How Can You Master Different Welding Positions for Optimal Results?
June 19, 2024
10 min read
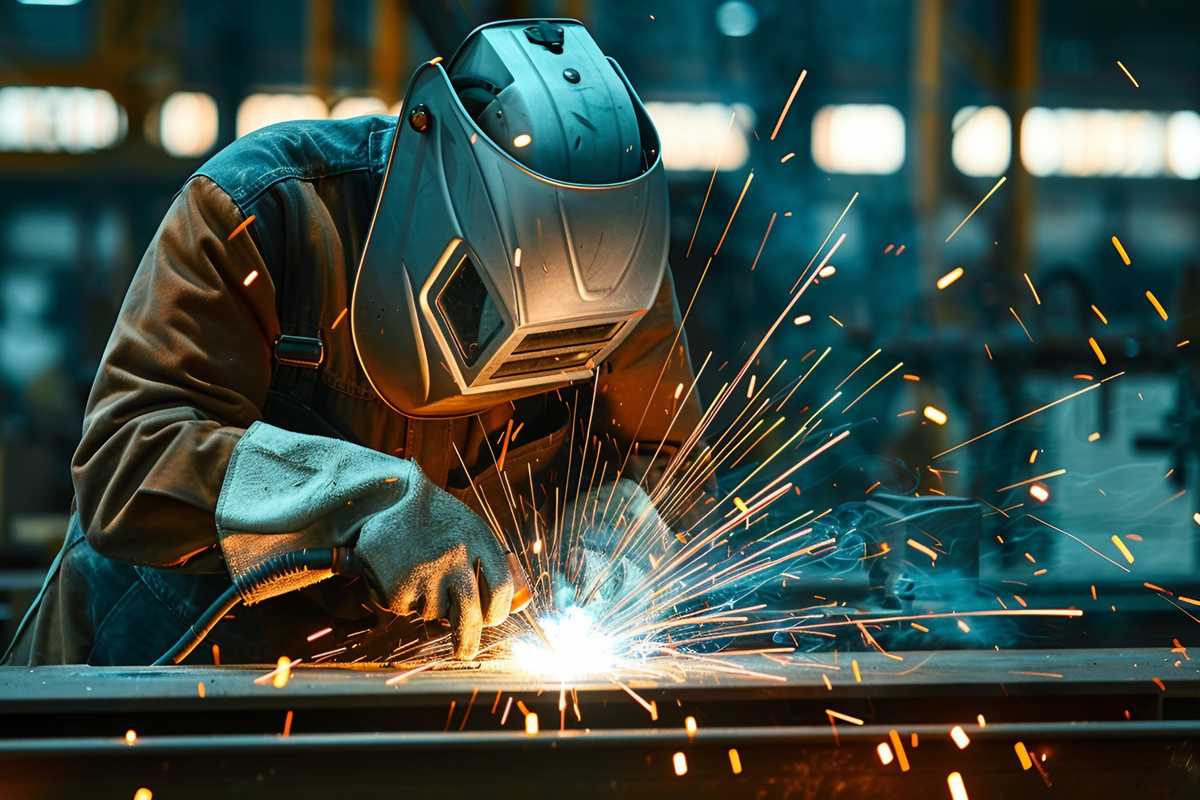
Welding is not just about joining metals; it's an art that demands precision and expertise, particularly when it comes to the positions a welder must adopt. The orientation of the welder and the direction of the weld play a pivotal role in the outcome of the project. Each welding position—flat, horizontal, vertical, and overhead—brings its own set of challenges that must be skillfully navigated to produce a robust, clean, and secure weld.
In this detailed guide, we'll dissect the four fundamental welding positions, each identified by a specific code for groove (1G to 4G) and fillet (1F to 4F) welds. These codes are the language of welders worldwide and are essential for anyone serious about enhancing their welding abilities. These positions are the bedrock of welding proficiency and are used in a multitude of settings, from large-scale industrial projects to simple home repairs.
We'll kick off with the flat position, the starting block for most beginners due to its relative simplicity. Next, we'll tackle the horizontal position, where gravity becomes a welder's adversary, pulling the weld puddle sideways. The vertical position escalates the complexity, demanding meticulous torch control to counteract gravity's pull on the molten metal. Lastly, the overhead position, a true test of a welder's skill, requires impeccable technique to execute a weld from beneath the joint.
For each position, we'll offer clear, actionable advice, and insider tips to help you execute flawless welds. Safety is paramount, so we'll also guide you through the necessary precautions to keep you protected as you practice.
Whether you're just starting out or you're a seasoned welder looking to polish your skills, this guide is packed with insights that will deepen your understanding of welding positions. By the end of this journey, you'll be equipped to approach any welding challenge with confidence and finesse. Let's embark on this educational adventure and transform your welding skills.
1. Mastering Welding Positions: A Comprehensive Guide
Welding requires not just technical knowledge, but also the ability to adapt to different physical positions to ensure a strong and effective join. In this section, we'll take a closer look at the four primary welding positions, each with a unique set of challenges and techniques. These positions are designated by standard codes, which are essential for welders to understand and follow.
Flat Position Welding (1G or 1F)
The flat position, or downhand welding, is where most beginners start. It's the simplest position where the weld is applied to the upper side of the joint, and the face of the weld is horizontal. This position takes advantage of gravity, helping the welder lay down a smooth, even bead. It's perfect for working on large, flat surfaces like plates. To excel in this position, keep your hand steady and move at a consistent pace to distribute the weld metal evenly.
Horizontal Position Welding (2F or 2G)
Horizontal welding is more complex. Here, the welder works on a joint that's horizontal, but against a vertical surface. Gravity can cause the molten metal to droop, so control is key. A popular technique to manage this is 'whipping'—a quick back-and-forth motion with the electrode. This helps control the weld pool and maintain a uniform bead.
Vertical Position Welding (3F or 3G)
Vertical welding is done on a vertical surface, and gravity can cause the weld metal to flow downwards, leading to an uneven bead. Welders combat this by using upward or downward welding techniques, depending on the job's requirements. The goal is to keep the weld pool small and the heat consistent, ensuring the metal is distributed evenly.
Overhead Position Welding (4F or 4G)
Overhead welding is the most challenging position. Welding from underneath the joint, welders must be highly skilled to control the weld pool and prevent dripping. It's crucial to use a smaller weld pool and carefully manage the heat to maintain a steady weld bead. Safety gear is a must to protect from falling molten metal.
By mastering these positions, welders can tackle any project with confidence. It's important to practice each position to understand how to adjust your technique for different scenarios. Knowledge of the materials you're working with and the correct filler metals is also vital. With dedication and practice, these skills will become second nature, allowing you to produce strong, high-quality welds in any situation.
2. Essential Welding Position Techniques for Optimal Results
Welding is both a science and an art, requiring a deep understanding of techniques tailored to each unique position. In this section, we'll break down the essential strategies for welding in flat, horizontal, vertical, and overhead positions, ensuring that you can produce high-quality, durable welds no matter the orientation of your workpiece.
Perfecting the Flat Position
Often the starting point for beginners, the flat position is where the workpiece lies flat, and you weld along the top. To excel in this position, it's crucial to maintain a consistent torch angle—aim for 15 to 20 degrees from vertical. This angle helps control the weld pool and minimizes spatter. Move the torch steadily and at a moderate speed to create a uniform bead. Too fast, and the weld may be weak; too slow, and you risk burning through the metal.
Horizontal Welding Mastery
In horizontal welding, gravity is not on your side, as it can cause the weld pool to sag. To counteract this, employ the 'whipping' technique: a rhythmic forward and back motion that helps maintain a stable weld pool. Angle the torch slightly upwards to fight the downward pull of the molten metal. Adjust your travel speed and arc length to keep the bead consistent, preventing it from becoming too thin or too thick.
Vertical Welding Strategies
Vertical welding presents the challenge of gravity pulling the molten metal downwards. Choose between upward (uphill) welding for better penetration on thicker materials, or downward (downhill) welding for speed on thinner materials. Use a 'zigzag' or 'triangle' pattern to distribute the metal evenly, pausing at the edges to build up the bead. Keep your heat input low to prevent the metal from running down the workpiece.
Overhead Welding Techniques
Overhead welding is the most demanding position, with the risk of molten metal dripping down. To mitigate this, keep your arc length short and your heat input low. A swift side-to-side motion with the torch can help spread the heat and keep the weld pool manageable. Always wear the appropriate safety gear to protect from sparks and spatter. This position requires practice to master, so be patient and focus on developing a steady hand and precise control.
By adopting these position-specific techniques, you'll be on your way to improving your welding quality and versatility. Practice is essential, so invest time in refining your skills across all positions. With dedication and attention to detail, you'll be able to tackle any welding project with confidence and achieve results that are both strong and aesthetically pleasing.
3. Navigating Complex Pipe Welding Positions
Pipe welding presents unique challenges due to the cylindrical nature of pipes and the necessity for precision in joining them at various angles. To ensure the integrity of pipe structures, welders must be adept at advanced welding positions that are critical for producing robust, leak-proof connections. This section will focus on two advanced positions that are integral in the industry: the horizontal rolled position for pipes and the vertical fixed position for pipe welding.
Mastering the Horizontal Rolled Position (1G)
The horizontal rolled position, also known as the 1G position, is a technique where the pipe is rotated on its axis while welding. This approach allows welders to perform the weld as if it were in a flat position, providing a stable environment for a consistent, high-quality weld around the pipe's circumference.
To execute a horizontal rolled weld effectively, consider these steps:
- Secure the pipe on rotating equipment designed to turn it smoothly, such as rollers or a positioner.
- Start your weld at the top of the pipe, where it's easiest to begin, and tack weld to keep the joint stable.
- As the pipe turns, keep your welding torch at a steady angle and pace to ensure uniform heat and penetration.
- Opt for straight weld beads over weaving to control heat input and avoid distorting the pipe.
- Regularly inspect the weld bead for evenness and adjust your technique as needed to maintain quality.
Conquering the Vertical Fixed Position Weld (5G)
The vertical fixed position, or 5G, is more demanding as the pipe remains stationary in a vertical orientation, requiring the welder to move around it. This position is common when pipes are too large or installed in a way that makes rotation impossible.
For successful vertical pipe welding, the backhand welding method is highly effective. This involves angling the torch backward toward the finished weld and dragging it along the seam. Advantages of this method include:
- Enhanced control of heat input, which is vital to prevent melting through the pipe.
- A focused arc that penetrates deeply for a strong joint.
- Easier management of the weld pool, aiding in bead shape control and avoiding drooping.
Key tips for vertical fixed position welding include:
- Begin welding at the pipe's base and move upwards, which helps manage the weld pool with gravity.
- Build the weld with small, consistent beads, either weaving slightly or using straight runs to control heat and bead shape.
- Keep the arc length short to ensure proper fusion and a solid weld.
- Pause to let the weld cool if needed, preventing overheating that can weaken the weld.
By mastering these advanced pipe welding positions, you'll be equipped to handle diverse and complex projects with assurance. Pipe welding demands precision and practice, so continual skill refinement is necessary. As you gain experience, your ability to execute strong, dependable welds in challenging positions will grow, enhancing your craftsmanship and value as a welder.
4. Solidifying Your Welding Expertise: A Final Word
As we wrap up this comprehensive welding guide, it's clear that mastering the art of welding in various positions is a cornerstone of exceptional metalwork. We've journeyed through the nuances of the four primary welding positions—flat, horizontal, vertical, and overhead—and shared targeted advice to help you navigate each one with precision and confidence.
From the basics of laying down a smooth bead in the flat position to the complexities of preventing sag in horizontal welds, and from the careful heat control required in vertical welds to the dexterity needed for overhead challenges, we've covered the essential techniques that pave the way for welding excellence.
Our exploration extended into the realm of pipe welding, where we emphasized the need for uniformity in the horizontal rolled position and the skillful application of the backhand technique in vertical pipe welding. These advanced methods are vital for ensuring the integrity and safety of piping systems in various applications.
The path to welding mastery is paved with consistent practice and a commitment to learning. Each time you strike an arc, you're not just joining metals; you're honing a craft that requires both patience and dedication. Always prioritize safety, investing in the proper gear and adhering to best practices to protect yourself and your workspace.
By embracing the insights and techniques outlined in this guide, you're setting yourself up for success in the welding field. Continue to refine your skills, stay abreast of emerging technologies, and take pride in the precision and durability of your work. Your passion for welding not only elevates your own projects but also upholds the esteemed standards of the welding community.
Sharing is Caring
Feedback
At WeldWins, we know we aren't perfect which is why we're always looking for ways to improve. You can help us do better by taking 2 minutes to fill out our simple feedback form.
Any and all feedback is welcome. It could be a complaint, an idea, or even just a comment, we'll always be grateful to hear what you think.