How Can You Overcome the Hidden Flaws of Weld Porosity?
June 26, 2024
10 min read
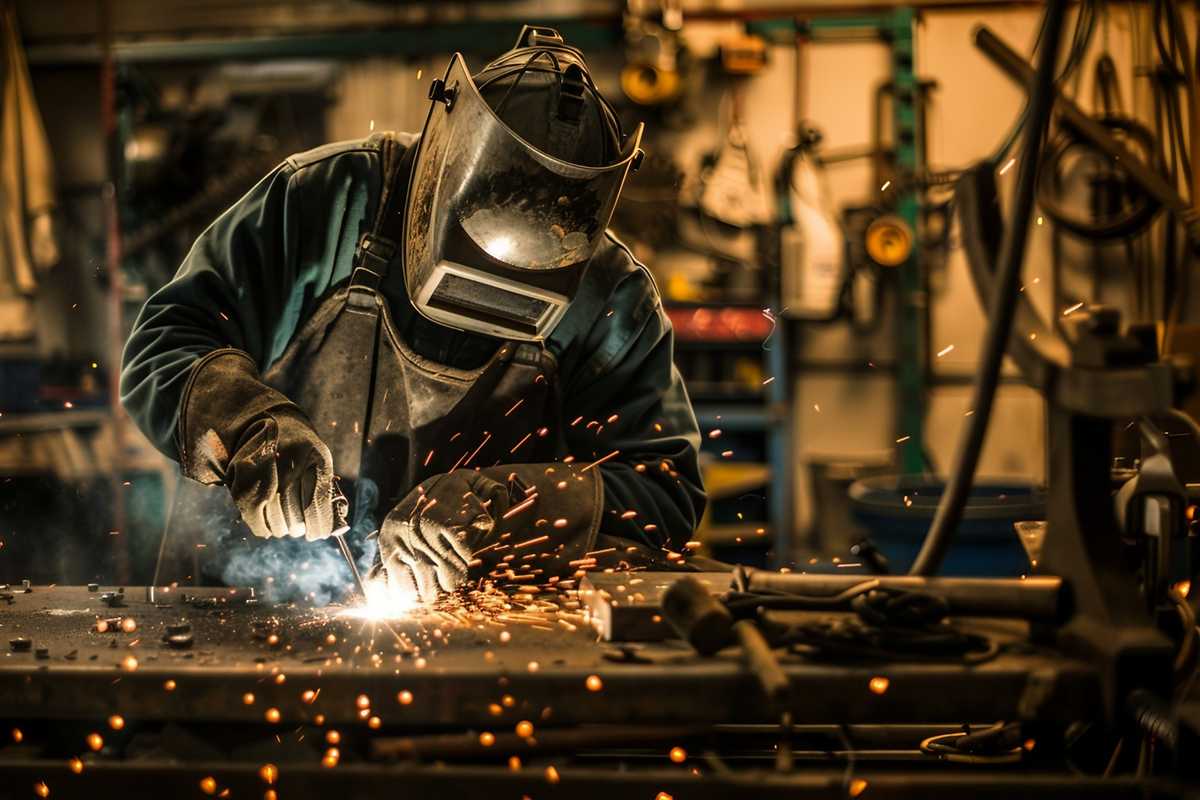
Welding is the backbone of many industries, essential for creating structures and products with strength and endurance. Yet, even the most experienced welders face a sneaky adversary that can weaken their creations: weld porosity. This hidden flaw, characterized by small cavities or bubbles within the weld, can be a silent threat to the safety and longevity of welded assemblies.
Weld porosity often goes unnoticed to the unaided eye, but its effects are far from invisible. These tiny voids can compromise the structural integrity, leading to potential failures under stress. It's a problem that can arise from various sources, including the environment, materials, and welding techniques used.
For those who take pride in their welding work, understanding how to spot, prevent, and fix weld porosity is crucial. This article serves as a comprehensive guide to mastering the challenge of weld porosity. We'll walk you through the details of what causes these imperfections, how to avoid them, and the steps to take if they do occur. With this knowledge, you can ensure your welds are not only visually flawless but also meet the highest standards of safety and durability.
1. Deciphering Weld Porosity: Types and Implications
Weld porosity is a sneaky defect that can weaken the very core of a welded structure. It's essential for welders to recognize and understand the different types of porosity to ensure the durability and safety of their work. Let's break down the various forms of porosity and their impact on weld quality.
Unveiling the Different Faces of Porosity
Porosity is not a one-size-fits-all problem; it comes in various shapes and sizes, each with unique challenges:
-
Surface Porosity: Imagine tiny, pockmarked craters on the moon's surface—that's what surface porosity looks like on a weld bead. These small pits or holes are usually visible without magnification and are a telltale sign of trapped gas during the metal's transition from liquid to solid.
-
Subsurface Porosity: This type is more of a hidden menace, lurking below the surface of the weld. It's trickier to spot and often requires advanced techniques like ultrasonic testing or X-ray inspection to detect.
-
Wormholing: Picture a series of underground tunnels in a weld—these are wormholes. They're elongated voids that form when gas gets trapped and doesn't escape before the metal hardens, potentially weakening the weld's structure significantly.
-
Cratering: Crater porosity is like an unfinished symphony—it occurs at the weld's end where the metal cools last. If the welding stops too abruptly, gas bubbles don't escape, leaving behind craters that can become the starting point for future cracks.
By familiarizing themselves with these types of porosity, welders can take the necessary steps to prevent these defects and maintain the integrity of their welds. Each type requires a keen eye and a steady hand to manage, but with the right knowledge and techniques, they can be effectively minimized or avoided, ensuring a strong and reliable weld.
2. Unraveling the Mystery: What Causes Weld Porosity?
Weld porosity can be a welder's worst nightmare, compromising both the look and the strength of a weld. To produce work of the highest quality, it's crucial to understand and address the factors that lead to this vexing issue. Let's dive into the primary reasons behind weld porosity and how to tackle them effectively.
Pinpointing the Culprits Behind Porosity
Battling Contamination
Contamination is a leading cause of porosity. Oils, grease, dirt, and even the moisture from your breath can spoil a weld. These unwelcome guests get trapped in the molten metal and, as it cools, they form those pesky pores. The solution? A thorough clean-up act. Before striking an arc, use a degreaser or solvent to clean the metal surfaces, then give them a good scrub with a wire brush. This simple prep work can make a world of difference in keeping porosity at bay.
Shielding Gas: Your Invisible Shield
The right shielding gas is like an invisible shield for your weld, keeping harmful air elements like oxygen and hydrogen away from the molten pool. If your gas type isn't a match for your material, or if there's a hiccup in the gas flow or a sneaky leak in the system, porosity can sneak in. Double-check your gas type, ensure your equipment is leak-free, and maintain a steady gas flow to protect your weld from these invisible invaders.
Equipment Health Check
Your welding gear needs to be in top shape to avoid porosity. A wire feeder that's acting up can lead to an unstable arc and, you guessed it, porosity. Regularly inspect and maintain your welding machine, wire feeder, and torch to keep your equipment—and your welds—running smoothly.
Perfecting Your Technique
Even the most experienced welder's technique can be the difference between a flawless weld and one riddled with porosity. The angle of your torch, the speed at which you move, and the length of your arc all play a part. For instance, a torch zipping along too fast can leave behind solidified metal with trapped gases, while a snail-paced weld can overheat the metal, inviting too much gas into the pool. Practice makes perfect, and the right technique will help you steer clear of porosity.
In essence, the main causes of porosity in welding boil down to contamination, shielding gas issues, equipment malfunctions, and technique mishaps. By recognizing and addressing these factors, you can take proactive steps to prevent porosity and ensure your welds are as strong and clean as they should be.
3. Proactive Measures to Eliminate Weld Porosity
Ensuring the strength and reliability of welded structures begins with proactive measures to prevent porosity. Porosity, the presence of tiny holes or voids in a weld, can significantly undermine a joint's integrity. To combat this, welders must adopt a series of preventative strategies that address the root causes of porosity. Here's a breakdown of the critical steps to take:
Meticulous Material Prep
A clean workpiece is the foundation of a porosity-free weld. Follow these steps to prepare your materials properly:
- Scrub Away Impurities: Use a wire brush or grinding tool to remove rust, scale, or old paint from the metal's surface.
- Degrease and Clean: Apply a solvent to eliminate oils, grease, and dirt. Use a fresh cloth for each wipe to prevent spreading the contaminants.
- Precision Cutting: Cut the metal with precision, ensuring edges align snugly to avoid gaps that can trap gas.
Diligent Equipment Upkeep
Your welding equipment's condition directly impacts the quality of your welds. Regular checks and maintenance can prevent porosity:
- Stabilize Gas Flow: Verify that the gas flow is steady and at the right level. Inconsistent flow can introduce air and cause porosity.
- Examine Hoses and Connections: Inspect for any leaks or damage that might allow air to seep in and lead to porosity.
- Nozzle Maintenance: Keep the nozzle clean to maintain proper gas flow and avoid contaminant buildup.
Environmental Awareness
The welding environment can introduce variables that affect weld quality. Take these precautions to minimize porosity risks:
- Shield from Wind: Use barriers to protect your welding area from wind that could disperse the shielding gas.
- Manage Humidity: High humidity can bring moisture into the weld. Weld in a controlled setting or take steps to lower humidity levels.
- Control Temperature: Extreme temperatures can alter the weld's cooling rate and gas coverage. Keep the work area at a moderate temperature.
By diligently following these steps, welders can greatly diminish the chances of porosity in their welds. The key to conquering weld porosity lies not only in knowing how to fix it but in implementing the right practices to prevent its occurrence from the outset.
4. Mastering Porosity Repair: Practical Solutions for Flawless Welds
Spotting the Signs of Porosity
Detecting porosity is the critical first step in the repair process. Look for small holes or uneven spots on the weld's surface, which are clear indicators of surface porosity. For a more thorough examination, especially to uncover hidden subsurface porosity, employ non-destructive methods like ultrasonic testing or X-rays. These advanced techniques can reveal the extent of the porosity without damaging the weld.
Step-by-Step Repair Techniques
Once you've pinpointed the porosity, it's time to take action with these targeted repair strategies:
-
Grind Away the Flaws: Begin with a grinding tool to meticulously remove the porous area, extending slightly past the visible defects to ensure complete removal of all weakened metal.
-
Clean and Re-Weld: After grinding, clean the area to eliminate any residual contaminants. Re-weld with precision, using the right technique and settings to avoid recurrence of porosity.
-
Control Temperature with Heat Treatments: Applying preheat and post-heat treatments can be particularly effective for thick or carbon-rich metals, reducing the likelihood of porosity during the repair.
-
Employ Backing Gas: To combat gas entrapment, introduce a backing gas underneath the weld. This technique provides an additional layer of shielding to prevent atmospheric contamination.
-
Fine-Tune Welding Parameters: Adjustments to your welding machine, such as increasing gas flow, modifying welding speed, or tweaking heat input, can make a significant difference in preventing porosity.
-
Choose the Right Filler Material: Select a filler metal that's less prone to producing gas during welding, which can help in reducing the chances of porosity.
Understanding the root cause of porosity in your specific situation is crucial for a successful repair. Sometimes, a combination of these methods may be necessary to achieve a solid, porosity-free weld. Always prioritize safety and adhere to best practices when conducting weld repairs. With these practical solutions, you can confidently address porosity and ensure your welds are robust and reliable.
5. Sealing Success: Overcoming Weld Porosity
In our comprehensive journey through the intricacies of weld porosity, we've armed you with the knowledge to identify, prevent, and rectify this common but critical issue in welding. Porosity, with its various manifestations like surface pits, hidden voids, and disruptive wormholes, can undermine the strength of your welds. However, understanding its causes paves the way for effective prevention and repair.
We've highlighted the importance of cleanliness, proper shielding gas usage, equipment maintenance, and precise technique to fend off porosity. These proactive steps are your first line of defense, ensuring you start on the right foot for a robust and clean weld.
But when porosity does rear its head, it's not a cause for defeat. We've guided you through the telltale signs to watch for and shared practical, step-by-step solutions to restore your welds to their intended glory. From grinding out imperfections to adjusting welding parameters, these strategies are your toolkit for turning flawed welds into showcases of your skill.
Embracing the challenge of weld porosity is about more than just fixes—it's about cultivating a mindset of prevention, attention to detail, and continuous improvement. By applying the insights from this guide, you can elevate the quality of your work and ensure your welds not only look good but are also structurally sound and durable.
In conclusion, mastering weld porosity is within reach. It requires a blend of knowledge, vigilance, and practice. Commit to these principles, and you'll find yourself producing welds that not only pass the eye test but also stand up to the rigors of use.
Sharing is Caring
Feedback
At WeldWins, we know we aren't perfect which is why we're always looking for ways to improve. You can help us do better by taking 2 minutes to fill out our simple feedback form.
Any and all feedback is welcome. It could be a complaint, an idea, or even just a comment, we'll always be grateful to hear what you think.