How Can Oxy-Fuel Cutting Transform Your Metalworking Projects?
June 21, 2024
13 min read
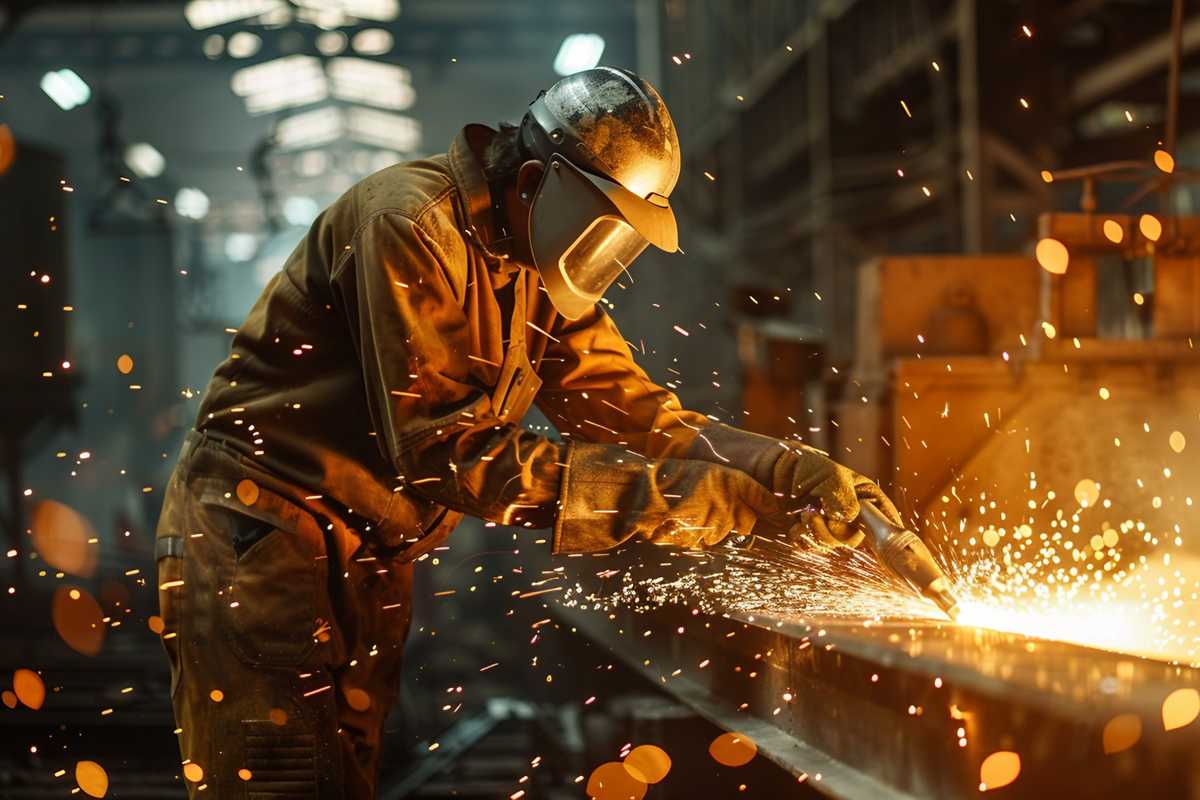
Oxy-fuel cutting stands as a cornerstone technique in metalworking, harnessing the intense energy of oxygen and fuel gases to slice through metal with remarkable precision. This time-honored method is not just about cutting; it's about shaping the world around us, from constructing awe-inspiring structures to crafting intricate metal art.
The versatility of oxy-fuel cutting makes it the method of choice for a myriad of projects. It's the trusted companion for professionals looking to dismantle hefty metal frameworks, tailor components for assembly, or create clean edges for welding. Its speed and control are unmatched, earning it a revered spot among builders, manufacturers, and artists alike.
In this guide, we'll embark on a journey through the essentials of oxy-fuel cutting. We'll dissect the process, introduce the tools of the trade, and share tips to sharpen your cutting edge. Whether you're a seasoned expert aiming to perfect your technique or a curious novice ready to dive into the craft, our comprehensive walkthrough is designed to equip you with the knowledge to excel in oxy-fuel cutting across various applications.
1. Mastering the Oxy-Fuel Cutting Technique
Oxy-fuel cutting is a powerful method that uses a combination of oxygen and fuel gases to cut through metal with impressive precision. This isn't just about blasting metal with heat; it's a controlled chemical reaction that, when done right, slices through steel like butter. Let's break down the science behind this process and go over the gear you'll need to pull it off like a pro.
The Science of Slicing Metal
At the core of oxy-fuel cutting lies oxidation, a chemical reaction where metal meets oxygen and transforms into an oxide. Here's how it works: you heat the metal until it's ready to catch fire in oxygen (this is called the kindling temperature). Then, you hit it with a jet of pure oxygen. The metal catches fire, burns up fast, and the metal oxide that forms gets blasted away by the oxygen stream. This reaction pumps out a ton of heat, keeping the cutting action going and heating up the metal around it, so the cutting continues smoothly.
For a clean and controlled cut, you need high-purity oxygen, the right mix of oxygen and fuel gas, and a flame that's just the right temperature. Nail this balance, and you'll get a cut that's sharp and wastes very little material.
Gear Up for Cutting
Ready to start cutting? You'll need the right equipment. Here's the lowdown:
- Cutting Torch: This tool mixes the oxygen with your fuel gas and points the flame at the metal. It's got two valves to control the gas flow.
- Gas Cylinders: You'll have separate tanks for oxygen (usually green) and your fuel gas (color varies by type).
- Regulators: These are attached to your gas tanks and make sure the gas comes out at a safe pressure.
- Hoses: These tubes carry the gas from the tanks to your torch. They're color-coded—red for fuel gas and green for oxygen—for safety.
- Protective Gear: Sparks and UV light are part of the deal, so gear up with safety glasses, gloves, and flame-resistant clothes.
Getting the hang of the oxy-fuel cutting process is step one on your way to becoming a cutting wizard. By understanding the science behind the cut and getting familiar with the tools of the trade, you're setting yourself up for safe and skillful cutting. With this know-how, you're ready to pick the best fuel gas and learn the moves that'll let you make perfect cuts on all sorts of metals.
2. Fuel Gas Selection: A Key to Cutting Mastery
The choice of fuel gas is a pivotal decision in oxy-fuel cutting, impacting not just the cut's quality but also the efficiency, overall cost, and safety of the operation. Here we'll compare the most popular fuel gases and offer guidance to tailor your selection to the task at hand, ensuring top-notch performance.
Fuel Gas Characteristics
In oxy-fuel cutting, the primary fuel gases are acetylene, propane, and MAPP. Each gas brings its own set of strengths to the table, suited for specific cutting scenarios.
Acetylene: Known for its high flame temperature, acetylene cuts quickly and is ideal for slicing through thin to medium-thick metals. Its downsides are the higher cost and the need for careful handling due to its instability at high pressures.
Propane: As a more budget-friendly option, propane is great for longer, extensive cutting jobs. It's less intense than acetylene, making it a better match for thicker materials, though it may slow down the job when working with thinner metals.
MAPP: This gas, a blend of methyl acetylene and propadiene, has a flame temperature that falls between acetylene and propane. While not as readily available since its original version was discontinued, MAPP's versatility is beneficial for both cutting and brazing tasks.
Tailoring Your Choice
When deciding on a fuel gas, weigh these factors to ensure you're making the best choice for your project:
-
Material Thickness: Acetylene's intense heat is perfect for thin metals, offering fast, neat cuts. For thicker pieces, propane or MAPP's steadier, slower cutting is more effective.
-
Speed vs. Cost: If you need speed, acetylene is your go-to. But if you're watching the budget on a large project, propane's slower pace can be cost-effective, thanks to its lower price and longer burn time.
-
Availability: Make sure your chosen gas is readily available in your area to prevent any hold-ups in your work.
-
Safety First: Each gas has its safety quirks. Acetylene demands careful pressure control, while propane and MAPP, though safer at high pressures, produce more fumes and require good ventilation.
By carefully considering these aspects, you can select a fuel gas that strikes the right balance between cutting performance, cost-effectiveness, and safety. Always follow the manufacturer's recommendations and seek advice from seasoned professionals if you're unsure. With the appropriate fuel gas, your path to precise and efficient oxy-fuel cutting is clear.
3. Step-by-Step Guide to Oxy-Fuel Cutting
Achieving precision in oxy-fuel cutting is all about following a clear set of steps and employing the right techniques. This section will guide you through the process, ensuring you execute each cut with accuracy while upholding the highest safety standards.
Setting Up for Success
Before igniting your torch, proper setup is non-negotiable. Here's what you need to do:
- Inspect Your Gear: Give your equipment a thorough check. Look for any damage on hoses, regulators, and torches. Make sure everything is tightly connected and there are no gas leaks.
- Dress Appropriately: Safety comes first. Wear protective eyewear, fire-resistant clothing, and gloves. Keep a fire extinguisher within reach.
- Prepare Your Space: Remove any flammable items from your work area. Good ventilation is key to prevent gas build-up.
- Secure Your Workpiece: Clamp down the metal you're cutting to keep it stable and minimize the risk of accidents.
Executing the Cut
Now that you're all set up, let's get cutting:
- Ignite the Torch: Turn on the fuel gas valve just a bit and light it with a striker. Add oxygen slowly until you have a neutral flame—this is the best for cutting.
- Adjust the Flame: Fine-tune the oxygen and fuel to get a sharp, blue flame with a concise inner cone. This means your torch is set to go.
- Heat the Metal: Angle the torch and heat the metal's edge until it glows red, signaling it's ready to be cut.
- Begin the Cut: With the metal preheated, hit the cutting lever to release oxygen and move the torch smoothly along your cut line.
- Control Your Speed: Keep the torch at a steady distance from the metal and move at an even pace. Go too slow, and you'll get a messy cut with lots of slag; too fast, and you might not cut all the way through.
- Finish Strong: Slow down as you reach the end of your cut to ensure you slice through the entire thickness. Then, turn off your fuel gas and oxygen as directed by your equipment's guide.
By sticking to these steps and techniques, you'll master the art of oxy-fuel cutting. Practice is essential, so take your time to get comfortable with the equipment and always stick to the safety rules.
4. Overcoming Oxy-Fuel Cutting Challenges
Even the most skilled metalworkers can run into issues with oxy-fuel cutting. Whether you're a beginner or have years of experience, you might find your cuts aren't as clean or precise as you'd like. Let's tackle some of the most common problems you might face and offer clear, actionable solutions to get your cutting back on track.
Pinpointing and Solving Cutting Difficulties
Wavy or Jagged Cuts: If your cuts aren't straight, the culprit could be your cutting speed. Cutting too quickly or too slowly can both lead to poor results. Check the manufacturer's guide for the right speed for your material's thickness and stick to it. Also, inspect your cutting tip for damage or blockages – a clean, correct-sized tip is crucial for a smooth cut.
Too Much Slag: Slag is the leftover metal that cools after cutting. A little is normal, but a lot can mean trouble. It's often a sign that your oxygen jet isn't focused or your cutting angle is off. Make sure your nozzle is spotless and you're holding the torch straight up and down. Adjusting the oxygen pressure can also cut down on slag.
Trouble Lighting the Torch: If your torch won't start, you might not have enough fuel or oxygen. Check that your tanks have enough pressure and all valves are open. Look for leaks in your setup – they can mess with gas flow and are a safety risk.
Subpar Cut Quality: If your cuts just don't look good, you might need to adjust your fuel-to-oxygen ratio, replace worn-out cutting tips, or improve how you handle the torch. Use the fuel and oxygen mix recommended for your gas type and always swap out damaged tips.
Refining Your Cutting Technique
Sometimes, it's not the tools but how you use them. Here are some tips to enhance your cutting skills:
- Hold the torch steady and glide it evenly over your workpiece.
- Keep the right distance between the tip and the metal – about the width of two dimes stacked together.
- Watch the angle of your torch – tilting it can warp your cut.
By focusing on these common issues and their solutions, you can make a big difference in the quality of your oxy-fuel cuts. Practice is key, and the more you get to know your tools and materials, the better you'll be at spotting and fixing problems. Keep these pointers in mind for cuts that are clean and precise every time.
5. Elevating Your Oxy-Fuel Cutting Skills with Advanced Techniques
Once you've got the hang of basic oxy-fuel cutting, it's time to step up your game with some advanced techniques and applications. These can help you tackle more complex projects with ease, whether you're working with different materials or dealing with varying thicknesses. Let's dive into these high-level strategies to take your cutting skills to new heights.
Embracing the Power of Mechanized Cutting
If you're looking to boost your productivity and achieve cleaner, more precise cuts, mechanized cutting systems are the way to go. These high-tech setups use computer control (CNC) to guide the cutting process, delivering consistent results every time. Here's what you gain by going mechanized:
- Non-Stop Productivity: These machines don't get tired. They keep cutting, hour after hour, multiplying how much work you can get done.
- Spot-On Accuracy: CNC can handle complex patterns and keep everything within tight tolerances—something that's tough to pull off by hand.
- Safer Operations: Since the machine does the cutting, you're not as close to the flames and hot metal, reducing the risk of injuries.
Thinking about upgrading to a CNC system? Consider the types of jobs you do. If you're doing the same cuts over and over on a big scale, a CNC cutter could pay for itself with the time and material you save.
Mastering Specialized Cutting for Different Materials
Not all metals are the same, and neither are the techniques to cut them. Here's a quick guide to help you adapt your approach:
- Know Your Metal: Cutting aluminum? You might need to use a special powder to help the process along, since it forms a tough skin when heated. Working with stainless steel? You'll need to tweak your technique a bit differently.
- Adjust for Thickness: If you're slicing through something thick, you'll need to preheat it more and go slower to make sure you cut all the way through. For thin stuff, speed up to avoid warping or melting the metal.
- Get the Edges Right: If the metal's going to be welded, you might need to cut the edges at an angle—a bevel—to get them ready for welding. This means tilting your torch to the right angle to make the bevel.
By getting these advanced techniques down, you'll be ready to take on more complex and varied projects, boosting the quality of your work. Keep pushing your skills forward, and you'll be cutting like a pro in no time.
6. Crafting Your Path in Metalwork: The Oxy-Fuel Cutting Journey
As we wrap up this comprehensive guide, it's clear that mastering oxy-fuel cutting is a journey that blends science with art. From the initial spark of understanding the chemical reactions to the final flourish of cutting through metal, we've covered the spectrum of skills and knowledge needed to excel in this field.
We started with the basics, explaining how oxygen and fuel gases like acetylene, propane, or MAPP gas come together to make precise cuts. We equipped you with a list of essential gear, ensuring you're prepared to start your cutting journey safely and effectively.
Selecting the right fuel gas is a critical step, and we've provided a comparison to guide you in making the best choice for your projects. Safety has been a recurring theme, emphasizing the importance of proper preparation and protective measures to keep you and your workspace secure.
We've walked you through the cutting process step by step, offering clear instructions to achieve clean and accurate cuts. When challenges arise, such as uneven cuts or too much slag, we've provided troubleshooting tips backed by specific examples to help you resolve these issues swiftly.
For those eager to push their skills further, we've introduced advanced techniques and mechanized cutting systems, broadening the scope of your capabilities and opening up new possibilities in metalwork.
Remember, the keys to success in oxy-fuel cutting are consistent practice, attention to detail, and a steadfast commitment to safety. By integrating the best practices from this guide, you're well on your way to facing any metal cutting challenge with confidence. Whether you're just starting out or refining your existing skills, the world of oxy-fuel cutting is rich with opportunities for growth and creativity.
Sharing is Caring
Feedback
At WeldWins, we know we aren't perfect which is why we're always looking for ways to improve. You can help us do better by taking 2 minutes to fill out our simple feedback form.
Any and all feedback is welcome. It could be a complaint, an idea, or even just a comment, we'll always be grateful to hear what you think.