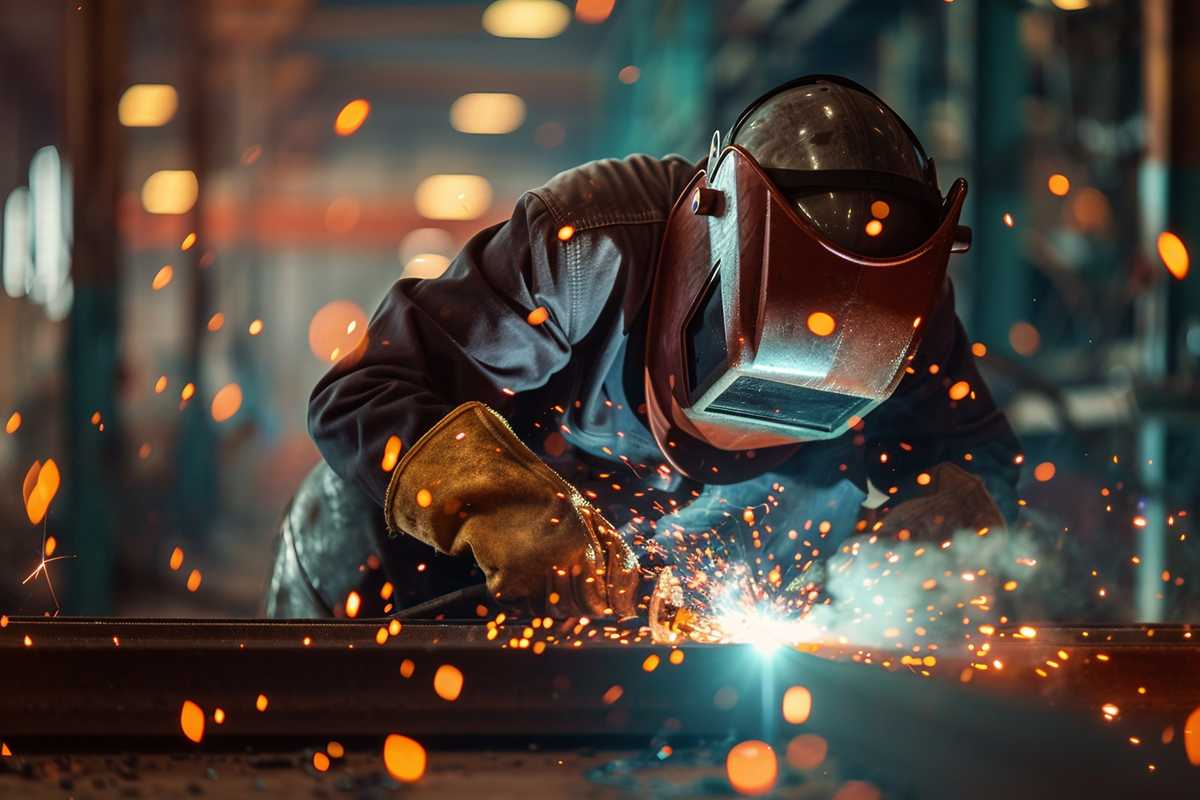
The art of welding, essential in building the structures and machines around us, involves more than just the visible sparks and intense heat—it also brings workers into contact with electromagnetic fields, or EMFs. These invisible forces are a natural part of using electrical equipment, but they come with potential health risks that are often overlooked. As we strive for safer workplaces, it's crucial to understand the impact of EMFs and take steps to protect those who work with welding tools daily.
EMFs are everywhere electricity flows, and welding is no exception. The type of EMFs associated with welding falls into the non-ionizing category, which means they don't have enough energy to remove electrons from atoms, unlike their ionizing counterparts such as X-rays. However, this doesn't mean they're harmless. Research points to a range of health effects from EMF exposure, from temporary discomfort to more severe issues like the possibility of increased cancer risk.
The responsibility to safeguard welders from EMF exposure is not just about following regulations—it's a moral imperative. This article will guide you through the invisible hazards of EMFs in the welding world, offering insights and practical measures to ensure the health and safety of welding professionals. Let's dive into the science of EMFs, the risks involved, and the strategies to mitigate them, ensuring a safer future for those in the welding industry.
1. Demystifying Electromagnetic Fields in Welding
Welding, a process integral to constructing the world around us, is not just about the visible spectacle of sparks and heat. It also involves exposure to electromagnetic fields (EMFs), which are less visible but equally important to understand for the safety of welding professionals.
EMFs are energy zones created by electrical currents, which are a natural byproduct of welding due to the high currents needed to fuse materials. These fields are invisible to the naked eye and are often overlooked, yet they can have health implications for welders. Short-term exposure might cause sensations like tingling or muscle twitches, while long-term exposure has been linked to more serious conditions, including chronic fatigue and possibly an increased risk of cancer.
It's essential to distinguish between the two types of EMFs: ionizing and non-ionizing. Ionizing EMFs, such as X-rays, are high-energy and can disrupt atoms, potentially causing damage to living tissue. Non-ionizing EMFs, which are emitted by welding equipment, don't carry enough energy to ionize atoms but can still pose health risks that warrant careful management.
The intensity of EMFs in a welding environment can vary based on factors like the welding technique, the current used, and how close the welder is to the equipment. For example, MIG (Metal Inert Gas) and TIG (Tungsten Inert Gas) welding produce different EMF levels. Even the layout of the welding setup and the positioning of cables can affect EMF strength and distribution.
To foster a safer workplace, it's crucial for welders to understand the sources of EMF exposure and the potential risks involved. This knowledge empowers them to take proactive steps to minimize exposure, such as reconfiguring the workspace to keep a safe distance from high-EMF zones or selecting welding methods that generate lower EMFs. Awareness and informed action are key to aligning with safety standards and developing best practices in the welding field.
2. Navigating EMF Safety Standards in Welding
Navigating the complex landscape of EMF safety standards is a critical responsibility for those in the welding industry. These standards are the safeguards that protect welders from the invisible dangers of electromagnetic fields. While the specifics can differ dramatically across borders and sectors, the goal remains the same: to minimize health risks for those on the welding front lines.
In the U.S., the absence of concrete EMF regulations from OSHA means that employers often look to the guidance of authoritative bodies like NIOSH and IEEE. These organizations offer research-backed recommendations that help businesses craft their own EMF safety protocols. For example, they might suggest rearranging workstations to keep welders further from EMF sources or using welding techniques that produce lower EMF levels.
Globally, the ICNIRP provides more explicit guidelines that many countries adopt, creating a more uniform standard for EMF exposure. These guidelines are instrumental in setting safety benchmarks and are regularly updated to reflect the latest scientific understanding of EMF risks.
Despite these frameworks, there's a consensus that existing regulations may not be all-encompassing, given the ongoing evolution of EMF research. As new health risk data emerges, it's anticipated that safety standards will be refined to incorporate these insights.
A significant hurdle in this realm is the practical application of these standards. Many welding operations lack the means to measure EMF levels accurately, which hampers compliance efforts. This highlights an urgent need for more user-friendly measurement tools and comprehensive training programs that empower both welders and employers to monitor and manage EMF exposure effectively.
In summary, while there are EMF safety regulations designed to protect welders, there's a clear need for enhancement in both the regulations themselves and the methods of enforcement. Staying abreast of the latest safety standards and adopting industry best practices is crucial for maintaining a safe welding environment.
3. Essential Strategies for Welder Safety Against EMF Risks
Welders are often in the line of fire when it comes to electromagnetic fields (EMFs), but there are effective strategies to minimize these invisible dangers. Let's explore specific, actionable steps that welders can take to protect themselves from the potential health hazards of EMF exposure.
Analyze and Adapt Your Work Environment
The layout of a welding workspace can significantly influence EMF exposure. Welders should conduct a thorough assessment to pinpoint high-EMF zones, which are typically closest to the welding equipment. Once identified, these areas can be avoided or workstations can be rearranged to increase distance from EMF sources, thereby reducing exposure time.
Choose Welding Equipment Wisely
Technological advancements have blessed the welding industry with machines that emit lower EMFs. Welders should prioritize the use of these newer models, which are engineered to keep EMF emissions at bay without sacrificing efficiency. Investing in such technology is not only a smart choice for immediate safety but also benefits long-term health.
Adopt EMF-Smart Working Techniques
Simple changes in work habits can have a profound impact on EMF exposure. For instance, welders should maintain a safe distance from the equipment when it operates at high currents, as the strength of the EMF correlates with the current level. It's also advisable to avoid standing between the welding unit and the workpiece to prevent increased exposure.
Utilize Protective Gear Effectively
While personal protective equipment (PPE) cannot block EMFs, it can mitigate associated risks. Wearing gloves and protective clothing shields against burns and UV exposure, which are common in welding. Additionally, using PPE correctly can help defend against other workplace hazards that may exacerbate the effects of EMFs.
Maintain Equipment to Reduce EMF Emissions
Regularly servicing welding equipment is a critical step in controlling EMF exposure. Worn-out or malfunctioning machines can emit higher levels of EMFs, so ensuring that all tools are in prime condition is essential for keeping emissions low.
Educate and Empower Through Training
Knowledge is power, and this holds true for EMF safety. Welders must be well-informed about EMF risks and the best practices for minimizing exposure. Employers play a crucial role by providing comprehensive training sessions and up-to-date safety information, enabling welders to work smartly and safely in EMF-prone environments.
By implementing these targeted strategies, welders can significantly cut down their EMF exposure and maintain a healthier work life. It's about making informed, practical changes that yield a safer welding environment for everyone involved.
4. Embracing a Safer Future for Welders Amidst EMF Concerns
In the intricate dance of metal and flame that is welding, we've seen how the invisible presence of electromagnetic fields (EMFs) poses a silent challenge to the health and safety of those who weld. It's evident that a deeper awareness and proactive management of EMF exposure are essential for the modern welder.
The potential health impacts of EMFs, ranging from short-term discomfort to more serious long-term effects, cannot be ignored. The welding community, including both workers and employers, must stay vigilant and informed about the latest scientific findings on EMFs to effectively mitigate these risks.
Adopting safer practices isn't just about ticking boxes for compliance; it's a commitment to the health and longevity of the workforce. Welders can take charge of their safety by following the strategies we've outlined, such as choosing low-EMF emitting equipment, reconfiguring workspaces, and staying educated on EMF safety protocols.
As technology progresses, it's crucial that our safety measures keep pace. The welding industry has a responsibility to invest in the health of its technicians by providing the necessary protective gear, offering ongoing training, and ensuring work environments are as safe as possible.
Let's pledge to a future where the safety of welding technicians is not just an afterthought but a priority. By doing so, we can ensure that the critical role welders play in building and maintaining our infrastructure is carried out in a way that is both productive and protective in this era of technological advancement.
Sharing is Caring
Feedback
At WeldWins, we know we aren't perfect which is why we're always looking for ways to improve. You can help us do better by taking 2 minutes to fill out our simple feedback form.
Any and all feedback is welcome. It could be a complaint, an idea, or even just a comment, we'll always be grateful to hear what you think.