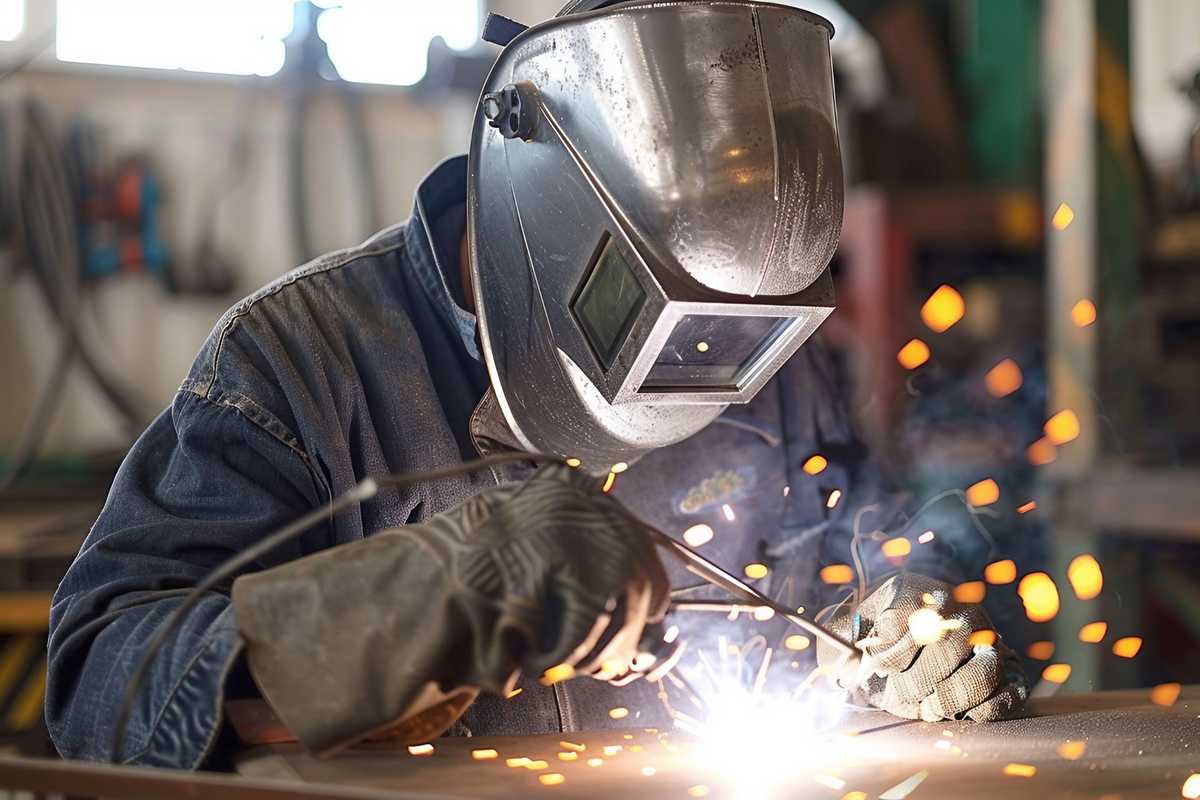
Welding is a craft that blends science and skill, where every detail matters. A common hurdle that welders face is undercut—a defect that can weaken a weld and threaten the stability of the entire structure. This flaw may seem minor, but its effects are far-reaching, potentially leading to structural failures when least expected.
In this comprehensive guide, we'll dive into the world of undercut prevention. We'll define undercut, discuss its implications, and provide you with the know-how to spot and avoid it. This article is designed for anyone in the welding field, from the seasoned veteran to the novice just starting out. Our goal is to arm you with the knowledge and techniques needed to produce impeccable welds, free from the risks of undercut. Let's embark on this educational journey and elevate the quality of your welding projects.
1. Decoding Undercut: The Welding Defect Explained
In the intricate dance of welding, every move counts towards the strength and durability of the final joint. One misstep that can jeopardize the entire performance is the appearance of undercut—a welding defect that's as harmful as it is common. But what is undercut, and how can you recognize it before it's too late?
Undercut manifests as a groove or trench that forms at the weld's edge or where the weld meets the base metal, known as the toe. This groove indicates that the metal hasn't been filled in correctly, leaving a weak spot in the weld. It's a telltale sign of a weld gone wrong, potentially reducing the thickness of the base metal and compromising the structural integrity of the entire piece.
Spotting undercut is straightforward if you know what to look for. Keep an eye out for a visible indentation running along the weld's edge, which can be seen unaided or with a simple magnifying tool. You might also notice the weld bead looking uneven or the surface showing signs of poor fusion with the base metal.
The stakes are high with undercut—it's not just a cosmetic issue. This defect can concentrate stress, becoming a breeding ground for cracks, especially when the welded structure is under repeated stress or load during its service life. Such a weak point can lead to the premature failure of the welded assembly, making it crucial to prevent undercut from the outset.
In essence, undercut in welding is a red flag, signaling a compromise in both the weld's appearance and, more critically, its structural soundness. Recognizing the visual cues of undercut is the first defense in tackling the problem. With a clear understanding of what to look for and the risks involved, welders can take the necessary steps to avoid undercut and ensure their welds are both strong and long-lasting.
2. Navigating the Causes of Undercut in Welding
Undercutting is a welder's nemesis, potentially weakening the weld and compromising the entire structure's integrity. To combat this, welders must understand and address the factors that lead to undercut. Here's a breakdown of the primary causes and how to tackle them:
-
Welding Speed: It's like driving at the right speed—too fast and you might miss filling in the gaps, too slow and you risk melting too much metal. Aim for a steady pace that allows the weld pool to form properly without creating grooves.
-
Welding Current: Think of current like the heat in your oven. Too high, and your meal burns; too low, and it's undercooked. The same goes for welding—adjust the current to avoid melting too much or too little of your metal.
-
Electrode Angle: Holding your electrode is like angling a flashlight—point it wrong, and you'll miss the spot. Keep your electrode angled correctly to ensure the arc hits the right area and fuses the metal evenly.
-
Electrode Size and Type: Using the right tool for the job is key. If your electrode is too big or not suited for the material, it's like using a sledgehammer for a nail. Choose the right size and type to prevent excessive melting.
-
Shielding Gas Flow: The flow of shielding gas should be just right—too much or too little can cause turbulence or oxidation, weakening your weld. It's like watering plants; the right amount keeps them healthy.
-
Fit-up and Joint Preparation: If your metal pieces are misaligned or poorly prepared, it's like trying to fit a square peg in a round hole. Proper alignment and preparation ensure a strong, even weld without gaps that can lead to undercut.
-
Surface Contaminants: Cleanliness is next to godliness in welding. Oil, rust, or paint on your metal is like dirt on a window—it obscures the view. Clean your metal to prevent irregularities in the weld pool.
-
Welding Technique: Consistency is key. Inconsistent weaving or torch manipulation is like a shaky hand while painting—it leads to an uneven finish. A steady hand and consistent technique help prevent undercut.
By recognizing these causes, welders can fine-tune their approach, much like a chef adjusts a recipe, to prevent undercut and ensure a strong, visually appealing weld.
3. Mastering Undercut Prevention in Welding
Ensuring a robust and durable weld requires attention to detail and a proactive approach to avoid common pitfalls like undercut. Undercut not only weakens the weld but also jeopardizes the entire structure's integrity. To help you achieve the best results, we've compiled a comprehensive list of practical steps and techniques to prevent undercut from compromising your welding projects.
Fine-Tune Your Welding Technique
- Optimal Torch Angle: Keep the torch angled between 10 to 15 degrees to distribute heat evenly and avoid creating weak spots.
- Consistent Movement: Glide the torch at a steady pace to prevent over-melting the metal, akin to a chef moving a pan to cook food evenly.
- Short Arc Control: Maintain a compact arc to limit heat and prevent the metal from becoming too thin at the edges.
Set the Right Welding Parameters
- Voltage and Amperage Adjustment: Tailor these settings to the metal's thickness and the welding method to avoid excessive penetration or lack of fusion.
- Matching Filler Material: Choose a filler that complements the base metal to ensure a seamless and strong weld.
- Appropriate Electrode Size: Select an electrode that's proportionate to the metal's thickness, much like choosing the right-sized brush for a painting job.
Prepare the Material Properly
- Clean Surfaces: Remove debris, rust, or coatings from the metal to prevent contamination, similar to prepping a surface before painting.
- Accurate Fit-Up: Align the metal pieces precisely to avoid gaps that can lead to undercut, much like fitting puzzle pieces together snugly.
Maintain Your Equipment
- Routine Inspections: Regularly check your tools for signs of wear or damage, ensuring they perform as well as a well-oiled machine.
- Control Gas Flow: If you're using gas-shielded processes, regulate the flow like a gardener waters plants—enough to protect without causing disturbance.
Develop Your Skills
- Consistent Practice: Hone your technique through regular practice, building muscle memory and stability in your hands.
- Constructive Feedback: Seek advice from seasoned welders to critique and improve your technique, much like an apprentice learning from a master.
Monitor Your Work in Real Time
- Watch the Weld Pool: Keep an eye on the weld as it forms, adjusting your technique on the spot to maintain quality.
- Inspect After Welding: Examine the finished weld for any signs of undercut and use this analysis to refine future work, similar to reviewing a draft before final submission.
By integrating these strategies into your welding routine, you can greatly diminish the risk of undercut and enhance the quality of your welds. Prevention is key, and with these actionable steps, you're equipped to tackle undercut head-on and achieve welding excellence.
4. Solidifying Your Welding Success: A Final Word on Undercut Prevention
In the intricate world of welding, precision is paramount, and the battle against undercut is a testament to a welder's skill. We've journeyed through the complexities of this common defect, uncovering its impact on weld strength and the factors that give rise to it. From the nuances of welding speed to the subtleties of electrode selection, we've pinpointed the primary culprits that can undermine your work.
The path to undercut prevention is paved with meticulous attention to detail—fine-tuning your welding parameters, mastering your technique, and ensuring your materials and equipment are up to the task. These are not mere suggestions but critical components of a superior welding practice. By embracing these strategies, you can dramatically lower the chances of undercut and elevate the caliber of your welds.
Remember, each weld you lay is a chance to apply what you've learned and to grow from the experience. We encourage you to continually experiment with your approach and share your discoveries with the welding community. Your insights can light the way for others to sidestep common errors and excel in their welding endeavors.
This guide aims to be a cornerstone in your quest to prevent undercut and achieve welding mastery. By putting these tips into action, you're setting yourself up for success, crafting welds that are not only aesthetically pleasing but structurally sound. Share your triumphs and tips with your peers, and let's collectively raise the bar for welding excellence.
Sharing is Caring
Feedback
At WeldWins, we know we aren't perfect which is why we're always looking for ways to improve. You can help us do better by taking 2 minutes to fill out our simple feedback form.
Any and all feedback is welcome. It could be a complaint, an idea, or even just a comment, we'll always be grateful to hear what you think.