How Can We Build a Lasting Safety Culture in Metal Fabrication?
July 4, 2024
13 min read
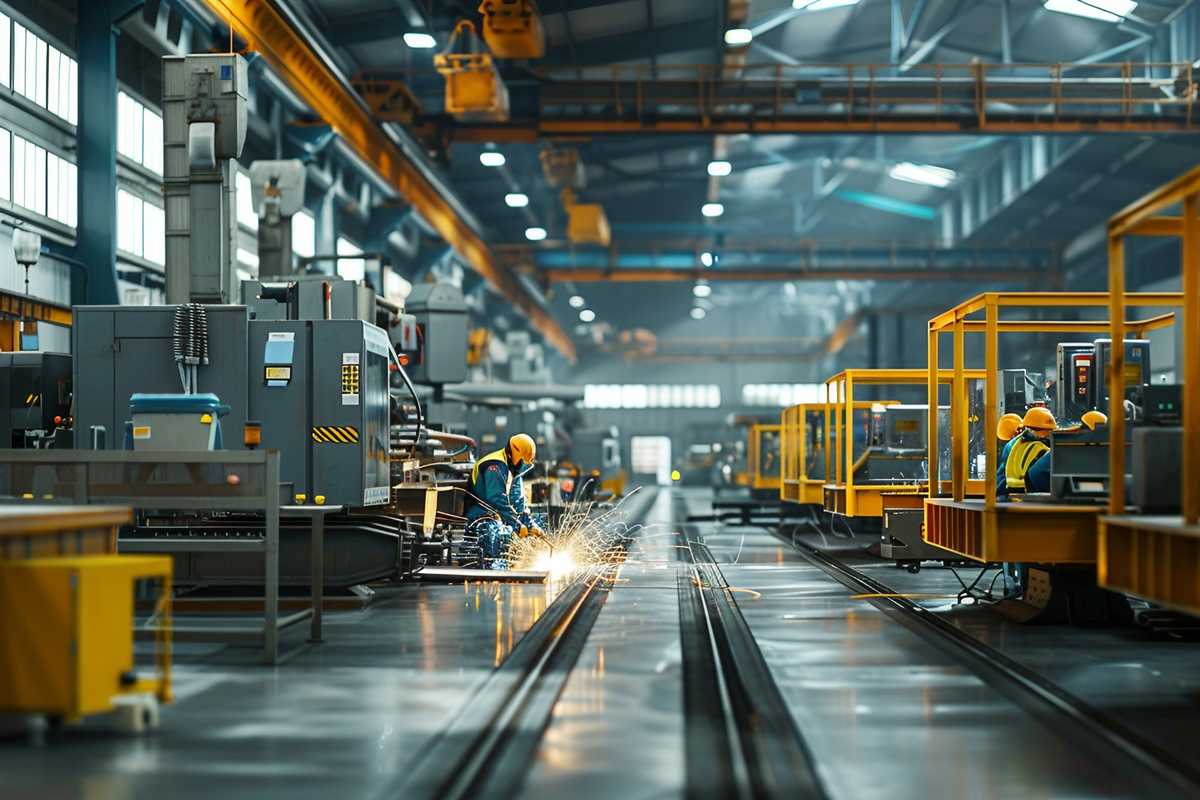
In the world of metal fabrication, where the stakes are high and the hazards are many, safety must be more than a checklist—it must be a way of life. It's essential to cultivate a culture where safety is ingrained in every action and decision, from the executive suite to the shop floor. This culture is not the responsibility of a single person; it's a collective effort that requires the commitment and vigilance of every team member.
Establishing a safety-first mindset begins with education. Regular training sessions are crucial, not just during onboarding but as an ongoing practice. These sessions should cover everything from the proper operation of heavy machinery to the correct way to report potential hazards. By keeping safety knowledge fresh, workers are empowered to make safer choices every day.
Open communication is another pillar of a strong safety culture. Encouraging workers to speak up about safety concerns without fear of reprisal can lead to the identification and resolution of issues before they result in accidents. This open-door policy helps foster trust and reinforces the idea that safety is everyone's business.
A proactive approach to safety also involves a thorough understanding of the specific risks associated with metal fabrication. Recognizing the dangers of sharp edges, the weight of materials, and the intense heat of welding is the first step in mitigating them. For example, implementing machine guards can prevent contact with moving parts, and using welding curtains can protect bystanders from harmful UV radiation.
Personal Protective Equipment (PPE) is the last line of defense against workplace hazards. Ensuring that every worker has access to the right PPE—and knows how to use it correctly—is non-negotiable. From cut-resistant gloves to auto-darkening welding helmets, each piece of equipment plays a critical role in worker safety.
Finally, a clean and orderly workspace is a safer workspace. Regular housekeeping reduces clutter and the risk of trips and falls, while proper labeling of hazardous materials helps prevent accidental exposure. A well-maintained shop is a visual reminder of the value placed on safety and sets the standard for daily operations.
By weaving these practices into the fabric of daily work life, metal fabrication businesses can create an environment where safety is second nature. It's about going beyond compliance and fostering a culture where every employee is an active participant in maintaining a safe and healthy workplace.
1. Navigating the Hazards of Metal Fabrication
Metal fabrication is an industry where precision meets heavy-duty labor, and with that combination comes a spectrum of safety risks that must be vigilantly managed. Recognizing and understanding these risks is the cornerstone of a robust safety program, essential for safeguarding the well-being of workers and the operational integrity of the business.
Heavy machinery is the backbone of metal fabrication, but it also presents one of the most significant dangers. Workers frequently engage with powerful equipment such as press brakes, shears, and plasma cutters. These machines have the potential to cause catastrophic injuries if mishandled. For instance, a momentary lapse in concentration around a punch press could result in a life-altering injury. It's also common for workers to maneuver large, cumbersome materials, which can lead to strains or more severe musculoskeletal injuries if proper lifting techniques are not employed.
The air in a metal fabrication shop can be just as hazardous as the equipment. Processes like welding and metal cutting can emit noxious fumes and microscopic particles that compromise air quality and pose serious health risks. For example, prolonged inhalation of hexavalent chromium, a compound released during stainless steel welding, can lead to respiratory conditions and other health complications.
Thermal burns from hot surfaces and materials, as well as electrical accidents, are also prevalent dangers. A stray spark or a drop of molten metal can inflict severe burns. Electrical hazards, such as using a damaged power tool or handling equipment with wet hands, can lead to shocks or even electrocution.
Ignoring these risks can have dire consequences, including physical injury to employees, operational downtime, legal repercussions, and damage to the company's reputation. In the worst-case scenario, workplace accidents can lead to fatalities, a devastating outcome that is preventable with the right safety protocols in place.
Adherence to safety regulations, such as those set forth by OSHA, is non-negotiable. These guidelines provide a safety blueprint that encompasses machine safeguarding, permissible exposure limits to hazardous substances, and the mandatory use of personal protective equipment (PPE). Following these regulations not only establishes a safety baseline but also significantly diminishes the likelihood of workplace incidents.
In essence, the metal fabrication industry is laden with risks that demand careful management. By thoroughly understanding these hazards, businesses can proactively fortify their workplaces against potential accidents. Compliance with established safety standards is not just a legal formality—it's a critical step in nurturing a safe and healthy work environment for everyone on the shop floor.
2. Essential Safety Protocols in Metal Fabrication
Metal fabrication shops are bustling environments where safety must be the top priority. To safeguard the well-being of employees and ensure smooth operations, it's crucial to implement a comprehensive set of safety protocols. These protocols are not just about ticking boxes for compliance—they are proactive steps to protect individuals from harm and prevent workplace incidents. Let's delve into the critical safety measures that form the backbone of a robust metal fabrication safety program.
Conducting Regular Risk Assessments
A proactive safety strategy starts with regular risk assessments. These are detailed evaluations where potential hazards are identified, risks are analyzed, and control measures are put in place. For example, if a new piece of equipment is introduced, a risk assessment would determine the best placement for the machine to minimize the risk of injury. These assessments should be updated frequently to adapt to new methods, tools, or regulations, ensuring that the workplace remains a safe environment.
Implementing Machine Guarding
Machine guarding is a vital defense against common fabrication injuries. Guards are barriers or shields placed around machinery to protect operators from flying sparks, moving parts, and other dangers. For instance, a guard on a metal press can prevent a worker's hand from accidentally slipping into the press area. Regular inspections and maintenance of these guards are essential, as is training employees to always check that guards are in place and functioning before they begin work.
Enforcing Lockout/Tagout Systems
Lockout/tagout systems are critical for machine maintenance and repair. They ensure that machines are properly shut down and cannot be started up again until maintenance is complete. This is done by placing locks and tags on the equipment to alert others not to use it. For example, if a worker needs to repair a conveyor belt, they would lock the control panel and tag it, indicating that the machine is out of service. Proper training on these procedures is crucial to prevent accidental startups and injuries.
Upholding Electrical Safety Standards
In metal fabrication, electrical safety is non-negotiable due to the high use of electrical tools and machinery. Regular inspections of electrical equipment, comprehensive training on safe handling practices, and adherence to industry standards are all part of a strong electrical safety protocol. Workers should be well-versed in recognizing electrical hazards and know the immediate steps to take in case of an electrical emergency.
Providing and Maintaining Personal Protective Equipment (PPE)
Personal Protective Equipment (PPE) is the last line of defense against workplace hazards. Items like safety goggles, gloves, and welding helmets shield workers from various risks. It's not enough to simply hand out PPE; employees must be trained on how to use it correctly and understand the importance of regular maintenance. For instance, welding helmets should be checked for cracks or damage before use, and replaced if they no longer provide adequate protection.
Establishing Fire Safety Practices
Given the sparks and heat involved in metal fabrication, fire safety practices are a must. This includes having accessible fire extinguishers, training employees on their use, and clear evacuation routes. Conducting regular fire drills ensures that everyone knows how to exit the building safely in case of an emergency.
Ensuring Proper Ventilation
Metal fabrication can release harmful fumes that compromise air quality. Effective ventilation systems, like local exhaust ventilation (LEV), are necessary to capture fumes at the source and maintain clean air. For example, a welding station should have an LEV system to extract toxic gases and keep the air breathable for the welder and nearby workers.
Prioritizing Ergonomics
Ergonomics is the science of designing workstations to fit the worker, reducing the risk of strain and injury. Adjustable tables, ergonomic tools, and training on proper lifting techniques are examples of ergonomic practices. Encouraging regular breaks and stretching can also help prevent repetitive strain injuries.
By weaving these essential safety protocols into the fabric of daily operations, metal fabrication businesses can significantly reduce the risk of workplace accidents and create a culture of safety that values the health and safety of every employee.
3. Elevating Safety Through Continuous Training
In the bustling environment of metal fabrication, where machinery roars and sparks fly, safety training transcends mere compliance—it's the heartbeat of a thriving workplace. Ongoing safety education is crucial, arming employees with the foresight to sidestep dangers and prevent mishaps.
Workshops and seminars should be regular fixtures in the training calendar, addressing a spectrum of topics from machinery operation to hazardous material management. These sessions keep safety practices at the forefront of workers' minds, encouraging the application of these protocols as second nature.
Practical, hands-on training brings safety from the abstract to the concrete. Simulated emergency drills, for instance, can sharpen a worker's response time and effectiveness in crisis situations. These drills might include extinguishing a controlled fire or administering first aid—vital skills that could one day turn a worker into a lifesaver.
Mentorship is another pillar of safety training. By pairing novices with seasoned professionals, new recruits gain practical insights and learn to navigate the workshop's daily risks under watchful, experienced eyes. This not only solidifies safety practices but also weaves a fabric of mutual care and vigilance among the workforce.
Accessibility and inclusivity are key in training programs. Materials should be available in multiple languages and tailored to various learning styles. Whether through visual aids, e-learning, or live demonstrations, the goal is to ensure every employee has a deep understanding of safety measures.
Safety education is not a one-off but a continuous journey. Regular updates through refresher courses, safety bulletins, and daily briefings keep the workforce abreast of the latest safety standards and technological advancements.
Investing in a robust, ongoing training program does more than just minimize risk—it boosts productivity and confidence among employees. A well-informed worker is not only an asset in maintaining a safe environment but also contributes to the efficiency and success of the business.
4. Maintaining a Safe Workspace Through Diligent Housekeeping
In the bustling world of metal fabrication, where every day is a symphony of clanging metal and whirring machines, the importance of housekeeping can easily be overlooked. Yet, it is a cornerstone of workplace safety, playing a pivotal role in preventing accidents and injuries. A well-kept shop floor is not just about aesthetics; it's about creating a secure environment where employees can focus on their craft without unnecessary risks.
Slippery floors and cluttered walkways are accidents waiting to happen. Spills of oil and grease must be swiftly cleaned to prevent falls, while scrap materials and tools need to be promptly cleared away to avoid tripping hazards. A simple routine of cleaning spills immediately and organizing tools after use can drastically reduce the likelihood of these common workplace mishaps.
The thoughtful organization of the workspace extends to how tools and materials are stored. A place for everything and everything in its place is not just an old adage—it's a safety principle. When tools are neatly arranged and materials are stacked securely, workers are less likely to suffer injuries from reaching for items stored haphazardly or using the wrong equipment for a task.
Regular upkeep of machinery is another facet of good housekeeping. Dust and debris can accumulate and interfere with the operation of equipment, potentially leading to dangerous malfunctions. Clean machines are not only safer, they're also easier to inspect for wear and tear, allowing for timely maintenance and repairs before problems escalate.
A clean and orderly environment also boosts morale and productivity. Employees take pride in a workspace that reflects respect and care, and they're more likely to follow safety protocols in such an environment. It's a positive feedback loop where good housekeeping reinforces a culture of safety, and a culture of safety promotes even better housekeeping.
To achieve this, metal fabrication shops should implement a housekeeping routine that includes:
- Scheduled cleaning for different zones of the facility.
- Immediate action plans for dealing with spills and debris.
- Clear responsibilities for tool and material organization.
- Regular inspections to ensure equipment cleanliness and functionality.
By prioritizing housekeeping, metal fabrication businesses not only protect their employees but also enhance the efficiency and smooth operation of their facilities. It's a straightforward yet effective approach to maintaining a safe and productive work environment.
5. Forging a Future of Safety in Metal Fabrication
As we wrap up our comprehensive guide, it's clear that ensuring safety in the metal fabrication industry is an ongoing commitment that extends far beyond mere compliance with regulations. We've dissected the layers of a safety-conscious workplace, highlighting the essential practices that pave the way for a hazard-free environment. From the meticulous implementation of machine guards to the rigorous enforcement of electrical safety and the correct use of personal protective equipment, we've underscored the strategies that are crucial for preventing workplace incidents.
The power of continuous education has been a recurring theme, emphasizing that a well-trained workforce is the best defense against accidents. By fostering a culture where safety training is as routine as clocking in for the day, employees become proactive guardians of their own well-being and that of their colleagues. We've also showcased the significant impact that a clean and organized workspace has on safety, demonstrating that good housekeeping is not just about cleanliness but also about creating a secure and efficient work setting.
In closing, we call upon every individual involved in metal fabrication to champion a culture where safety is deeply embedded in every aspect of the work. This culture strives not just to meet the standards set by OSHA but to exceed them, with the ultimate aim of achieving a workplace where accidents are a rarity. The commitment to refining safety practices must be relentless, as the well-being of the workforce is invaluable, and the benefits of a stellar safety record are immeasurable.
Let this article be a catalyst for change, inspiring all metal fabrication stakeholders to rigorously evaluate and fortify their safety protocols. Every worker deserves to end their shift as they started it—safe and sound. Safety is not a static goal but a dynamic process of continuous enhancement. Together, let's take decisive steps toward a future where the highest safety standards in metal fabrication are not just aspired to but achieved.
Sharing is Caring
Feedback
At WeldWins, we know we aren't perfect which is why we're always looking for ways to improve. You can help us do better by taking 2 minutes to fill out our simple feedback form.
Any and all feedback is welcome. It could be a complaint, an idea, or even just a comment, we'll always be grateful to hear what you think.