How Is Robotic Welding Shaping the Future of Manufacturing?
July 8, 2024
14 min read
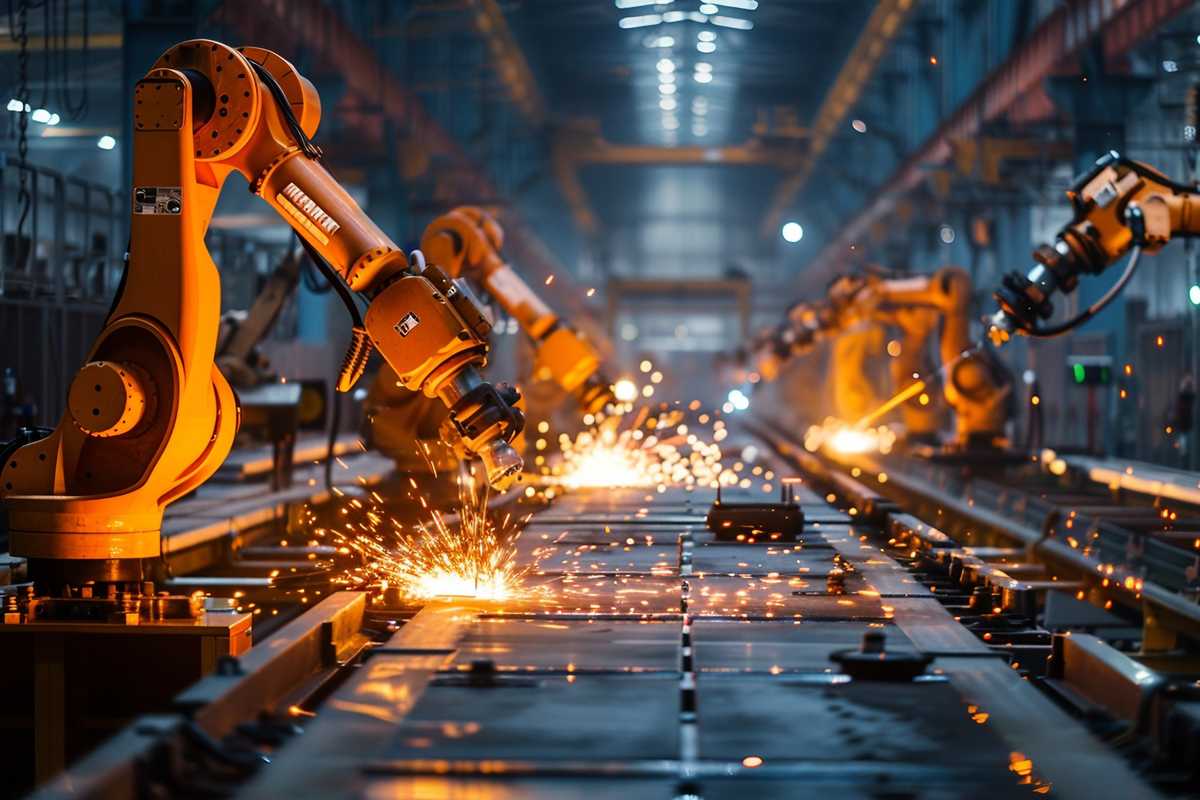
Welcome to the dawn of a new age in manufacturing, where the buzz and hum of robots are becoming as familiar as the clank of metal on metal. Robotic welding, a marvel of modern engineering, is leading this industrial revolution. Picture a world where robots with unerring precision and tireless arms perform the intricate dance of welding, a task once solely in the domain of skilled human hands. This leap forward isn't just about swapping out people for machines; it's about elevating the entire production process to new heights of innovation and efficiency.
In this journey through the world of robotic welding, we'll explore how it's changing the game for manufacturers everywhere. From the evolution of these metal-crafting marvels to the various types that cater to different industry needs, we'll dive into the myriad benefits they bring. But it's not all smooth sailing; we'll also tackle the hurdles and limitations that come with such technology. And finally, we'll cast our gaze forward to the exciting possibilities on the horizon, where robotic welding is not just transforming the manufacturing floor but also paving the way for a new chapter in industrial history. Join us as we unveil the transformative power of robotic welding and its role in shaping the factories of the future.
1. Tracing the Journey of Robotic Welding
The story of robotic welding is a fascinating saga of technological evolution, mirroring the broader narrative of industrial advancement. It all started back in the 1960s with the debut of the first industrial robots—clunky and simplistic by today's standards, yet groundbreaking for their time. These pioneering machines set the stage for the highly sophisticated robotic welders we rely on today.
As we progressed into the 1970s, a pivotal breakthrough occurred with the advent of microprocessor technology. This innovation was a game-changer, endowing robotic arms with unprecedented control and precision, thereby making them more adept at handling the intricate demands of welding tasks. The affordability and increasing power of microprocessors over time further propelled the popularity and capabilities of robotic welding systems.
The surge in robotic welding really took off during the 1980s and 1990s, especially within the automotive sector. Automakers quickly recognized the unmatched consistency and speed that robots brought to the table, allowing them to undertake repetitive and hazardous tasks previously performed by human hands. This era also introduced us to sensors and computer vision, empowering robots to adjust to material inconsistencies, thus boosting their effectiveness.
Entering the 21st century, we witnessed the emergence of collaborative robots, affectionately known as "cobots." These innovative machines were designed to work in tandem with human workers, blending the relentless precision of robots with the creative problem-solving skills of humans. Cobots have since unlocked new opportunities, particularly for smaller businesses that once considered robotic welding systems too complex or expensive.
Fast forward to today, and we're seeing the boundaries of robotic welding being pushed further than ever before. Artificial intelligence and machine learning are now equipping robots with the ability to learn and enhance their performance progressively. Meanwhile, the integration of Internet of Things (IoT) technology is knitting robotic welding systems into a more interconnected fabric, capable of analyzing data in real-time for smarter, more responsive manufacturing.
The current trend in robotic welding leans heavily towards flexibility and versatility. Manufacturers are on the hunt for robots that can transition between various welding tasks with minimal fuss and reprogramming. This adaptability is crucial in a marketplace where product life cycles are shrinking, and the demand for customization is ever-increasing.
The transformative journey of robotic welding stands as a testament to the relentless innovation within the manufacturing industry. From the initial robotic arms to today's intelligent, adaptive systems, each step forward has brought us closer to a future where robots are an indispensable part of manufacturing, enhancing productivity, safety, and quality in every aspect.
2. Exploring the Spectrum of Robotic Welding Techniques
In the realm of manufacturing, robotic welding stands as a pillar of innovation, offering a suite of techniques tailored to meet the diverse needs of various industries. Understanding the nuances of each welding type is essential for manufacturers to select the optimal approach for their specific projects. Let's take a closer look at the three primary robotic welding methods that have become industry staples: arc welding, spot welding, and laser welding.
Arc Welding: The Backbone of Heavy Industry
Arc welding robots are the workhorses of the welding world. They use an electric arc—a discharge of electricity across a gap in a circuit—to melt and fuse metals at the welding point. These robots come equipped with welding guns and are programmed to execute complex welding tasks with remarkable precision. You'll find arc welding robots in the heart of the automotive and construction sectors, where they're prized for their ability to consistently produce strong, high-quality welds on a large scale. For example, in building a car, arc welding robots ensure that the frame is solid and durable, contributing to the vehicle's overall safety and longevity.
Spot Welding: Masters of Sheet Metal
Spot welding robots specialize in joining sheet metal with speed and precision. They apply pressure and intense heat from an electrical current to bond metal sheets at specific points. This method is crucial in manufacturing products like cars and household appliances, where each piece of metal must be joined accurately and quickly. Picture a car assembly line where robotic spot welders rapidly connect door panels and frames, significantly boosting production rates while maintaining a consistent level of quality across each vehicle.
Laser Welding: The Precision Experts
Laser welding robots are the surgeons of the welding family, offering unmatched precision and control. They use a focused laser beam to melt and join materials, making them ideal for delicate tasks that demand exact accuracy, such as in electronics or medical device manufacturing. These robots can work with both metals and non-metals, providing a flexible solution for intricate welding needs. For instance, in creating medical implants, laser welding robots can join small metal components without damaging surrounding areas, ensuring the implants meet strict medical standards.
Each robotic welding method brings distinct advantages to the table, enhancing manufacturing processes through automation. This leads to increased precision, efficiency, and safety, resulting in significant productivity gains. As we continue to witness technological advancements, we can expect the emergence of even more specialized robotic welding systems designed to address the unique challenges of different industries.
3. The Compelling Benefits of Robotic Welding
In the fast-paced world of manufacturing, robotic welding stands out as a game-changer, offering a suite of benefits that propel production into the future. The precision of robotic welding is unparalleled; these machines are designed to execute welds with pinpoint accuracy, ensuring a level of consistency that manual welding can't match. This is especially critical in fields like aerospace and medical device manufacturing, where even the smallest error can have serious consequences.
Speed is another area where robotic welding shines. Robots don't tire like humans do, and they don't need breaks. They can keep working around the clock, which means they can churn out products much faster than traditional methods. This is a huge advantage for any business that needs to keep up with high demand or tight schedules, like during the holiday rush for electronics or toys.
Safety is a significant concern in welding, with risks ranging from burns to eye damage from the bright welding arc. Robotic welding takes workers out of harm's way, reducing the risk of workplace injuries. This not only keeps employees safe but can also save companies money on health insurance and workers' compensation.
The benefits of robotic welding extend beyond just making things faster or safer. In the automotive industry, for example, robotic welding helps ensure that every car part is welded with the same high standards, which means safer, more reliable vehicles for consumers. In the construction of infrastructure like bridges, the speed of robotic welding can help finish projects faster, which is crucial when deadlines are tight and delays can be costly.
Robotic welding systems can also be linked with cutting-edge software and sensors, allowing for adjustments on the fly and real-time quality control. This smart approach to manufacturing means less waste, more efficient use of materials, and the ability to predict when machines need maintenance before they break down, which keeps the production line moving smoothly.
In essence, the benefits of robotic welding—its accuracy, speed, safety, and smart integration—make it an irresistible choice for industries looking to stay competitive and produce top-notch products. These advantages not only boost the bottom line for businesses but also lead to better, more reliable products for consumers.
4. Navigating the Hurdles of Robotic Welding
Despite the impressive strides made in the field of robotic welding, it's important to acknowledge the hurdles that manufacturers face when implementing these systems. The initial cost of setting up robotic welding can be steep, especially for small to medium-sized businesses. This financial barrier often means that only larger companies with deeper pockets can afford to invest in these advanced technologies.
Programming and operating robotic welders also present a significant challenge. These systems require skilled technicians who understand the intricacies of robotic programming. With the rapid growth of robotic welding, the demand for such expertise is skyrocketing, leading to a shortage of qualified professionals. This gap in the workforce can slow down the adoption of robotic welding and hinder its potential benefits.
Flexibility—or the lack thereof—is another issue. Robotic welders are champions of repetitive tasks, but they struggle with adapting quickly to new designs or custom orders. This can be a major setback for industries that need to frequently update their product designs or that specialize in small, customized production runs.
When it comes to maintenance, robotic welding systems are not immune to breakdowns. And when they do falter, it can lead to costly production halts. The specialized knowledge required to fix these high-tech machines means that not every technician can handle repairs, potentially leading to extended downtime.
Safety is another area that requires careful consideration. While robotic welding can reduce the risk of human exposure to dangerous welding tasks, it also introduces new safety hazards. Without strict adherence to safety protocols, there's a risk of accidents involving the robotic equipment and human workers.
Lastly, the shift toward robotic welding can have social and economic impacts, particularly in terms of employment. As robots increasingly take on welding jobs, the demand for human welders may decrease, leading to job displacement. This shift necessitates new strategies for workforce development and training to prepare workers for the changing landscape.
Despite these challenges, the future of robotic welding is bright, with ongoing advancements aimed at making these systems more user-friendly, adaptable, and cost-effective. Innovations in artificial intelligence and machine learning are set to simplify programming, while improvements in sensor technology could make robots more versatile. As the technology evolves, it's expected that many of these hurdles will be overcome, further solidifying robotic welding's place in modern manufacturing.
5. Envisioning the Next Wave in Robotic Welding
The future of robotic welding is poised to ignite a manufacturing renaissance, where the integration of cutting-edge technologies will not only enhance current processes but also revolutionize the industry as a whole. Let's delve into the transformative advancements that are set to elevate robotic welding to unprecedented levels of performance and versatility.
Intelligent Automation and Machine Learning: The Brainy Bots
Imagine robots that don't just follow instructions but learn and adapt like seasoned craftsmen. This is the promise of intelligent automation combined with machine learning. These smart robots will be able to analyze data from past welding jobs to perfect their techniques, handle new materials with ease, and even predict when they might need a tune-up to avoid unexpected downtime. For instance, a robotic welder could learn to adjust its methods for welding lightweight aluminum in high-performance electric cars, ensuring strong, reliable joins without adding unnecessary weight.
Collaborative Robots (Cobots): Team Players on the Factory Floor
Cobots are set to redefine teamwork in manufacturing. These friendly machines are designed to work hand-in-hand with human workers, blending the unwavering precision of robots with the creative insights of their human colleagues. This collaboration could transform production lines into more adaptable and nuanced workspaces. Imagine a cobot assisting a human worker in assembling a custom motorcycle, handling the repetitive welding tasks while the human fine-tunes the unique design elements.
Enhanced Connectivity and the Internet of Things (IoT): The Networked Workshop
The future of robotic welding will be deeply interconnected thanks to IoT technology. Welding robots will be part of a network that allows for real-time monitoring and control from anywhere, making it easier to manage production and maintain quality. For example, a factory manager could oversee and adjust welding operations from their smartphone, ensuring that every product meets the highest standards without being physically present on the shop floor.
New Materials and Applications: The Innovators' Palette
As new materials emerge, robotic welding will evolve to keep pace. Robots will need to be versatile enough to handle materials with unique properties, such as advanced composites used in aerospace or biodegradable plastics in sustainable packaging. This adaptability will be key to staying ahead in a market that's constantly seeking the next big thing.
Sustainability and Green Manufacturing: Eco-Friendly Fabrication
Sustainability is no longer a nice-to-have; it's a must. Robotic welding will contribute to greener manufacturing practices by reducing energy use, cutting waste, and potentially running on renewable energy. This shift will not only help the planet but also improve the bottom line and public image of companies. Imagine solar-powered welding robots constructing energy-efficient homes, reducing the carbon footprint of the building process.
Advanced Safety Features: The Guardians of the Shop Floor
As robotic welding becomes more widespread, the safety of human workers will be paramount. Future systems will likely include advanced sensors and AI-driven safety measures to prevent accidents and foster a safer workplace. Think of a robotic welder that can instantly shut down if a human gets too close, or one that can detect and correct potential hazards before they become problems.
The horizon of robotic welding is bright with the promise of increased efficiency, flexibility, and innovation. These advancements are not mere possibilities but are rapidly becoming realities that will redefine manufacturing. The potential for robotic welding to transform the industry is immense, offering a glimpse into a future where high-quality products are made faster, safer, and in more environmentally conscious ways.
6. Conclusion: Embracing the Robotic Welding Revolution
As we stand on the cusp of a new era in manufacturing, robotic welding emerges as a transformative force, reshaping the industry with its precision, speed, and safety. This technological marvel has already begun to redefine production standards, proving that the future of manufacturing is not just a concept, but a tangible reality taking shape across factory floors worldwide.
The advantages of robotic welding are undeniable. Its superior accuracy ensures that products meet the highest quality standards, while its rapid operation accelerates production timelines, allowing businesses to thrive in a market where efficiency is king. Moreover, the enhanced safety protocols of robotic systems create a safer work environment, protecting employees from the hazards traditionally associated with welding.
Yet, the evolution of robotic welding is an ongoing narrative, marked by continuous innovation and boundless potential. Every day, new breakthroughs are charted, paving the way for even more sophisticated and capable systems. Early adopters of this technology are not merely keeping pace with the times; they are trailblazers, setting themselves apart as leaders in a competitive and ever-changing marketplace.
Consider the automotive industry, where robotic welding has become integral to the assembly line, ensuring each vehicle is constructed with uniform excellence. Or envision the construction of vital infrastructure, where the speed of robotic welding can mean the difference between meeting a deadline or facing costly delays.
The ascent of robotic welding is a testament to the power of human creativity and the relentless drive for advancement. It's a chapter in the story of how technology elevates our potential and propels entire sectors forward. Looking ahead, we can expect a cascade of pioneering developments in robotic welding that will continue to revolutionize the way we manufacture goods.
The promise of a more efficient, safer, and innovative manufacturing process is not a distant dream but a present-day achievement that is expanding before our eyes. The age of robotic welding has arrived, and it is redefining the manufacturing landscape in profound and exciting ways.
Sharing is Caring
Feedback
At WeldWins, we know we aren't perfect which is why we're always looking for ways to improve. You can help us do better by taking 2 minutes to fill out our simple feedback form.
Any and all feedback is welcome. It could be a complaint, an idea, or even just a comment, we'll always be grateful to hear what you think.