How Can You Choose the Right Metal and Welding Technique for Your Project?
June 30, 2024
12 min read
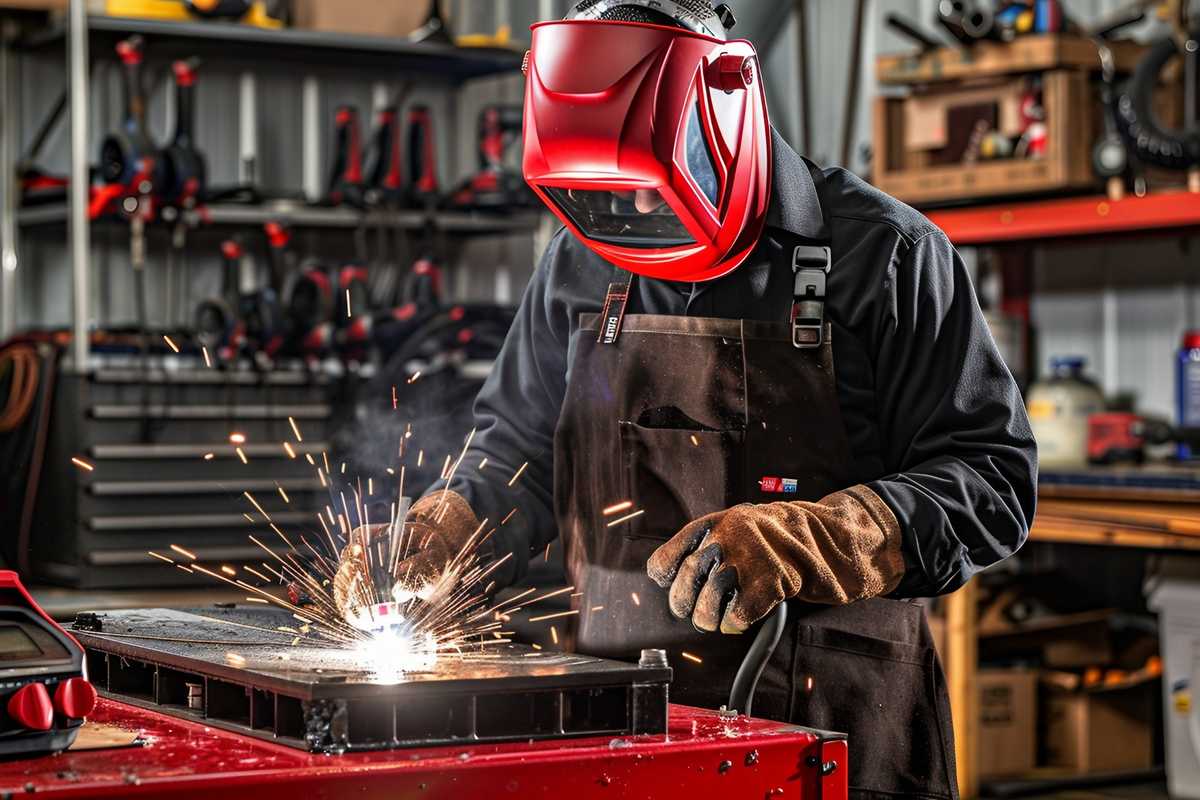
Embarking on the journey of metal welding is like stepping into a world where art meets precision engineering. It's a craft that demands a keen understanding of the metals you're working with, whether you're a weekend DIY enthusiast or a seasoned professional. Each type of metal has unique characteristics that can make or break your welding project.
Understanding how different metals behave under the intense heat of welding is crucial. They vary in how easily they melt, bend, conduct electricity, and withstand force. For example, welding a high-melting-point metal like steel is a different ball game compared to a lower-melting-point metal like aluminum. And while some metals bend under pressure without breaking, others offer the strength needed for heavy-duty structures.
As you dive into the world of welding, it's vital to grasp these metal properties and how they mesh with various welding techniques. This knowledge is not just about achieving a flawless finish; it's also about ensuring your work is safe and stands the test of time. So let's gear up and explore how to pick the perfect metal for your next project, and craft it with skill and confidence.
1. Selecting the Right Metal for Your Welding Project
Choosing the appropriate metal for your welding project is a pivotal decision that affects the project's outcome in terms of durability, strength, and functionality. To ensure the best results, it's essential to consider several critical properties of metals that will influence your welding process and the performance of the finished piece. Here's a simplified guide to what you need to keep in mind.
Understanding Melting Points
Metals melt at different temperatures. For example, steel requires a higher temperature to melt compared to aluminum. Knowing the melting point is important because it affects the type of welding you can do and the equipment you'll need. If you're working with a metal that has a high melting point, you'll need a welding method that can generate enough heat, like arc welding.
The Importance of Ductility
Ductility is a fancy word for how easily a metal can be bent or stretched. If you're making something that needs to bend without breaking, like a metal bracket that might bear weight, you'll want a metal that's ductile. A metal like mild steel is a good choice for projects requiring some flexibility.
Considering Electrical Conductivity
Some welding methods, like TIG or MIG welding, use electricity to create the weld. Metals that conduct electricity well, such as copper, might need special settings on your welding machine to ensure a stable welding process and a strong bond.
Assessing Metal Strength
The strength of a metal refers to how much force it can take before it deforms or breaks. If you're building something that needs to support a lot of weight, like a steel frame, you'll need a metal with high strength. It's crucial to match the metal's strength to the demands of your project to ensure it's safe and lasts a long time.
By taking into account these factors—melting point, ductility, electrical conductivity, and strength—you can make a more informed choice about the metal for your welding project. Each aspect will affect how the metal responds to welding and how it will hold up in its intended use. Selecting the right metal ensures your welding project not only looks good but is also structurally reliable and suited to its purpose.
2. Essential Metals in Welding and Their Unique Characteristics
Welding is more than just fusing metals together; it's about understanding the unique characteristics of each metal to ensure a successful and enduring bond. In this section, we'll take a closer look at the most popular metals in welding, highlighting their distinct properties and the specific applications they're best suited for.
Steel: The All-Rounder
Steel is a staple in the welding industry due to its adaptability. It's available in numerous grades, with mild steel being a favorite for its welding ease—perfect for everything from building structures to manufacturing vehicles. However, high-carbon steel, while stronger, demands more expertise to weld because of its proneness to cracking. Welders must carefully manage the carbon content and select the right welding method to avoid any issues.
Stainless Steel: The Resilient One
For projects that must endure corrosive environments, stainless steel is the go-to metal. Its chromium content creates a self-protecting oxide layer, preserving the metal's integrity. Welders must use specific techniques, such as controlling heat input and choosing the correct filler materials, to maintain this corrosion resistance and prevent any deformation or cracks.
Aluminum: The Lightweight Champion
Aluminum's strength-to-weight ratio makes it a prime choice for the aerospace and transportation sectors. Its thermal properties and lower melting point require precise heat control during welding, often using TIG or MIG methods, to achieve a solid weld without burning through the material.
Copper: The Conductor
Copper's superior electrical and thermal conductivity is ideal for electrical components. However, these same properties can make welding challenging, as heat dissipates quickly. Techniques like preheating and selecting a compatible filler material are vital to prevent cracking and ensure a successful weld.
Cast Iron: The Complex Case
Welding cast iron is intricate due to its high carbon content, which can lead to a brittle and crack-prone final product. A common approach involves preheating the entire piece to minimize thermal stress and using specialized welding rods that can cope with the metal's expansion and contraction during the process.
Nickel Alloys: The Tough Contenders
In environments where extreme temperatures and corrosion are a concern, such as in the chemical industry, nickel alloys are the preferred choice. Welding these alloys requires precision to avoid cracking and to maintain the weld's integrity under harsh conditions.
Magnesium: The Flammable Lightweight
Magnesium alloys are celebrated for their lightness and strength, which are highly valued in automotive and aerospace applications. However, their flammability necessitates stringent safety measures during welding, including the use of an inert gas shield to prevent oxidation and fire risks.
Each metal brings its own set of welding requirements based on its properties. A welder's ability to select the right metal and apply the appropriate welding techniques is crucial for crafting durable, high-quality welds that meet the demands of their intended application.
3. Exploring Common Welding Techniques
Welding fuses artistry with technical prowess, and to excel, one must master a variety of techniques tailored to different materials and projects. Each welding method offers unique benefits and poses distinct challenges, making the understanding of these techniques essential for creating strong, lasting welds. Let's dive into the most prevalent welding techniques and their applications.
TIG Welding: Precision and Purity
TIG (Tungsten Inert Gas) welding stands out for its precision and the superior quality of its welds. It employs a tungsten electrode that doesn't melt, ensuring a pure weld, and uses argon gas to protect the weld area from airborne contaminants. This technique is particularly effective for welding delicate sections of stainless steel and aluminum. While TIG welding demands significant skill and steady hands, it rewards the welder with unmatched control and a clean finish.
MIG Welding: Versatility and Ease
MIG (Metal Inert Gas) welding is celebrated for its versatility and ease of learning, which explains its popularity across various industries. It involves feeding a wire electrode that melts into the weld, combined with an inert gas to shield the weld pool from impurities. This method is quick and adaptable, making it ideal for a broad range of metals such as steel and aluminum. Its efficiency makes MIG welding a favorite in fast-paced environments like auto repair shops and construction sites.
Stick Welding: Simplicity and Strength
Stick welding, or Shielded Metal Arc Welding, is a time-honored technique known for its simplicity and effectiveness. It uses a consumable electrode coated with flux, which not only creates the weld but also shields it from contamination. This method is robust and less affected by wind or weather, making it suitable for outdoor projects. Stick welding is commonly used in heavy repair work and construction due to its straightforward approach and strong results.
Flux-Cored Arc Welding: Speed and Portability
Flux-Cored Arc Welding is akin to MIG welding but uses a special wire filled with flux, eliminating the need for a separate shielding gas. This makes it highly portable and fast, which is why it's often the go-to choice for construction projects where mobility is key. Whether you're working on a skyscraper or a bridge, this technique can provide the speed and flexibility required for large-scale tasks.
Submerged Arc Welding: Industrial Efficiency
Submerged Arc Welding is a technique that creates an arc between a continuous electrode and the workpiece, submerged under a layer of protective flux. This method is largely automated and is used in industrial applications where large, thick materials are joined, such as in the fabrication of pressure vessels and large pipes. It's known for its deep penetration and high quality, making it suitable for critical structures that require exceptional strength.
Each of these welding techniques has its place in the welder's toolkit, and the choice of which to use depends on factors like the type of metal, the position of the weld, and the desired finish. Mastery of these methods enables welders to approach a wide array of projects with the confidence that they can deliver durable, high-quality results. Whether you're just starting out or are looking to polish your skills, remember that practice and ongoing education are the cornerstones of becoming a proficient welder.
4. Welding Equipment Essentials: Your Toolkit for Quality and Safety
Embarking on a welding project requires more than just skill and knowledge of metals—it demands the right set of tools. The quality of your equipment can make or break your welding efforts, impacting not only the outcome but also your safety and productivity. Let's break down the key components of a welder's toolkit and understand their roles in crafting top-notch welds.
At the core of your setup is the welding machine, a critical investment that determines the capabilities of your work. Depending on your chosen welding technique—be it TIG, MIG, or Stick—the machine should align with the metal type and complexity of your projects. For instance, a TIG welder is ideal for precision work on thinner metals like aluminum, while a MIG welder might be your go-to for a variety of tasks, thanks to its ease of use and speed.
Your personal protection starts with a high-quality welding helmet. Modern helmets offer auto-darkening lenses that instantly adjust to the brightness of the welding arc, safeguarding your eyes from harmful rays and improving visibility. This feature is not just about comfort; it's about maintaining focus on your weld for the best results.
Don't overlook the importance of welding gloves and protective clothing. These are your first line of defense against heat, sparks, and UV exposure. Gloves should balance heat resistance with flexibility, allowing you to handle tools and materials with precision. Flame-resistant garments, such as jackets and aprons, are equally important, providing a barrier between your skin and the intense conditions of welding.
Hand tools like clamps, hammers, brushes, and pliers are the unsung heroes of welding. They keep your workpieces secure, clean up after welds, and manage hot materials safely. Investing in quality hand tools pays off in the long run by making your work smoother and preventing accidents.
Lastly, your workspace is as much a part of your equipment as the tools you hold. Adequate ventilation is non-negotiable, whether it's through built-in exhaust systems or strategic positioning outdoors. Keeping the air clear of hazardous fumes not only protects your health but also ensures a cleaner working environment.
In essence, the right welding equipment is the backbone of successful welding. It's about choosing tools that not only fit the job but also stand up to the rigors of welding, all while keeping you protected. With a well-curated set of equipment, you're equipped to tackle any welding challenge with confidence and produce work that's both strong and safe.
5. Final Thoughts: The Welder's Path to Mastery
In concluding our comprehensive exploration of metal welding, we've uncovered the intricate dance between material properties and welding techniques that defines the craft. From the melting point and ductility to electrical conductivity and inherent strength, each metal's unique traits guide us in selecting the perfect candidate for our welding endeavors.
We've journeyed through the world of metals, examining the reliable versatility of steel, the enduring resilience of stainless steel, the advantageous lightness of aluminum, the excellent conductivity of copper, the complex nature of cast iron, the industrial might of nickel alloys, and the careful handling of flammable magnesium. These metals, each with their own quirks and best practices, remind us that the right choice is critical for a successful weld.
Our exploration didn't stop at materials; we've also navigated the seas of welding techniques. From the precision of TIG welding, the user-friendly MIG welding, to the rugged reliability of Stick welding, and beyond, we've highlighted the importance of matching technique to task. Each method offers a unique set of benefits tailored to specific materials and project requirements.
And let's not forget the tools of the trade. We emphasized the importance of proper welding equipment, which not only affects the outcome of your projects but also ensures your safety. A reliable welding machine, a protective helmet, durable gloves, and a well-ventilated workspace are just a few essentials in a welder's arsenal.
By absorbing the insights from this guide, you're poised to elevate your welding skills, whether you're a novice or a seasoned artisan. Remember, the key to excellence in welding lies in persistent practice and a commitment to lifelong learning. Embrace the journey, and you'll forge welds that are not only aesthetically pleasing but also structurally sound and enduring.
Sharing is Caring
Feedback
At WeldWins, we know we aren't perfect which is why we're always looking for ways to improve. You can help us do better by taking 2 minutes to fill out our simple feedback form.
Any and all feedback is welcome. It could be a complaint, an idea, or even just a comment, we'll always be grateful to hear what you think.