How Can You Prevent Slag Inclusions in Welding?
May 25, 2024
12 min read
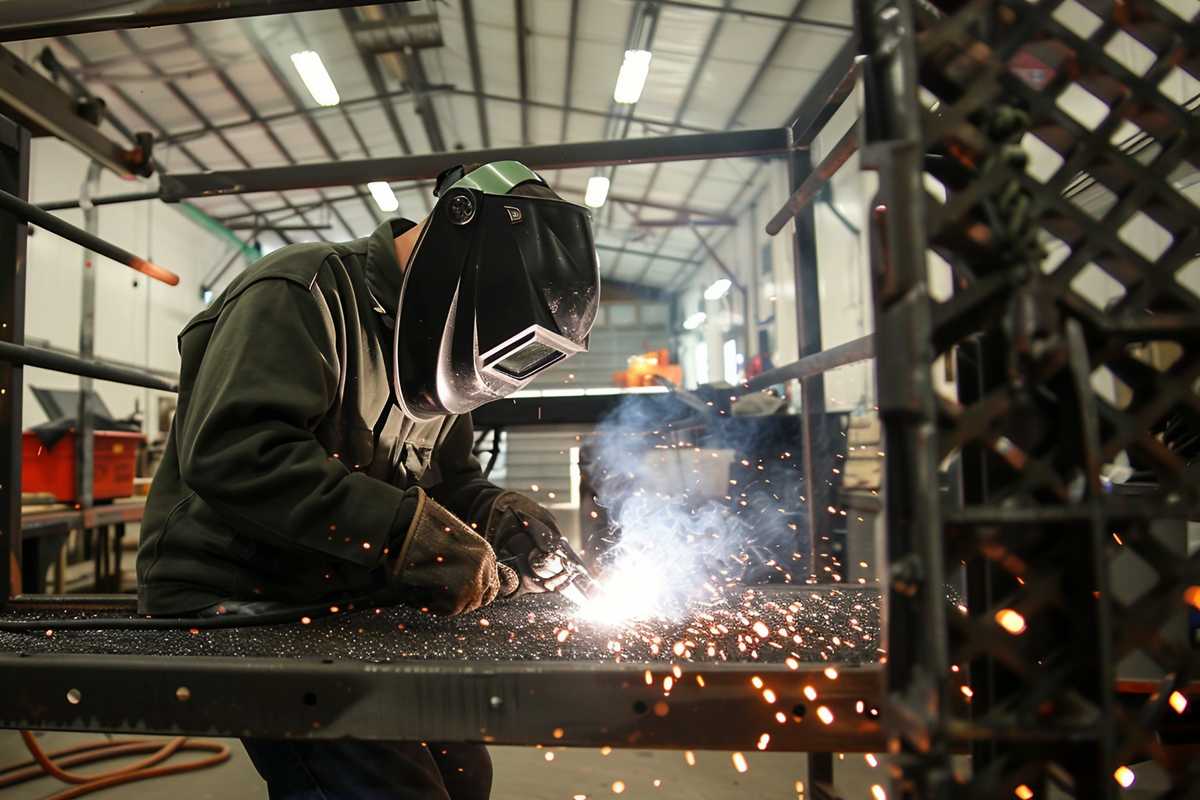
Welding is more than just joining metals; it's an art that demands precision and expertise. A common foe in this art is slag inclusion, a defect that can weaken the entire structure it's meant to hold together. Imagine a metal chain with a fragile link; that's what a weld with slag inclusions is like. It's a hidden flaw that can cause the metal to break when it's needed the most.
In this guide, we'll take a deep dive into the world of welding, focusing on the pesky problem of slag inclusions. We'll explain what they are, why they're a big deal, and how to spot them. Plus, we'll share some insider tips on how to avoid these unwelcome intruders in your welds.
Whether you're just starting out or you've been welding for years, this article is your toolkit for producing stronger, more reliable welds. By the end, you'll know how to keep slag inclusions at bay, ensuring your welded creations are as sturdy as they are meant to be.
1. The Impact of Slag Inclusions on Weld Quality
Slag inclusions are a common but serious issue in welding, where non-metallic particles get trapped in the weld or between the weld and base metal. These particles are leftovers from the flux used during welding and are mostly made up of substances like oxides and silicates. When these inclusions are present, they can weaken the weld by creating points where stress is concentrated, which can lead to reduced strength and flexibility.
In high-stakes industries such as aerospace or automotive manufacturing, the presence of slag inclusions can lead to the rejection of critical components, which can be costly and cause delays. Even in less critical applications, these inclusions can mar the appearance of a product, which is a significant concern for consumer goods where looks are important.
Slag inclusions can also pose challenges for testing the integrity of welds. They can interfere with nondestructive testing methods like ultrasonic testing or radiography, potentially hiding other defects and giving a false impression of safety.
To ensure the highest weld quality, it's essential to understand the nature of slag inclusions and their detrimental effects. Recognizing the risks they pose allows welders and inspectors to take steps to prevent them, such as optimizing welding procedures. The subsequent sections will delve into the causes of slag inclusions and provide practical advice on how to avoid them, ensuring that every weld is strong, reliable, and free of defects.
2. Mastering the Detection of Slag Inclusions
Ensuring a weld's strength and longevity hinges on the early detection of slag inclusions—those unwelcome foreign materials that can lurk within the weld, threatening its integrity. It's imperative for welders to be adept at spotting these defects, which can range from tiny specks to more pronounced irregularities. Let's delve into the methods that can help you uncover these hidden imperfections.
Sharpen Your Visual Inspection Skills
A meticulous visual inspection is your first tool in the fight against slag inclusions. Post-weld, scrutinize the weld bead and adjacent metal for any signs of trouble. Slag typically manifests as dark, jagged formations either within the weld or at its edges. Their size can vary, and while some are visible to the naked eye, others may require the aid of magnification tools like a jeweler's loupe or an inspection mirror.
Be on the lookout for surface anomalies such as pits or cracks, which can be telltale signs of underlying slag. A uniform weld bead is a positive indicator, but any irregularities warrant a closer look.
Leverage Non-Destructive Testing Techniques
When visual checks don't cut it, non-destructive testing (NDT) methods come into play. These advanced techniques can unearth inclusions without harming the weld:
- Radiographic Testing (RT): This method uses X-rays or gamma rays to capture an image of the weld, with slag inclusions appearing as dark anomalies against the lighter backdrop of solid metal.
- Ultrasonic Testing (UT): UT employs high-frequency sound waves that, when reflected by inclusions, reveal their presence.
- Magnetic Particle Testing (MPT): Applicable to ferromagnetic materials, MPT can detect both surface and subsurface inclusions by observing the accumulation of magnetic particles where the magnetic field is disturbed by an inclusion.
Consider Destructive Testing When Necessary
Sometimes, you may need to resort to destructive testing to assess the extent of slag inclusions. This method involves taking a sample from the weld and subjecting it to cutting, etching, or bending to examine its internal makeup. Destructive testing is definitive but damaging, so it's reserved for critical situations or when there's substantial doubt about a weld's quality.
Recognize the Value of Prompt Identification
Catching slag inclusions early can save you time and resources. Immediate remedial actions, such as grinding out the affected area and re-welding, can be taken. It's beneficial to conduct regular inspections throughout the welding process, not just at the end, to intercept potential inclusions before they escalate into larger issues.
In essence, the detection of slag inclusions is a layered approach that starts with keen visual inspection and may extend to sophisticated testing methods. By remaining vigilant and utilizing these techniques, welders can maintain the highest standards in their work and avert the complications that slag inclusions might cause.
3. Navigating the Pitfalls of Slag Inclusions in Welding
Slag inclusions can be the bane of a welder's existence, potentially undermining the strength and integrity of metal connections. To combat this issue effectively, it's crucial to understand the typical culprits behind these unwelcome defects. Let's break down the common factors that lead to slag inclusions and how to address them:
Shielding Gas: Your First Line of Defense
Shielding gas is like an invisible shield for your weld, keeping harmful air elements at bay. If this gas coverage falters, the molten metal is exposed, and slag inclusions are more likely to form. Picture a weld without enough gas coverage as an apple slice left out—it quickly turns brown as it reacts with the air. Similarly, a weld pool reacts with oxygen and nitrogen, leading to contamination.
The Flux Factor: Getting It Just Right
Flux is the welder's friend, but only when used correctly. It's like using the right amount of seasoning in cooking—too much or too little can spoil the dish. In welding, the wrong flux type or quantity can lead to stubborn slag that's hard to remove, increasing the risk of it getting trapped in the weld.
Dialing In Welding Parameters
Imagine driving a car; if you go too fast or too slow, you might not reach your destination safely. The same goes for welding parameters like current, voltage, and travel speed. They need to be just right for the material and welding process. If they're off, you might end up with a poor-quality weld that's prone to slag inclusions.
Technique Matters: The Welder's Craft
A welder's skill is like a painter's brushstroke—it must be precise and deliberate. Incorrect angles, inconsistent arc lengths, or erratic speeds can all create conditions that invite slag inclusions. It's about maintaining a steady hand and a sharp eye to ensure a clean, high-quality weld.
Cleanliness Is Key: Prepping Your Work Surface
A dirty work surface can ruin a weld, much like painting over a dirty wall. Rust, oil, paint, or leftover slag can all interfere with the weld, creating a perfect storm for slag inclusions. A thorough cleaning of the weld area is a simple yet vital step in preventing these defects.
Temperature Control: The Warm-Up Routine
Some metals need a good warm-up before welding, similar to an athlete before a race. Preheating to the right temperature helps prevent the weld from cooling too quickly, which can trap slag. Likewise, managing the temperature between weld passes is crucial for proper slag removal.
The Importance of Interpass Cleaning
When welding involves multiple passes, think of it as layering a cake—each layer needs to be smooth before adding the next. Any leftover slag from a previous pass can get caught under the new layer, leading to inclusions. Thorough cleaning between passes is a must-do step.
By being aware of these common pitfalls and taking proactive measures to avoid them, welders can greatly diminish the likelihood of slag inclusions. It's all about fine-tuning your approach, maintaining your equipment, and sticking to welding best practices. With these guidelines in mind, you're on your way to producing robust, defect-free welds.
4. Essential Tactics to Eliminate Slag Inclusions
Achieving flawless welds means waging a war against slag inclusions, those pesky impurities that can compromise the strength of metal bonds. To ensure your welds are clean and robust, it's important to employ a series of targeted strategies. Let's explore these tactics, designed to keep slag inclusions out of your welding projects.
Selecting the Ideal Flux
Think of flux as the guardian of your weld pool—it's there to protect and cleanse. But not all flux is created equal. You must choose a flux that's compatible with your base metal and the specific welding conditions you're working under. If the flux is too harsh, it can overwhelm the weld with slag. On the other hand, if it's too mild, it won't shield the weld pool adequately. It's like picking the right sunscreen—too strong and it's overkill, too weak and you're not protected.
Fine-Tuning Welding Parameters
Adjusting your welding parameters is akin to setting the right temperature for baking a cake. If the oven's too hot, the cake burns; too cool, and it won't cook through. Similarly, the current, voltage, and travel speed in welding need to be precisely set to match the material's thickness and type. This ensures the weld pool is neither too runny nor too solid, reducing the chance for slag to get trapped.
Mastering Welding Techniques
Your welding technique should be as smooth and consistent as a pianist's keystrokes. In stick welding, for example, the right angle and motion are crucial for spreading the flux evenly and allowing slag to surface. Avoid hasty movements or overly broad weaves, as these can seal slag within the weld.
Preparing a Pristine Welding Surface
Before you start welding, make sure your work area is as clean as a new pin. Any dirt, rust, or leftover slag can sabotage the weld, creating a breeding ground for slag inclusions. It's like painting over a dirty canvas—the end result just won't look good.
Executing Multi-Pass Welding with Care
When your welding job requires multiple passes, treat each layer with the same care as a gardener tending to their plants. After each pass, remove all traces of slag before adding the next layer. Neglecting this step is like planting seeds without clearing away the weeds—they just won't grow right.
Preheating: The Warm Welcome
For thicker materials, preheating is like giving your metal a warm welcome before the main event. It slows down the cooling process, giving slag more time to float away. It's similar to letting a stew simmer—doing so brings all the flavors to the surface.
Choosing the Right Electrode
Selecting an electrode is like choosing the right fishing rod for the catch you're after. Too big, and it's overkill; too small, and it won't do the job. The size and type of the electrode should be tailored to your specific welding task. Some electrodes are even designed to produce slag that's easier to remove—like a non-stick pan that makes cleaning a breeze.
The Final Clean-Up
Once the welding is done, it's time for clean-up. Removing slag from the weld bead and surrounding area is not just about aesthetics—it's like clearing the stage after a performance, ensuring it's ready for the next act.
By integrating these strategies into your welding routine, you'll be setting the stage for impeccable welds, free from the clutches of slag inclusions. With practice and a keen eye for detail, you'll become adept at keeping your welds clean and your metal strong.
5. Solidifying Excellence: The Final Word on Preventing Slag Inclusions
The art of welding transcends mere metal joining; it embodies a dedication to precision and a relentless pursuit of quality. Throughout this article, we've dissected the issue of slag inclusions, those stealthy defects that can undermine a weld's integrity. It's clear that preventing these inclusions isn't just about ticking boxes—it's about embracing a philosophy of unwavering attention to detail and striving for unparalleled craftsmanship.
We've equipped you with a robust arsenal of strategies to combat slag inclusions. From the judicious selection of flux to the meticulous execution of welding techniques, every action you take is a deliberate step towards a pristine weld. It's about more than just the motions; it's about understanding the why behind each process and the impact it has on the final outcome.
Consider your welds as a reflection of your professional pride and expertise. The continuous journey of learning and honing your skills is what forges a master welder. Implement the insights and techniques shared here with confidence and watch as your efforts culminate in welds that are not only structurally sound but also exemplify the high standards of the welding craft.
In conclusion, welding is not merely about joining materials; it's about creating enduring connections that can withstand the tests of time and stress. By mastering the art of preventing slag inclusions, you're not just ensuring the reliability and safety of your projects; you're upholding the revered traditions of excellence that are the hallmark of the welding industry. Keep pushing the boundaries of your abilities with every weld you lay, and the quality of your work will stand as a testament to the skill and care invested in it.
Sharing is Caring
Feedback
At WeldWins, we know we aren't perfect which is why we're always looking for ways to improve. You can help us do better by taking 2 minutes to fill out our simple feedback form.
Any and all feedback is welcome. It could be a complaint, an idea, or even just a comment, we'll always be grateful to hear what you think.