What Does the Future Hold for Resistance Welding?
April 28, 2024
12 min read
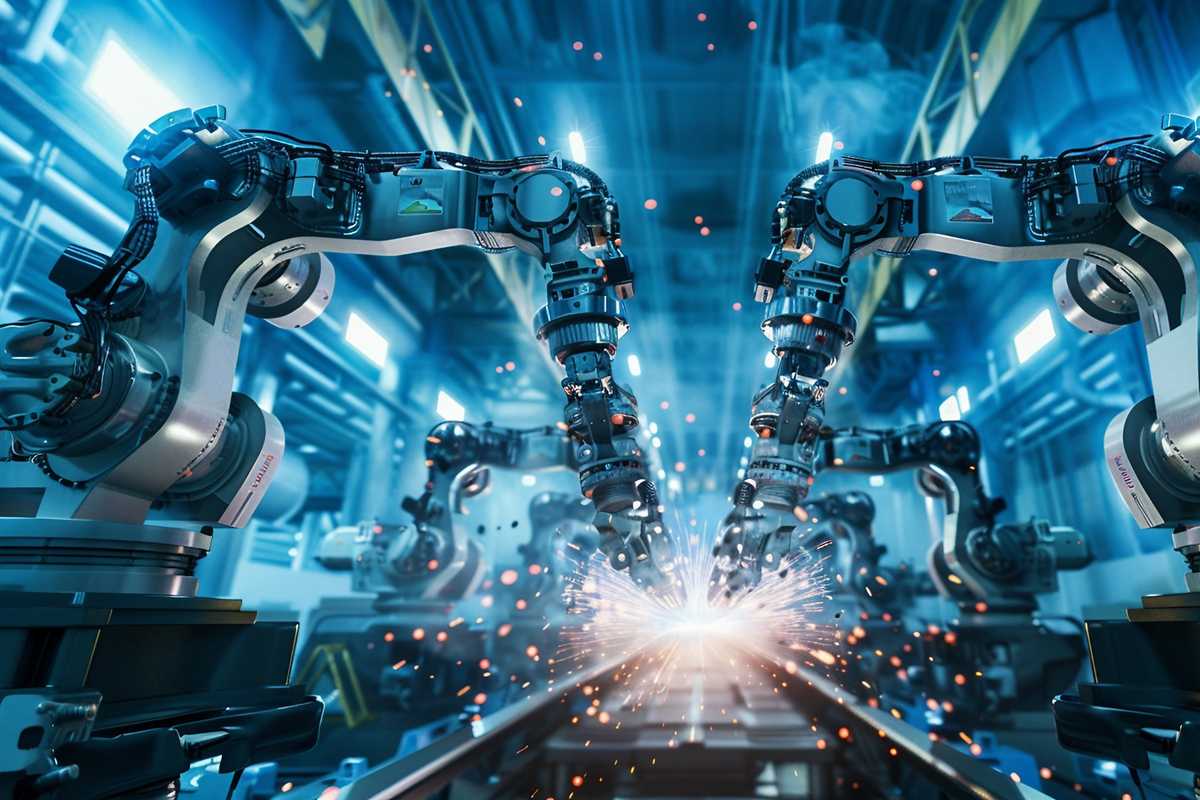
Introduction
Resistance welding is a transformative technique in manufacturing, enabling the fusion of metal parts with precision and strength. This method is distinguished by its use of electric current and pressure to create welds, eliminating the need for additional materials like solder. Its efficiency and reliability have made it indispensable in industries such as automotive and electronics, where it's essential for assembling complex components quickly and with minimal thermal distortion.
In this comprehensive guide, we'll navigate through the intricacies of resistance welding, shedding light on its various forms, including spot, seam, projection, and butt welding. Each of these methods is tailored for specific tasks and materials, and understanding their applications is crucial for anyone looking to excel in the manufacturing field.
Join us as we explore the principles that make resistance welding work, its practical applications, and the latest advancements that keep it at the forefront of manufacturing technology. Whether you're a seasoned professional or new to the field, this article will provide you with a deeper understanding of how resistance welding continues to shape the production landscape.
2. The Fundamentals of Resistance Welding
Resistance welding stands out in the manufacturing world for its unique approach to fusing materials. This process generates heat internally by passing an electric current through the metals to be joined, a method that distinguishes it from traditional welding techniques that typically rely on external heat sources. The absence of flames or arcs makes resistance welding a cleaner and more controlled procedure, as it doesn't require additional substances like filler materials or fluxes.
At the heart of this process lies the concept of electrical resistance. Imagine running water through a narrow pipe—the friction created by the pipe's walls slows down the water flow. Similarly, when an electric current flows through metal, the natural resistance of the metal to the current generates heat. By carefully adjusting the current's strength and the duration it's applied, we can control the amount of heat produced, ensuring the metals reach the perfect temperature to meld together.
There are several specialized forms of resistance welding, each designed for specific tasks:
-
Spot Welding: Common in the automotive industry, this method uses two electrodes to press against the metal sheets and pass a current through them, creating a "weld nugget" that bonds the sheets at specific points.
-
Seam Welding: Operating like an extended version of spot welding, this process forms a continuous, leak-tight seam, ideal for constructing tanks and containers.
-
Projection Welding: This technique is excellent for joining parts with uneven surfaces or varying thicknesses. It uses strategically placed bumps or projections on the parts to focus the welding current, ensuring a solid connection.
-
Butt Welding and Flash Butt Welding: Used to join the ends of metal parts, butt welding applies heat until the parts meld together. Flash butt welding adds a dynamic step where the parts are rapidly pressed together, creating a "flash" that cleans the surfaces before fusing them.
Understanding these processes is crucial for anyone looking to achieve consistent, high-quality welds. By selecting the right method and fine-tuning the welding parameters, manufacturers can create durable joints that withstand the rigors of their intended applications.
3. Decoding the Science of Resistance Welding
Resistance welding is a process that ingeniously uses the principles of electricity to bond metal pieces together. It's a bit like toasting bread in an electric toaster. Just as the toaster uses electrical resistance to generate heat and toast the bread, resistance welding uses the resistance of metal to an electric current to create the heat needed for welding.
Here's how it works: when electricity flows through metal, it encounters resistance, which produces heat. This is the same concept behind the red glow of a heater's coils. In resistance welding, this heat is precisely controlled to melt the metal at specific points, allowing two or more pieces to be fused together when pressure is applied.
The formula for this process is quite simple: Heat (H) = I²Rt. This is known as Joule's law, where 'I' represents the electric current, 'R' is the resistance, and 't' is the time the current runs. The more current and resistance there are, and the longer the current is applied, the more heat is generated.
Different metals react differently to this process. For example, stainless steel, which doesn't conduct electricity very well, is perfect for resistance welding because it naturally heats up more at the point of contact. On the other hand, aluminum conducts electricity too well, so it tends to spread the heat around, making it a bit trickier to weld.
The pressure applied is just as important as the heat. It's like pressing down on a sandwich to make sure the fillings stick together; the right amount of pressure ensures the metals bond properly as they cool down. But just like with a sandwich, too much pressure can squeeze out the good stuff—in this case, the molten metal—resulting in a weak weld.
To get the perfect weld, the process is broken down into four stages: squeeze, weld, hold, and off. During the squeeze stage, the welding machine presses the electrodes against the metal to make sure there's good contact. Next, during the weld stage, the current is switched on, and the heat is generated. The hold stage is when everything cools down under pressure to solidify the bond. Finally, the off stage gives the machine a brief rest before starting the next weld.
By understanding and controlling these factors—the electrical and thermal properties of metals and the welding cycle—manufacturers can create strong, reliable welds for all sorts of products, from cars to electronics.
4. Weighing the Pros and Cons of Resistance Welding
Resistance welding is a technique that has revolutionized the manufacturing industry with its quick and reliable method of joining metals. However, it's important to weigh both the benefits and the challenges that come with this process to fully understand its impact on production.
The Benefits of Resistance Welding
The speed of resistance welding is unmatched. It's a rapid process that allows for a large number of parts to be joined in a short amount of time, which is especially beneficial in fast-paced industries like car manufacturing.
Consistency is another major advantage. With resistance welding, you can expect every weld to be just like the last one, thanks to the precise control of the welding machines. This is crucial when making products that require uniformity, such as in the assembly of electronic devices.
Energy efficiency is a standout feature of resistance welding. It focuses energy right where it's needed, reducing waste and saving on costs. This is not only good for a company's bottom line but also for the environment, as it supports sustainable practices in manufacturing.
The process is also cleaner since it doesn't need extra materials like flux or filler metals. This means there's less mess and a lower impact on the environment.
Versatility is another key point. Resistance welding isn't picky—it can join a variety of metals, which is great for industries that use different kinds of materials.
The Challenges of Resistance Welding
Despite its many benefits, resistance welding isn't without its hurdles. The cost of the welding equipment can be steep, which might be a problem for smaller companies or those just starting out.
Maintenance is another issue. The electrodes used in the process wear out and need to be replaced regularly to keep the welds strong. This can slow down production and add to costs.
The skill level required for resistance welding is high. Operators need to know the ins and outs of the machines and the materials they're working with to get the best results. This means investing in training and gaining experience, which can be a barrier for new employees.
Not all materials are suitable for resistance welding. Metals like aluminum alloys, which conduct electricity really well, can be tricky to weld because they don't heat up as easily in the right spots.
Finally, the cleanliness of the metals is vital for a strong weld. Any dirt or oil can weaken the weld, so there's an extra step in making sure everything is clean before starting, adding to the complexity of the process.
In essence, resistance welding is a powerful tool in manufacturing, offering speed, consistency, and energy savings. However, it's important to consider the initial investment, ongoing maintenance, the need for skilled workers, material limitations, and the importance of cleanliness. By addressing these challenges, industries can make the most of resistance welding and keep it as a key player in production.
5. Charting the Future: Innovations in Resistance Welding
As we look to the horizon, resistance welding is not just holding steady; it's charging forward with breakthroughs that promise to elevate its role in manufacturing. The relentless pursuit of efficiency, superior weld quality, and the ability to join a diverse array of materials is driving innovation in this field.
One of the most exciting developments is the advent of advanced control systems. Picture a resistance welder that's not just a tool but a smart partner, equipped with cutting-edge sensors and intelligent algorithms. These systems are like the welder's sixth sense, constantly monitoring the welding process and making on-the-fly adjustments to ensure every weld is as close to perfect as possible. For example, if the system detects a slight change in the material's resistance—perhaps due to varying thickness or electrode wear—it can tweak the welding parameters to compensate, ensuring a consistent outcome every time.
Electrodes—the points of contact in resistance welding—are also getting a high-tech makeover. Researchers are experimenting with new materials that are tougher and can handle heat better, reducing wear and tear. Imagine electrodes made from advanced composites that last longer and keep their cool even under extreme temperatures, making them more reliable and cost-effective in the long run.
The manufacturing world is also embracing automation and robotics with open arms, and resistance welding is no exception. Robotic welders are stepping onto the scene, bringing with them the promise of precision and repeatability that human welders can find challenging to match. These robotic marvels can be programmed for complex tasks, boosting productivity and allowing for more intricate and delicate welds.
In a bold move, the industry is tackling the challenge of welding dissimilar materials—like joining metals to plastics—a feat that once seemed nearly impossible. This innovation could revolutionize sectors such as automotive and aerospace, where the demand for lightweight yet strong materials is skyrocketing.
The digital transformation of the industry, often referred to as Industry 4.0, is set to leave its mark on resistance welding too. Imagine a world where welding machines are part of a network, communicating with each other and making smart decisions based on real-time data. This level of connectivity could lead to predictive maintenance, where the machines can alert operators to potential issues before they escalate, minimizing downtime and keeping production humming along.
Lastly, the push for sustainability is spurring research into energy-efficient welding processes. As companies strive to shrink their environmental footprint, resistance welding is expected to evolve, becoming even more energy-conscious without compromising on weld integrity.
In essence, the trajectory of resistance welding is set for an exciting future. With smarter machines, innovative materials, and a nod to environmental responsibility, these advancements are poised to ensure that resistance welding continues to be an essential asset in the manufacturing world.
Conclusion: Embracing the Future of Resistance Welding
As we wrap up our exploration of resistance welding, it's clear that this method is more than just a way to join metals—it's a vital part of the manufacturing world's backbone. We've journeyed through the different resistance welding techniques, from the pinpoint precision of spot welding to the continuous bonds of seam welding, and the targeted force of projection welding to the end-to-end fusion of butt welding. Each technique is a specialized tool in the manufacturer's kit, designed to tackle specific challenges and materials.
We've uncovered the scientific principles that make resistance welding so effective. The dance of electricity and resistance that generates the heat necessary for welding is a delicate balance, one that requires knowledge and precision to master. The choice of electrode material, the weldability of the metals, and the careful control of the welding cycle are all critical factors that determine the strength and quality of the weld.
The benefits of resistance welding shine through in its speed, consistency, and energy efficiency. It's a method that can keep pace with the demands of high-volume production while minimizing waste and environmental impact. Yet, we've also recognized the hurdles, such as the investment in specialized equipment and the need for skilled technicians to operate and maintain this machinery.
Looking to the future, resistance welding is poised for exciting advancements. Innovations in control systems and electrode materials are on the horizon, promising to make welding even more reliable and cost-effective. The integration of robotics and automation stands to revolutionize the precision and capabilities of welding operations. And as we move towards a more connected and sustainable industry, resistance welding is adapting to meet these new standards without sacrificing quality.
In summary, resistance welding is an indispensable technique that continues to evolve and adapt. It's a testament to the ingenuity of the manufacturing industry, offering a reliable and versatile solution for today's challenges and tomorrow's innovations. As we continue to refine and advance resistance welding, we can look forward to a future where the production of high-quality, durable products is not just a goal but a standard, meeting the ever-changing demands of a dynamic global market.
Sharing is Caring
Feedback
At WeldWins, we know we aren't perfect which is why we're always looking for ways to improve. You can help us do better by taking 2 minutes to fill out our simple feedback form.
Any and all feedback is welcome. It could be a complaint, an idea, or even just a comment, we'll always be grateful to hear what you think.