How Can You Choose Between AC and DC Welding?
May 7, 2024
10 min read
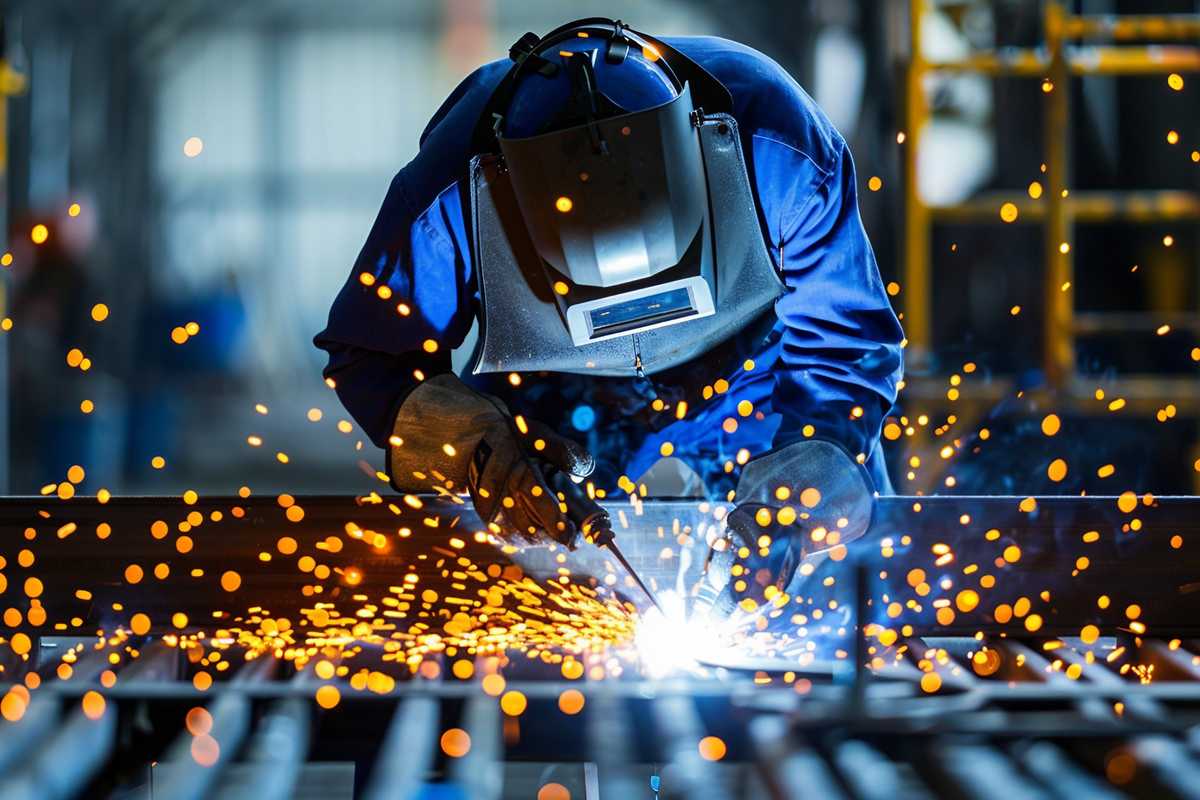
1. Introduction
Welcome to the dynamic world of welding, where the fusion of materials forms the backbone of countless structures and products we use daily. At the heart of this transformative process lies the choice between two types of electrical currents: alternating current (AC) and direct current (DC). This decision is more than just technical jargon; it's a pivotal factor that affects the strength, longevity, and quality of every weld you make.
Whether you're a budding welder or a seasoned artisan, understanding the distinct roles of AC and DC welding currents is essential. Each current type brings its own set of advantages and challenges to the table, influencing how you approach different welding projects. This guide is designed to demystify these currents, offering clear insights into their characteristics, benefits, and optimal uses.
Join us as we delve into the intricacies of AC and DC welding. We'll compare their applications, discuss their technical differences, and provide practical advice to help you choose the right current for your welding tasks. By the end of this guide, you'll be equipped with the knowledge to enhance your welding techniques and achieve superior results. Let's light up the torch and begin our journey into the electrifying realm of welding currents.
2. Decoding the Power Behind the Weld: AC vs. DC Currents
Welding is an art that melds science and skill, where the choice of electrical current—Direct Current (DC) or Alternating Current (AC)—plays a pivotal role in the outcome of your work. The type of current you select can affect the weld's integrity, appearance, and strength. Let's break down the specifics of DC and AC currents to see how they influence the welding process.
Direct Current (DC): Precision and Control for Welders
Direct Current (DC) is like a steady stream of water flowing in one direction—it's predictable and constant. This makes DC ideal for welding jobs that demand precision, such as when working with delicate or thin metals. The unwavering nature of DC provides a stable arc, essential for strong, reliable welds.
DC comes in two flavors based on polarity—DC electrode positive (DCEP) and DC electrode negative (DCEN). With DCEP, the electrode acts as the positive pole and is your go-to for deep penetration into thick materials, perfect for robust constructions. DCEN, where the electrode is negative, shines when you're aiming for fast welds on thin surfaces, like crafting a delicate metal sculpture.
Alternating Current (AC): Versatility in Challenging Conditions
Alternating Current (AC) is the rhythmical dance of electricity, changing direction like the ebb and flow of tides. This dynamic movement of AC is excellent for tackling metals that are prone to getting 'dirty' with oxides, such as aluminum. The switching current cleans these metals as you weld, ensuring a stronger bond.
AC is also your ally when dealing with magnetized materials that could throw off a DC arc. It's less expensive than DC equipment, making it a budget-friendly option for many welders, especially when starting out or sticking to specific materials like aluminum.
By understanding the unique qualities of DC and AC currents, you can make informed choices that lead to better welding results. Whether you're crafting a custom motorcycle frame or repairing a garden gate, knowing which current to use can be the difference between an average weld and a masterpiece.
3. AC vs. DC Welding: A Detailed Comparison
Welding requires a deep understanding of the tools and techniques at your disposal, particularly the type of electrical current—AC (Alternating Current) or DC (Direct Current). Each current type has unique properties that can significantly impact the quality and efficiency of your welding projects. In this section, we'll dissect the technical distinctions between AC and DC welding and outline their advantages and disadvantages to help you make the best choice for your welding needs.
Understanding the Technical Nuances
AC welding is characterized by a current that reverses direction at regular intervals, often multiple times per second. This fluctuation can be advantageous in welding, as it assists in cleaning the weld area of oxides and minimizes spatter. AC welding is the preferred method for materials and electrodes that demand an alternating current for a consistent arc.
Conversely, DC welding offers a steady current flowing in a single direction, leading to a more stable and manageable arc. This consistency is particularly beneficial for welders of all skill levels, as it allows for greater control and reduces the likelihood of arc blow—a common issue where the arc strays due to magnetic interference.
Weighing the Pros and Cons
AC Welding Advantages:
- Enhanced arc stability on materials such as aluminum and magnesium.
- Reduced sensitivity to arc blow with thicker materials.
- More effective for metals that tend to oxidize, like aluminum.
AC Welding Disadvantages:
- Tendency to produce more spatter than DC welding.
- Not typically recommended for welding thinner metals.
- The oscillating current can be challenging for inexperienced welders to manage.
DC Welding Advantages:
- Yields a smoother and more stable arc.
- Simpler to learn and control, making it a great starting point for beginners.
- Offers deeper metal penetration, ideal for thicker materials.
- Results in less spatter and cleaner welds overall.
DC Welding Disadvantages:
- Susceptible to arc blow in certain conditions.
- May not be as effective on specific metals that are better suited to AC welding.
Armed with this knowledge, welders can make educated choices about the current type that's best for their particular welding tasks. Whether tackling a DIY project at home or taking on a professional assignment, the decision to use AC or DC welding can have a substantial impact on your work's outcome.
4. Choosing the Right Current for Your Welding Project
Selecting the appropriate electrical current—AC (Alternating Current) or DC (Direct Current)—is a critical decision that can significantly influence the outcome of your welding project. Each type of current shines in different scenarios, and understanding when to use each can lead to superior welds. Let's dive into the specific situations where AC or DC current is the best fit.
Optimal Situations for AC Welding
AC welding is your best bet in the following circumstances:
- Handling Magnetized Materials: If you're welding materials that have become magnetized, AC is your ally. It reduces the arc blow, which can otherwise cause uneven welds and compromise quality.
- Joining Thicker Metals: For substantial materials, AC welding comes to the rescue, especially when using techniques like shielded metal arc welding (SMAW).
- Welding in the Great Outdoors: The alternating nature of AC current is less affected by wind and environmental factors, making it a reliable choice for outdoor welding tasks.
- Using Specific Electrodes: Some electrodes are designed to perform optimally with AC, particularly those that need a high level of arc cleaning action to combat oxidation.
Ideal Conditions for DC Welding
DC welding is the preferred method in these instances:
- Welding Thin Metals: DC's stable arc is perfect for thin metals, helping to prevent burn-through and ensuring a clean, precise weld.
- Challenging Positions: When welding overhead or vertically, DC provides the control needed to produce consistent, high-quality welds.
- Aiming for High-Quality Finishes: DC welding is known for producing less spatter and a smoother weld bead, which is crucial for a polished final product.
- Working with Non-Ferrous Metals: For metals like aluminum and magnesium, DC welding, particularly with a TIG setup, offers better control and results in cleaner welds.
By considering these specific applications, you can choose the most effective current type for your welding project. It's not just about AC or DC; it's about the material you're working with, the welding position, and the quality you aim to achieve. With this targeted knowledge, you'll be able to navigate the nuances of welding currents and ensure your projects are executed with precision and skill.
5. Selecting the Ideal Welding Equipment
Embarking on welding projects requires the right tools for success. Your choice of welding machine—whether AC, DC, or AC/DC—plays a pivotal role in the quality and efficiency of your work. Here's a streamlined guide to assist you in making a well-informed equipment selection.
Types of Welding Machines
Different welding jobs call for specific types of machines. Here's a quick rundown:
- Stick Welders (SMAW): Great for a variety of jobs, these machines work with both AC and DC.
- TIG Welders: Best for detailed work, they also accommodate both AC and DC.
- MIG Welders: Known for their user-friendliness and speed, they come in AC, DC, or AC/DC models.
- Flux-Cored Arc Welders: Ideal for outdoor projects, these don't need a shielding gas and can handle windy conditions.
Choosing Between AC, DC, and AC/DC Models
- AC Welders: Cost-effective and suitable for materials like aluminum or for outdoor use where power supply can be inconsistent.
- DC Welders: Pricier but provide a more consistent arc, making them perfect for steel and precision tasks.
- AC/DC Welders: The most flexible option, allowing you to switch currents to match different materials and environments.
Features to Consider
When shopping for a welder, keep an eye out for:
- Amperage Range: A broad range allows you to weld various metal thicknesses.
- Duty Cycle: A higher duty cycle means you can weld longer without a pause.
- Portability: If you need to move your welder often, choose a lightweight model.
- Digital Displays: These provide precise control over your welding parameters.
- Thermal Overload Protection: A must-have to prevent your machine from overheating.
Brand Reliability and Warranty
Invest in a reputable brand with a solid warranty and customer support. This ensures you have access to parts and assistance when needed.
In summary, align your equipment choice with the materials you'll be welding and the conditions you'll face. Whether you need the versatility of an AC/DC model or the precision of a DC welder, the right machine will enhance your welding quality, safety, and efficiency.
6. Wrapping Up: Making the Right Current Choice in Welding
To wrap up, the journey through the world of welding currents reveals that both AC and DC have their unique strengths and ideal applications. We've dissected the characteristics of AC and DC currents, highlighting how DC's steady flow is perfect for smooth, stable welds on metals like steel, while AC's alternating nature combats arc blow and excels with materials such as aluminum.
The guide has laid out the advantages and disadvantages of each current type, equipping you with the knowledge to balance the benefits with any limitations. This information is vital for selecting the most suitable equipment and techniques for your welding projects.
As you progress in your welding practice, remember the significance of choosing the right current for the job. Your decision should be informed by the material, the work environment, and the qualities you want in your final weld.
Use the insights from this guide to inform your decisions and improve your welding outcomes. With practice and hands-on experience, you'll refine your skills and understand the nuances of AC and DC welding. So, take this knowledge into the shop, experiment with both currents, and see how they can elevate your welding artistry. Here's to achieving robust and dependable welds—happy welding!
Sharing is Caring
Feedback
At WeldWins, we know we aren't perfect which is why we're always looking for ways to improve. You can help us do better by taking 2 minutes to fill out our simple feedback form.
Any and all feedback is welcome. It could be a complaint, an idea, or even just a comment, we'll always be grateful to hear what you think.