How Can You Master the Art of Magnesium Brazing?
June 18, 2024
13 min read
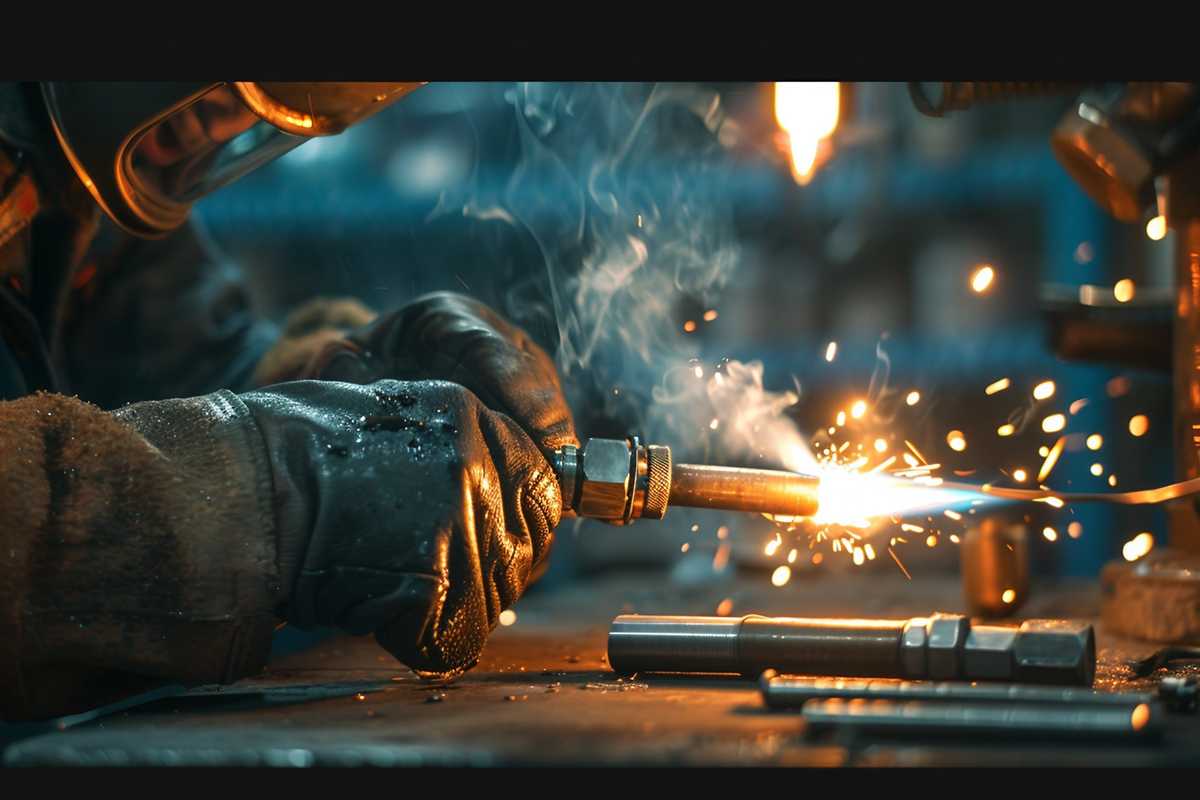
Magnesium, celebrated for its remarkable strength-to-weight ratio, is a cornerstone in industries where reducing weight without sacrificing durability is paramount. Aerospace and automotive sectors, in particular, prize magnesium for its ability to lighten the load while maintaining structural integrity. Yet, the process of fusing magnesium components—brazing—poses distinct challenges. It demands a nuanced understanding of the metal's properties and a mastery of specialized techniques.
This comprehensive guide is tailored to demystify the process of magnesium brazing. We'll navigate through the complexities of working with magnesium and its alloys, pinpoint the differences between brazing and welding, and equip you with a detailed blueprint for the tools, materials, and methods necessary to craft high-quality, resilient joints. Whether you're a seasoned metalworker or a newcomer to the field, the knowledge and strategies outlined here will empower you to enhance your brazing proficiency, ensuring your magnesium assemblies are as robust as they are lightweight.
1. Magnesium Alloys: Composition and Challenges
Magnesium, renowned for its exceptional lightness, is a game-changer in industries where reducing weight is crucial without compromising strength. Its remarkable strength-to-weight ratio, ease of machining, and effective vibration absorption make it an ideal material for sectors like automotive, aerospace, and electronics, where performance and efficiency are paramount.
Delving into magnesium alloys, they are crafted by combining magnesium with other elements such as aluminum, zinc, manganese, silicon, and sometimes rare earth metals. This fusion results in alloys with enhanced characteristics—greater strength, better resistance to corrosion, and the ability to endure higher temperatures. For instance, the alloy AZ31B is a go-to material in the aerospace industry, while AZ91D is celebrated for its superb casting qualities and mechanical strength.
However, magnesium's advantages come with their own set of challenges, particularly when joining pieces through welding or brazing. The metal's tendency to react chemically means it can easily oxidize or burn if not handled with care. Moreover, its high thermal conductivity and expansion rate demand meticulous temperature control during brazing to avoid warping or other deformities.
Brazing magnesium is also tricky due to its vulnerability to galvanic corrosion, which can occur when it comes into contact with different metals. This risk necessitates the use of compatible filler metals and fluxes that can forge strong, corrosion-resistant bonds without harming the magnesium alloy's integrity.
To successfully braze magnesium, it's essential to have a thorough understanding of its unique properties and how they influence the brazing process. This knowledge is the key to choosing the right materials and methods that guarantee the strength and performance of the final product. Armed with this understanding, professionals can confidently tackle magnesium brazing and meet the high standards required in their fields.
2. Brazing vs. Welding: Which is Best for Magnesium?
Choosing the right method to join magnesium parts is crucial for professionals in fields like aerospace and automotive manufacturing. Brazing and welding are two common techniques, but they differ significantly, especially when working with magnesium.
Understanding Welding
Welding involves melting the base materials along with a filler to create a strong bond. It's a common method for joining metals, but when it comes to magnesium—a metal with a low melting point and high thermal conductivity—welding can be challenging. The intense heat can cause warping or other heat-related issues.
The Brazing Advantage
Brazing, in contrast, uses a filler metal with a lower melting point than magnesium. The base metal doesn't melt, which means there's less risk of damaging the magnesium. The filler metal is heated until it flows into the joint, bonding the pieces together as it cools. This method is less likely to distort the parts because it uses lower temperatures.
Why Brazing Often Wins for Magnesium
Here's why brazing is frequently the preferred choice for magnesium:
- Lower Temperatures: Brazing's cooler temperatures mean less risk of warping the magnesium parts.
- Precision: Brazing provides more control, which is great for complex or delicate parts.
- Material Flexibility: Brazing can join different types of materials, including non-metals.
- Cost-Effective Equipment: The tools for brazing are generally more affordable and portable than those for welding.
- Ease of Learning: Brazing tends to be easier to pick up, particularly for working with magnesium.
Brazing Benefits Specific to Magnesium
Magnesium benefits from brazing in several ways:
- Less Thermal Distortion: The lower heat reduces the chance of changing the shape of magnesium parts.
- No Shielding Gas Needed: Unlike welding, brazing doesn't usually require a gas to protect magnesium from burning.
- Versatility: Brazing is suitable for thin-walled magnesium parts that might be damaged by welding.
When to Choose Brazing Over Welding
Brazing is especially useful for magnesium in these scenarios:
- Complex assemblies needing high precision.
- Joining thin or delicate parts.
- Combining different materials.
- Situations where it's important to limit heat exposure.
- When welding tools or expertise are not available.
In summary, brazing stands out as the go-to method for joining magnesium due to its lower temperatures, precision, and versatility. It's a valuable technique for those who want to excel in working with this challenging metal.
3. Selecting the Right Tools and Materials for Brazing Magnesium
To ensure a successful brazing of magnesium parts, it's essential to choose the appropriate tools and materials. This section will provide you with a clear and concise guide to making the best choices for your brazing needs.
Crucial Equipment for Brazing
- Brazing Torch: Opt for a torch that offers a steady flame and can be easily adjusted. It should reach the necessary temperatures for melting your chosen filler metal without causing damage to the magnesium by overheating it.
- Brazing Furnace: For projects on a larger scale, a furnace with accurate temperature controls is ideal. This ensures even heating and prevents hot spots that could weaken the joint.
- Safety Gear: Protect yourself with heat-resistant gloves, safety goggles, and flame-retardant clothing to minimize the risk of burns and exposure to fumes.
- Clamps and Fixtures: Use these to hold your magnesium parts firmly in place during brazing, maintaining alignment for a strong joint.
- Cleaning Supplies: Prepare the metal surfaces with brushes, solvents, or abrasives to remove any impurities that could interfere with the brazing process.
Brazing Materials
- Filler Metals: Choose a filler metal that melts at a lower temperature than magnesium but still bonds well with it. Aluminum-based and zinc-based alloys are commonly used for their compatibility and strength.
- Flux: This substance is crucial for preventing oxidation and helping the filler metal flow into the joint. Make sure to use a flux that's specifically designed for magnesium alloys.
- Flux Remover: After brazing, clean off any leftover flux to avoid corrosion. Have a suitable flux remover ready for this purpose.
How to Choose Consumables
When selecting filler metals and fluxes, consider the following:
- Compatibility: Match the filler metal and flux to the specific type of magnesium alloy you're working with.
- Joint Design: The filler metal should be appropriate for the joint's design, ensuring it fills gaps effectively and provides the necessary strength.
- Operating Conditions: Think about where the brazed joint will be used. The filler metal must be able to withstand any environmental stresses, such as extreme temperatures or corrosive elements.
By carefully selecting your equipment and materials, you're setting yourself up for a successful brazing operation. The quality of your tools and consumables has a direct impact on the strength and durability of the brazed joints.
4. Essential Steps for Preparing Magnesium Before Brazing
To achieve a strong and lasting brazed joint with magnesium, meticulous preparation of the metal surfaces is essential. This section will guide you through the critical steps to prepare magnesium effectively, ensuring the best possible outcome for your brazing project.
Clean the Magnesium Surfaces
Begin by removing any impurities such as oils, grease, or oxidation from the magnesium parts. These contaminants can hinder the bonding of the filler metal. Use a cleaner specifically designed for magnesium or a gentle alkaline solution, scrubbing the surfaces thoroughly. After cleaning, rinse the parts with water to eliminate any leftover cleaning agent.
Roughen the Surface for Better Adhesion
After cleaning, the next step is to create a rough surface texture to enhance the adhesion of the filler metal. Gently sand the area to be brazed with fine-grit sandpaper or use an abrasive pad designed for metal preparation. Ensure you cover the entire surface evenly to maintain a uniform texture that will help the filler metal grip effectively.
Apply Flux to Prevent Oxidation
Flux is vital for a successful brazing process. It prevents oxidation and assists the filler metal in flowing smoothly into the joint. Apply an appropriate flux to both the magnesium parts and the filler metal, choosing a type that's compatible with magnesium alloys to avoid chemical reactions that could weaken the joint.
Assemble and Secure the Parts
Position the magnesium parts as they will be joined and secure them in place. You can use clamps or fixtures to hold them steady. A stable setup is crucial to prevent any movement during brazing, which could result in a weak or misaligned joint.
Prioritize Safety Measures
Magnesium can be highly flammable when in the form of dust or shavings. Keep your workspace clean and free from magnesium debris. Always wear protective equipment such as safety glasses and gloves when preparing magnesium for brazing. Have a Class D fire extinguisher within reach, as this type is specifically designed for metal fires.
By following these detailed preparation steps, you're setting the stage for a successful brazing process. Properly cleaned, textured, and fluxed magnesium surfaces, along with a secure assembly and adherence to safety protocols, will lead to a strong, durable brazed joint.
5. Mastering Magnesium Brazing Techniques
Brazing magnesium is a delicate process that demands precision to achieve durable and robust joints. There are several key techniques to consider, each tailored to different project needs.
Expert Torch Brazing
Torch brazing is a hands-on approach that uses a gas torch to heat the parts and filler metal. Here's how to do it right:
- Clamp the parts firmly to prevent movement during heating.
- Heat the joint area evenly, taking care not to overheat—magnesium's low melting point means a gentle approach is needed.
- Add the filler metal once the parts are hot enough. It should flow into the joint naturally.
- Keep the heat steady until the filler has spread, then let the joint cool in the open air.
Precision Furnace Brazing
Furnace brazing is perfect for complex or multiple parts, providing uniform heat distribution. Follow these steps:
- Position the assembly in the furnace, with the filler metal at the joint.
- Heat to a precise temperature that melts the filler but not the magnesium.
- Use a controlled atmosphere in the furnace to prevent oxidation.
- Cool the parts slowly to avoid stress from temperature changes.
Efficient Dip Brazing
Dip brazing is a quick method for brazing many joints at once. Here's the process:
- Preheat the assembly to prevent shock from the molten filler metal.
- Submerge the assembly in the filler metal bath, covering all joints.
- Keep it in the bath until the filler has fully penetrated the joints.
- Remove and cool the assembly, using a fixture to maintain alignment.
Achieving Optimal Brazed Joints
- Clean all surfaces before starting to ensure the filler metal adheres well.
- Select the right flux to aid filler flow and prevent oxidation.
- Manage the heating rate to avoid warping the magnesium.
- Choose a filler metal that complements the magnesium alloy and the project's needs.
- Maintain precise temperature control to prevent melting the base metal.
- Design joints with the correct gap for capillary action.
By adhering to these methods and tips, you can perfect the art of brazing magnesium for strong, lasting joints across various industrial uses. Whether opting for torch, furnace, or dip brazing, a deep understanding of each technique's intricacies is crucial for achieving the best results.
6. Finalizing the Brazing Process: Post-Brazing Best Practices
The completion of the brazing process marks the beginning of crucial post-brazing practices that are essential for ensuring the longevity and functionality of the magnesium joint. These practices are designed to preserve the structural integrity of the joint and guarantee its performance in its intended application.
Thorough Cleaning for Joint Integrity
After the joint has cooled, it's imperative to remove any remaining flux, which can cause corrosion if neglected. A soft-bristled brush should be used to gently scrub away flux residues. For more stubborn remnants, a warm water rinse or a mild acid solution may be necessary. It's important to finish with a clean water rinse to prevent any harmful chemical reactions that could damage the magnesium.
Rigorous Inspection to Assure Quality
A thorough inspection of the brazed joint is necessary to confirm a successful brazing process. Indicators of quality include a smooth fillet and consistent coloration around the joint. Employ visual checks and non-destructive testing methods, such as dye penetrant or ultrasonic testing, to uncover any hidden flaws like voids or cracks that could weaken the joint.
Addressing and Resolving Common Brazing Issues
Despite careful brazing, issues such as porosity or cracking may occur. Porosity can be the result of excessive moisture or insufficient cleaning prior to brazing. In such cases, re-brazing after additional cleaning may be required. Cracks, often caused by thermal stress or incorrect filler metal choice, necessitate either re-brazing or possibly employing an alternative brazing technique or filler metal.
Guaranteeing the Joint's Durability
For the brazed joint to last, it's important to consider the environment where the magnesium component will operate. Protect the joint from harsh substances and extreme temperatures to prevent weakening. Regular maintenance and inspections are key to catching issues early and avoiding joint failure.
By adhering to these post-brazing best practices, you can significantly improve the quality and durability of your magnesium brazed joints. Proper cleaning, detailed inspection, and prompt issue resolution are critical to the success of your brazing endeavors.
7. Perfecting the Craft: A Recap of Magnesium Brazing Mastery
As we conclude our comprehensive exploration of magnesium brazing, let's reflect on the key insights and strategies that will elevate your brazing projects to professional standards. We've journeyed through the intricacies of magnesium's properties, the advantages of brazing over welding, and the critical selection of tools and materials tailored for this unique metal.
We've underscored the importance of thorough preparation, from meticulous cleaning to precise assembly, setting the stage for a flawless brazing process. Our deep dive into brazing techniques—be it with a torch, in a furnace, or through dip brazing—has equipped you with the knowledge to choose the best method for your specific needs and to execute it with precision.
Post-brazing practices were highlighted as the final, yet crucial steps to ensure the longevity and functionality of your brazed joints. From diligent cleaning to rigorous inspections, these practices are your assurance of a job well done.
By embracing the detailed guidance provided, you're now ready to approach magnesium brazing with a newfound level of confidence and competence. Remember, the path to excellence in brazing is paved with practice and a commitment to ongoing learning. Take these lessons forward and become a distinguished practitioner in the art of magnesium brazing.
Sharing is Caring
Feedback
At WeldWins, we know we aren't perfect which is why we're always looking for ways to improve. You can help us do better by taking 2 minutes to fill out our simple feedback form.
Any and all feedback is welcome. It could be a complaint, an idea, or even just a comment, we'll always be grateful to hear what you think.