What is the Best Way to Weld Copper for Lasting Results?
April 28, 2024
14 min read
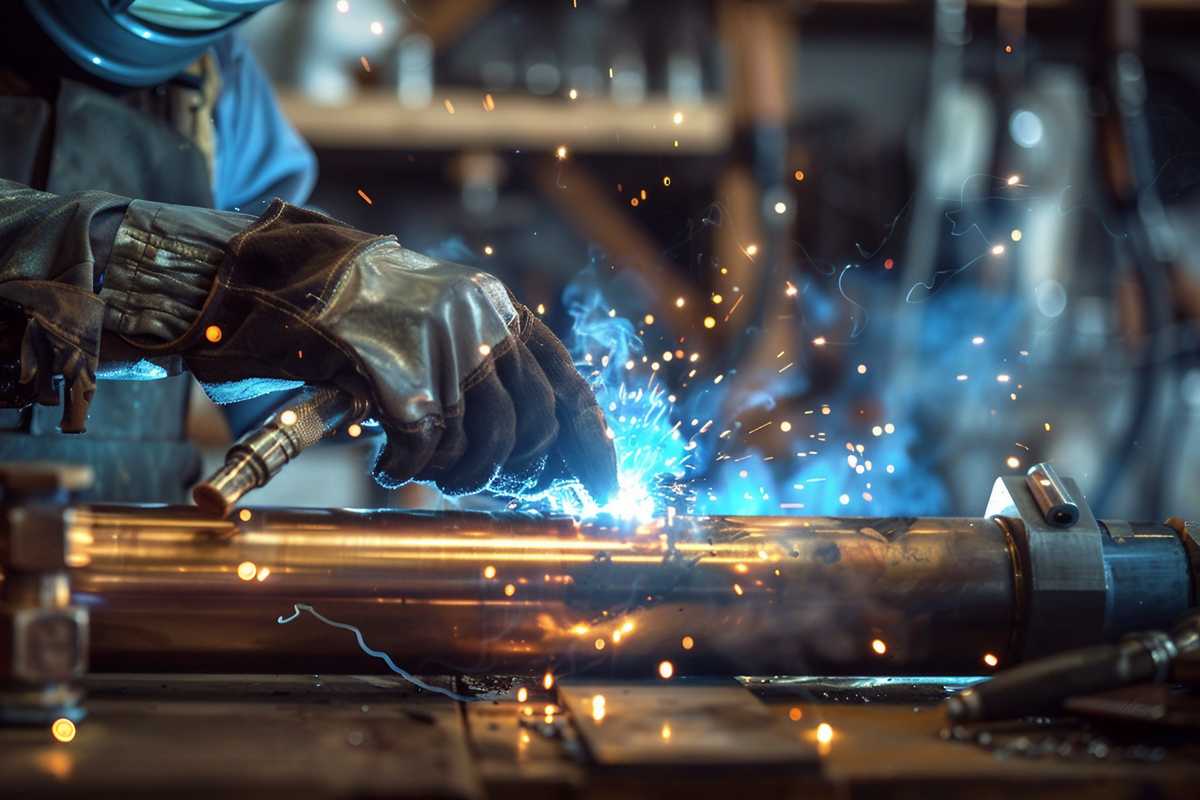
1. Introduction
Welcome to the world of copper welding, a skill that's as challenging as it is rewarding. Copper's widespread use in industries such as plumbing, electronics, and even art makes it a valuable material to master. Its excellent ability to conduct heat and electricity is a boon for many applications, but it also adds a layer of complexity to the welding process.
This guide is crafted to take you through the nuances of welding this reddish-gold metal. We'll share essential techniques, tips, and insights to elevate your welding projects. Whether you're piecing together heavy-duty pipes or assembling delicate electronic parts, understanding how to navigate copper's unique properties will set your work apart. Let's dive into the world of copper welding, where we'll equip you with the knowledge to produce strong, lasting welds and open up a realm of possibilities in your professional endeavors.
2. Navigating Copper's Welding Complexities
Copper, a metal revered for its electrical and thermal conductivity, is indispensable across various sectors like electronics and construction. Yet, these same prized properties pose significant hurdles in welding, demanding a nuanced understanding from welders to ensure robust and reliable joins.
The high thermal conductivity of copper means it loses heat swiftly when welded, complicating the maintenance of the necessary temperatures for a solid weld. To counteract this, welders may need to increase the amperage, a careful balancing act to avoid overheating or insufficient penetration.
Electrical conductivity introduces another layer of complexity, potentially leading to erratic arcs. A stable arc is vital for a consistent weld, so adjustments in welding parameters or the use of advanced equipment may be required to manage this issue.
Copper's propensity to warp under heat is another challenge, especially where precision is key. Techniques like securing the copper with jigs or fixtures, or strategically planning the welding sequence to distribute heat evenly, are strategies to prevent distortion.
Surface oxides, which can inhibit the fusion of copper to the filler material, must be meticulously cleaned to ensure a strong bond. This preparation step is non-negotiable for a successful weld.
In essence, the intricacies of welding copper—from managing its rapid heat transfer to ensuring arc stability and addressing potential warping—require a deep dive into specialized techniques and careful preparation. By mastering these aspects, welders can produce superior welds that harness copper's benefits without falling prey to its challenges.
3. Essential Steps for Copper Weld Preparation
To achieve a flawless weld with copper, meticulous preparation is key. Copper's excellent thermal and electrical conductivity, while beneficial in many applications, can present challenges during welding. To mitigate these issues and ensure a robust weld, follow these essential preparation steps:
Thoroughly Clean the Copper Surface
Start by rigorously cleaning the copper to remove any impurities that could compromise the weld. Use a clean cloth to wipe away loose dirt and debris. For more persistent grime, such as grease or oil, apply a solvent or a diluted vinegar solution, then rinse the copper with water. Remember to wear gloves to prevent transferring skin oils onto the metal.
Eliminate Oxidation with Care
Copper tends to oxidize and develop a copper oxide layer when exposed to air, which hinders the welding process. To remove this layer, gently scrub the copper with a wire brush or sandpaper, taking care to move along the metal's grain to avoid scratches. If the oxidation is substantial, consider using a specialized chemical remover designed for copper.
Preheat the Copper Evenly
Due to copper's ability to quickly spread heat, preheating can help maintain consistent temperatures during welding, reducing the risk of warping. Use a torch or furnace to evenly preheat the copper. The required temperature can vary, but generally, aim for a range of 200°F to 400°F. Use a temperature-indicating device like a temp stick or infrared thermometer to monitor and maintain the correct preheat level.
By diligently cleaning, deoxidizing, and preheating your copper, you set the stage for a successful welding process. These steps are crucial in overcoming the common challenges associated with copper welding, leading to a durable and aesthetically pleasing result. With the copper now properly prepared, you can confidently move on to the actual welding, knowing you've laid the groundwork for a high-quality finish.
4. Mastering Copper Welding: Key Techniques and Their Applications
Welding copper presents unique challenges due to its high thermal and electrical conductivity. To achieve durable and precise welds, it's essential to understand and apply the right welding techniques. In this section, we'll focus on three primary methods: TIG, MIG, and Stick welding, each with its own advantages for specific copper welding tasks.
Precision and Aesthetics with TIG Welding
TIG (Tungsten Inert Gas) welding, also known as GTAW (Gas Tungsten Arc Welding), is the go-to method for projects that demand precision and a polished finish. This technique uses a non-consumable tungsten electrode to create the weld, while a separate filler metal is manually added to the weld pool. TIG welding shines when working with copper because it allows for meticulous heat control, which is vital to prevent warping. It's particularly well-suited for delicate or detailed copper work, producing strong, clean welds with little to no spatter.
Efficiency and Strength with MIG Welding
MIG (Metal Inert Gas) welding, or GMAW (Gas Metal Arc Welding), is favored for its efficiency, especially on thicker copper sections that require substantial filler material. With MIG welding, a wire electrode is continuously fed through the welding gun, accompanied by a shielding gas to protect against contamination. This method is quicker than TIG welding, making it ideal for extensive projects or long, uninterrupted welds. However, it's worth noting that MIG may not offer the same level of detail as TIG and can be more challenging to manage in terms of heat input.
Versatility and Accessibility with Stick Welding
Stick welding, or SMAW (Shielded Metal Arc Welding), is a traditional approach that's particularly useful in outdoor settings or when access to advanced welding equipment is limited. It employs a consumable electrode coated with flux to create the weld. While it's not the first choice for copper due to its lower precision and higher likelihood of warping, stick welding can be effective for robust repairs or working with thick copper that can tolerate more heat.
Each welding technique has its rightful place in copper welding, and the best choice depends on the project's specific needs, such as copper thickness, desired finish, and equipment availability. To master these methods, practice is key, along with a deep understanding of copper's behavior under heat to ensure strong, lasting welds.
5. Optimizing Weld Quality: Filler Metals and Shielding Gases
The materials you choose for welding copper are pivotal in determining the strength and quality of your welds. It's essential to select the right filler metals and shielding gases to ensure a robust and enduring weld.
Matching Filler Metals to Copper Alloys
The key to selecting the right filler metal is to match it with the base metal's properties. For welding pure copper, opt for a copper alloy filler like silicon bronze or aluminum bronze, which melds well and provides a strong joint. If you're working with copper alloys such as brass or bronze, choose a filler that corresponds to the specific alloy. For instance, naval brass filler is ideal for welding brass. Always check with the manufacturer's recommendations or industry standards to pick the best filler for your project.
The Role of Shielding Gases in Copper Welding
Shielding gases are crucial as they prevent contamination of the weld pool by atmospheric gases. Argon and helium are the most common choices for copper welding. Argon is preferred for its arc stability and ability to minimize oxidation, while helium is used for its deep penetration capabilities, especially useful for thicker copper pieces. Combining argon and helium can give you the benefits of both gases, and the ratio can be adjusted depending on the copper's thickness and the welding requirements.
Fine-Tuning Gas Flow Rates
The flow rate of your shielding gas can make or break a weld. Too little flow may leave the weld pool unprotected, while too much can cause turbulence and contamination. The ideal flow rate generally falls between 20-30 cubic feet per hour (CFH), but this can vary based on the welding technique, torch size, and the environment. Adjust as necessary to maintain the perfect balance for your specific welding situation.
Ensuring Welding Success with Proper Material Choices
In conclusion, the careful selection of filler metals and shielding gases is a critical step in copper welding. By aligning the filler metal with the copper alloy and fine-tuning your shielding gas mix and flow rate, you'll be well on your way to creating clean, high-quality welds. Always refer to professional guidelines and manufacturer instructions to make the best choices for your welding projects.
6. Ensuring the Longevity of Your Copper Welds
Once you've completed the welding of copper, it's imperative to engage in certain post-welding practices to guarantee the durability and quality of your work. Copper, with its distinctive characteristics, demands careful handling after the welding torch has been laid down.
Controlled Cooling for Copper Stability
Due to copper's excellent thermal conductivity, it loses heat rapidly, which can cause the weld to cool too quickly, introducing stress and the potential for cracks. To counteract this, it's important to regulate the cooling rate. You can do this by draping an insulating blanket over the weld immediately after you finish. This simple step slows the cooling rate, reducing the risk of stress fractures.
Alternatively, you can let the piece cool naturally in a draft-free environment. This gradual cooling is crucial for the weld's integrity. Remember, plunging your copper into water or other liquids for quick cooling is a no-go—it can shock the metal, leading to cracks or other damage.
Post-Weld Cleaning for a Pristine Finish
After welding, copper often bears the marks of the process—oxidation and flux residue. To bring back its shine and ensure a top-notch finish, a thorough cleaning is necessary. Start with a copper-specific wire brush to gently scrub away surface impurities. For stubborn areas, a chemical cleaner designed for copper can be used, but always adhere to the manufacturer's guidelines to avoid harming the metal.
Once you've brushed and cleaned the weld area, a soft cloth can be used to wipe away any leftover particles or cleaning solution. If the copper's appearance is critical for its end use, you might need to polish the piece to achieve the desired sheen.
Weld Inspection for Quality Assurance
After the weld has cooled and is clean, it's time for a detailed inspection. Examine the weld for any signs of cracks, holes (porosity), or areas where the weld didn't fully fuse. If you spot any imperfections, you may need to re-weld or take other corrective actions to ensure the weld is up to standard.
Proper Storage to Preserve Weld Integrity
How you store and handle the copper post-welding can affect its condition. Copper tends to tarnish when exposed to air, so keeping it in a dry, clean place will help maintain its appearance. If the copper is part of a larger structure, ensure it's properly supported to prevent any stress that could weaken the weld.
By diligently following these post-welding steps, you can be confident that your copper welds will not only look good but will also be structurally sound for their intended use.
7. Prioritizing Safety in Copper Welding
Welding copper requires a keen focus on safety to prevent accidents and health hazards. The intense heat, light, and fumes associated with welding can pose serious risks without the right precautions. Below are vital safety measures every welder should implement:
Essential Protective Gear
Don't start welding without donning the necessary safety equipment. A welding helmet with an appropriate lens shade is crucial to shield your eyes from harmful rays. Heavy-duty gloves will protect your hands from burns, while a flame-resistant jacket and long pants safeguard your skin. High-top leather boots and an apron offer additional defense against sparks and hot metal.
Ensuring Clean Air with Proper Ventilation
Welding copper can release dangerous fumes. To keep the air safe, work in a well-ventilated space. Indoor welders should use a fume extractor to actively remove harmful gases. While fans can help circulate air, they shouldn't be the only source of ventilation.
Fire Prevention Tactics
Sparks from welding can quickly ignite fires, so it's essential to maintain a clean workspace, free from flammable materials. Always have a fire extinguisher within reach, and familiarize yourself with its operation. For added safety, keep a fire blanket nearby to smother unexpected flames.
Electrical Hazard Mitigation
Copper's excellent conductivity increases the risk of electric shock. Before you begin, inspect all welding equipment for any signs of wear or damage. Stand on a dry, non-conductive surface during welding, and avoid touching any metal parts of the electrode holder with your skin or wet clothing.
Comprehensive Training and Knowledge
Proper understanding of copper welding techniques and equipment is the foundation of safety. Read the manuals for your tools, and stay informed about the risks specific to your welding method. If you're new to the craft, seek out professional training to build your skills safely.
By integrating these safety practices into your routine, you'll establish a secure environment that supports your development as a proficient copper welder. Safety is a continuous mindset, not just a checklist—remain alert and well-protected to ensure a successful and injury-free welding experience.
8. Crafting Excellence: The Final Touches in Copper Welding Mastery
In wrapping up our comprehensive guide to copper welding, we've journeyed through the intricacies of working with this versatile metal. From the initial steps of understanding copper's unique properties to the detailed exploration of welding techniques, we've equipped you with the tools to excel in your welding projects.
The art of copper welding is nuanced, requiring a blend of precision and adaptability. We've underscored the necessity of preparing the metal surface with meticulous cleaning and, when needed, preheating to combat copper's rapid heat dissipation. This preparation is the bedrock upon which a superior weld is built.
Our exploration of TIG, MIG, and stick welding has revealed the strengths of each method, allowing you to choose the most effective technique for your project's demands. Whether you're seeking the finesse of TIG welding for intricate art pieces or the robustness of MIG welding for industrial applications, the knowledge you've gained here will serve as your guide.
We've also navigated the selection of filler metals and shielding gases, emphasizing their critical role in achieving a flawless weld. By matching the filler metal to the copper alloy and fine-tuning your shielding gas choice, you're setting yourself up for success.
But the journey doesn't end once the weld is complete. Post-welding practices, such as controlled cooling and diligent cleaning, are essential to ensure the longevity and appearance of your work. These steps are the hallmark of a skilled welder who values both form and function.
Safety has been a golden thread throughout this guide, reminding you that the well-being of the welder is paramount. By adhering to safety protocols and wearing the right gear, you ensure that your welding practice is sustainable and harm-free.
As you continue to refine your skills with each new copper welding challenge, remember that practice is the key to perfection. Embrace each project as an opportunity to apply the principles you've learned and to further hone your craft. With dedication and a commitment to continuous learning, you'll see your confidence and capabilities flourish, solidifying your place in the rewarding world of copper welding.
Sharing is Caring
Feedback
At WeldWins, we know we aren't perfect which is why we're always looking for ways to improve. You can help us do better by taking 2 minutes to fill out our simple feedback form.
Any and all feedback is welcome. It could be a complaint, an idea, or even just a comment, we'll always be grateful to hear what you think.