How Can You Overcome Welding Overlap for Stronger Joints?
June 27, 2024
10 min read
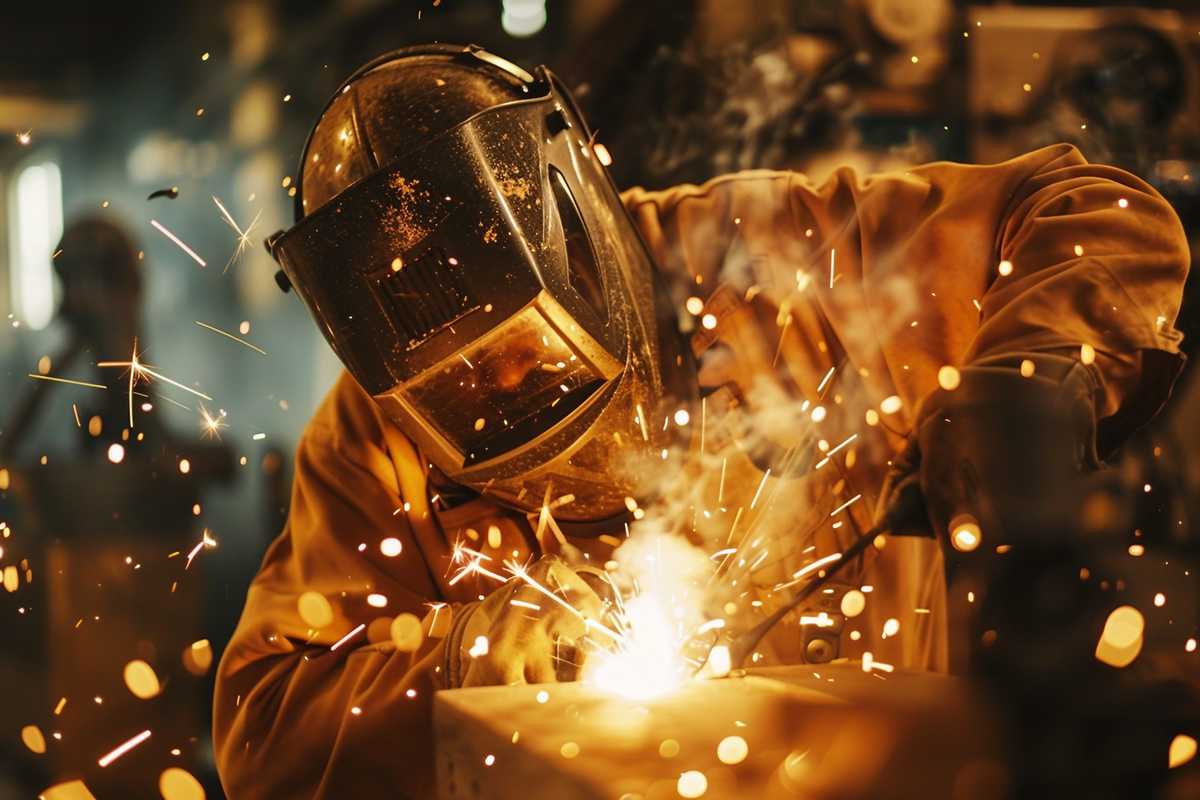
Embark on a journey into the world of welding, where precision melds with skill to forge the backbone of our modern infrastructure. From towering skyscrapers to the vehicles that power our commutes, the strength of a weld can mean the difference between enduring safety and unforeseen failure. Yet, even the most adept welders face challenges that can undermine their craft.
Among these challenges is the pesky welding overlap, a defect where molten metal strays beyond its intended boundary, resulting in a bond that's as unsightly as it is unstable. This article serves as your guide to understanding and conquering welding overlap. We'll dissect its causes, compare it to other welding woes, and reveal strategies to ensure your welds are not only visually impressive but also structurally robust.
Join us in honing your welding prowess to achieve that perfect union of metal, where every joint is a testament to durability and craftsmanship. Let's dive into the techniques that will elevate your welding game to the pinnacle of excellence.
1. Demystifying Welding Overlap: Causes and Consequences
Welding overlap is akin to a spill on a clean tablecloth – it's where the metal flows out of bounds, creating a messy and weak spot in the weld. This defect not only looks unprofessional but also jeopardizes the strength and durability of the welded structure. Imagine a metal blob that's supposed to be a neat line; that's overlap for you. It's like a pancake that's spread too far on the griddle, thinning out at the edges and not cooking evenly.
When we talk about welding defects, each has its own brand of trouble. Porosity leaves tiny holes in the weld, and cracks are like ticking time bombs that can cause a weld to snap unexpectedly. Overlap, on the other hand, is sneaky. It might not cause immediate problems, but over time it can lead to the welded parts separating or breaking because they're not joined as they should be.
In high-stakes fields like aerospace or construction, where every weld counts for safety and performance, understanding and preventing overlap is non-negotiable. It's about making sure that the metal joins smoothly and completely, without any weak spots that could give way under stress.
Spotting overlap is step one in tackling it. Once welders know what to look for – that telltale smudge where the metal has crept out of line – they can adjust their technique, fine-tune their equipment, and ensure their welds are picture-perfect and strong. It's all about keeping an eye on the details and making the necessary tweaks to keep overlap at bay.
2. Unraveling the Causes of Welding Overlap
Welding overlap is a defect that can weaken a weld and ruin its look. To avoid this, welders must understand what causes overlap. Here's a breakdown of the main reasons and how to prevent them:
Setting the Right Amperage
Amperage is the power of the welding current. If it's too high for the metal's thickness, the weld pool gets too runny and spills over, creating overlap. If it's too low, the weld pool won't form properly. The trick is to set the amperage just right, which depends on the metal's type and thickness. For example, thin sheets of steel might need an amperage setting around 100-140 amps, while thicker sections could require upwards of 200 amps.
Mastering Travel Speed
Travel speed is how fast you move the welding torch. Move too slowly, and the weld pool grows and spills over the edges. Move too fast, and the metal doesn't melt enough, making a weak weld. The goal is to find a speed that keeps the weld pool small and controlled. A good starting point is around 6 to 8 inches per minute, adjusting as needed for the material and welding position.
Choosing and Using Electrodes Wisely
The electrodes you choose and how you use them can prevent overlap. Here's what to consider:
Electrode Angle
Holding the electrode at the right angle helps spread the weld pool evenly. An incorrect angle can push the pool to one side, causing overlap. Aim to keep the electrode at about 70 to 80 degrees from the workpiece for even heat and metal distribution.
Electrode Size
The size of the electrode affects the weld pool's size. A big electrode can make a pool that's hard to control, leading to overlap. Pick an electrode size that matches the job. For instance, a 1/8-inch electrode is common for general-purpose welding, while a 3/32-inch might be better for thinner materials.
Fine-Tuning Welding Technique
Your overall welding technique, from preparing the joint to executing the weld, is key to avoiding overlap. Make sure the metal is clean and fits together well before you start. During welding, keep your motion and speed steady, and handle the electrode or torch correctly to keep the arc stable and the pool in check.
By focusing on these areas—amperage, travel speed, electrode choice and handling, and overall technique—you can greatly reduce the chance of welding overlap and make your welds strong and good-looking.
3. Proactive Strategies to Avoid Welding Overlap
Welding overlap can compromise the strength and aesthetics of your metalwork. To prevent this defect, it's essential to adopt a series of proactive strategies that enhance the quality of your welds. Here's how to keep your welding projects on track and overlap-free:
-
Set the Right Amperage: Consult your welding machine's manual to find the correct amperage for the material you're working with. Too much power can melt the metal excessively, causing it to overflow.
-
Maintain Consistent Travel Speed: A steady hand is key. Move too slowly, and the metal pools and overflows; too quickly, and the weld may be weak. Practice to find the sweet spot that yields a smooth bead.
-
Handle Electrodes Properly:
- Angle with Care: Position the electrode at a slight angle, usually 10 to 30 degrees, to spread the weld evenly across the joint.
- Choose the Right Size: Match the electrode size to the job at hand. A large electrode can overwhelm the workpiece, while a small one may not fill the joint adequately.
-
Refine Your Welding Technique:
- Start with a Clean Slate: Remove any dirt or rust from the metal before you begin to prevent weld defects.
- Prepare Edges: For thicker pieces, bevel the edges to ensure deep penetration and a strong bond.
- Adapt Your Bead Approach: Use stringer beads for thin materials to avoid overheating and overlap. For thicker materials, weave beads can be effective but require careful control.
-
Inspect as You Go: Regularly check your work. Catching overlap early means you can correct your technique without having to redo the entire weld.
-
Practice Makes Perfect: The more you weld, the better you'll get. Experiment with different positions and materials to develop a feel for the right settings and movements.
-
Learn from the Pros: If you can, get feedback from experienced welders. They can spot issues you might miss and offer advice to improve your skills.
By integrating these strategies into your welding routine, you can greatly reduce the risk of overlap and ensure your welds are both strong and visually appealing. Remember, taking the time to prepare and execute your welds carefully is far more efficient than fixing mistakes after the fact.
4. Effective Remediation of Welding Overlap
Despite meticulous attention to welding techniques, overlap—a defect where excess metal extends beyond the joint—can still occur. Addressing this issue promptly is essential to maintain the structural and visual quality of your work. Here's a concise guide to rectify welding overlap:
Evaluate the Overlap Severity
Begin by closely inspecting the overlap. The size of the excess metal will dictate your approach: small protrusions might need a quick grind, whereas larger ones could require a more thorough intervention.
Remove Excess Metal with Precision
For slight overlaps, use a grinder to methodically shave off the surplus. Always wear safety equipment like gloves and goggles during this process. Proceed with caution to avoid taking off more material than necessary or harming the adjacent areas.
Re-establish the Weld
Post-grinding, the joint may need a fresh weld for strength and aesthetics. Start with a clean surface to prevent impurities from affecting the weld quality. Select the appropriate welding method and parameters, then reapply the weld with care.
Inspect the Corrected Area
After re-welding, examine the joint meticulously for any signs of imperfections such as new overlaps, cracks, or porosity. A successful correction should look seamless and reintegrate the structural integrity of the original weld.
Verify the Repair's Integrity
For critical projects, you might need to perform non-destructive testing (NDT) on the repaired weld. Techniques like ultrasonic testing or magnetic particle inspection can confirm the repair's quality without causing damage.
Emphasize Prevention
Ultimately, the best strategy is to avoid overlap from the start. Regularly refine your welding practices, adjust equipment settings, and prepare materials properly to reduce the likelihood of defects.
By following these targeted steps, you can effectively manage welding overlap, ensuring your projects are durable and visually appealing. Quick and appropriate action is key to upholding the high standards of your welding work.
5. Perfecting Your Weld: Overcoming Overlap for Lasting Results
In the journey of mastering welding, understanding and preventing overlap is crucial. This article has equipped you with the knowledge to identify and tackle the causes of overlap, ensuring your welds are not only visually appealing but also structurally reliable. We've dissected the factors that lead to overlap, such as amperage settings, travel speed, and electrode choice, and provided actionable advice to help you avoid this common pitfall.
By now, you should be well-versed in setting the correct amperage to match the metal's thickness, moving the welding torch at an optimal speed to prevent pooling, and selecting the right electrode for the job. These elements are the foundation of a strong, clean weld. We've also emphasized the importance of a steady hand and a meticulous approach to your welding technique, which are indispensable in achieving the desired results.
Should you encounter overlap, we've guided you through the steps to correct it, from grinding away excess metal to re-welding with precision. Remember, the goal is to address any issues swiftly to maintain the integrity of your work.
As you continue to refine your skills, let the insights from this article serve as a constant reference. Practice diligently, pay attention to the details, and don't hesitate to seek advice from seasoned welders. With persistence and a commitment to quality, you'll be able to create welds that not only look professional but also stand up to the demands of time and use.
Keep these guidelines close at hand, and embrace the process of learning and improvement. Your dedication to the craft of welding will surely lead to exceptional work that you can take pride in. Here's to achieving seamless welds that are as strong as they are impressive—happy welding!
Sharing is Caring
Feedback
At WeldWins, we know we aren't perfect which is why we're always looking for ways to improve. You can help us do better by taking 2 minutes to fill out our simple feedback form.
Any and all feedback is welcome. It could be a complaint, an idea, or even just a comment, we'll always be grateful to hear what you think.