How Can You Identify Metals for Welding Like a Pro?
May 25, 2024
10 min read
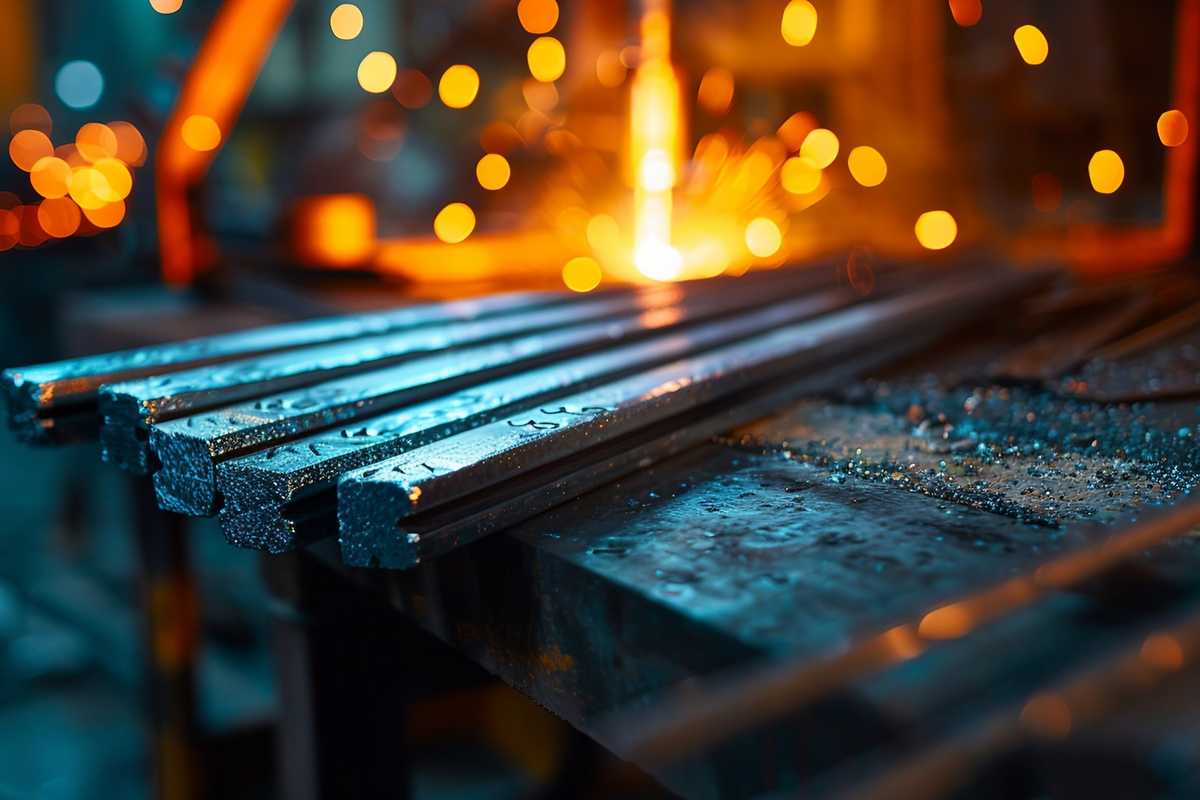
Welding is a craft that blends technical skill with a touch of artistry. At the heart of this craft is the ability to identify the metals you're working with. This skill is essential because each metal has its own set of characteristics that dictate the welding approach, from the choice of filler material to the protective measures needed during the process.
This guide is your companion in the art of metal identification. It's tailored for both experienced welders and those new to the trade, providing a clear understanding of how to recognize different metals and their properties. We'll cover the basics, such as the visual cues like color and texture, and delve into more complex aspects, such as a metal's melting point and how it reacts to corrosion.
By the end of this guide, you'll have a solid foundation in identifying metals, which will empower you to make smart choices in your welding projects. You'll learn to match the right materials and techniques to ensure your work is not only visually appealing but also structurally robust and designed to last. Let's embark on this journey into the world of metals and unlock the secrets to their identification.
1. Mastering Metal Characteristics for Welding Excellence
In the world of welding, understanding the unique characteristics of different metals is key to achieving a successful and durable weld. Each metal responds differently to heat and stress, and recognizing these responses is essential for choosing the appropriate welding method. Let's break down the essential physical and chemical properties that welders must grasp to ensure top-notch welding results.
Key Physical Properties of Metals
Physical properties are observable traits that help us identify and work with metals without altering their chemical makeup. Here are the most important ones:
- Color: The hue of a metal can be a quick identifier. For example, aluminum boasts a bright, silvery sheen, while steel has a more subdued, grayish tone.
- Density: A metal's weight per unit volume influences how it reacts to heat. Denser metals like steel require more heat to weld than lighter ones like aluminum, which are also more susceptible to distortion.
- Melting Point: Knowing the temperature at which a metal melts is crucial for applying the right amount of heat. Too much heat can damage the metal, while too little may result in a weak weld.
- Thermal and Electrical Conductivity: Metals differ in their ability to transfer heat and electricity. This affects the amount of welding current needed and the speed at which you'll work to maintain a stable weld pool.
- Thermal Expansion: Metals expand when heated and contract when cooled. Understanding a metal's expansion rate is vital to prevent warping and misalignment during and after welding.
Chemical Properties Influencing Welding
Chemical properties dictate how metals interact with their environment, particularly during chemical reactions like rusting or tarnishing. Here's what to consider:
- Corrosion Resistance: Metals vary in their ability to withstand corrosion. Choosing a metal with the right level of resistance is critical, especially in environments that accelerate corrosion, to ensure the longevity of the weld.
By becoming proficient in these metal properties, welders can make educated choices about materials, welding techniques, and necessary safety measures to create welds of the highest quality. This knowledge forms the bedrock of safe and efficient welding practices.
2. Deciphering Metals at a Glance: A Welder's Visual Guide
Being able to quickly identify metals by sight is an invaluable skill for any welder. It streamlines the selection process for welding techniques and materials, ensuring efficiency and precision in your work. While it doesn't replace detailed chemical testing, visual inspection is a fast and effective first step. Let's dive into the key visual indicators that can help you pinpoint the type of metal you're dealing with.
Recognizing Metals by Their Looks
Each metal has a unique set of visual characteristics that can serve as identification markers:
- Aluminum: This metal has a characteristic silvery-white color and is notably reflective. Its surface is typically smooth, adding to its distinct appearance.
- Copper: Easily recognizable by its reddish-brown color, copper stands out among other metals. Over time, it may develop a green patina due to oxidation.
- Stainless Steel: Known for its sleek, mirror-like finish, stainless steel is not only aesthetically pleasing but also resistant to rust, which helps maintain its shine.
- Iron and Carbon Steel: These metals are darker and have a more matte surface. Rust is a common issue if they're not adequately protected, giving them a reddish or orange tinge.
The Feel of Metal: Texture and Grain
The way a metal feels to the touch can also be a clue:
- Smoothness: Metals like aluminum are smooth to the touch, which can help differentiate them from others.
- Grain Visibility: On freshly cut steel, you might see lines or patterns on the surface, which can help you tell it apart from metals with a uniform appearance.
Decoding Metal Markings
Manufacturers often stamp metals with codes that provide valuable information:
- Mill Markings: These markings can tell you about the metal's grade, origin, and sometimes its composition. Learning to read these can be a game-changer in metal identification.
The Magnet Test: A Simple Yet Effective Trick
One of the quickest ways to sort metals is by using a magnet:
- Ferrous vs. Nonferrous: If a magnet sticks to the metal, it's likely iron or steel. Metals like aluminum and copper won't attract a magnet, indicating they are nonferrous.
The Spark Test: Observing Metal Under Friction
Although it involves a bit more than just looking, the spark test is a visual technique:
- Spark Patterns: When you grind a metal, pay attention to the sparks. Long, yellow sparks suggest carbon steel, while stainless steel produces shorter, less bright sparks.
Corrosion: What Rust and Patina Can Tell You
The way a metal corrodes can also be a telltale sign:
- Corrosion Colors: Aluminum might show white powdery spots, while copper tends to turn green. Stainless steel might display a rainbow hue if it starts to corrode.
By paying attention to these visual cues and combining them with your existing knowledge of metals, you can quickly identify what you're working with. However, for the most accurate results, especially in critical applications, always confirm your visual assessment with more precise testing methods.
3. Evaluating Metal Identification Techniques: Old School vs. High-Tech
In the realm of welding, correctly identifying the metal at hand is crucial for ensuring the quality and safety of the work. Welders have a range of techniques at their disposal, from time-honored methods that have been around for generations to cutting-edge technologies that provide detailed analyses. This section will help you understand these different approaches and decide which is best for your welding projects.
Time-Honored Techniques for Metal Testing
Let's look at some traditional methods that have been the backbone of metal identification for years:
-
Spark Test: By grinding the metal and studying the sparks, you can get clues about its identity. Each metal emits a unique spark pattern; for instance, a long, white spark could indicate a high-carbon steel. This method is quick but requires a seasoned eye to interpret the results accurately.
-
Hardness Test: A simple file can reveal a lot about a metal's hardness. If the file digs in easily, the metal is likely softer, like aluminum. A metal that resists filing, such as hardened steel, is much tougher. This test is straightforward but gives you more of a general idea than exact numbers.
-
Magnet Test and Visual Inspection: A magnet can instantly tell you if a metal is ferrous (magnetic) or nonferrous. Additionally, observing the metal's color, texture, and any surface markings can provide further insights. These methods are fast and non-destructive but aren't foolproof and can sometimes lead to incorrect assumptions.
-
Chemical Test: Applying specific chemicals to the metal's surface can cause reactions that indicate its identity, like a color change or a particular type of residue. This approach requires a careful hand and a good understanding of the chemical reactions involved.
High-Tech Methods for Precise Metal Analysis
Now, let's explore the modern techniques that offer a more detailed look at a metal's composition:
-
Spectrometry: This advanced method analyzes the light spectrum emitted by a metal when energized, revealing its elemental makeup. It's highly accurate and can pinpoint the exact type of metal you're working with.
-
X-ray Fluorescence (XRF): XRF technology uses X-rays to excite a metal's atoms and then measures the secondary X-ray emissions to determine its composition. It's a non-destructive technique that can be performed on-site, though the equipment is costly.
-
Ultrasonic Testing: This technique employs high-frequency sound waves to detect flaws in metals. While it's not primarily used for identification, it can give you insights into the metal's grain structure and overall quality.
-
Eddy Current Testing: By inducing magnetic fields in metals and measuring the eddy current responses, this method can detect surface flaws and, to some extent, differentiate between metal types based on the variations in the currents.
Making the Right Choice: Traditional vs. High-Tech
Selecting between traditional and modern methods involves considering factors like the required level of accuracy, budget, and equipment availability. Traditional techniques are more accessible and easier to perform without specialized training, making them suitable for quick assessments. However, they may not provide the detailed information that modern methods can offer.
On the flip side, modern techniques deliver a comprehensive analysis and high accuracy but at a higher cost and with the need for specialized knowledge. They are particularly valuable when precise metal composition is critical, such as in high-stakes structural welds or when dealing with specialized alloys.
In summary, as a welder, you need to balance the pros and cons of each method to choose the one that aligns with your project's needs. While traditional methods are valued for their simplicity, modern technologies cater to the demands for precision in contemporary welding tasks.
4. Solidifying Your Welding Craft: The Final Word on Metal Identification
In wrapping up this comprehensive guide, we've journeyed through the essential aspects of metal identification, a fundamental skill that welders must hone to ensure excellence in their craft. From the visual cues of color and texture to understanding the significance of melting points and conductivity, we've dissected the traits that dictate the best welding practices for various metals.
For welders, the ability to distinguish between metals like the commonly used carbon steel, the corrosion-resistant stainless steel, or the versatile aluminum is crucial. It's the difference between a mediocre job and a masterpiece. By sharpening your skills in visual identification and interpreting a metal's physical properties, you're not only avoiding potential errors but also reinforcing the quality and safety of your welds.
We've also delved into the evolution of metal identification techniques, contrasting the tried-and-true methods like spark and hardness tests with the precision of modern spectrometry. While the old-school approaches offer simplicity and quick insights, the advanced technologies provide unparalleled accuracy, essential for critical welding applications.
Ultimately, the mastery of metal identification transcends mere procedure. It's a testament to your dedication to the welding profession. It's about crafting welds that are as resilient as the metals they join, ensuring that your projects endure over time and adhere to the strictest standards of excellence and safety. By integrating the insights from this guide into your practice, you're poised to elevate your welding projects to new heights of durability and integrity.
Sharing is Caring
Feedback
At WeldWins, we know we aren't perfect which is why we're always looking for ways to improve. You can help us do better by taking 2 minutes to fill out our simple feedback form.
Any and all feedback is welcome. It could be a complaint, an idea, or even just a comment, we'll always be grateful to hear what you think.