What are the Essential Welding Techniques for Industry Mastery?
June 24, 2024
15 min read
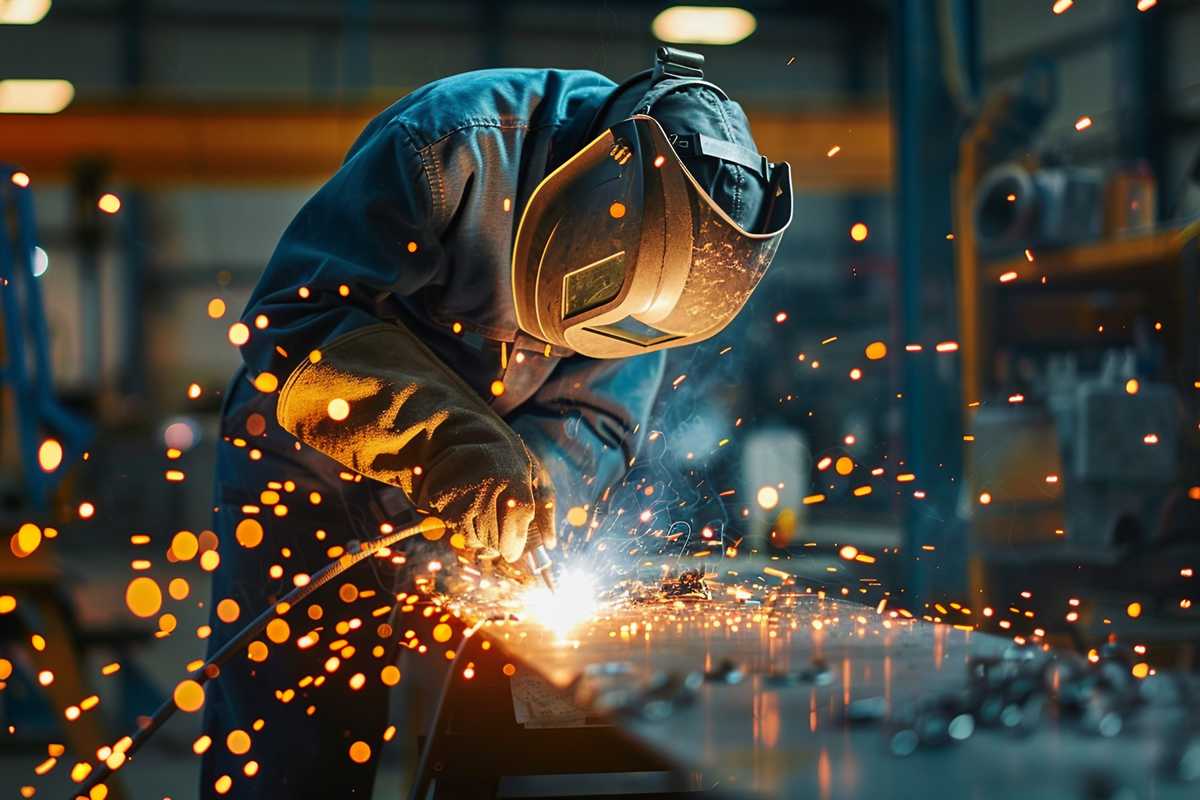
Embark on a journey through the transformative world of welding, a craft integral to the construction and manufacturing industries that shape our daily lives. From the steel bones of towering buildings to the intricate metalwork in our cars, welding is the invisible force that fuses these elements into the sturdy structures we rely on. This guide is your comprehensive roadmap to understanding the pivotal role of welding and mastering its most prevalent techniques.
We'll navigate the nuances of the four primary welding processes that have become the gold standard in the industry: Gas Metal Arc Welding (GMAW or MIG), Gas Tungsten Arc Welding (GTAW or TIG), Shielded Metal Arc Welding (SMAW or Stick), and Flux Cored Arc Welding (FCAW). Each method is tailored to specific tasks, offering distinct benefits that we'll examine closely.
This guide is crafted for everyone, from the experienced welder seeking to polish their skills to the novice ready to spark their first bead. We'll equip you with the essential knowledge, stress the importance of safety, and guide you through the intricate details of each welding process. Your path to welding mastery starts here—let's ignite the torch and begin the transformation from learner to expert.
1. Welding Fundamentals: The Building Blocks of Mastery
Welding is an essential craft that forms the backbone of many industries, from the vehicles we drive to the buildings we inhabit. It's a process that fundamentally involves fusing metal pieces together by melting them with intense heat, often adding a filler material to create a strong, cohesive bond. Each welding method has its own set of benefits tailored to different tasks, making it crucial to understand the basics to select the right approach for your project.
Safety cannot be overstated in the world of welding. The bright light and high temperatures that welding produces can pose serious risks if proper safety measures are not taken. To protect yourself, it's vital to wear the right gear: a welding helmet with the correct lens shade to guard your eyes, flame-resistant clothing to protect your skin, and durable gloves to keep your hands safe from heat and sparks. Ensuring good ventilation in your workspace is also critical to prevent the inhalation of dangerous fumes.
Equally important to safety is having the appropriate equipment. A dependable welding machine and the correct selection of electrodes, clamps, and other accessories are fundamental tools for a welder. Since different welding techniques might require unique equipment, it's essential to know what each job requires before you begin.
A solid understanding of welding also means being familiar with the materials you'll be working with. Metals like steel, aluminum, and stainless steel are common in welding projects, but each one behaves differently when exposed to welding's high temperatures and requires specific approaches.
In essence, the journey to becoming a proficient welder starts with grasping the core principles of welding, prioritizing safety, and equipping yourself with the necessary tools. With this foundational knowledge, you're ready to explore the details of popular welding methods and begin crafting strong, lasting welds.
2. Mastering MIG Welding: A Versatile Tool for Fast Results
MIG welding, or Gas Metal Arc Welding, stands out in the welding world for its remarkable speed and user-friendliness. This technique, which uses a consumable wire electrode and a blend of gases to shield the weld area from contamination, is a go-to choice for both novices and seasoned professionals.
The adaptability of MIG welding is one of its strongest suits. It's capable of joining a wide array of metals, including common ones like steel and aluminum, making it invaluable in diverse fields such as auto repair and infrastructure construction.
Before diving into MIG welding, you'll need to gear up with a few key items: a reliable welding machine, a wire feed unit to guide the electrode, a welding gun for control, and a supply of shielding gas—usually a mix of argon and carbon dioxide—to envelop the weld pool and keep it clean from environmental impurities.
Choosing the correct wire is crucial for a successful weld. Thinner wires work best for delicate materials, while thicker wires are suited for joining heavier sections. The wire feed speed is another critical factor; it must be synchronized with the welding pace to ensure a consistent and strong joint.
MIG welding shines when it comes to projects that require welding large sections quickly. It's not the best pick for extremely thick materials or when a flawless finish is paramount, as it can produce some spatter. Nevertheless, with a bit of practice, you can minimize this and achieve neat, robust welds.
For the best results, keep a steady hand and maintain the right distance between the welding gun and the workpiece. The gun's angle also plays a role in the outcome, so it's worth paying attention to your technique.
In essence, MIG welding is a powerful and efficient method that's suitable for a broad spectrum of welding tasks. With the appropriate setup and a willingness to practice, you can become proficient in MIG welding, enabling you to tackle everything from small home repairs to major industrial projects with confidence.
3. The Art of TIG Welding: Precision and Versatility
TIG welding, or Gas Tungsten Arc Welding, is a sophisticated process that demands precision and control, making it the preferred choice for projects where weld quality is paramount. Unlike other welding methods, TIG uses a tungsten electrode that doesn't melt, ensuring a clean and precise weld. The area being welded is protected from air impurities by a shield of inert gas, usually argon.
This welding technique shines when working with a variety of metals, especially thinner materials like stainless steel and aluminum. It's the go-to method for delicate tasks where a fine touch is needed, such as creating seamless joins in kitchen utensils or crafting detailed metal artwork.
Cleanliness is key in TIG welding. Even the smallest amount of dirt or grease can ruin a weld, so it's important to clean the metal surface thoroughly before you start. Also, keep your workspace free from dust and other contaminants to avoid any defects in your weld.
When welding with TIG, you'll need to keep a steady hand to manage the weld pool, which is the molten metal that forms when you're welding. You may also need to add filler metal with your other hand to build up the weld. This method is slower than others, like MIG welding, but the superior results are worth the extra time. Plus, TIG welding is versatile—it can be done in any position, whether you're working on a flat surface or joining pipes overhead.
To get the best results with TIG welding, start with a clean metal surface. Practice keeping a consistent arc length—this is the distance between the tip of the electrode and the metal you're welding. Also, experiment with the speed you move the torch and the angle you hold it at. These factors can greatly affect the quality of your weld.
In essence, TIG welding is like an art form that requires patience and a detailed eye. With the right technique and practice, you can create strong, visually stunning welds that are up to the highest standards. Whether you're piecing together a custom motorcycle frame or working on components for a spacecraft, mastering TIG welding can lead to a wealth of professional opportunities and personal achievement in the world of metalwork.
4. Stick Welding Essentials: Mastering SMAW
Stick welding, or Shielded Metal Arc Welding (SMAW), is a robust and straightforward welding technique that's been around for generations. It's known for its no-nonsense approach and the ability to withstand tough conditions, making it ideal for outdoor projects or in environments where more sensitive welding methods might fail.
SMAW's popularity stems from its ability to join a wide range of metals and its minimal equipment needs, making it a cost-effective option for many. It's particularly favored in the construction and maintenance sectors due to its portability and the ease of setting up the equipment on-site.
If you're new to welding or looking to refine your SMAW skills, here are some practical tips to guide you:
-
Selecting the Proper Electrode: The choice of electrode affects the strength and quality of your weld. Match the electrode to the metal you're working with—using a 6013 electrode for mild steel is a common choice for its versatility and smooth weld appearance.
-
Consistent Arc Length: A steady arc length is vital for an even weld bead. Aim to maintain an arc length close to the thickness of the electrode's metal core for the best results.
-
Pacing Your Weld: Your travel speed influences weld integrity. Move too fast, and the weld may be weak; too slow, and you risk excessive metal deposit. Find a rhythm that allows the weld pool to cool sufficiently while still maintaining a consistent bead.
-
Skill Development: SMAW requires coordination and a steady hand. Practice on scrap metal to perfect your technique, starting with simple lines and progressing to more complex shapes.
-
Preparing the Metal: A clean work surface is crucial. Remove any rust, paint, or debris to ensure a strong weld. A wire brush or grinder can be used for this purpose.
-
Prioritizing Safety: Protect yourself with a welding helmet, gloves, and flame-resistant clothing. Work in a well-ventilated area to avoid fume inhalation.
While stick welding might lack the finesse of newer welding methods, its reliability makes it indispensable. It's a skill that, once mastered, can be applied to a variety of projects, from fixing farm machinery to erecting steel frameworks. Dedication to practice will lead to durable and reliable welds that can withstand the rigors of time and use.
5. Harnessing the Power of FCAW for Robust Welds
Flux Cored Arc Welding, or FCAW, is a dynamic welding technique that marries the efficiency of MIG welding with the practicality of a flux core. This method stands out because it doesn't rely on external shielding gas, thanks to the flux-filled wire that forms its own protective barrier around the weld. This characteristic makes FCAW particularly suitable for outdoor projects where wind could blow away shielding gas, or in remote locations where hauling gas tanks is impractical.
Imagine you're constructing a bridge or repairing a ship—environments where the elements are against you. FCAW is your ally here, allowing you to work uninterrupted by gusts of wind. The process is straightforward: a wire electrode is continuously fed through a welding gun, melting and fusing materials together. As it melts, the wire's flux core forms a gas shield and creates a protective slag over the weld, safeguarding it from the air and ensuring a clean joint. After cooling, this slag is simply chipped off to reveal a strong, clean weld.
FCAW's main advantage is its adaptability. It's a fast process, making it ideal for projects that require long, uninterrupted welds on thick materials. Unlike other welding methods, FCAW is less sensitive to outdoor conditions, which boosts its appeal for on-site construction or repair jobs.
Choosing the right wire is crucial for FCAW. You'll find two primary types: self-shielding and gas-shielded. Self-shielding wires are perfect for outdoor use since they don't need an external gas source. Gas-shielded wires, while requiring a shielding gas, result in neater welds and are often used indoors or when appearance is important.
When considering FCAW for your project, think about the environment you'll be working in, the thickness of the materials, and how quickly you need to complete the job. FCAW excels with steel and penetrates deeply into the base material, resulting in durable, high-quality welds.
The equipment for FCAW includes a welding machine with constant voltage and a wire feed system. Don't forget about personal safety—welding helmets, gloves, and protective clothing are a must to guard against heat and spatter.
If you're new to FCAW, practice is your best friend. Try out different wire feed rates and gun movements on scrap material before tackling the real thing. And always clean your workpiece before starting to ensure the highest quality weld.
In essence, FCAW is a robust and flexible welding method that's perfect for challenging conditions. With the right tools and a bit of practice, you can leverage FCAW to achieve strong, reliable welds for a wide range of applications.
6. Expanding Your Welding Repertoire with Advanced Techniques
Having mastered the core welding processes, you're now ready to elevate your craft with advanced welding techniques. These specialized methods are your gateway to tackling complex projects and distinguishing yourself as an expert in the field. We'll explore cutting-edge welding practices that promise precision, efficiency, and innovation.
Precision and Efficiency with Laser Beam Welding (LBW)
Laser Beam Welding (LBW) harnesses the power of lasers to join materials with remarkable accuracy. This high-tech method is a favorite in industries where precision is non-negotiable, such as in the delicate assemblies of electronics or the exacting standards of the medical device sector. To excel in LBW, you'll need to fine-tune the laser settings, adjusting the beam's intensity and pinpointing its focus to achieve the desired weld quality.
Clean and Strong Joins via Electron Beam Welding (EBW)
Electron Beam Welding (EBW) offers unparalleled cleanliness and penetration by using a concentrated beam of electrons in a vacuum environment. This technique is ideal for aerospace applications where the integrity of the weld is critical. Learning EBW involves getting hands-on with specialized vacuum chamber equipment and gaining an understanding of how electron beams interact with different metals.
Joining Plastics and Metals with Ultrasonic Welding
Ultrasonic Welding stands out for its ability to join dissimilar materials, such as plastics and metals, without the need for heat. This process is widely used in the automotive industry for assembling complex components like dashboard panels. Mastering this method requires familiarity with the ultrasonic welding machine's settings and an understanding of how different materials respond to ultrasonic energy.
Innovating with Friction Stir Welding (FSW)
Friction Stir Welding (FSW) is a revolutionary technique that uses a specialized rotating tool to blend materials together through friction-generated heat. This eco-friendly method is making waves in the shipbuilding industry for its ability to create strong, high-quality welds in aluminum structures. To master FSW, you'll delve into the mechanics of the process, learning about tool design and the way materials flow and fuse under friction.
Real-Time Precision with Adaptive Welding
Adaptive Welding is at the forefront of welding technology, integrating sensors and control systems to adjust welding parameters in real-time. This smart technique is crucial for projects that require consistent quality across varying conditions, such as in pipeline construction. Embracing adaptive welding means becoming adept with technology, analyzing welding data, and applying a deep understanding of welding principles to make on-the-spot adjustments.
As you venture into these advanced welding techniques, you're not just learning new methods; you're unlocking a higher level of craftsmanship. Each technique demands dedication to practice and a willingness to immerse yourself in the nuances of the process. The journey may be challenging, but the rewards are substantial, paving the way for innovation and excellence in your welding career.
7. Igniting Your Future: The Final Weld
As we draw the curtains on this comprehensive guide, it's clear that welding is not just a trade but a vital skill that molds the infrastructure of modern civilization. From the sleek lines of a sports car to the soaring heights of skyscrapers, welding is the invisible force that binds metal to metal, dream to reality. We've journeyed through the intricacies of the four primary welding techniques—MIG, TIG, Stick, and Flux Cored—each with its own set of strengths for various projects and environments.
Our exploration began with the essentials of welding, where we underscored the non-negotiables: safety and the right tools. These basics form the bedrock for anyone aspiring to thrive in the welding world. We then ventured deeper into each welding process, offering you a clear view of their applications and the nuances that make them effective.
From the adaptable nature of Stick welding, perfect for outdoor conditions, to the finesse of TIG welding, ideal for precision work, we've spanned the full array of skills you'll need to elevate your welding artistry. We've even ventured beyond the conventional, peering into the realm of advanced techniques that push the boundaries of what's possible with metal.
Remember, the path to welding mastery is paved with practice. Each time you weld, you're sharpening your skills, learning from the heat of the moment. Mistakes are simply stepping stones to mastery, so embrace them. Keep your curiosity alive, always put safety first, and relentlessly polish your craft.
By absorbing the insights from this guide, you're now equipped to forge ahead in the vast universe of welding. Whether you're a DIY enthusiast aiming to sculpt metal masterpieces or a professional welder constructing the backbone of industry, the opportunities are as boundless as your ambition. So, don your helmet, light up your torch, and let the sparks of your passion sculpt the metal—and your future.
Sharing is Caring
Feedback
At WeldWins, we know we aren't perfect which is why we're always looking for ways to improve. You can help us do better by taking 2 minutes to fill out our simple feedback form.
Any and all feedback is welcome. It could be a complaint, an idea, or even just a comment, we'll always be grateful to hear what you think.