How Can You Choose the Right Welding Electrode for Your Project?
June 29, 2024
10 min read
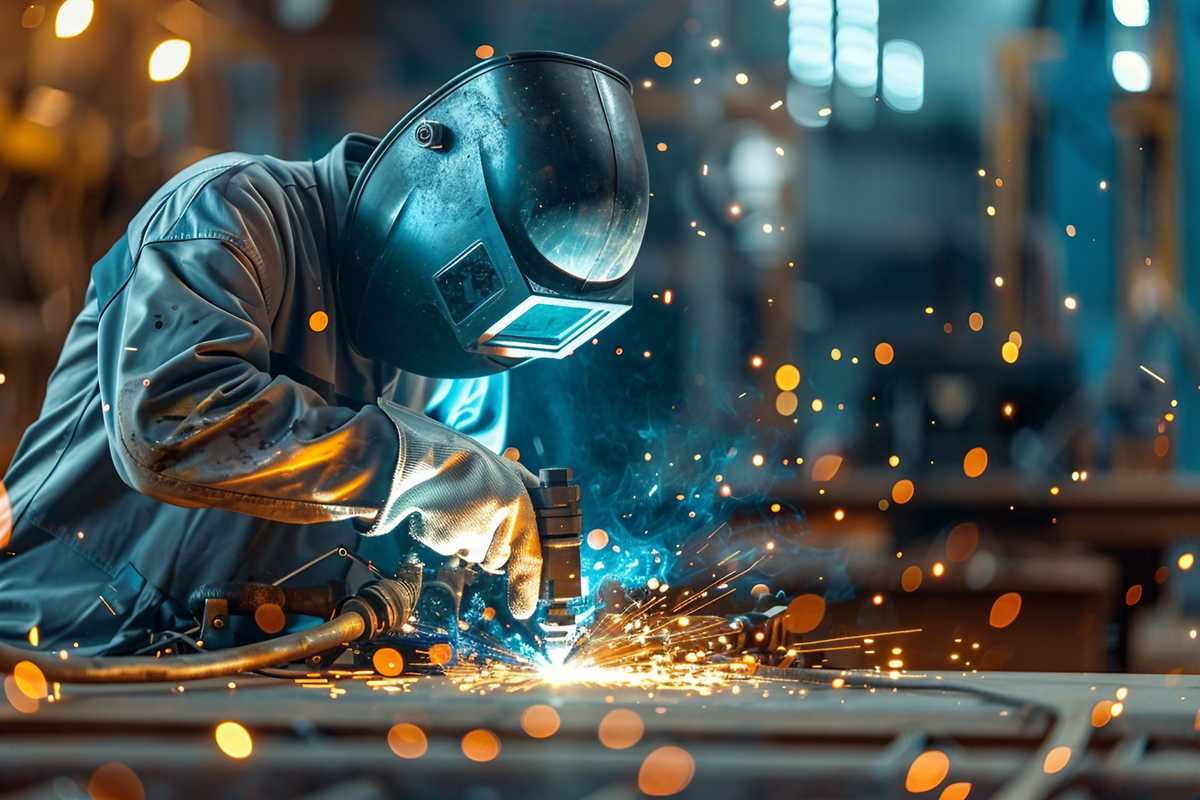
Embarking on the journey of welding requires not just skill but also a profound understanding of the tools and materials involved. At the heart of this craft lies the welding electrode, a pivotal element that channels the electric current necessary to meld materials together. The choice of electrode is a critical one, impacting the weld's integrity, longevity, and finish.
Navigating the intricate world of welding electrodes can be daunting, with a plethora of types and specifications at your disposal. This guide is tailored for both the experienced welder seeking to perfect their craft and the novice eager to lay a strong foundation. We aim to simplify the complexities surrounding welding electrodes, equipping you with the knowledge to select and utilize the ideal electrode for your projects.
In this comprehensive exploration, we will distinguish between consumable and non-consumable electrodes, decipher the coding on welding rods, and highlight the most prevalent types of welding rods and their uses. Additionally, we will impart essential tips for storing your welding rods to maintain their prime condition.
By the conclusion of this guide, you will possess the insights necessary to make informed decisions regarding welding electrodes, thereby elevating the caliber of your work and ensuring the triumph of your welding endeavors. Let's begin this enlightening expedition into the world of welding electrodes.
1. The Essential Guide to Welding Electrodes
Welding electrodes are the lifeline of the welding process, acting as the critical link that channels electricity to forge metals together. Their selection is not just a matter of choice but a decisive factor that influences the strength and quality of the weld. It's essential to recognize that electrodes vary widely, and the right match is key to a successful weld.
Electrodes fall into two primary categories: consumable and non-consumable. The choice between them hinges on the nature of the welding task.
Consumable electrodes are the workhorses of the welding world. They do more than just conduct electricity; they melt and fuse with the metals being joined, supplying additional material to the joint. This makes them integral to the welding process. Typically, these electrodes are composed of materials akin to the metals being welded, ensuring a compatible and robust joint.
Non-consumable electrodes, in contrast, are the stalwarts that don't melt away. They're crafted from resilient materials like tungsten that can endure extreme temperatures without degrading. In welding techniques such as TIG (Tungsten Inert Gas) welding, these electrodes are used when the filler material is applied separately, not consumed from the electrode itself.
Grasping the differences between consumable and non-consumable electrodes is a fundamental step in honing your welding skills. The decision to use one over the other is dictated by factors such as the metal type, the weld's required strength, and the position of the weld.
In essence, welding electrodes are indispensable in the welding process, serving as the pathway for electrical current and, for consumable types, providing the filler material needed for the weld. Knowing which type of electrode to use is crucial for optimal results in your welding projects, ensuring each joint is as strong and durable as possible.
2. Unraveling the Mystery of Welding Rod Identification Numbers
Selecting the appropriate welding rod can be perplexing, especially when confronted with a series of numbers that resemble a cryptic code. These numbers, however, are not random; they follow a standardized classification that provides valuable insights into the rod's performance and suitability for various welding tasks. Let's demystify these numbers to empower you to choose the ideal welding rod for your project with ease.
A welding rod's identification numbers are a sequence of four or five digits, each revealing a different aspect of the rod's characteristics. It's essential for welders to grasp the significance of these numbers to ensure the correct application and to achieve optimal welding results.
The initial two or three digits represent the rod's tensile strength, which is the maximum stress it can withstand without breaking. This strength is expressed in thousands of pounds per square inch (psi). For instance, a rod labeled with '60' at the beginning can handle a stress of up to 60,000 psi.
The third digit indicates the welding positions for which the rod is suitable. This number is key because each welding position—flat, horizontal, vertical, or overhead—presents unique challenges. Selecting a rod that is compatible with the welding position is crucial for creating a robust and secure weld.
The final one or two digits describe the rod's coating type and the electrical current it requires. This information helps you understand the rod's penetration depth, whether it works with alternating current (AC), direct current (DC), or both, and additional traits such as the amount of slag produced and the ease of its removal.
Armed with the knowledge of what these numbers signify, you can confidently navigate the selection process for welding rods. This understanding not only contributes to superior welding outcomes but also promotes safety and efficiency in your welding projects. With this clear guide, you're now ready to interpret welding rod numbers like an expert.
3. Selecting the Right Welding Rod: A Practical Guide
The welding rod you select is a critical factor in the success of your welding job. It affects not just the strength of your weld, but also its appearance and longevity. With a variety of welding rods on the market, each tailored for different tasks and materials, it's essential to understand which one to use for your specific project. Let's break down the characteristics of some of the most commonly used welding rods to guide you in making the best choice.
E6010: The Deep Penetrator
The E6010 welding rod is a go-to for tough jobs like pipeline welding where you need deep penetration to create a strong bond. It's especially good for welding through rust or paint because its intense arc slices right through surface contaminants. This rod is compatible with DC power sources and is prized for its ability to produce durable welds under difficult conditions. However, it's not the easiest rod to handle and requires a welder with a good level of skill to manage its vigorous arc.
E7018: The Versatile Performer
If you're looking for a welding rod that's user-friendly and versatile, the E7018 is your match. It's a favorite for projects like building frameworks because it lays down smooth, clean welds with very little spatter. You can use it with both AC and DC machines, and its special low-hydrogen coating helps prevent cracks and other common welding flaws. This rod is perfect for jobs that demand a neat finish and a weld that's both strong and reliable.
E7024: The Efficiency Expert
When you're working on flat or horizontal welds and time is of the essence, reach for the E7024 rod. Known for its high-speed welding capabilities, this rod allows you to deposit more material faster than many others. It has a heavy flux coating that stabilizes the arc and results in a smooth, even weld bead that looks great. It's particularly handy for welding thick materials and is commonly used in industries like shipbuilding and construction.
By understanding the specific benefits and ideal applications of these popular welding rods, you can make an informed decision that ensures your welding is not only strong and durable but also visually appealing. Whether you're repairing a pipeline, erecting a steel structure, or working on a large-scale manufacturing project, choosing the right welding rod is essential for a successful outcome.
4. Best Practices for Welding Rod Storage
To achieve the best results in welding, it's not just about skill and precision during the welding process; how you store your welding rods also plays a pivotal role. Proper storage is essential to prevent damage to the rods, which can lead to compromised weld quality. Here's a concise guide to keeping your welding rods in top-notch condition:
Ensure a Moisture-Free Environment
Welding rods are highly sensitive to moisture, which can cause hydrogen-induced cracking in your welds. To avoid this, store the rods in a place that's free from dampness. If they're not in moisture-resistant packaging, move them to a sealed container or consider using a rod oven for those particularly vulnerable to moisture, like low-hydrogen electrodes.
Maintain a Stable Temperature
Just like moisture, extreme or fluctuating temperatures can negatively impact welding rods. Find a cool, stable spot for storage, steering clear of areas that experience high heat or direct sunlight, such as the inside of a vehicle on a sunny day.
Keep Rods Clean and Contaminant-Free
Contaminants like oil, dirt, or workshop residue can transfer from the rod to your weld, causing defects. Store your rods in a spot that's clean and free from such pollutants. Before placing the rods in storage, double-check that the area or container is clean.
Prefer Original Packaging for Storage
The packaging from the manufacturer is designed to shield the rods from environmental damage. Use this to your advantage and keep the rods in their original packaging as long as possible before use.
Implement a First-In, First-Out System
To prevent welding rods from degrading over time, use older stock first. This rotation ensures that no rod sits unused for too long, which could lead to a decline in performance.
Adhere to Manufacturer's Storage Recommendations
Different welding rods might have unique storage needs. Always check the manufacturer's instructions for any specific storage advice to ensure you're not inadvertently shortening the life of your rods.
By following these straightforward storage guidelines, you can preserve the integrity of your welding rods, ensuring that each weld you perform is as strong and defect-free as possible. Proper storage is a reflection of the professionalism and care you put into your welding work.
5. Wrapping Up: Your Path to Welding Mastery
In our comprehensive journey through the world of welding electrodes, we've armed you with the essentials to make informed choices that will enhance the strength and quality of your welds. From the basics of electrode roles to the intricacies of their classification codes, we've covered the critical information you need to navigate the welding landscape with confidence.
We've highlighted the importance of understanding whether an electrode is consumable or non-consumable and how each serves a distinct purpose in the welding process. The consumable electrodes meld into your work, adding strength, while non-consumable ones stand resilient, guiding your weld without melting away.
The deep dive into the coding on welding rods has equipped you with the ability to decipher tensile strength, welding positions, and other key characteristics. For example, knowing that an E6010 rod is designed for deep penetration and is ideal for challenging conditions like pipeline welding can be the difference between a mediocre weld and an exceptional one.
We've also showcased popular welding rods such as the E7018, known for its versatility and user-friendliness, and the E7024, celebrated for its efficiency in specific welding positions. Understanding when and where to use these rods will help you achieve not only a strong bond but also a visually pleasing finish.
Furthermore, we've emphasized the significance of proper storage for your welding rods. By keeping them dry, at a stable temperature, and away from contaminants, you'll maintain their integrity and performance. Remember, good storage practices reflect the care and professionalism you invest in your craft.
As we conclude this guide, remember that the right electrode is pivotal to the success of your welding projects. Invest time in understanding your options, practice proper storage, and always prioritize safety. With the insights gained here, you're well on your way to becoming a proficient welder, capable of tackling any project with skill and assurance.
Sharing is Caring
Feedback
At WeldWins, we know we aren't perfect which is why we're always looking for ways to improve. You can help us do better by taking 2 minutes to fill out our simple feedback form.
Any and all feedback is welcome. It could be a complaint, an idea, or even just a comment, we'll always be grateful to hear what you think.