What is Friction Welding and How is it Changing Manufacturing?
April 28, 2024
13 min read
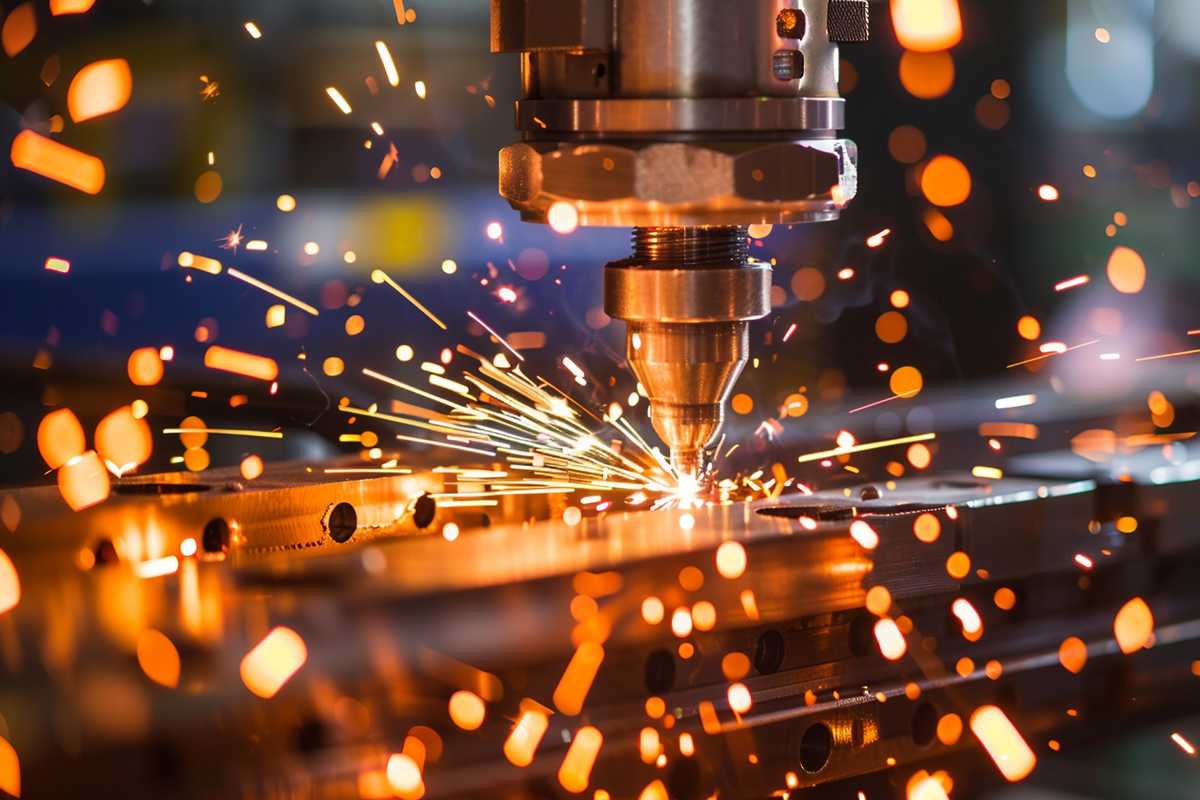
1. Introduction: The Power of Friction in Modern Manufacturing
Welcome to the world of friction welding, a groundbreaking technique that has revolutionized how we join materials in the manufacturing industry. This process is unique because it doesn't rely on melting metals with a filler; instead, it uses the heat generated from friction and pressure to create incredibly strong bonds. Think of it as the difference between using glue to stick pieces of paper together and pressing them so firmly that they become one.
Friction welding isn't just a neat trick—it's a vital innovation that has transformed production lines across the globe. From the cars we drive to the planes that soar above us, this method has become essential for assembling parts that need to be exceptionally reliable and robust.
Imagine the automotive industry, where the strength of a weld can mean the difference between safety and disaster. Or consider the aerospace sector, where even the smallest flaw can lead to catastrophic failure. Friction welding steps up to these challenges, offering a way to join different materials while maintaining their original strength and integrity.
In this article, we'll take a closer look at how friction welding works, the various techniques available, and the incredible range of applications it has. So buckle up and get ready to discover how this innovative process is pushing the boundaries of manufacturing and engineering.
2. Exploring the Mechanics of Friction Welding
Friction welding is a revolutionary technique that joins materials using heat from mechanical friction and pressure, without melting them. This method produces joints of exceptional quality with fewer imperfections than traditional welding.
The Friction Welding Process Explained
Imagine rubbing your hands together on a cold day. The friction generates heat, warming your hands. Friction welding works on a similar principle but at a much higher intensity. Two pieces of metal are rubbed together with such force that they heat up and become malleable. Then, with a final push, they are fused into one solid piece. This process can be completed in mere seconds and is meticulously fine-tuned for each specific task.
Diving Into the Different Techniques
Friction welding comes in various forms, each tailored for specific jobs:
-
Rotary Friction Welding: Picture a drill spinning against a surface. In this method, one metal piece spins rapidly against a stationary piece, perfect for round items like pipes or rods.
-
Linear Friction Welding: Here, one piece moves back and forth against another. It's like sawing wood, but instead of creating sawdust, you're creating a weld. This is great for parts that aren't round, like blades or flat panels.
-
Friction Stir Welding: Think of mixing ingredients with a spoon. A special tool stirs the metals together at the seam, blending them without melting. This technique is a favorite in industries where precision is key, like in aerospace or automotive manufacturing.
Each method has its own recipe—how fast to move, how much pressure to apply, and for how long. These "recipes" are crucial to ensure a consistent and top-notch weld every time.
By understanding the ins and outs of friction welding, manufacturers can pick the best method for their needs, ensuring a strong, lasting bond. It's a smart choice for a wide range of applications, from creating sturdy car parts to ensuring the reliability of space-bound rockets.
3. Friction Welding: A Key Player in Diverse Industries
Friction welding is not just a process; it's a game-changer for industries that demand the utmost in durability and precision. This section highlights how this innovative technique has become indispensable in sectors such as aerospace, automotive, marine, and electronics, each with its own set of rigorous standards.
The Aerospace and Automotive Edge
In the high-stakes world of aerospace, every component counts. Friction welding steps up to the plate, delivering joints that are exceptionally strong and can endure the harshest conditions. Turbine blades and engine parts, for instance, benefit from friction welding's ability to fuse materials seamlessly, ensuring that aircraft remain safe and perform at their best.
Similarly, the automotive industry relies on friction welding for parts that are integral to a vehicle's operation and safety. Drive shafts and steering systems are just a couple of examples where this method provides consistent and reliable welds. The efficiency and repeatability of friction welding make it perfect for the large-scale production that this industry demands.
Navigating Marine Challenges and Powering Electronics
The marine industry faces a unique battle against corrosion and the relentless force of the sea. Friction welding offers a solution by joining large, structural parts and propeller shafts that not only hold up against corrosion but also maintain watertight integrity. The ability to join different types of metals is a significant advantage in this field, where material properties can be as varied as the ocean itself.
Electronics manufacturing, where precision is paramount, also benefits from friction welding. Connections in batteries and heat sinks need to be mechanically sound and conduct electricity flawlessly. Friction welding achieves this with pinpoint accuracy, ensuring that electronic devices perform reliably and efficiently.
Friction welding's role in these industries is a testament to its versatility and the trust that manufacturers place in its capabilities. By delivering strong, durable, and dependable joints, it meets the stringent quality standards of these diverse sectors, solidifying its position as a foundational technique in modern manufacturing.
4. Friction Welding: Superiority and Sustainability in Joining Techniques
Friction welding is not just another way to join materials; it's a superior approach that outshines traditional welding in several key areas. Let's delve into the distinct advantages that make friction welding the go-to choice for a variety of industries seeking quality, efficiency, and sustainability.
Unmatched Joint Strength
The standout feature of friction welding is its ability to produce exceptionally strong joints. Traditional welding methods often weaken materials due to high temperatures that melt and then solidify them. In contrast, friction welding uses mechanical pressure and movement to join materials at a molecular level without reaching their melting points. This innovative approach results in bonds that are typically stronger than the materials being joined, ensuring durability and longevity.
A World of Material Possibilities
Friction welding breaks down barriers when it comes to material compatibility. It allows for the joining of different metals and alloys that would pose a challenge for conventional welding techniques. This versatility empowers engineers to craft components that leverage the best properties of multiple materials, leading to innovative designs and enhanced product performance.
Eco-Friendly and Worker-Safe
This method is a win for both the environment and workplace safety. It eliminates the need for filler materials, fluxes, or shielding gases, which traditional welding relies on. As a result, friction welding produces no harmful UV radiation or toxic fumes, making it a cleaner and safer option for workers and the planet.
Efficiency That Translates to Savings
Friction welding's speed and automation-friendly nature make it a highly efficient process. It can significantly boost production rates while maintaining consistent, high-quality results. This efficiency not only saves time but also reduces labor costs, translating to financial savings for manufacturers and faster delivery times for consumers.
Simplified Welding Preparation and Finishing
The process simplifies the entire welding operation. Unlike traditional methods that require extensive surface cleaning and post-weld treatments, friction welding needs minimal preparation and often no additional treatments after welding. This streamlining reduces production times and costs, making the manufacturing process more straightforward and cost-effective.
Keeping Shapes Intact
Because friction welding doesn't melt the materials, it avoids the thermal distortion commonly associated with traditional welding. This means that the components maintain their original shape and dimensions more accurately, reducing or even eliminating the need for further machining or finishing, saving both time and resources.
Enhanced Workplace Safety
Friction welding is inherently safer than traditional methods. It does away with the hazards of open flames, extreme heat, and gas handling. This not only creates a safer environment for workers but also minimizes the risk of accidents, promoting a healthier and more secure workplace.
In essence, friction welding is a game-changing technique that offers stronger joints, material flexibility, environmental benefits, cost savings, and improved safety. It's a method that not only meets the current demands of manufacturing but also sets a new standard for the future of industrial joining processes.
5. Navigating the Hurdles of Friction Welding
Friction welding has been a game-changer in joining materials, but it's not a perfect solution. It's important to recognize the hurdles that come with this innovative technique to ensure its effective use and to drive advancements in the field.
The cost of setting up can be steep. The specialized machinery required for processes like friction stir welding comes with a hefty price tag, which can be a significant obstacle for smaller businesses with tight budgets.
When it comes to the materials themselves, not all are created equal in the eyes of friction welding. Metals that share similar properties tend to join together more easily. Trying to weld together materials that are very different can lead to a weaker bond, which limits the technique's use in projects that require a mix of materials.
The skill required to operate friction welding equipment shouldn't be underestimated. Even though machines do most of the work, a human touch is needed to oversee the process. Operators must be well-trained to handle the sophisticated setup and to troubleshoot any issues that arise, which can be a challenge in finding the right talent.
The size and shape of the parts being joined also play a role in whether friction welding is suitable. Some processes are designed for specific part geometries, so large or oddly shaped items might not be compatible, limiting the technique's application.
Managing the intense heat produced during welding is crucial for a successful join. If the heat isn't controlled properly, it can create imperfections like voids or unwanted material called flash around the weld, weakening the joint.
And while friction welding is fast and efficient, it's not always the quickest option, especially for high-volume production needs. In some cases, traditional welding methods can churn out more units in less time, which can influence a manufacturer's choice of technique.
Despite these challenges, the future is bright for friction welding. Continuous research and development are leading to better equipment designs, improved control over the welding process, and advancements in materials science. These innovations are helping to overcome current limitations and are expanding the potential of friction welding in manufacturing, making it an even more valuable tool in the industry's arsenal.
6. The Evolution and Future Prospects of Friction Welding
Friction welding is on the cusp of a transformative era, with its already established reputation for producing robust and superior quality joints set to reach new heights through innovation and technological progress. The following insights offer a glimpse into what the future holds for this dynamic welding technique.
Embracing Cutting-Edge Technology
The future of friction welding is intertwined with technological advancements. The integration of sophisticated computer systems is expected to refine the precision of welding operations, minimizing inconsistencies. Automation is set to become a cornerstone, streamlining production and curtailing human error. Additionally, the advent of novel materials and composites promises to broaden the scope of friction welding, enabling the fusion of materials once deemed incompatible.
Broadening Horizons Across Industries
Although friction welding hasn't reached the ubiquity of traditional welding methods, its adoption is accelerating. Industries are recognizing its advantages and are increasingly incorporating it into their manufacturing processes. This trend is particularly noticeable in sectors that prioritize strong, lightweight structures, such as renewable energy. For instance, friction welding is becoming a method of choice for joining diverse metals in the construction of wind turbines and solar panel frameworks.
Championing Environmental Sustainability
In an era where sustainable manufacturing practices are paramount, friction welding stands out for its eco-friendly attributes. It is generally more energy-efficient than conventional welding, doesn't generate waste from filler materials, and avoids the emission of hazardous fumes. As businesses strive to reduce their ecological footprint, friction welding is poised to become a favored technique, contributing to the industry's overall efforts to minimize environmental impact.
Tailoring Solutions Through Innovation
The inherent flexibility of friction welding lends itself to customization, paving the way for bespoke machines and processes tailored to specific industrial requirements. The future may see the development of portable friction welding tools for convenient on-site repairs or the incorporation of robotics to execute intricate welds in demanding conditions.
Investing in Education and Skill Development
Advancements in friction welding necessitate a workforce skilled in its latest techniques. We anticipate a surge in specialized educational programs and certifications aimed at equipping welders with the knowledge required to navigate the evolving landscape of high-tech manufacturing.
Fostering Collaborative Breakthroughs
The continued evolution of friction welding will rely heavily on collaborative efforts among industry experts, academic scholars, and research institutions. Such partnerships are expected to drive innovation in material science and welding technology, ensuring that friction welding remains a leading method for material joining.
In essence, the trajectory of friction welding is marked by promising advancements that are set to enhance its effectiveness, expand its applications, and uphold its status as an environmentally conscious choice. As the industry embraces and refines this technique, friction welding is destined to play a crucial role in shaping the future of manufacturing.
7. Sealing the Deal: The Lasting Impact of Friction Welding
As we wrap up our exploration of friction welding, it's clear that this innovative method is more than just a way to fuse materials—it's a catalyst for change in the manufacturing world. By enabling the union of diverse materials with unmatched strength, friction welding has carved out new avenues for creativity and efficiency in industries far and wide. From the exacting standards of aerospace engineering to the high-volume production lines of the automotive world, this technique has become indispensable.
Friction welding's various forms, including rotational, linear, and stir welding, showcase its adaptability to different tasks and materials. Each technique is tailored to specific applications, ensuring that manufacturers can achieve the best possible results for their unique needs.
The advantages of friction welding are numerous and significant. It delivers joints of superior quality, streamlines production, and offers a greener alternative to conventional welding methods. These benefits make a strong case for companies looking to enhance their operations and reduce their environmental footprint.
Challenges do exist, but they are being met with ongoing research and technological breakthroughs that promise to refine and expand the applications of friction welding. As the industry continues to innovate, we can expect this method to become even more precise, efficient, and cost-effective.
Friction welding is not merely a joining process; it's a stepping stone to a future of stronger, more reliable products. It's a testament to the progress and growth that can be achieved when industries embrace new technologies and strive for excellence in their craft.
Sharing is Caring
Feedback
At WeldWins, we know we aren't perfect which is why we're always looking for ways to improve. You can help us do better by taking 2 minutes to fill out our simple feedback form.
Any and all feedback is welcome. It could be a complaint, an idea, or even just a comment, we'll always be grateful to hear what you think.