping into a world where precision meets durability. Revered for its robustness and resistance to the elements, stainless steel is a favorite in industries ranging from skyscraper construction to the creation of chef's knives. Yet, the path to perfecting stainless steel welds is fraught with unique challenges that can stump even experienced welders.
The common pitfalls when welding stainless steel—warping, discoloration, and weakened joints—are often the result of treating it like any other metal. But stainless steel is special; it demands a nuanced approach to preserve its celebrated qualities.
In this comprehensive guide, we'll unveil the secrets to successful stainless steel welding. We'll equip you with the know-how to sidestep common obstacles and share insights that will sharpen your skills, whether you're a seasoned welder or just starting out. By understanding the correct techniques and adopting best practices, you'll be well on your way to crafting welds that are not only strong but also visually impeccable. Join us as we navigate through the art and science of welding stainless steel, ensuring your projects endure the test of time.
1. The Essentials of Stainless Steel
To excel in welding stainless steel, it's imperative to understand what makes this material unique. Renowned for its resistance to corrosion, stainless steel stands out due to its composition. It's an iron-based alloy, enriched with a minimum of 10.5% chromium, which creates a protective chromium oxide layer on its surface, shielding the metal from rust and blemishes.
Stainless steel comes in various forms, each with specific characteristics that influence welding techniques:
-
Austenitic Stainless Steel: The most prevalent type, recognized for its superior formability and corrosion resistance. It's composed of high chromium and nickel levels, often supplemented with manganese and nitrogen. Grades 304 and 316 are typical examples.
-
Ferritic Stainless Steel: This variety has less nickel but more chromium than austenitic stainless steel, making it magnetic with somewhat lower corrosion resistance. It's commonly found in automotive parts, with grade 430 being a standard example.
-
Martensitic Stainless Steel: This type shares similarities with ferritic stainless steel but includes more carbon, allowing it to be hardened. It's suitable for items needing high strength and moderate corrosion resistance, like cutlery and hardware.
-
Duplex Stainless Steel: A hybrid of austenitic and ferritic types, duplex stainless steel boasts high strength and exceptional resistance to corrosion, especially stress corrosion cracking. It's typically used in harsh environments like chemical processing and seawater applications.
Welding stainless steel is distinct from welding carbon steel, mainly because of its heat sensitivity. Too much heat can cause warping and unwanted changes in the metal's structure, weakening the corrosion resistance of both the weld and the adjacent areas. Stainless steel also holds onto heat longer than carbon steel due to its lower thermal conductivity, raising the risk of distortion.
It's crucial to recognize the specific type of stainless steel you're dealing with, as each reacts differently to heat and necessitates unique welding approaches to preserve the weld's integrity. For example, austenitic stainless steel is relatively more forgiving and easier to weld than ferritic or martensitic types, which may need preheating and post-weld heat treatment to avert cracking.
In essence, a thorough understanding of stainless steel's composition and classification is vital for proficient welding. This knowledge dictates the welding method, choice of filler material, and necessary precautions to uphold the material's corrosion resistance and mechanical properties. Armed with this information, welders can tackle their projects with the confidence required to produce robust, long-lasting, and high-quality welds.
2. The Welder's Toolkit: Must-Have Equipment for Stainless Steel Projects
Embarking on a stainless steel welding project means gearing up with the right arsenal of tools. Each piece of equipment plays a pivotal role in ensuring your welding is precise, strong, and up to professional standards. Let's break down the essentials you'll need to transform raw metal into a work of strength and durability.
Selecting a Welding Machine
Your primary tool is the welding machine, and for stainless steel, precision is key. TIG welders are the go-to for their fine control, perfect for delicate or detailed work. However, if you're tackling thicker materials, a MIG welder can be your ally, offering efficiency and ease. Whichever you choose, ensure it has adjustable amperage to manage stainless steel's sensitivity to heat and avoid warping.
The Right Welding Wire or Rod
For MIG welding, match your wire to the stainless steel grade you're working with—this ensures a harmonious weld. TIG welders will need a filler rod, again, choosing one that complements the base metal to prevent corrosion and maintain strength.
Shielding Gas: Your Weld's Invisible Shield
Shielding gas is like an invisible protector for your weld, keeping contaminants at bay. MIG welding typically uses a mix of argon and carbon dioxide, while TIG welders will lean towards pure argon or an argon-helium blend for the cleanest, strongest welds.
Personal Protective Equipment: Safety First
Never skimp on safety. A top-notch welding helmet with auto-darkening lenses is a must to shield your eyes from harmful rays. Pair it with flame-resistant gloves, a sturdy welding jacket, and safety glasses to fend off sparks and spatter.
Clamps and Magnets: The Unseen Helpers
Welding clamps and magnets are your silent assistants, holding your workpiece steady and true. They're the unsung heroes that help you achieve that perfect alignment and prevent heat-induced warping.
Angle Grinder: The Multitasker
An angle grinder is your versatile sidekick, ready to cut, grind, or polish. It's indispensable for prepping your metal before you start and cleaning up your welds to a professional finish.
Cleaning Tools: The Foundation of a Strong Weld
A pristine surface is the starting point of a great weld. Use a stainless steel wire brush for a good scrub, and pair it with specialized cleaning chemicals to remove any oils or residues. This prep work is crucial to prevent weld contamination.
Equipping yourself with these essential tools sets you up for success in stainless steel welding. Quality tools lead to quality welds, so invest wisely and maintain your equipment for the best results. With this toolkit, you're ready to tackle any stainless steel project with confidence.
3. Essential Steps for Pre-Welding Preparation
The journey to a perfect stainless steel weld begins long before the first spark. Pre-welding preparation is the cornerstone of a successful welding project, ensuring that your work is not only strong but also free from any imperfections that could compromise its integrity. Let's walk through the critical steps to prepare your stainless steel, ensuring it's primed and ready for the welding torch.
Thoroughly Clean the Metal
The first commandment of welding preparation is cleanliness. Any oil, grease, or dirt on your stainless steel can ruin your weld before you even start. Use a commercial degreaser and a lint-free cloth to meticulously clean the surface. Remember, common steel wool or brushes are off-limits—they can leave behind tiny steel fragments that may cause rust. Instead, opt for a stainless steel-specific brush or a clean rag.
Eliminate Oxidation
Stainless steel can develop a thin, stubborn layer of chromium oxide that hinders the welding process. To remove this, gently scrub the welding area with a stainless steel brush or a non-metallic abrasive pad. This step is crucial for a clean weld that fuses properly without any barriers.
Measure, Cut, and Bevel
Accuracy is key when preparing your pieces. Measure twice and cut once to ensure your stainless steel fits perfectly. Straight edges and tight fits are your goals to avoid gaps that could weaken the weld. For thicker pieces, consider grinding a bevel along the edges to allow the weld to penetrate deeply, creating a stronger bond.
Secure the Pieces Firmly
With your pieces cut and prepped, it's time to lock them in place. Use clamps or a welding jig to hold the metal steady during the welding process. This not only prevents movement but also helps maintain the alignment you worked so hard to achieve. Double-check that your clamps are as clean as your workpiece to avoid transferring any contaminants.
Ensure Adequate Ventilation
Welding stainless steel can produce fumes that are harmful if inhaled. Protect your health by working in a well-ventilated area. If you're indoors, set up an exhaust system or position fans to keep fresh air circulating. And don't forget to wear the right respiratory protection.
Organize Your Workspace
A cluttered workspace can lead to accidents and mistakes. Take the time to organize your tools and equipment, placing everything within easy reach. This includes your welding machine, electrodes, filler material, and safety gear. A well-arranged space not only boosts your efficiency but also minimizes the risk of mishaps.
By meticulously following these pre-welding preparation steps, you're setting yourself up for success. A clean, well-prepared surface is the foundation of a superior weld, and an orderly workspace helps ensure the process goes smoothly. Now, with your stainless steel in prime condition, you're ready to start welding with confidence.
4. Mastering Stainless Steel Welding: MIG and TIG Techniques
When it comes to welding stainless steel, two techniques stand out for their effectiveness: Metal Inert Gas (MIG) and Tungsten Inert Gas (TIG) welding. Each method has its own advantages and specific steps to ensure a high-quality finish. Let's break down these techniques to help you achieve the best results on your stainless steel projects.
MIG Welding: Fast and Flexible
MIG welding is favored for its speed and adaptability, suitable for a range of stainless steel projects. Here's how to get it right:
-
Wire Selection: Pick a MIG wire that complements the stainless steel you're working with. For example, 308L wire is often used for 304 stainless steel.
-
Machine Settings: Dial in the correct voltage and amperage on your MIG welder. The thickness of your metal dictates these settings; thicker metal requires more power.
-
Shielding Gas: Opt for a tri-mix gas—90% helium, 7.5% argon, and 2.5% carbon dioxide. This combination ensures a stable arc and superior weld quality.
-
Welding Speed: Keep a consistent pace with your welding gun to allow the weld pool to form properly. Too fast and your welds will be weak; too slow and you risk burning through the metal.
-
Stick-Out Length: Maintain a short wire stick-out, about 1/4 inch, to prevent oxidation and maintain control over your weld.
TIG Welding: Precision and Aesthetics
TIG welding is the go-to for precision work, especially on thinner stainless steel or when a high-quality finish is required. Follow these steps for a flawless TIG weld:
-
Electrode Choice: Select a tungsten electrode suited to your stainless steel type. A 2% lanthanated tungsten is a versatile option.
-
Tungsten Preparation: Sharpen your electrode to a fine point for a focused arc and better control of the weld pool.
-
Filler Metal: Use a filler rod that matches your stainless steel's composition to ensure a strong, compatible weld.
-
Amperage Settings: Set your TIG welder's amperage based on the material thickness—one amp per thousandth of an inch is a good rule of thumb.
-
Shielding Gas: Pure argon is ideal for TIG welding stainless steel, helping to prevent oxidation and achieve a clean weld.
-
Bead Technique: Weld in short beads to control heat input and avoid warping the metal. Let the area cool between passes.
-
Heat Management: Since stainless steel is heat-sensitive, use a heat sink or back purge with argon to maintain the metal's shape and weld quality.
By adhering to these steps and practicing regularly, you'll enhance your MIG and TIG welding skills. Remember, the key to success is patience and precision, so take your time to perfect your technique for strong and visually appealing stainless steel welds.
5. Fine-Tuning Your Stainless Steel Welding Approach
Achieving excellence in stainless steel welding is about more than just joining two pieces of metal; it's about precision, finesse, and a commitment to quality. To help you elevate your welding game, we've compiled a list of key strategies that will ensure your welds are not only strong but also aesthetically pleasing.
Regulate Heat Like a Pro
Stainless steel doesn't take kindly to excessive heat—it distorts and its properties can degrade. To combat this, apply heat in controlled, short bursts and let the metal cool down intermittently. Think of it like sprinting and then walking to catch your breath. You can also use a heat sink—a piece of copper or aluminum placed behind the weld—to absorb excess heat and keep things even.
Match Filler Material to Your Steel
Imagine wearing a wool sweater in a cotton outfit—it just doesn't blend well. The same goes for welding: your filler material should match the "outfit" of your stainless steel. For example, when welding the popular 304 stainless steel, opt for a 308L filler rod to ensure the weld area remains resistant to corrosion and maintains its strength.
Prioritize a Clean Workspace and Materials
Cleanliness is next to godliness in welding. Before striking an arc, scrub the metal surface with a stainless steel brush (and only use it for stainless steel to avoid contamination). Wipe it down with a solvent to remove any oils or dirt. This step is crucial; any leftover grime can cause porosity or inclusions, weakening your weld.
Pace Your Welding for Perfection
Welding speed is a balancing act—too fast, and the weld won't penetrate deeply; too slow, and you risk overheating. Practice makes perfect here. Aim for a consistent speed that allows the weld bead to flow evenly, creating a smooth, uniform finish.
Shielding Gas: Your Invisible Ally
The right shielding gas can make or break a weld. For MIG welding, a tri-mix gas (helium, argon, and carbon dioxide) provides a stable arc and superior results. TIG welders should stick to pure argon for its clean, oxidation-free protection. This gas acts like an invisible shield, keeping the air's impurities away from your molten metal.
Keep Contamination at Bay
Use stainless steel-specific tools to avoid introducing foreign particles that can lead to rust. It's like using a separate cutting board for meats and vegetables to prevent cross-contamination in the kitchen.
Post-Weld Cleanup for Lasting Quality
After welding, it's not just about how the weld looks—it's about preserving its resistance to corrosion. Techniques like pickling (applying a chemical paste) and passivation (treating the metal to restore its protective layer) are like giving your weld a spa treatment, ensuring it stays clean and corrosion-free.
By integrating these tips into your welding routine, you'll notice a marked improvement in your welds' quality. Remember, welding is an art form that rewards patience and practice. Keep refining your skills, and don't hesitate to try new methods to discover what yields the best results for your projects.
6. Wrapping Up: Your Path to Stainless Steel Welding Mastery
As we conclude our comprehensive guide, it's clear that welding stainless steel is both an art and a science. We've journeyed through the specifics of stainless steel's unique characteristics, the critical tools for your welding projects, and the vital steps to prepare your materials. Our deep dive into MIG and TIG welding techniques has equipped you with the knowledge to select appropriate materials and apply the right methods for impeccable welds.
It's important to remember that high-quality welding goes beyond simply following steps; it's about grasping the reasons behind each action. For instance, managing the heat during welding is essential to prevent the stainless steel from warping and to preserve its structural integrity. Likewise, maintaining a clean and orderly workspace is imperative not only for the quality of your work but also for your safety.
Consider every stainless steel project as a learning experience, an opportunity to hone your skills. Challenges will arise, but with each one, you're building your expertise. Embrace these moments as valuable lessons on your path to becoming a skilled welder.
We hope you'll keep this guide close at hand, revisiting the advice and techniques as you continue to practice. With persistent effort and meticulous attention to detail, you can achieve mastery in stainless steel welding, creating joints that are not only robust and long-lasting but also visually striking. So, gear up, stay safe, and enjoy the rewarding process of welding stainless steel to perfection.
Sharing is Caring
Feedback
At WeldWins, we know we aren't perfect which is why we're always looking for ways to improve. You can help us do better by taking 2 minutes to fill out our simple feedback form.
Any and all feedback is welcome. It could be a complaint, an idea, or even just a comment, we'll always be grateful to hear what you think.