How Does Electroplating Combine Art and Science to Transform Materials?
June 23, 2024
11 min read
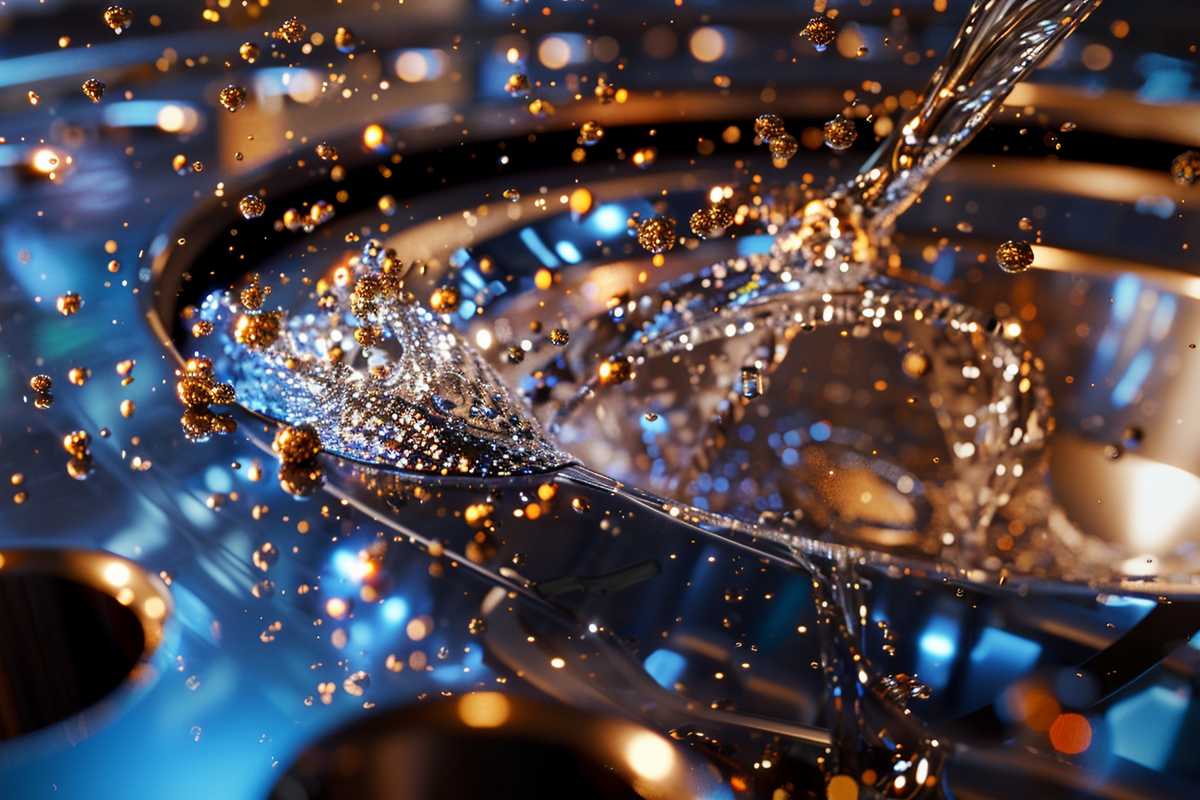
Imagine turning ordinary metals into objects of beauty and strength—this is the essence of electroplating. A blend of historical techniques and modern science, electroplating is the art of coating objects with a fine metal layer through the power of electricity. This process, which began in the 1800s, has become a cornerstone in enhancing the quality and longevity of materials across various industries.
Electroplating is not just about aesthetics, though it certainly adds a shimmering allure to items like jewelry and home decor. More importantly, it plays a pivotal role in protecting and improving the functionality of objects. By electroplating, we can make materials more resistant to corrosion, wear, and tear, reduce friction, and boost electrical conductivity. These enhancements are vital for the reliability and efficiency of everything from heavy machinery to the delicate circuits in our smartphones.
Join us on a journey through the transformative world of electroplating. Discover how this process doesn't just decorate—it reinforces materials to withstand the test of time and usage. From the radiant finish on classic automobiles to the critical gold plating in electronic components, electroplating is an indispensable technique that marries the decorative with the practical. Let's dive into the fascinating interplay of ions and metals that revolutionizes our daily-use materials.
1. Demystifying the Electroplating Technique
Electroplating is a remarkable technique that artfully combines chemistry and electricity to alter the surface characteristics of various materials. Essentially, it involves the application of a metal layer onto an object to enhance its appearance, durability, and functionality. Let's break down this process to understand how it transforms ordinary objects into resilient and attractive items.
The Fundamentals of Electroplating
At the heart of electroplating lies a scientific process driven by electric currents and chemical reactions. The object intended for plating becomes the cathode, or negative electrode, attracting positively charged metal ions from the surrounding solution. The anode, or positive electrode, is usually composed of the metal destined for coating the object. When electricity flows through this setup, it prompts the metal ions to move from the anode, through the solution, and onto the cathode, creating a smooth, adherent metal layer.
The electrolyte solution is pivotal in this process. It's a specially formulated conductive liquid containing metal ions that facilitates the flow of electricity and the transfer of metal onto the object. The solution's makeup, along with controlled variables like temperature and electrical voltage, are meticulously adjusted to ensure a uniform and quality coating.
The Electroplating Procedure: A Stepwise Approach
Electroplating can be distilled into a series of precise steps:
-
Surface Preparation: The target object is rigorously cleaned to strip away any contaminants, oils, or rust. This typically involves chemical baths that may include degreasing, rinsing, and etching to prepare a pristine surface for plating.
-
Configuration: The clean object is submerged in the electrolyte solution and connected to the power supply's negative terminal, establishing it as the cathode. The anode, composed of the plating metal, is linked to the positive terminal.
-
The Plating Process: Turning on the power initiates the migration of metal ions towards the cathode, where they bond and form a metal coating. The plating's thickness is regulated by the amount of time the object spends in the solution and the intensity of the electric current.
-
Completion: Once the coating reaches the desired thickness, the object is extracted from the solution, rinsed, and dried. It may then undergo additional treatments like polishing or the application of a protective layer to further enhance its appearance and resilience.
Safety is a top priority in electroplating due to the use of potentially dangerous chemicals. Proper handling, protective gear, and adherence to environmental regulations are essential to mitigate risks. Waste materials from the process must be managed responsibly to prevent environmental harm, and the industry is increasingly turning to more eco-friendly materials and practices.
Through a clear understanding of the electroplating process, we gain insight into the intricate blend of artistry and science that goes into improving the materials that are integral to our daily lives. Electroplating is a vital method in the fields of material science and manufacturing, offering both aesthetic and functional benefits to a wide range of products.
2. Exploring the Spectrum of Electroplating Metals and Their Applications
Electroplating is a transformative process that enhances the properties of materials for diverse applications across various industries. By coating objects with specific metals, we can tailor their characteristics to serve unique purposes. Below, we explore the most prevalent metals used in electroplating and their practical applications, illustrating how this process is integral to innovation and efficiency in manufacturing.
Key Metals in Electroplating
Gold Plating is prized for its exceptional electrical conductivity and resistance to tarnishing. It's a staple in the electronics industry, where it's used to coat connectors and circuit boards, ensuring devices operate smoothly.
Silver Plating is another excellent conductor, often chosen for its cost-effectiveness compared to gold. It's widely used in electrical systems where heat dissipation is key, such as in radiators and heat exchangers.
Copper Plating is notable for its high electrical conductivity and is frequently used as a base layer to improve metal adhesion in subsequent plating steps. It's a common sight in automotive parts and electronic devices.
Nickel Plating is synonymous with durability and wear resistance, making it perfect for hard-wearing components like gears and valves. Its shiny finish also makes it popular for decorative purposes.
Chrome Plating is known for its hard and glossy surface, which is why you'll find it on car parts like bumpers and rims, as well as on household fixtures and tools that benefit from its aesthetic and protective qualities.
Zinc Plating acts as a safeguard against rust for steel parts, offering an economical rust-proofing solution for items such as screws and brackets in construction and automotive applications.
Electroplating's Innovative Roles
Electroplating's role extends into innovative territories, showcasing its versatility:
In aerospace, it's crucial for crafting lightweight yet robust components that can endure extreme conditions.
In the automotive industry, beyond just adding a shiny touch, electroplating is essential for enhancing the durability and performance of engine components.
Artists have adopted electroplating to give their creations a metallic sheen, adding both value and longevity to their work.
In the realm of medical devices, electroplating is employed to coat surgical instruments with precious metals, ensuring they are non-reactive and safe for medical procedures.
The consumer electronics sector utilizes electroplating to boost the electrical performance of gadgets while also providing an attractive metallic finish.
Electroplating is more than just a metallic cover—it's a strategic enhancement of an object's functionality and aesthetics. As the technology progresses, it continues to redefine material capabilities, playing a pivotal role in the advancement of everyday items and cutting-edge technologies.
3. Harnessing the Power of Electroplating in Advanced Manufacturing
The integration of electroplating with contemporary manufacturing methods marks a significant leap in material science, leading to products that are not only more durable and functional but also aesthetically superior. This section explores how the synergy between these two processes is revolutionizing the production of goods.
Enhancing 3D Printed Objects with Metal Finishes
The marriage of 3D printing and electroplating is one of the most innovative advancements in manufacturing. 3D printing allows for the creation of complex shapes by building up layers from a digital blueprint. When these intricate designs are electroplated, they gain a metal coating that can enhance their electrical properties, protect against corrosion, or add a touch of elegance with a shiny finish.
Take, for example, a 3D-printed drone part. By electroplating it with copper, its electrical pathways become more conductive, which is crucial for efficient operation. In the world of consumer electronics, a 3D-printed phone case electroplated with gold can provide a luxurious look while also improving signal transmission.
The aerospace industry benefits greatly from this combination. Electroplating 3D-printed satellite components with a thin metal layer can significantly increase their strength and resistance to the extreme conditions of space. This not only prolongs the life of these parts but also contributes to lighter spacecraft, which can lead to substantial fuel savings.
Pioneering New Composite Materials
The future holds great promise for the development of new materials through the fusion of electroplating and modern manufacturing. Researchers are experimenting with different base materials and plating metals to create composites with unprecedented properties. These new materials are set to redefine what we expect from products in terms of weight, strength, and versatility.
Imagine a world where the materials used in building a car or a surgical implant are selected not just for their strength but also for their ability to integrate with other materials, resulting in lighter, more durable, and adaptable products. The potential for innovation is limitless, with the power to transform industries such as healthcare, automotive, and beyond.
Electroplating is no longer just about adding a metallic layer; it's about enhancing the core properties of materials. By combining precise manufacturing techniques with the transformative capabilities of electroplating, we are on the brink of ushering in a new era of materials that promise to make our future more efficient, sustainable, and visually appealing.
4. Navigating the Complexities of Electroplating
Electroplating is a process that brings numerous benefits to materials, but it also comes with its fair share of challenges. These range from environmental issues to technical difficulties that can affect the final product's quality. However, the industry is continually finding innovative solutions to overcome these obstacles.
Addressing Environmental and Health Risks
The use of toxic chemicals in electroplating, such as heavy metals and cyanide, poses significant environmental and health risks. These chemicals can lead to water and soil pollution and are dangerous for workers handling them. To combat these issues, the industry is shifting towards less harmful substances and implementing rigorous waste management practices. For instance, new filtration technologies are being used to treat and dispose of waste safely, reducing the risk of contamination.
Worker safety is also a top priority. Facilities are now equipped with better ventilation systems to reduce the inhalation of harmful fumes, and employees are provided with comprehensive training and personal protective equipment (PPE) to minimize exposure to hazardous materials.
Tackling Technical Challenges
Achieving a consistent coating thickness, plating complex shapes, and ensuring strong adhesion to various materials are some of the technical hurdles in electroplating. To address these, the industry is turning to advanced techniques and technologies. Pulse plating, for example, has emerged as a method to improve control over the metal deposition process, resulting in more even coatings. Automation and computer modeling have also enhanced the precision of plating, particularly for items with intricate designs.
The introduction of new additives to electroplating baths is another breakthrough. These additives help improve the finish and quality of the coating, ensuring a more reliable and durable end product.
In summary, while electroplating presents certain challenges, the industry's commitment to innovation and safety is leading to effective solutions. These advancements not only enhance the quality of electroplated items but also ensure the process's sustainability and safety for the environment and workers.
5. Reflecting on Electroplating's Journey and Future
As we conclude our exploration of electroplating, it's clear that this process is a remarkable fusion of art and science. Electroplating has been a key player in manufacturing for over a century, consistently enhancing the strength, conductivity, and beauty of various materials. It's a technique that has made its mark on everything from delicate electronic parts to robust aerospace components, proving its value across numerous industries.
The evolution of electroplating has been marked by continuous improvement and innovation. It has adapted to the times, embracing new technologies such as 3D printing to create composite materials with enhanced properties. These advancements are not just theoretical—they're practical, leading to real-world applications that push the boundaries of what we thought possible.
However, the journey of electroplating isn't without its challenges. Environmental concerns and the safety of workers are issues that the industry takes seriously. Ongoing research and the implementation of best practices are driving the development of safer, more sustainable electroplating methods. These efforts are crucial as we strive to balance progress with responsibility.
Looking ahead, the potential for electroplating to contribute to material science and manufacturing is immense. It's an exciting time for those in the field, as they collaborate to refine and innovate the materials that shape our world. Electroplating is more than just a process—it's a catalyst for change, enhancing not only the objects we use but also the future we envision.
Sharing is Caring
Feedback
At WeldWins, we know we aren't perfect which is why we're always looking for ways to improve. You can help us do better by taking 2 minutes to fill out our simple feedback form.
Any and all feedback is welcome. It could be a complaint, an idea, or even just a comment, we'll always be grateful to hear what you think.